
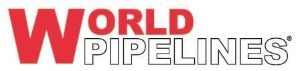
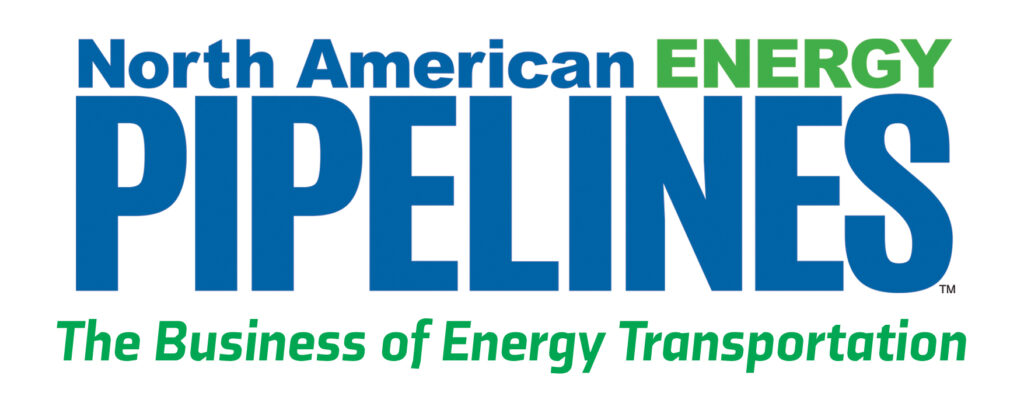
Interested in becoming a media partner? Click here for more information.
Interested in becoming a media partner? Click here for more information.
Pushpendra Tomar1, Geoffrey Krause2, Muthu Chandrasekaran3
1Dynamic Risk Assessment Systems, Houston, USA. 2Dynamic Risk Assessment Systems, Calgary, Canada. 3NDT Global, Calgary, Canada
The aging infrastructure and increasing regulatory requirements have heightened the need for substantial investment in maintaining pipeline system integrity. Consequently, integrity budgets must compete with other financial demands, including growth, expansion, innovation, and strategic acquisitions. It is essential to demonstrate that the integrity investment request is justified and optimized.
This paper presents a financial investment methodology that leverages risk-based likelihood and consequence values, converting them into financial metrics to aid capital allocation and decision-making. This approach evaluates the economic viability of investments by comparing the costs of preventative measures against potential future failure costs in present-day terms. Additionally, it identifies the year when remediation or preventative investments become economically viable.
We illustrate this methodology through a case study for an operator, evaluating whether it is more cost-effective to repair an existing pipeline to support production growth or to construct a new pipeline section at a significant expense. The study involved simulating various operating scenarios and inputs related to revenue, operating costs, maintenance, and repair costs to calculate net cash flow and internal rate of return. By considering the net present value of all investments and benefits, the study determines the economic viability of different scenarios and provides a final recommendation on the repair versus replacement decision.
Joel Van Hove1, Owen Bunce2, Casey Dowling3, Pete Barlow4
1BGC Engineering, Vancouver, Canada. 2BGC Engineering, Calgary, Canada. 3BGC Engineering, Golden, USA. 4BGC Engineering, Edmonton, Canada
Horizontal directional drilling (HDD) is a widely used trenchless technology for pipeline installations, especially in areas where conventional open trench construction poses significant construction challenges, such as river or landslide crossings – areas which also present geohazard risks. HDD installations can be highly effective at avoiding and nearly eliminating geohazard risk, but the failure records from industry reveal that many HDDs fail to effectively avoid landslides and some significantly increase geohazard risk. A recent study of North American pipeline systems estimated that HDD installations have been used at approximately 14% of landslide crossings, and at 16% of those crossings, the pipeline is drilled through, rather than below the landslide. The same study reviewed an extensive history of geohazard related pipeline failures and found a 15 times greater failure rate for pipelines intersected by active moving landslides where the installation method was HDD versus conventional trenching. This observation means that pipelines installed by HDD, which do not effectively avoid landslides, are at a much higher risk of failure and represent the category of geohazards most likely to cause pipeline failure.
Considering the elevated risk HDD crossings of landslides represent, assessing the effectiveness of each crossing is critical to successful geohazard risk management. Existing methods of landslide assessment such as visual inspections from landslide experts, survey monitoring, and lidar change detection often fall short in evaluating the depth and activity of a landslide, which is crucial for understanding the risk to HDDs. While installing deep instrumentation like slope inclinometers can provide the necessary data, it is costly, time-consuming and prohibitive for wide scale application.
Inertial Measurement Unit (IMU) bending strain analysis has become a critical tool for HDD effectiveness assessment because the data is widely available, precise, and provides the opportunity to directly observe landslide impact to a pipeline by transforming the pipeline itself into an instrument to detect bending strain, much like a slope inclinometer. This paper compiles findings from bending strain analysis across hundreds of HDDs, detailing characteristic strain patterns and cataloging examples where landslide impact was identified and confirmed. The distinct bending strain patterns caused by landslide movements can be detected at low strain levels, often below typical reportable limits for bending strain analysis, due to the unique and low strain magnitude signatures typical of HDD installation.
Recognizing these strain signatures and interpreting them in the context of potential landslide loads allows early identification of landslide impact and provides operators the opportunity to proactively manage risk and avoid ruptures and service outages. Since HDDs represent a disproportionate amount of geohazard risk, assessing HDDs for landslide impact is one of the highest value actions operators can take to manage geohazard risk. IMU bending strain analysis proves to be an effective tool for this purpose, offering a practical method for detecting and assessing landslide impacts on HDD pipelines.
Rhett Dotson1, Liam Hagel2, Jing Wang2, Rick Wang2, Duncan Wang1
1D2 Integrity, Houston, USA. 2TC Energy, Calgary, Canada
Curvature-based strain assessments have served as the basis for identifying injurious dents in natural gas pipelines for the last decade. Improvements have been made to the original ASME B31.8 equations over the last six years, and a decade of studies have resulted in broader application of the strain limit damage (SLD) and ductile failure damage indicator (DFDI) as suitable methods for assessing strain limits. While these methods have been shown to be capable of identifying dents that have formation cracking, there are examples where cracking has been found in dents with low strains. This paper examines three separate case studies of dents with acceptable strains where cracking was found during excavations. Initial curvature-based strain calculations and finite element-based strain calculations presented in prior publications did not accurately identify these dents as having critical strains or being susceptible to formation-induced cracking. This study examines other factors that may have led to the observed cracking including changes in restraint condition, variations in maximum internal pressure, or tool tolerances. The paper concludes with considerations for identifying these features in future assessments and provides recommendations to operators using curvature-based strain assessments.
Denise Earles1, Mehdi Laichoubi1, Hamza Kella Bennani1, Miaohang Hu1, Florian Stasse1, Vincent Benet1, Yvan Hubert2, Jared Kowis2, Samuel Cheng2, Teko Hanvi2
1Skipper NDT, Paris, France. 2Enbridge, Houston, USA
There are several threats to the integrity of buried pipelines, including geohazard events such as landslides, earthquakes and other types of ground movements. These event cause axial and/or lateral deformations that induce bending strains in these structures, leading to catastrophic consequences. It is estimated that 16% of pipeline failures over the last 10 years have resulted from geohazard events.
To address this issue, Skipper NDT has developed a proprietary embedded system which can be mounted on a drone or ground-based cart, capable of generating a high-precision digital twin of buried pipelines. This technology enables the acquisition of position data with high data density, which can be utilized to assess bending strain.
A three-step validation process was undertaken to validate the drone-based positional data. Step one involved controlled validation of the XYZ data for precisions and accuracy. The second step, previously completed and reported during PPIM 2024 involved limited testing and validation to a segment of pipe with cold bends. This verified the ability of the sensor to identify small changes in pipeline geometry as a proxy for ground movement.
This paper will focus on the third and final step used to validate this technology’s effectiveness by way of a case study completed with a leading pipeline operator. For this study, Enbridge Gas Transmission and Midstream selected candidate pipelines in active, high-risk geohazard locations to be studied. Data from this study were compared against known presence, location, and bending strain data acquired from ILI tools in 2022 and 2023. The results confirmed that the drone-based acquisition produced reliable and repeatable data within 0.02% agreement with the baseline ILI IMU and bending strain data. The details of this study and its results are presented in this paper.
Brian Ellis1, Nigel Curson2, Louise O’Sullivan2, Blake Bixler3, Rabindra Chakraborty4
1pipelinelogic, Lakewood, USA. 2Penspen, London, UK. 3Senslytics, Oklahoma City, USA. 4Senslytics, Atlanta, USA
The Gas Mega Rule not only imposes stringent requirements on pipeline operators, but also provides an opportunity to streamline integrity management practices through gained efficiencies. By integrating digital twins, AI-driven compliance solutions, and data from multiple inline inspection (ILI) runs, operators can move beyond regulatory compliance while enhancing pipeline safety and operational efficiency.
Digital twins act as virtual models of pipeline systems. These models enable predictive analytics, allowing operators to simulate risk conditions like corrosion and stress, and prioritize maintenance and inspections where needed. This proactive approach reduces unnecessary work and targets integrity management funds to high-risk areas, maximizing safety while minimizing costs.
Multiple ILI runs, using technologies like magnetic flux leakage and ultrasonic testing, generate vast datasets that can be consolidated to provide a clear view of pipeline conditions. When strategically analysed in a digital twin environment, this streamlines decision-making, reduces downtime, and optimizes repairs, extending pipeline life and cutting maintenance costs. With AI integration, operators can automate data processing, anomaly detection, and regulatory reporting, meeting Mega Rule compliance while improving efficiency. AI also helps predict corrosion growth, optimize inspection intervals and chemical programs, improve integrity assessments even when not all data is available, and reduce human error, allowing engineers to focus on high-value tasks.
By integrating AI compliance tools with digital twins and ILI data, operators can turn compliance into a strategic advantage. AI-driven insights, such as using AI to predict corrosion growth and mitigate microbial-influenced corrosion (MIC), enable faster, more accurate decision-making and pre-emptive maintenance actions, improving safety and reducing operational costs along the regulatory compliance path.
KEYWORDS: Gas Mega Rule, digital twins, Artificial Intelligence (AI), Inline inspection (ILI), predictive maintenance, anomaly detection
William Deschamps-Robertson, McKenzie Kissel
Onstream Pipeline Inspection, Calgary, Canada.
The gathering market primarily involves small-diameter pipelines, typically ranging from nominal pipe size (NPS) 3 to NPS 6, with NPS 3 and NPS 4 being the most common sizes. Construction practices for these pipelines emphasize rapid installation to align with the operational timelines of wellheads or production pads, making inspection and maintenance secondary considerations. These pipelines often feature tight bends, heavy wall thicknesses, variable product flows and pressure conditions that are not ideal for inline inspection (ILI), especially for smaller diameters like NPS 4.
Historically, inspecting these pipelines required taking them offline and accessing them through bell holes or mid-bend risers, using tethered wireline or crawler systems. However, recent economic shifts have led to higher operating pressures and increased throughput, necessitating a more efficient inspection approach with minimal operational disruption.
This paper highlights the challenges of designing small diameter ILI tools and the iterative design and development process undertaken by Onstream to advance a NPS 4 1.5D TriStream MFL™ technology. This combination magnetic flux leakage (MFL), caliper and inertial mapping tool is designed to inspect gathering lines that were previously deemed uninspectable due to their tight bends and heavy wall thicknesses (HWT). This paper will also present a case study of a recent 1.5D inspection conducted for a pipeline gathering operator. This inspection, which had previously been performed using a tethered wireline tool five years ago, was recently achieved with a free-swim ILI tool, demonstrating the technological advancements and improved inspection capabilities.
Michael Kobelak1, Arvind Chaabra2, Agatha Lee1, Rod Lee1, Avi Neimet1, Roni Sierra3
1Intero Integrity, Toronto, Canada. 2Enbridge, Toronto, Canada. 3Intero Integrity, Conroe, USA
The identification and management of dents and mechanical damage / deformation is an ongoing challenge for pipeline operators. Apart from excavating and examining, performing in-line-inspection is typically required to detect and size dents.
To exceed the mandated standard, Enbridge initiated targeted assessments on a subset of distribution pipes to gain focused insight on pipeline health. These pipelines are located in both urban and agricultural terrain which can increase susceptibility to 3rd party damage.
This paper will review the ILI tool selection process, execution, and the integrity results focusing on Intero’s Laser Deformation Sensor (LDS).
The laser-based system provides a high-resolution dataset by projecting a continuous laser ring inside the pipeline. This allows for profiling dents with complex geometry (such as multi-apex and skewed dents) and supports further advanced processing including strain analysis using the ASME B31.8 standard.
Matt Ellinger1, Stacy Hickey1, Adriana Nenciu1, Pam Moreno2, Ben Ross2, Shanshan Wu2
1DNV, Dublin, USA. 2DNV, Houston, USA
In-line inspection (ILI) run-to-run comparisons can provide valuable insights into the integrity of a pipeline asset. Results from an ILI run-to-run comparison can be utilized to identify anomalies that might become critical prior to the next planned integrity assessment. Alternatively, or in addition to, ILI run-to-run comparison results may indicate that an anomaly that is part of existing excavation plans may not be predicted to reach criticality prior to the next planned integrity assessment. In these cases, such anomalies are perhaps removed from existing excavation plans and replaced with anomalies that are more likely to reach criticality. This allows for more efficient and effective use of limited resources while decreasing overall risk.
Often, corrosion growth rates are established by comparing ILI spreadsheet listings between subsequent inspections. Examples of how to derive spreadsheet-based corrosion growth rates include, but are not limited to:
Relying only on ILI spreadsheet listings to derive corrosion growth rates may result in a misrepresentation of the actual corrosion growth (or lack of growth) that may be occurring in a pipeline segment. By incorporating ILI signal review comparisons between the subsequent surveys, definitive evidence of corrosion growth (or lack of growth) can be established, and more realistic corrosion growth rates can be derived.
In this case study, the authors applied the spreadsheet-based corrosion growth rates (described above) to identify anomalies calculated to reach criticality prior to the next planned integrity assessment. The authors then performed ILI signal review comparisons at this subset of anomalies to establish more realistic corrosion growth rates. Upon applying the signal review-based corrosion growth rates, the number of anomalies calculated to reach criticality prior to the next planned ILI survey was reduced.
Additionally, several anomalies which spreadsheet comparisons indicated were growing minimally were found to be growing at higher than spreadsheet calculated rates. This resulted in the addition of some anomalies to the excavation plan that were previously considered lower criticality.
The reduction in anomalies calculated to reach criticality and the addition of a few anomalies previously considered non-critical prior to the next planned ILI survey will be utilized by the pipeline operator to optimize their excavation program. The result is less overall repair cost coupled with a reduction in risk.
KEYWORDS: ILI analysis, ILI run comparison, Corrosion growth assessment, ILI signal data
Niels Pörtzgen
ApplusRTD, Rotterdam, Netherlands
As part of the integrity management program, pipelines can be screened for possible damage with efficient in-line inspection (ILI) tools. The type of damage depends on the degradation mechanism such as dents (mechanical damage), wall thickness loss (corrosion) or cracks (fatigue, stress corrosion cracking (SCC)). Although ILI tools have been proven to be adequate for the detection of such damage, accurate characterization and sizing of indications is usually very limited. Therefore, the pipeline can be excavated at suspicious locations identified by ILI tools for confirmation and further investigation with additional non-destructive testing techniques.
For integrity assessment and remaining lifetime analyses, accurate information of the most critical indication or area is required. In case of SCC, the remaining wall thickness between the tip of the largest crack and the surface is most critical. However, SCC often appears as clusters of multiple cracks whereby it is challenging to identify and size the deepest with traditional ultrasonic testing strategies such as the pulse-echo technique, phased array sectorial scanning or the time of flight diffraction (ToFD) technique.
In this paper, we will introduce the latest strategy of ultrasonic inspection based on full matrix capture (FMC) ultrasonic data which is processed in real-time into an image with the IWEX system. With this technique also known as the total focusing method (TFM), it is possible to detect clusters of SCC and to identify and size individual cracks within the cluster.
To demonstrate the performance of the technology, measurements were performed on a test sample. The test sample contained a cluster of SCC in the area of the seam weld of a 10mm thick carbon steel pipe. For reference purposes, the test sample was also inspected with the ToFD technique. Scan results from measurements with IWEX will be presented together with the interpretation. In contrast with traditional technologies, IWEX utilizes multiple ultrasonic travel paths (known as imaging modes) resulting in a comprehensive image which shows the shape of the cracks and its tip which can be used for accurate height sizing. The sizing accuracy will be demonstrated using a reference piece of approximately the same wall thickness containing controlled machined notches at different depths.
The visualization and sizing accuracy are unique for the IWEX system and it facilitates an improved analysis for the pipeline integrity. Furthermore, we will evaluate conditions for adequate use of the technology, and we will discuss practical considerations for use under field conditions.
Kaushal Shah’s career has been marked by his contributions to a range of high-profile energy projects, primarily in the natural gas and biofuels industries. His technical proficiency encompasses a wide array of responsibilities, from the design and construction of transmission natural gas pipelines to leading innovative solar energy projects. Throughout his career, Kaushal has successfully navigated the complexities of large-scale infrastructure projects by applying his deep knowledge of engineering, risk mitigation, and project execution.
Kaushal spent the first decade of his career at Mott MacDonald with starting as an Engineer I and growing to a Project Manager. During his tenure at Mott MacDonald, he led a team of 30 engineers and designers on transmission natural gas pipelines and compressor stations, and refinery projects. His experience includes design engineering, CAPEX/OPEX budget development, technical report writing, permitting, project execution, and risk mitigation. Kaushal is a Professional Engineer in multiple states and has supported marquis projects including NorthEast Energy Direct, PennEast pipeline, Iroquois Enhancement by Compression, North Montney Mainline and Prince Rupert Gas Transmission to name a few. He has worked for all of the major pipeline operators as an engineer including Williams, TC Energy, Enbridge, Kinder Morgan and Iroquois Gas.
Since joining ICF in 2022, Kaushal has impacted the firm’s consulting engagements. As a Senior Project Manager, one of his notable contributions includes leading the Independent Engineering (IE) review for the sale of gas operator company 2023. In this project, he evaluated operator processes, conducted site visits, and assessed adherence to regulatory standards, providing expert technical opinions that were integral to the successful transaction of the asset. His leadership and technical expertise were crucial in ensuring the project met delivery timelines, underscoring his capability to manage high-stakes environments.
Additionally, Kaushal’s leadership in managing multiple engagements for a major Oil and Gas company to help them expand their renewable energy portfolio to include renewable natural gas asset expansion. He also recently led a study analyzing Lifecycle GHG Emissions of U.S. LNG Exports for Natural Allies for a Clean Energy Future (NACEF) and the Partnership to Address Global Emissions (PAGE) that indicated LNG exports are likely to have represented a net reduction in the world’s GHG emissions compared to the mix of alternative fuels (primarily coal and oil).
In addition to supporting the domestic oil and gas industry, Kaushal has also managed international oil and gas engagements helping national oil companies evaluate impacts of Task Force on Climate-Related Financial Disclosures (“TCFD”) and the Greenhouse Gas Protocol. This study evaluated various abatement curves for industry emitters to provide insights for high impact and change industries for a Middle East oil and gas producing company. Kaushal measured strategies employed by similar national oil companies in the Middle East and compared it to the client’s progress to achieving a net zero 2050 policy.
Kaushal also leads large portfolio of solar, e-methanol and biofuel project which highlights his experience diversity and new energies. As the lender’s technical advisory, Kaushal overseeing corporate process and procedure reviews, mechanical and substantial completion reviews, production and investment tax credit generation reviews, and construction loan revolver reviews.
His ability to manage multiple projects simultaneously—often with various stakeholders and nationwide lenders—demonstrates his expertise in both technical and financial aspects of energy projects.
Zach has seven years of pipeline-related experience. He holds a Bachelor of Science degree in Mechanical Engineering from The Ohio State University, and he is an integral technical expert and project manager at DNV.
Zach joined DNV in 2017 and quickly matured from a new engineer into a technical leader in pipeline integrity, concentrating on research projects related to ILI, NDE, testing protocols, and toughness testing of long seam welds. In addition to his projects internal to DNV, Zach has contributed as a leader to the following research projects/publications as either the project manager, deputy project manager, or author.
Zach has also made significant leadership contributions to various industry organizations, such as the Young Pipeline Professionals USA (YPP USA), American Society of Mechanical Engineers (ASME), and SGA. Zach’s leadership roles in these industry organizations are summarized below.
Zach is leading major and complex research projects to advance the technical capabilities of the pipeline industry. He volunteers a significant amount of time to support industry organizations, such as YPP USA and ASME B31.4, where he has held multiple leadership positions.
Ken Maxfield1, Jeffery Knighton2, Phil Tisovec1
1KMAX Inspection, Salt Lake City, USA. 2ExxonMobil, Baton Rouge, USA
Recent updates to 49 CFR Parts 192 & 195 call for pipeline operators in the USA to comply with new regulations covering the construction and operation of their pipelines. These codes require that when a new line is constructed or when an existing pipeline is modified, it must be designed and built to accommodate the passage of ILI tools.
Besides the typical challenges of designing a new pipeline or modifying an existing one to ensure it meets the code requirements for ILI tool passage, some unexpected issues can occur when operators attempt to construct new lines or modify them to be piggable. In particular, selection of small-diameter piping (14" and below) and fittings can meet design standards, but still be completely unpiggable resulting in new pipeline construction that is less or not piggable at all. Several real-world situations are discussed where good intentions to increase piggability have backfired, including pipelines that are designed with restricted bores, pipelines that are constructed of materials that due to the manufacturing process have unexpected bore restrictions, and pipelines that have bore restrictions due to the construction process.
Atul Ganpatye1, Emmanuel Valencia1, Debartha Bag2
1Acuren, Magnolia, USA. 2Enbridge, Houston, USA
Hard spots in pipelines have been historically associated with multiple failures. Although assessment of hard spots is a critical aspect of integrity management of pipelines, several aspects of the detection, identification, measurements, and evaluation of hard spots have posed continuing challenges for the industry. One of the fundamental issues that forms the bedrock of integrity management approach for hard spots is the uncertainty in the measurement and interpretation of the hardness values associated with hard spots. Indeed, what cannot be reasonably measured cannot be effectively managed. The aim of the paper is to discuss interpretation of hardness data in light of measurement techniques, tools, procedures, statistical variation, and characteristics of hard spots. The paper will highlight multiple perspectives that will provide a more complete understanding of hardness measurements towards comprehensive integrity management of hard spots.
The paper will focus on a case study that will include the findings from the examination of a set of recently excavated hard spot features in 30 inch A.O. Smith pipe. Specific results from in-the-ditch NDE activities, and detailed laboratory-based examinations will be presented and interpreted. Results will be discussed in light of potential improvements for increasing confidence in the in-the-ditch hard spot evaluation techniques. The findings and recommendations discussed in the paper will be practical and can be readily implemented by operators and NDE vendors for better management of hard spots going forward.
Russell Giudici1, Travis Greenstreet2, Chris Alexander2
1Advanced FRP Systems, Inc., Weymouth, USA. 2Acuren, Magnolia, USA
Pipelines that operate at elevated temperatures present unique challenges to composite repair applications. The material performance of a composite repair is impacted both by its cure temperature and the operating temperature. These variations collectively influence the pressure capacity of the applied composite system.
The first question explored in this paper is the degree to which the properties of a composite system, specifically the tensile strength and modulus, change at various elevated temperatures compared to ambient temperatures. The second question explored in this paper is how the cure temperature of the composite affects the tensile strength and modulus at various temperatures. An elevated temperature post-cure will increase the crosslink density of the polymer, which should result in a stronger, stiffer cured material. Increased crosslink density will also likely affect the elevated temperature properties of the composite repair system.
The testing program referenced in this paper developed a protocol to evaluate the abovementioned questions. Two commercially available, carbon fiber-based composite repair systems were tested. Each system was tested for tensile strength and modulus at various temperatures, from 70oF – 250oF. All samples were analyzed based on tensile strength, yield strength, glass transition temperature (Tg), and ductility on a stress/strain curve. The full test protocol was performed on both composite repair systems at three different cure temperatures. Ultimately, the intent of this testing program was to evaluate how the properties of composite repair systems change at elevated temperatures and to explore how variations in a composite’s cure temperature affect these properties.
Brian Cooper, Jonathan Ferris
Acuren, Grand Rapids, USA
This paper presents the results of a review of recent major pipeline failure investigations by the National Transportation Safety Board (NTSB). Investigations conducted after loss-of-containment failures reveal opportunities for root cause analyses that, if conducted after the failure of a single threat barrier, could have prevented the later loss-of-containment failure. Recognizing these opportunities proactively rather than in hindsight is challenging. This study provides insight into the factors that emerge from the recent major pipeline failure investigations reviewed that can support the proactive identification and prioritization of single-barrier failures for root cause analysis and corrective action.
Ahmed Hassanin1, Atul Ganpatye1, Brian Yeung2, Tommy Mikalson2, Brett Conrad2
1Acuren, Magnolia, USA, 2TC Energy, Calgary, Canada
Girth welds joining pipes/components of dissimilar wall thicknesses exhibit higher stress concentrations at the wall thickness transition region, significantly affecting their fatigue performance and limit load capacities. In addition, the presence of flaws in these welds exacerbate the stress concentration, potentially further degrading their performance. Therefore, when flaws are detected in girth welds, assessment and remediation becomes critical to ensure safe operation.
This paper discusses a case study that utilized numerical and experimental methods to assess the performance of girth welds when the pipe segment is subjected to high strain – low cycle axial loads that result from environmental forces. Additionally, the effectiveness of girth weld reinforcements such as steel sleeves, composite wraps, or a combination of both are examined to evaluate the benefits to the fatigue life.
Numerical analyses involved simulating a typical girth weld using finite element (FE) models to assess the localized stresses and stress concentration factors, with and without reinforcements. Various scenarios were examined, including different wall thickness transition ratios, material mismatches, and repair installation pressures, aiming to evaluate the effectiveness of repairs in reducing stresses and enhancing the fatigue life of the weld.
Testing encompassed sub-scale, small-scale, and full-scale tests aimed at validating the performance of the girth weld with and without reinforcements. Sub-scale and small-scale testing results were coupled with the numerical analyses results to design and execute the full-scale test, which simulated the real-life behavior of the girth weld in the field.
The paper discusses the details of the numerical and testing methods and demonstrates the effectiveness of the reinforcements in improving the fatigue life of girth welds.
KEYWORDS: Girth Welds, Geohazard, Fatigue, Numerical Analysis, Experimental Testing, Pipe Reinforcement, Steel Sleeve, Composite Repair, FEA, Full-Scale Testing
David Futch1, Sean Moran2
1Acuren, Magnolia, USA. 2Williams, Houston, USA
Circumferential stress corrosion cracking (C-SCC) is being identified on a more frequent basis. More often than not, these indications require repair upon discovery. Repair techniques are limited due to the progression of the crack colonies in the circumferential direction. Industry standards limit the applicability of some repairs as the crack direction lies perpendicular to the applied hoop stress and forms due to an axial or bending stress present on the pipeline. Traditional repair techniques, such as a Type B sleeve, Mechanical Clamp, or grinding may have limitations in some scenarios. Therefore, additional testing of repair techniques is warranted.
C-SCC forms when the pipeline experiences an axial or bending load. In many ways, the environment to form and grow SCC is removed once excavated in repaired or recoated. Therefore, these indications would grow due to normal operations of the pipeline – which may include axial bending cycles. Understanding how the repair technique behaves in a bending regime is critically important to accessing other repair options. This study examines a Type A Compression Sleeve and a Composite Repair for their applicability in repairing C-SCC.
C-SCC colonies removed from service were selected for various repair techniques and one colony selected for an unreinforced control sample. C-SCC indications were strain gaged to monitor growth during the test and samples were installed in a pure bending apparatus. The unreinforced sample was cycled (bending load) to failure and the repaired samples were subsequently cycled to the same amount and then subjected to a burst test. Results show that the use of other repair techniques provide sufficient reinforcement under typical bending loads expected. This allows additional repair techniques when C-SCC is encountered in the field.
Atul Ganpatye1, Ahmed Hassanin1, Matt Jaouhari2
1Acuren, Magnolia, USA. 2Bechtel Energy, Houston, USA
This paper provides a parametric overview of the design parameters that influence the installation and performance of Type A compression sleeves on pipelines. When designed and installed correctly, Type A compression sleeves can be effective in reducing the net hoop stress in the carrier pipe. At the functional level, the interaction between a compression sleeve and the carrier pipe manifests as an interference fit where the installation is achieved by way of thermal expansion of the sleeve rather than by the use of mechanical force (without the interference fit aspect, the functionality degrades to a traditional Type A sleeve).
On account of the nature of the initial stresses imparted on the sleeve (tensile) and the carrier pipe (compressive) during installation, some level of optimization of installation parameters is necessary to achieve the desired final stress levels in the carrier pipe as well as the sleeves. This requires careful consideration of the temperature difference between the carrier pipe and the sleeve, material properties of both the pipe and the sleeve, sleeve thickness, and operation and hydrostatic testing pressures. By way of examples, the paper demonstrates the influence of such parameters on the performance of compression sleeves and the resulting state of stress in the carrier pipes. The paper will also address the effect of installation pressure on the performance of the sleeves.
The paper follows an analytical approach that utilizes spreadsheet-based mathematical modeling of the system parameters as well as finite element analysis (FEA). FEA results also provide additional insight into the circumferential and axial distribution of stresses along the sleeve as well as the carrier pipe. A more rigorous understanding of the performance of the compression sleeves will allow wider application opportunities for such sleeves and allow better control of the performance.
Matheus Abreu Lopes, Manuelle Corbani Romero, Rafael Wagner Florêncio dos Santos
Petrobras, Rio de Janeiro, Brazil
Abstract
Petrobras oversees more than 4,000 kilometers of subsea rigid pipelines across Brazilian offshore fields, where ensuring safe hydrocarbon transportation relies heavily on a robust integrity management (IM) program. This program involves periodic inspections, which pose significant challenges due to the insulating layers of these pipelines, obstructing external evaluations, and the random distribution of potential flaws along their length. Intelligent pigs remain the preferred inspection technology. However, approximately 50% of the global subsea pipeline network cannot accommodate in-line inspection (ILI) tools due to design constraints, including multi-diameter configurations, tight bends, and bifurcating Y-shaped junctions. Retrofitting these systems with pig launchers and receivers is frequently cost-prohibitive.
This paper outlines Petrobras’ inspection strategy aimed at advancing the IM of both piggable and unpiggable pipelines. Two categories of inspection tools—screening tools and localized tools—are currently being qualified for operations at water depths reaching 2,000 meters. Screening tools are engineered to scan entire pipeline lengths at speeds of at least 1 m/s, efficiently detecting and locating defects. Once potential anomalies are identified, localized tools are deployed to these specific areas to perform quantitative defect characterization, enabling precise fitness-for-service (FFS) assessments. For piggable pipelines, Petrobras integrates Direct Magnetic Resonance (DMR) technology into cost-effective cleaning pigs frequently deployed during routine maintenance. This approach allows deferral of intelligent pig runs when no defects are detected.
For unpiggable pipelines, a distinct strategy is required. Remotely Operated Vehicles (ROVs) deploy external screening tools utilizing Metal Magnetic Memory (MMM) technology, capable of penetrating insulating layers to detect potential flaws. Localized inspection tools are further categorized based on defect type: corrosion defects or cracks. These tools are also applicable to piggable pipelines, enhancing defect characterization accuracy through cross-validation with intelligent pig data. This integrated inspection framework not only optimizes operational costs but also enhances diagnostic reliability, contributing significantly to the safe and efficient management of subsea asset integrity.
Thomas Beuker1, Felipe Freitas2, Matthias Hilvert1
1ROSEN, Lingen, Germany. 2ROSEN, Houston, USA
EMAT technology has been established as a viable method for In-Line Inspection (ILI) of pipelines. Recently, the practices in the industry for increasing sensitivity regarding axial crack detection has been connected to the emerging fuel discussion, such as hydrogen and its potential influence on cracking. In addition, the maintenance of existing assets can also benefit from an optimized hydrotest and dig programs through an improved ILI approach.
The presented new EMAT Ultra technology builds upon the existing technology and allows a seamless integration of existing experiences and workflows. The sensor coverage for this ILI technology has been doubled to achieve redundancy and a dual sound path approach (CW, CCW). In principle, the detection reliability for cracks with critical dimensions has been improved beyond the industry’s current standards to 95% (POD). This paper presents the performance of this new technology based on industry standards and highlights the results obtained from several pipeline inspections. This technological improvement aims to contribute positively to the pipeline industry by fostering innovation while respecting the robust foundations laid by the existing EMAT technology.
Stuart Clouston1, Jeff Sutherland2, Ryan Louie3, Steve Worthington3
1Baker Hughes, Cramlington, UK. 2Baker Hughes, Oklahoma City, USA. 3Baker Hughes, Calgary, Canada
Over 15 years ago, pipeline operators requested the development of an in-line inspection (ILI) axial strain measurement tool to support their geohazard management programs. Since then, Axial Strain Measurement Inspection Service (AXISSTM) has been employed on over 25,000kms of pipeline with many high strain locations successfully identified and mitigated. Like any new technology, it took the axial strain tool a few years to become a unique, established and proven tool for a pipeline operator to assess geohazards, movement and other strain – related threats.
Over the years, the operators’ experience has provided key insights as to where the current technology strengths lie and of course where the provision of additional information could further enhance their integrity engineers’ more complete understanding of stress and strain-based threats to then develop proactive mitigation strategies and importantly conduct more cost-effective repair programs – ensuring their pipeline’s safe and continuing operation.
This paper presents a response to these learned and clearly defined needs. It introduces a new bi-axial stress measurement inspection technology, AXISS™ EPS, that adopts these required advancements by providing detailed information on the entire stress landscape of both active loading and residual stresses. The proprietary sensing technology used by this new tool is an evolution of a mature stress measurement technique that has successfully delivered bi-axial stress measurements for steel structures for the last 3 decades in a range of industries including flexible pipeline riser systems in the offshore oil and gas industry as well as nuclear, automotive, aerospace and rail.
This paper provides a comprehensive overview of the new bi-axial stress tool technology, and a summary of the testing validation and verification program. By focusing on the proven performance, the paper will demonstrate the advancements introduced to the AXISS EPS system versus the previous AXISS system, that provide operators an understanding of their pipelines’ total stress and strain status in both the elastic and plastic regions, which in the past would rely on key assumptions to conduct assessments. Using measured condition data will lead to optimized fit-for-service decision-making. In addition, there will be a discussion on how these new advancements will enhance the integrity engineering assessment for high-risk zones such as bends and girth welds.
Jim Marr
Mar Associates, Winnipeg, Canada.
Since the mid-1980s’ to the present there has been some success with the use of various environmental “tools” for SCC threat management, but the variability of individual inputs has spatial, temporal and inter-relationships resulting in complex, non-aligned or inconsistent correlations that continues to be disconcerting to industry.
Even ILI crack tool reliability can suffer without any additional program inputs, mainly from SCC environmental attributes, which also consider stress and material parameters. The incidence of integrating environmental data that includes stress and pipe characteristics with ILI analysis has resulted in fewer false positives and negatives and improved run-to-run issues when addressing the SCC pipeline threat.
ILI Crack tools emerged in the mid-1990s, but it was not until the mid-2000s to late 2010s (depending on the technology) that these tools were fully commercialized. They are now recognized as an industry-wide SCC threat management tool along with hydrotesting and direct assessment.
This presentation will discuss the objective of supporting SCC management activities with the incorporation of the known environmental parameters from both a historical and present perspective within the context of recent regulatory changes.
Michelle Unger1, Michael Rethman1, Karen Collins2
1ROSEN GROUP, Newcastle upon Tyne, UK. 2ROSEN GROUP, Houston, USA
The pipeline industry has long recognized the critical importance of establishing competency and qualification standards to ensure the safety, reliability, and integrity of pipeline operations. The journey toward internationally accredited certifications began by addressing the limitations of traditional competency measures, such as IQ tests and personality assessments. Instead, the focus shifted to developing competency-based frameworks specifically tailored to the pipeline industry, emphasizing the ability to perform tasks to a recognized standard and the need for practical, job-specific qualifications. This foundational phase established key competency elements and standards, guided by international standards like ISO 13623 and ASME codes, ensuring that qualified and competent personnel are engaged across all stages of pipeline activities.
The journey then progressed into the development and implementation of a structured certification process. This phase was marked by creating a qualification ‘route map’ that integrated competency-based learning programs with objective assessments. Extensive collaboration with industry experts led to the development of robust learning guides and digital learning platforms that facilitated knowledge transfer and continuous professional development. Rigorous competency assessments were also introduced to ensure that the certifications awarded reflected genuine expertise and aligned with industry standards.
The culmination of these efforts was achieving international ANAB accreditation for pipeline integrity certifications. This milestone marked the successful transition from theory to practice, establishing a new global standard for pipeline competency certifications. The widespread implementation of eight ANAB-accredited certifications in critical areas of pipeline integrity management has set a new benchmark for the industry, providing a clear and structured path for professionals to achieve and demonstrate their competency.
This paper showcases the evolution of competency certification in the pipeline industry, underscoring its transformation from concept to a robust, globally recognized standard that ensures the highest levels of safety and expertise in pipeline operations.
Gianluca Roscioli
Arculus Solutions, Inc., Arlington, USA
Abstract
Bulk transportation of CO2 and H2 is a crucial development in our efforts to reach net zero by 2050. While using the extensive US 320,000-mile grid of natural gas transmission pipelines seems the simplest, fastest and most cost-effective solution, those pipes suffer (i) strong corrosion from carbonic acid in the case of CO2, and (ii) hydrogen embrittlement leading to high leak rates and catastrophic failures when blending even small percentages of hydrogen with natural gas.
Dense oxide and nitride layers have an extremely low hydrogen diffusivity that can effectively delay hydrogen ingress into the steel substrate, yet they are not widely used because of their poor mechanical durability and their failure as long-term solution. Despite that, when alternated with metallic layers of the same base metal in metal-oxide multilayer composite structures (such as aluminum/aluminum oxide), three peculiar properties can be observed. (i) Formation of a physical barrier to hydrogen permeation thanks to the development of extended space-charge zones at the metal/oxide interface, which repel incoming positively charged hydrogen ions diffusing in the oxide. (ii) Improved adhesion to the substrate thanks to the metallic interlayer that provides physical and mechanical compatibility between the metallic substrate and the oxide layer, thus preventing delamination. (iii) Enhanced resistance to mechanical damage thanks to the strong micro-cracking resistance and the self-healing behavior of the multi-layer composite structure.
Arculus brings to market, partnering with N2 Solutions, a patent-pending, multi-layer Al/Al2O3 coating developed at MIT that is inert to carbonic acid and impermeable to hydrogen. In this study, we produced several coatings with different structures and demonstrated their hydrogen-barrier effect through hydrogen permeability testing using a Devanathan-Stachurski permeation cell, both in the as-deposited and in a damaged state. The results are compared to identify the best structure for field application. Last, we will show a novel application method we developed to apply the optimized coating structure onto the internal surface of pipelines using a smart pig.
KEYWORD(S) FOR SUBJECT AREA: Coatings, Coating inspection, Hydrogen, CO2, Corrosion studies, Emerging technologies, ILI applications, Instrumentation, Manufacturing, Pipe, Repair, Rehabilitation, Robotics.
Willem Vos
NDT Global, Houston, USA
Abstract
NDT global was approached by a large energy business to review the possibilities of inline inspection of a new and challenging crude oil pipeline in the Gulf of Mexico. The line is in very deep waters, shows high pressure and high production volumes and includes a diameter change. Upon review of the combination of these challenges, NDT Global concluded that ART Scan technology can address them, although no off-the-shelf tool would meet the requirements. To assure a successful inspection, the tool design was adapted, and an extensive program to test and validate the tool under those challenging conditions was developed and executed.
This paper shows the specific challenges faced by the team, the solutions that were developed to overcome them and the underlying validation concepts. It therefore highlights the capabilities of advanced inline inspection technologies and also provides guidance to the industry to assure reliable inline inspection projects under extreme challenging conditions.
The authors will discuss the high-pressure testing completed on individual components such as cabling, odometers and sensors, which required new dedicated pressure chambers.
Using this setup, various pump trials were executed where the tool could pass the feature spools at elevated speeds. This kind of setup allows a solid combination of both standard testing and blind testing, but it was also used for advanced training and validation purposes.
Safe and reliable passage through the various diameters was able to be confirmed through repeated pump trials, specifically focused on maintaining drive in the larger-diameter section. The compression set of the polyurethane was identified as a potential risk, and this was assessed through full-scale testing and prolonged exposure.
Measurement capabilities of ART Scan technology at high speeds were confirmed and underlie the various capabilities of this inline inspection method.
Hamood Rehman, TK Akins
Altamira-US, Houston, USA
Abstract
Introduction: This paper addresses the challenges in developing and implementing a Facilities Integrity Management Program (FIMP) due to the diverse and non-uniform nature of facility assets with varying life cycles, contrasting with the more uniform assets and clear regulations of pipeline integrity management programs.
Methods: We present a systematic nine-step framework that guides the entire life cycle of facility assets, from corporate policy setting to performance monitoring, with a special focus on inspection, testing, and maintenance challenges.
Results: The framework provides pragmatic guidance for better integrity management and regulatory compliance, particularly addressing the inspection and testing challenges associated with process piping, including insulated, elevated, and limited inspection space piping.
Conclusions: The proposed framework aids in overcoming the disparate nature of facility assets, ensuring thorough integrity management and adherence to regulatory standards. The use of specialized in-line inspection (ILI) tools for process piping is highlighted as a key component in addressing inspection challenges.
KEYWORD(S) FOR SUBJECT AREA: Facility Integrity Management, FIMP, Inspection Challenges, Process Piping, Regulatory Compliance, Asset Life Cycle, In-Line Inspection (ILI) Tools.
Yougui Zheng1, Pedro Rincon1, Adam Maggio2, Ryan Meyer2, Eric Pierce2
1Shell Global Solution US Inc., Houston, USA. 2Shell Exploration & Production Company, New Orleans, USA
This study provides a comparative analysis of Internal Corrosion Direct Assessment (ICDA) and In-Line Inspection (ILI) methodologies for subsea pipelines. It reveals that while ICDA is effective in predicting corrosion depth during its Pre-assessment and Indirect Inspection stages, it struggles with accurately locating specific damage points. This difficulty arises because internal corrosion is often localized and influenced by factors like severe corrosion at joints, making it challenging to identify critical defects even when predictive models highlight vulnerable areas. Moreover, there is a notable difference in the effectiveness of inspection and defect detection when conducted onshore compared to offshore environments.
The study also explores the impact of corrosion inhibitors on inspection processes. These inhibitors are generally effective against widespread corrosion but are less effective at preventing localized pitting. This variability introduces randomness on predicting defect location, which challenges the standard inspection approach outlined by NACE SP-0116. This standard assumes a pattern of widespread corrosion for detailed examinations, but it is inadequate for pipelines with inhibitors where pitting is unpredictable.
To address these issues, the study recommends enhanced inspection strategies. For pipelines that cannot be inspected using traditional pigging methods, it suggests increasing inspection frequency beyond the ICDA guidelines. These adjustments aim to improve defect detection accuracy and better manage the complexities introduced by corrosion inhibitors, ultimately ensuring more reliable pipeline integrity.
KEYWORDS: Direct assessment, ILI analysis, Corrosion Prediction, Inhibitor, Localized Corrosion
Samarth Tandon, Sergio Limon, Ravi Krishnamurthy, Shaikh Rahman
Blade Energy Partners, Houston, USA
Accurately predicting limiting pressures in fitness-for-service evaluations is crucial for maintaining pipeline integrity, determining necessary mitigations, and scheduling the next assessment intervals. While API 579-1/ASME FFS-1 FAD Level 2 has been used in the past for fitness for service determination of limiting pressure predictions, its conservatism has not been thoroughly quantified for pipelines with cracking and seam weld defects. This lack of quantification has led operators to apply additional safety factors, resulting in overly conservative limiting pressure predictions. This paper estimates the inherent conservatism of API-579 FAD Level 2 with respect to pipeline rupture failures by analyzing results from the burst testing, in-service, and pressure test failures of pipelines with natural Stress Corrosion Cracking and Toe Weld Cracks. Implications of the findings are discussed.
McKenzie Kissel1, Keila Caridad2, Aaron Schartner3, Neil Shortt3, Jose Fernando Vazquez2, Pu Gong1, Stephen Westwood1
1Onstream Pipeline Inspection, Calgary, Canada. 2TC Energy, Mexico City, Mexico. 3TC Energy, Calgary, Canada
TC Energy operates a 430 km (267 mile) NPS 24 pipeline through the Sinaloa state of Mexico, supplying natural gas to a main client power plant near Mazatlán. The system is configured with a compressor station 500 km (310 miles) upstream of the NPS 24 pipeline, and the final compressor station is located at the end of the pipeline near the power plant. This compressor configuration results in the system operating with low differential pressure along the line and flows that are dependent on the client’s demand.
Due to the unique operating conditions, inline inspection (ILI) of the system can be unpredictable and challenging, requiring an engineered approach since standard ILI methods may not be sufficient. This paper describes the collaboration between the operator and ILI vendor, and the ILI vendors approach to successfully inspect the line. An optimized ILI Magnetic Flux Leakage (MFL) TriStream combo tool was utilized, reducing the tool differential pressure requirements by more than 66% and allowing navigation of the pipeline at low differential pressures, while still providing validated Ultra-High resolution Triaxial sizing specification.
John Nonemaker1, Fernando Perez1, Borge Hamnes2
1ROSEN Group, Houston, USA. 2ROSEN Norway, Bergen, Norway
Inspecting offshore risers using in-line inspection technology is generally a complex operation with inherent risks. However, it is particularly challenging when the risers were not built with standard pigging facilities, like launchers and receivers, or the operating conditions don’t allow for pigging operations.
In 2024 a major operator in the Gulf of Mexico experienced such challenges in inspecting its risers and therefore approached ROSEN for an alternative in-line inspection solution. The company operates multiple offshore assets in the Gulf of Mexico, however it operates two risers that were deemed as having a risk of external corrosion in the splash zone. Therefore, the operator required inspections of the risers for potential corrosion at the splash zone down to the seabed so that it could take steps to ensure the safety and longevity of these critical offshore assets.
These pipelines are normally used to transport natural gas from offshore production facilities to onshore processing facilities. Ultrasonic technology (UT) was defined as a potential inspection solution because of the exceptionally heavy wall thickness of the risers; this required the risers to be filled with a liquid medium which, in this case, was decided to be diesel. However, the risers were considered unpiggable due to the following challenges:
• A lack of pig launchers or receivers
• Only a single access point available
• The company preferred not to use external equipment such as pumps and vessels for fluid circulation.
To overcome the challenges and perform high-quality in-line inspections, ROSEN proposed the use of a self-propelled UT tethered inspection solution. This solution allowed the company to proceed with the inspections independent of flow and without performing major modifications to the risers, therefore reducing the risk and integrity expenses. This paper covers the advantages of the self-propelled approach and then describes the implementation of the solution for the offshore risers, including the validation, testing, and execution. It further describes how the cost-effective solution has provided the operator the necessary pipeline inspection data in order to operate the lines in a safe manner.
Atul Ganpatye
Acuren, Houston, USA
Hard spots in pipelines have been historically associated with multiple failures in the past. Although assessment of hard spots is a critical aspect of integrity management of pipelines, several aspects of the detection, identification, quantification, and evaluation of hard spots has been a continuing challenge for the industry. The aim of the paper is to discuss the in-the-ditch assessment activities for hard spots from the perspective of confirming the presence of hard spots reported by ILI and validating the hardness values associated with the hard spot. This is a critical step in managing hard spots for two reasons: 1) typical workflow for in-the-ditch verification of hard spots is highly resource-intensive and therefore efficient deployment of resources is necessary, and 2) the outcomes of in-the-ditch activities influence the interpretation of the quality of ILI data as well as the repair/remediation process.
Several in-the-ditch NDE technologies/methods are currently being used by various operators to identify hard spot areas and quantify the hardness levels associated with such areas. While the use of various technologies is perfectly reasonable, it is important to establish a set of guidelines that allow consistent outcomes and interpretation of the data generated from in-the-ditch activities. Without a consistent process, results from in-the-ditch efforts can lead to misleading conclusions and ineffective remediation for hard spots.
This paper provides practical guidance for establishing a workflow for in-the-ditch activities, including surface preparation, data collection and documentation, hardness measurements, and interpretation of hardness results. Following the guidance presented in the paper, operators will be able to increase consistency between information collected by various NDE vendors, have higher confidence in the verification of ILI results, and have a more robust set of data on which an effective hard spot integrity management program can be built.
Sarah Newton1, Caroline Scheevel2
1Cambio Earth Systems, Calgary, Canada. 2BGC Engineering, Golden, USA
In line inspection (ILI) inertial measurement unit (IMU) bending strain features can provide key insights for early detection of geohazard risks to pipelines. A program of regular IMU data collection yields significant quantities of data. Appropriate organization, analysis, and integration with other key datasets enables integrity managers to maximize their returns on investing in this data collection. Earlier publications have shown that IMU detects key change at around 50% of all critical geohazard sites (Van Hove et al., 2024). This paper explores a novel approach of applying a data model to IMU data that both geospatially organizes the data and integrates the data with lidar, lidar change detection, InSAR, geohazard inspections, landslide hazard mapping, and instrumentation data. The data model establishes the relationships between ILI runs, bending strain reporting, IMU bending strain features, and IMU bending strain inspections. A software platform is used to visualize these data and enable workflows to enhance geohazard threat detection, assessment, and monitoring. Data associations are established with the geohazards threats such that analysts can easily investigate the geohazard and IMU bending strain feature histories, recommend and track next actions, and monitoring changing conditions that could accelerate geohazard activity and impact the pipelines. This approach is currently in use by 10 pipeline operators in the United States and Canada.
KEYWORDS: Geohazards, Data Management, Integrity Management Plans, ILI analysis
Leslie Ward
Kiefner and Associates, Inc., Houston, USA.
Dead legs in piping systems create a high risk for internal corrosion because of their no-flow or low-flow condition. Within the Midstream industry, designs continue to include dead legs, so facility integrity management programs must manage the threat of internal corrosion. Due to recent failures, there is a growing interest in providing more guidance on what integrity management programs should include to address the internal corrosion threat to dead legs.
The AMPP SC 15 Pipelines and Tanks committee recently met at the AMPP Gulf Coast Conference. The potential to create an AMPP Standard to address the challenges of managing internal corrosion in midstream dead legs became a strong contender for development.
This paper will discuss what may be included in the new AMPP document. The new standard will draw from existing industry knowledge and is intended to supplement existing standards, such as SP0106-2018 Control of Internal Corrosion in Steel Pipelines and Piping Systems, SP0208-2008 Internal Corrosion Direct Assessment Methodology for Liquid Petroleum Pipelines, SP0206-2016 Internal Corrosion Direct Assessment Methodology for Pipelines Carrying Normally Dry Natural Gas, SP0110-2024 Wet Gas Internal Corrosion Direct Assessment (WG-ICDA), SP0116-2022 Multiphase Flow Internal Corrosion Direct Assessment for Pipelines (MP-ICDA), the newly released API Technical Report 1189, and API 1160 3rd Edition.
Matt Romney, Jonathan Hardy, Dane Burden
TD Williamson, Houston, USA
Axial stress corrosion cracking (SCC) has been a known threat for many years. SCC has been found in many pipelines that are susceptible based on material, stress, and environment and are especially prevalent in high pressure gas lines. In-line inspection (ILI) tools such as ultrasonic crack detection (UTCD) and electromagnetic acoustic transducer (EMAT) are designed to detect and size crack anomalies inclusive of SCC. However, in more recent years, circumferential stress corrosion cracking (CSCC) has been found in both gas and liquid pipelines where other stresses (axial, bending, and combined) are present, than those result from pressure alone.
To manage this threat, several operators have adopted magnetic based combination tools that incorporate inertial mapping units (IMUs). These tools enable operators to combine data sets, allowing the assessment of multiple signals. When analyzed together, these signals can help accurately identify and characterize CSCC, as well as rule it out when it is not present. This paper highlights the use of an existing commercially available ILI tool without any modifications to look for CSCC by using multiple data streams such as geometry, metal loss (axial, circumferential and helical), low field magnetic response, internal/external proximity sensors and IMU bending strain.
This paper will present the development of the CSCC model, its application to real pipeline data and some field data feedback.
Amir Ahmadipur1, Ali Ebrahimi1, Suraj Khadka1, Arash Mosaiebian2
1Geosyntec Consultants, Houston, USA, 2Enbridge, Calgary, Canada
Stress relief excavation is a landslide mitigation method in which the pipeline segment affected by a landslide is exposed to allow for pipeline rebound and release of a portion of the accumulated elastic strains on the pipeline caused by the landslide. The procedure of stress relief excavations is relatively well-established. Pipeline rebound during stress relief excavations are sometimes measured through frequent measurements of survey laths installed at certain intervals tangent to either side of the pipeline. In some cases, strain gauges are installed on pipelines prior to the stress relief excavation to monitor the strain change during stress relief excavation. Another way to evaluate the effectiveness of a stress relief excavation is to compare the run-to-run bending strain measurements using Inertial Measurement Unit (IMU) before and after the stress relief excavation. Most of the times, at best, only one of these measurement approaches is available to evaluate the effectiveness of the stress relief excavation. Case studies having 2 or more of these approaches are not very common; however, when available, they can provide valuable information to the pipeline industry on the effectiveness of the stress relief excavation to reduce the strain demand on pipelines. Such information can also assist pipeline operators with decision making about stress relief excavation versus pipe cutout and replacement or other potential mitigation measures.
This paper presents the data collected during and after stress relief excavations at four landslide sites in the USA. These case studies include a variety of situations in which the stress-relief excavations were performed. The collected information includes pipe rebound measurements using survey laths, strain change measurements during and after stress relief excavation from strain gauges when available, and strain change comparison before and after the stress relief excavations using Inertial Measurement Unit (IMU) measurements.
Cassidy Ryan1, David Classen1, Steve Farnie2, Oleg Shabarchin3, Austin Janousek3
1Baker Hughes, Houston, USA. 2Baker Hughes, Cramlington, UK. 3Enbridge, Houston, USA
A hard spot is defined in the 2024 PRCI hard spot susceptibility review as “localized area in the body of the pipe having elevated hardness levels compared with normal hardness levels prevalent in the rest of the pipe body. They are, in most cases, the result of unintended rapid cooling (quenching) of the steel while in a hot condition in the plate or hot strip mill, or during the forming or forging process for seamless pipe or fittings, with or without benefit of subsequent annealing or tempering.” When stressed, they can be subject to failure from mechanisms such as hydrogen-stress cracking or fracture cracking. Industry experience in managing the hard spot threat paired with the recently published operator susceptibility review have raised awareness to the importance of a reliable inline inspection (ILI) hard spot specification to detect and classify hard spots. Validation data is key for developing a robust specification.
This paper describes how, in collaboration with industry partners, an enhanced solution for hard spot detection and reporting with a robust POD, POI, and POS specification has been demonstrated. Using a three-pronged approach, applied to an established hard spot ILI technology, a rigorous re-validation was conducted comprising testing of essential variables in three design environments. Extensive pull tests, existing and historical dig data, and FEA modeling in the comprehensive development program utilized multiple data streams to establish an enhanced specification and refine classification techniques to ensure confident hard spot identification – and, therefore, efficient dig programs. The enhanced hard spot assessment process was applied to historical inline inspection data to add further optimization and confidence in the derived specification.
Furthermore, the paper will describe how the program not only considered all essential variables in the process and certified an analysis process for the classification of the various hard spot feature types but then how it was effectively extended to three MFL platforms. The result – a broad range of opportunities for combination inspection with standard, planned corrosion inspections.
Rhett Dotson1, Brian Leis2
1D2 Integrity, Houston, USA.2B N Leis, Columbus, USA.
The shape parameter methods used to define the severity of a dent developed as part of research efforts within PRCI have been the subject of significant debate within the pipeline industry. Publications as early as 2019 began identifying challenges in applying the methods outlined in PRCI Reports. Since that time, the shape parameter methods have been updated and incorporated into the 2021 edition of API recommended practice (RP) 1183. Following their inclusion in RP 1183, several publications identified technical questions surrounding the methods and example problems included within the RP. Additionally, many operators have begun incorporating the methods into their integrity management plans. In response, ILI vendors and consultants have sought to automate the process for extracting the required information from dent profiles captured by ILI tools. This paper examines some of the key challenges in automating the process of characterizing dents and extracting the necessary information for the shape parameter methods which have not been broadly discussed within the industry to date. In particular, the paper examines the challenges in identifying complex dents, establishing depth baselines, repeatability, and employing smoothing. Additionally, the paper examines some questionable behavior in the recently released updates to the equations. The paper concludes with recommendations for operators and vendors using the method and potential questions that should be addressed in future industry research.
Henning Bø1, Thomas Bergsland2
1T.D. Williamson, Stavanger, Norway. 2T.D. Williamson, Houston, USA
In the complex and demanding environments of subsea and offshore pipeline operations, ensuring the safety and integrity of critical infrastructure is paramount. The ability to precisely control and monitor non-intrusive isolation tools is essential, particularly during valve repair or replacement on offshore platforms, where depressurization of the entire pipeline can be costly and environmentally detrimental.
This paper explores the innovative combination of non-intrusive isolation tools with a tetherless two-way communication system, which allows for remote activation, isolation, and monitoring of pipeline isolations. By utilizing extremely low-frequency electromagnetic signals, this system enables precise two-way communication through pipeline walls up to 65 mm (2.56 inches) thick, a feature especially valuable in subsea or buried applications where physical access is limited. The remote communication capability allows operators to monitor key parameters such as annulus pressure, pipeline temperature, and the integrity of isolation barriers in real time, ensuring that the isolation is maintained without compromising safety or operational efficiency.
Furthermore, this integration provides significant advantages during valve replacement operations, where localized pipeline isolation can minimize production downtime and loss of product through flaring or venting of the pipeline, thereby reducing environmental impact and associated costs. The paper will present case studies, including a four-year isolation project in the Tyra field of the North Sea, where the integrated system was used to remotely monitor and control the isolation without any degradation in seal integrity. The combination of non-intrusive double block and monitor technology with advanced communication systems offers a robust solution that satisfies both regulatory requirements and operator concerns, enhancing the safety, reliability, and efficiency of pipeline operations.
KEYWORD(S) FOR SUBJECT AREA : Tracking and Locating, Isolating/Plugging, Pig Signalers, Non-intrusive isolation
Mussab Al-Nammi, Khalaf Al-Anazi, Mohammed Al-Rabeeah
Aramco, Dhahran, Saudi Arabia
A case study was conducted on a sour gas service pipeline with high H2S concentration. The aim of the study was to evaluate the current condition of the pipeline and to provide a solution to perform the In-line Inspection (ILI) base run. The sour gas service pipeline was constructed in 2012, has been operating since 2013, and has over 50 KM in length with a size of 20" in diameter.
As part the commissioning, a caliper run was conducted to assess the pipeline’s internal diameter, which revealed that there were no restrictions or dents in the line. After the pipeline was commissioned, ILl runs were scheduled as per the standard requirements, to inspect the newly commissioned pipeline to ensure full integrity. A gauging run was conducted to assure pipeline mechanical readiness for the ILI run.
The gauging run resulted in an unsuccessful run due to considerable damages in the tool and huge amount of debris (more than 1000 kg). A following gauging run was conducted after assuring that all valves were fully opened, which resulted in an unsuccessful with the same damage profile as the previous run.
Given the unsuccessful gauging runs, a caliper run was conducted to identify the obstacle. The caliper tool was retrieved with severe damages and was inconclusive with regards to the internal obstruction.
A comprehensive assessment on the pipeline was conducted to evaluate the causes of the damages, which revealed that the damage was due to hardened debris within the pipeline as a consequence of improper chemical cleaning that was implement after the line was in-service.
The assessment recommended a cleaning campaign with specialized spring-loaded cleaning tools with magnets followed by a caliper tool. The cleaning campaign contained a minimum of thirty back-to-back aggressive cleaning runs. After completing the cleaning campaign, the caliper tool was conducted successfully and the internal restriction was negotiable by utilizing the 18/20" ILl tool, which was conducted successfully. This cleaning campaign resulted in a successful revalidation of the pipeline.
Lucinda Smart, Benjamin Wright
Kiefner and Associates, Ames, USA
The concept of in-line inspection (ILI) tool validation could be summarized as follows: identify dig locations based on ILI-reported features, measure these features in the ditch, compare in-ditch results with ILI predictions, log the results for future ILI assessments at specified intervals, and then proceed to the next pipeline segment. However, the complexities involved in ILI tool validation make it interesting. Each pipeline and ILI run is unique, presenting its own set of challenges that must be addressed.
This paper will provide insight into the analysis decisions made in a case in which a pipeline underwent multiple axial magnetic flux leakage (MFL-A) ILI runs, along with a circumferential MFL (MFL-C) ILI, which reported thousands of defects of varying geometries and depths. The focus will be on the efforts that may be performed to validate this tool run, how to resolve the differences in reporting between the two tool technologies, and how to ensure the pipeline’s safety for continued operation.
Understanding the levels of validation as outlined in API 1163 is essential in whether the tool run can be deemed validated. When validation digs are performed to assess tool performance, particularly when a wide array of defects are reported, it is important to account for the types of defects that may be found and to have appropriate technology available to capture them. More data can explore many facets, and handling that appropriately can be challenging. The results can give a wealth of insight into the tool’s performance and the line’s condition. This paper will continue to provide recommendations on what factors an operator should consider when obtaining a large data set of correlated features from validation digs. Understanding ILI tool performance and the true condition of the pipeline is critical to maintaining the integrity of pipeline assets.
Janille Maragh1, Emily Brady2, Jeffrey Kornuta2, Owen Lopez-Oneal3, Peter Veloo3
1Exponent, Inc., Menlo Park, USA. 2Exponent, Inc., Houston, USA. 3Pacific Gas & Electric Company, Oakland, USA
Federal regulations governing gas transmission pipelines allow nondestructive (NDT) or destructive testing (DT) techniques to verify the material properties of pipe joints. As part of its material property verification program, the Pacific Gas & Electric Company (PG&E) routinely performs pipe grade determination using NDT strength and chemical composition measurements with associated uncertainty values. Over the course of several years, PG&E has also assembled a database of DT data for pipe joints, which includes data for pipe joints both with and without known pipe grade. For the pipe joints without known grade, it is desired to determine the pipe grade to update PG&E’s system of record. Any DT measurements have some degree of uncertainty associated with them that should be accounted for in the pipe grade determination process. However, DT data obtained for pipe joints may not include replicate measurements that could be used to estimate uncertainty (i.e., standard deviation), usually due to the cost and labor required to obtain that data. Therefore, we developed an alternative process to determine reasonably conservative uncertainty values for DT strength and chemical composition measurements.
For this process, we reviewed scientific and engineering literature, testing standards, and instrument manufacturer technical documents. We then obtained or calculated uncertainty values based on the literature and chose reasonably conservative uncertainty values within the element concentration ranges typically observed in low carbon pipeline steels. Additionally, we analyzed PG&E’s historic database of DT measurements and used a subset of the database, which consisted of DT chemical composition and strength data for 633 pipe joints with known grades, to validate our proposed uncertainty values. We did so by comparing the predicted pipe grades calculated using the DT measurements and the proposed uncertainty values with the known pipe grades. This validation process was also used to assess the sensitivity of pipe grade predictions to uncertainty values.
Alan Cornejo1, Martin Melucci1, Brian Kerrigan2, Dom Murray2
1TGN, Ciudad Autonoma de Bs As, Argentina. 2Frontline Integrity, Newcastle, UK
The main goal of any pipeline operator managing an active cracking threat is to find the real cracks and minimize costly verifications of false positives. Crack detection In-Line Inspection (ILI) is commonly deployed by operators as the primary integrity assessment technique to manage axial Stress Corrosion Cracking (SCC) due to its coverage and relative convenience. Whilst these tools can be excellent at detecting planar crack-like reflectors, the performance specification typically states that there is no guarantee that a reported crack-like reflector will be an actual crack with time-dependency, which could pose a threat to a pipeline’s integrity.
This paper presents how a natural gas transmission operator in Argentina has leveraged their extensive ILI and field database to benchmark a predictive, data driven process to support the management of stress corrosion cracking in-line with API 1176 along their network and minimize the number of future verifications of false positives, allowing focus on real integrity threats.
Avenida Central Garage rates
Avenida South Garage rates
Avenida North Garage rates
Ryan Stewart1, Jason Skow1, Ryan Okamura2, Mohammad Al-Amin2, Zain Al-Hasani3, Luigi Calabretta2
1Integral Engineering, Edmonton, Canada. 2TC Energy, Calgary, Canada. 3TC Energy, Houston, USA
49 CFR §192.607 defines unique populations for pipeline material verification. These are defined by wall thickness, pipe grade, manufacturing process, manufacturing date, and construction date. Using ILI to identify pipe attributes has the potential to significantly improve the efficiency of satisfying the material verification requirements outlined in 49 CFR §192.607 for delineating unique populations along a pipeline. However, some of the ILI technologies used in this process are relatively new, and ILI vendors do not yet provide a performance specification for their performance in identifying populations.
This analysis explores quantifying ILI tool performance in defining pipe populations by similar heuristic rules. It incorporates them into a probabilistic model specification for ILI population identification for three attributes: wall thickness, pipe seam detection, and yield strength. The models were fit using populations identified by the ILI vendor and validated using records review and field verification by an operator. Models adequate for characterizing the ILI tools, assumptions regarding pipe populations, and heuristics that can be used as proxies for the ILI vendor’s interpretation of measurement data are discussed.
The methodology outlined in this study aims to quantify ILI’s ability to classify transmission pipeline segments into populations with unique material properties to comply with PHMSA’s material verification requirements. The framework uses statistical methods similar to those outlined in API 1163 for ILI measurement validation, which the industry has been using for about twenty years. These models are designed to estimate the accuracy of future population identifications and identify populations that are more likely to be misclassified, thereby informing an operator’s decision-making to prioritize population validation efforts.
Greer Simpson, Corey Richards
DarkVision Technologies, North Vancouver, Canada
This paper presents findings from test loop data to indicate the strong performance of high-resolution acoustic imaging in an ILI application to evaluate axial cracks. High-resolution acoustic imaging ILI technology represents a significant change in the way ultrasound-based ILI is conducted, and results are interpreted for pipeline inspections. This direct imaging-based approach is grounded in core ultrasound principles, such as time of flight, and speed of sound in fluid and steel, however, it overcomes traditional amplitude based inferred sizing practices for crack flaws based on known calibration manufactured flaws.
The study utilizes high-resolution acoustic imaging to present direct spatial measurements of axial discontinuities in various locations, such as Heat Affected Zones (HAZ) and welds. A full-scale 16-inch test flow loop was manufactured to validate the ILI tool’s performance at line speed with EDM notches, manufactured cracks, and actual field-removed cracks. The results, aligned with API 1163 standards, cover discontinuities on the interior diameter (ID), exterior diameter (OD), and mid-wall, including defects such as lack of fusion (LOF), weld flaws, and stress corrosion cracking.
Tim Rudd1, Carl Scott1, Brian Kerrigan2, Samuel DuRand2
1Valero, Pembrokeshire, UK. 2FrontLine Integrity, Newcastle, UK
In today’s expanding world, pipeline operators are usually inundated with planning requests which interact with their pipeline right of way. In order to evaluate the potential impact on the pipeline and whether mitigation is required, each site requires a time-consuming analysis of the pipe materials, ground conditions, construction plans and above ground loads. This paper outlines how a liquid pipeline operator has digitally optimized a process that reviews load distribution requirements covering all credible scenarios along their system in line with API 1102 and other relevant standards.
Mike Byington, Anouk van Pol, John van Pol
INGU Solutions, Houston, USA
Free floating inline inspection (ILI) tools using magnetic flux density (MFD) measurements have been enhancing pipeline integrity programs for nearly a decade. The use of MFD measurements to infer information on the pipeline wall condition has been demonstrated and with more inspection data becoming available, the capability of using MFD measurements is continuously increasing. This work focuses on anomalous weld identification by applying principal component analysis to magnetic flux density data captured by free-floating ILI tools. The concept of principle component analysis will be explained, how this approach can be applied to unsupervised classification tasks in general, and the results of the specific use case of anomalous weld identification.
Muntaseer Kainat1, Amandeep Virk1, Chike Okoloekwe2, Nader Yoosef-Ghodsi2, Saheed Akonko2
1IntegraFrame, Edmonton, Canada. 2Enbridge, Edmonton, Canada
Pipeline dents are a major threat to the integrity and safety of aging oil and gas transmission systems. While API 1183 provides methodologies for dent assessment, it has several limitations. Traditional strain assessment methods rely heavily on 2D cross-sections, assuming maximum strain or minimum radius of curvature occurs at the dent’s apex, and do not distinguish between restrained and un-restrained dents. Furthermore, fatigue evaluation based on regression models often leads to overly conservative and inconsistent outcomes. This paper presents a novel framework to address these limitations and enhance pipeline safety.
The process begins with ILI data collection, followed by an automated Quality Assurance/Quality Control (QA/QC) process utilizing machine learning to resolve data inconsistencies. The framework employs filtering and smoothing techniques to refine the ILI data. Determining the restraint condition is a key step, guiding the appropriate assessment workflow. Un-restrained dent shapes are scaled appropriately to simulate indentation depth which is always greater than ILI reported depth.
Strain analysis follows both API 1183 guidelines and recent recommendations published in the PRCI report “Improve Dent/Cracking Assessment Methods, PR-214-203806”. Fatigue life is estimated by transforming ILI caliper data into a 3D finite element analysis (FEA) mesh, enabling a rigorous assessment of dent severity.
A critical advancement in this framework is the use of non-linear material properties in the screening level FEA, calibrated to account for residual stresses, to improve stress estimation for restrained dents. By incorporating estimated approximate residual stresses from strain data, the resulting stress values align closely with Level 3 non-linear FEA results, enhancing both accuracy and efficiency in fatigue assessments. Other advancements include the 3D evaluation of dent curvature to identify potential high-strain regions beyond the dent’s deepest point, and the integration of IMU data for identifying dents in non-straight pipeline sections.
This paper presents the technical development and real-world applications of the framework, demonstrating its effectiveness in managing pipeline integrity through risk-informed decision making.
Rhett O’Briant
GUL Americas, Houston, USA
Contact-point corrosion, also known as corrosion under pipe supports (CUPS) presents an ongoing integrity threat and inspection challenge to operators of gas and liquid processing facilities, refineries and compressor stations globally. Contact corrosion most often occurs within difficult-to-access areas such as tightly spaced pipe racks, full encirclement supports, concrete wall or deck penetrations, and air-soil interfaces. The technology now exists for rapid quantitative corrosion measurement within these difficult applications utilizing axially and circumferentially transmitted guided waves.
This novel, low-profile scanning technique is robust and tolerant of pipe surface condition while providing reliable corrosion profile analysis in areas inaccessible by other inspection methods. This presentation will discuss the advantages of guided wave quantitative corrosion measurement and how it can serve to enhance existing inspection programs.
Fan Zhang
Phillips 66, Houston, USA
Due to its body-centered-cubic or BCC crystal structure, carbon steel exhibits a transition behavior of toughness along temperature. The fracture is fully brittle with very low toughness at low temperature, known as lower shelf, and is fully ductile with saturated high toughness at high temperature, known as upper shelf. For the transition region of temperature in between, the steel can exhibit mixed brittle and ductile fracture. This transition behavior is well represented by the transition curve from a Charpy-V-Notch or CVN test.
In quasi static fracture mechanics-based tests, such as J-integral test or crack-tip-opening-displacement or CTOD test, the specimen can exhibit stable crack extension and early unstable crack extension, such as pop-in, if tested at multiple temperatures. In s general transportation pipeline, the surface crack focused by integrity assessment is low constrained and initiates at a static status before failure. Thus, its transition region is at a much lower temperature, more than 100 F for certain cases, than that of a dynamic CVN test or a quasi-static but high constrained standard J-Integral or CTOD test. Thus, A crack feature in a pipe may fail at fully ductile model with burst pressure related to the toughness at upper shelf level even if the tests fall into the transition or even low shelf region at the operating temperature.
In this paper, equations are provided on how to calculate the temperature supporting fully ductile initiation of surface crack in a pipe based on tests data. The worked examples are also provided to demonstrate the application. Certain challenges and potential needs for extra tests are also discussed.
Monique Roberts1, Leigha Gooding2
1PODS Association, Houston, USA. 2PHMSA, Washington DC, USA
At PPIM 2023 PHMSA and PODS presented on the upcoming NPMS Information Collection Changes with 2024 as “Year Zero” or the baseline foundational year for the new submittal requirements with additional minimum requirements for several years to come.
Now that we are in 2025 we will get an update from Monique Roberts, Executive Director of PODS and Leigha Gooding, PHMSA OPS GIS Manager on what they have learned since their 2023 presentation. Leigha manages NPMS (National Pipeline Mapping System) so we will hear first-hand on the new data attribute requirements for your NPMS submittal for 2025 and beyond as well as lessons learned in Year Zero (2024) from both PHMSA and Operators.
PODS and PHMSA have met with several operators over the last 12 months on their experiences with the new changes so we would like to share that information as well as review the MFA requirements, break out tank info, abandonment items, in-plant submissions and many other items that may need some clarification.
This presentation will also cover a high-level overview of the NPMS submittal process, the radical increase in segmentation and new attributes that PHMSA is expecting operators to capture over the next several years as well as some feedback on the new system from the PODS Community.
Did you know that the NPMS system uses the PODS Model? So, if you have ever uploaded your NPMS submittal you have used PODS! PHMSA has been a member of PODS for over a decade now in fact, so the PODS Association works closely to make sure that all data tables and schema are standardized for use by all operators and service companies that support them. The PODS Model is operator designed to comply with regulations, support specific pipeline operations and decrease risk through digital twin/asset knowledge management.
Rhett Dotson1, Alex Brown2, Justin Taylor2
1D2 Integrity, Houston, USA. 2TC Energy, Houston, USA
Assessments based on inertial measurement unit technology are an important component of many operator’s geohazard integrity management programs. Bending strain assessments are commonly used by operators to identify areas of the pipeline that have been impacted by geohazards, and strain change assessments can be used to determine the stability of those suspected areas.
Performing a bending strain assessment requires a vendor to successfully identify and classify bending strain features above the reporting threshold as either reportable bending strain features or as manufactured bends. Features identified as manufactured bends are excluded when reporting a bending strain feature or identifying peak strain locations. While the identification of manufactured bends is a critical step in performing a bending strain assessment, there have not been any publications to date examining vendor performance in correctly identifying manufactured bends. This is partly because documentation does not exist for most pipelines conclusively identifying the location of cold bends. However, this does not change the fact that subjectivity exists in bending strain assessments that has not been critically reviewed by the industry.
This paper presents a first of its kind case study examining bending strain assessment performed on a recently built pipeline with records of manufactured cold bends from construction. The paper compares the bends recorded from construction with the bends identified by the vendor. This paper will help operators using bending strain assessments to understand both the subjectivity in these assessments and the expected real-world performance in identifying manufactured bends.
Richie Joseph1, Saul Chirinos1, Eduardo Munoz2, Pushpendra Tomar2
1Dynamic Risk Assessment Systems, Calgary, Canada. 2Dynamic Risk Assessment Systems, Houston, USA
The viability of a risk model is dependent on the availability and quality of the input parameters. The data gathering effort can either push the risk model (i.e., the model is built around the available data) or be pulled by the risk model (the model dictates the data needs). The former option is not available to US pipeline gas operators that must now adhere to a list of data items prescribed in 45 CFR § 192.917(b). This work produced data quality diagnostic tools, Key Performance Indicators (KPI), and an approach to incorporate data uncertainty into the different types of risk models. A Data Quality Score was developed to allow the internal stakeholders to assess the suitability of the input database before running risk, which is also useful to demonstrate the progress with the data acquisition effort. Data quality KPIs can be evaluated in many dimensions; their development was based on a review of data quality systems for scientific and engineering processes, which had many coincidences with the parameters in the guideline in API Bulletin 1178. The multidimensionality of the data uncertainty makes the definition of the associated meta data a complex task and a possible issue for the database definition. The sensitivity analysis can be leveraged to assess the data importance and minimize the amount of meta data stored. Finally, a guideline for modifying the risk model to compensate for data with high uncertainty. For probabilistic models, the distribution of the input parameter with high uncertainty needs to be modified depending on the nature of source of uncertainty.
The sensitivity analysis can be leveraged to assess the data importance and minimize the amount of meta data stored. Finally, a guideline for modifying the risk model to compensate for data with high uncertainty: For probabilistic models, the distribution of the input parameter with high uncertainty needs to be modified depending on the nature of source of uncertainty.
Tom Bubenik, Matt Ellinger
DNV, Dublin, USA
Pipeline operators use the verification and validation requirements of API Standard 1163, In-Line Inspection Systems Qualifications, to ensure quality in-line inspections (ILIs). Verification confirms an ILI was conducted according to plan, procedures, and processes and that the inspection conditions are consistent with those used to establish the ILI Performance Specification. Validation evaluates the accuracy of the reported anomaly types and characteristics (depth, length, width, etc.) and provides assurance the ILI met its Performance Specification.
Many of the guidelines (i.e., “should” statements) and requirements (i.e., “shall” statements) in API 1163 require the pipeline operator to establish acceptance limits based on pipeline industry experience. Often, API 1163 does not provide guidance on how to establish the acceptance limits. PRCI has developed a guidance document and spreadsheet for conducting the Level 2 and 3 validations and establishing acceptance limits in accordance with the 3rd Edition of API 1163. Both API 1163 and the PRCI documents are widely used in industry to verify and validate metal-loss ILIs, but questions have been raised about the ability to use them for crack-detection inspections. These questions primarily concern the ability to use field non-destructive evaluation (NDE) techniques, which have accuracies similar to or worse than stated ILI Performance Specifications for cracks, to validate the inspections. Simply put, how can an operator validate an inspection when field validation measurements are questionable?
This paper assesses the ability to use API 1163 for crack-detection ILIs including, but not limited to the following:
Several case studies are included to demonstrate the impact of field NDE uncertainties and their impacts on API ١١٦٣ validations.
KEYWORDS: ILI Analysis, ILI Verification and Validation
Shanshan Wu1, Steven Polasik1, Joe Bratton1, Spencer Hoy2
1DNV, Columbus, USA. 2DNV, Calgary, Canada
Operators utilize the calculation methods prescribed in ASME B31.8 Appendix R to predict the likelihood of cracking during the dent formation process. ASME B31.8 Appendix R provides acceptance limits for calculated strain levels below which there is a limited likelihood of crack initiation. Dent strain calculations require detailed caliper measurements, data smoothing, and shape-based analysis for each dent. The industry has been attempting to develop streamlined dent screening criteria based on dent characteristics available in ILI-reported feature listings. These dent characteristics, such as depth, length, and width can be implemented in a screening methodology that does not require the same level of data and assessment as a detailed strain analysis to estimate the likelihood of dent formation cracking.
One such screening criteria that has been used in the industry to assess the sharpness of dents is the length to depth ratio. A length to depth ratio less than 20 has been used by the industry as a predictor of dent sharpness. Logically, a smaller length to depth ratio would indicate a sharper dent and; therefore, a higher strain value. Various studies have compared this ratio to strain estimates with mixed results. This study aims to build on previous studies by incorporating additional data from multiple ILI vendors and tool technologies. Existing screening criteria and industry presented results are explored, along with additional parameters, to identify correlations between dent measurement characteristics and strain results.
If a dent screening methodology based on readily available ILI-reported characteristics is possible, this would result in a valuable tool to enable more efficient assessments, while still maintaining the confidence of a dent strain assessment, to predict the likelihood of cracking during dent formation. This study will share learnings and provide guidelines to be used when considering the development of a dent screening methodology.
Tom Bubenik, Matt Ellinger
DNV, Dublin, USA
API Standard 1163, In-Line Inspection [ILI] Systems Qualifications, was developed to help pipeline operators ensure successful ILI projects. The second edition of the standard is incorporated by reference into the U.S. Code of Federal Regulations Title 49, Parts 192 and 195. The third edition of API 1163 (September 2021) is not yet incorporated by reference but is expected to be soon. In addition, PRCI has developed a guidance document and spreadsheet for conducting verification and validation in accordance with API 1163. Both the second and third editions are widely used in industry to verify and validate metal-loss ILIs.
API 1163 Level 2 and Level 3 validations require an operator to compare field non-destructive evaluation (NDE) measurements to ILI reported dimensions, such as depth, length, and width. Per API 1163, the results of the comparisons are assigned to three “Outcomes” that determine whether the ILI is rejected outright (Outcome 1), further evaluated (Outcome 2), or accepted (Outcome 3).
This paper assesses 100 metal-loss ILIs using the Level 2 requirements of API 1163, 3rd edition, and the PRCI guidance document/spreadsheet. The case studies involve actual ILIs that were previously performed by pipeline operators to ensure the integrity of their pipeline systems. The results indicate that API 1163 is more stringent than expected.
This paper demonstrates that:
The PRCI guidance document and spreadsheet also provide an “equivalent” tolerance for Outcome 2 cases, and they give a method to estimate of the actual ILI performance using a Level 3 approach for Outcomes 2 and 3. Lessons learned from these evaluations are discussed and guidelines for use are given.
Finally, the paper identifies several errors in the PRCI spreadsheet. The authors understand PRCI is addressing and correcting these errors, which affect the calculated probability of detection (POD), probability of correct identification (POI), false call rate, and false negative rate.
Benjamin Mittelstadt1, Terry DeLong2, Matthew Nicholson3, Brian Jimenez4, Robert Zmud5
1Dynamic Risk Assessment Systems, Houston, USA. 2Enbridge, Calgary, Canada. 3TC Energy, Houston, USA. 4Energy Transfer, Houston, USA. 5Dynamic Risk Assessment Systems, Calgary, Canada
The deployment of In-Line Inspection (ILI) tools plays a critical role in pipeline integrity management helping ensure reliability and safety of a pipeline system. ILI tools employ various technologies to gather data used to detect and characterize anomalies including but not limited to metal loss, cracks, or deformations in the pipe wall.
Determining and appropriately considering ILI tool measurement tolerances is critical in the interpretation of the data collected. ‘Determining’ is how the tool tolerance is estimated and quantified, whereas ‘considering’ is the process decision on how use tool tolerance is used in a program. Measurement tolerance (or tool tolerance), in this context, denotes the range of error or deviation between the true value and the measured value reported by the ILI tool. ILI vendors define specific tolerances for each measurement parameter accounting for the tool’s design, calibration, and intended application.
Various methods exist for considering measurement tolerance, varying from the deterministic addition of pre-determined values based on prior tool performance and desired safety targets to reliability methods using statistical techniques that consider the sources of uncertainty individually. Each method has certain practical advantages and challenges that must be understood.
Justin Bekker1, Sri Chimbli2
1Stress Engineering Services Canada, Calgary, Canada. 2Stress Engineering Services, Houston, USA
The in-service welding of pipelines, i.e., sleeves and hot taps, presents unique challenges from accelerated cooling, residual stresses, and risk of burnthrough. While adherence to relevant welding codes is essential, it may not be sufficient to ensure the weld integrity. This paper explores factors beyond code requirements that must be considered when qualifying welding procedures for in-service applications with fillet, groove and overlay welds. The standards that are followed in North America are API 1104, CSA Z662, and ASME B31.3 (which references ASME BPVC Section IX). The essential variables of these codes are generally similar to ASME BPVC Section IX, with some additional requirements, such as closer attention to heat inputs, cooling rates, and the resulting hardness.
Standards require that the cooling rate and welding restraint be considered, but do not state specific requirements. Hardness requirements are specified but the hardness test locations are open to interpretation and standard CSA Z662 allows higher hardness values at an engineer’s discretion. Further, determining acceptable heat inputs for minimizing the risk of burnthrough in a thin-wall pipe is not specified. These aspects of the codes requiring consideration and determining acceptable heat inputs is critical to ensure safety of the welding crew and long-term integrity of the in-service welds. This paper provides the industry best practices on these considerations.
KEYWORDS: Welding, in-service, hot tap, sleeve
Eric Jenkins1, Stella Cunha2
1Tetra Tech, Denver, USA. 2Enbridge, Calgary, Canada
The challenge in many erosion remediation projects for pipeline water crossings lies in achieving a delicate balance: providing robust, protective coverage for the pipeline while minimizing impacts on aquatic life and the natural progression of the waterbody. Often, these projects resort to pipe lowering, a costly and environmentally disruptive measure that can interrupt pipeline operations, leading to service disruptions and financial losses. Although such projects ultimately yield a pipeline with reduced integrity risk alongside a naturally developing water body, the high costs involved often divert funds away from addressing other integrity issues. This can lead to further degradation of low cover and exposed sites awaiting funding.
The Enbridge L41 pipeline at the South Fork Nemaha crossing, which suffered from low cover due to both downward and lateral scour, serves as a case study. This study will detail five methodologies implemented to ensure adequate pipeline protection while facilitating the passage of aquatic life under typical low-flow river conditions. Initially, the project team pinpointed two upstream structures that altered historical flow patterns as the primary causes of increased scour, addressing these root causes as feasibly as possible. Secondly, a concrete mat system was deployed over the pipeline to provide cover without significantly elevating the riverbed. Thirdly, the bank, previously near-vertical and prone to scour and slough, was regraded to a more stable 2:1 slope to mitigate flooding during heavy rain. Fourth, traditional riprap was used to armor the bank’s toe up to the ordinary high-water mark, safeguarding against typical annual high flow events. Lastly, the area above the high-water mark was revegetated using willow species indigenous to the region, known for their rapid propagation and strong rooting on riverbanks, offering natural erosion protection during extreme flooding.
Daniel Sandana, Lauren Guest, Emily Burrow
ROSEN, Newcastle upon Tyne, UK
Carbon Capture and Storage (CCS) involves the conveyance of carbon dioxide (CO2) through pipelines from the capture facility to a storage field. While CO2 can be transported in a gaseous state, the dense or supercritical state is preferred due to efficiency and project economics, particularly for storage applications. This paper will review the integrity threats faced by purpose built and repurposed CO2 pipelines and the role of in-line inspections (ILI) in detecting and sizing critical defects while overcoming the mechanical and operational challenges of this medium.
The management of time-dependent threats in CO2 pipelines must overcome unique challenges in these high-pressure dense phase operations, which can be compounded with the presence of impurities originating from various industrial processes and applications. This paper reviews, in line with current industry understanding, the time-dependent threats which could arise in pure (naturally occurring) CO2 and anthropogenic (man-made) CO2 pipelines depending on operational scenarios. Key gaps and challenges are highlighted.
The requirements of in-line inspection programs in CO2 pipelines, aligned with the integrity threat review, are discussed, including specific considerations for pipeline change of product (repurposing). Considering historical pipeline design and practices (e.g. diameter, thickness, toughness), high operational stresses and specific offshore axial load considerations for offshore applications, the paper reviews critical flaw dimensions e.g. volumetric, crack-like, that may be applicable and reviews the capability of ILI under these circumstances.
The paper then reviews the key design, mechanical and operational considerations and challenges associated with CO2 pipelines, considering fluid-specific properties, in successfully ‘designing’ and deploying in-line inspection programs in dense CO2. For example, the operational parameters and pipeline construction have key roles in defining the most adequate combination of in-line technologies and also the actual configuration of each cleaning pig and inspection tool. The current industry ILI limitations of diameter and pipeline wall thickness are also highlighted; this is of particular importance considering a trend of CO2 pipeline designs asking for higher wall thicknesses to address fracture propagation and accelerated corrosion issues, to the detriment of inspection capabilities (and thus safe integrity management) .
Exposure testing of tool components, customization of tool configurations, and proving robustness both mechanically and in terms of technology repeatability through a track record all contribute to in-line inspection run success in this increasingly important medium.
KEYWORDS: CO2, CCUS, ILI, pipeline integrity, repurposing, testing
Lewis Barton
ROSEN UK, Newcastle, UK
In-Line Inspection (ILI) is widely used to monitor pipeline conditions, identify and size defects, and meet regulatory requirements. However, alternative approaches for ‘non-piggable’ pipelines are needed where ILI is not feasible. In these cases, knowledge-based models relying on data, engineering assessments, and assumptions are required.
External Corrosion Direct Assessment (ECDA) is a process where variables believed to contribute to corrosion are combined with above-ground surveys or computational modeling to identify corrosion ‘hotspots’ for in-field investigation. However, these techniques have several known limitations, leading often to wasted excavations and lingering uncertainty
To enhance the direct assessment process, ROSEN has incorporated predictive analytics from its Integrity Data Warehouse (IDW). The IDW contains data from over 26,000 in-line inspections, covering more than 620,000 miles (1,000,000 kilometers) globally. These data provide significant improvement in predictive capacity and the likely condition of pipeline assets across all diameters, pressures, and fluids.
ROSEN has also begun incorporating Large Stand-off Magnetometry (LSM) into its direct assessment approaches. LSM detects changes in the magnetic signature of the pipeline that correlate with increased stresses, enabling the detection of a wide range of stress-raising anomalies and defects. This adds another layer of information, allowing for the greater confidence in the identification of potential excavation sites.
This paper provides a detailed overview of the new process and the improvements made through the addition of LSM and the integration of the IDW.
Rafael Wagner Florencio dos Santos1, Thomas Gabriel Rosauro Clarke2, Henrique Tormen Haan de Oliveira2, Alberto Bisognin2
1Petrobras, Rio de Janeiro, Brazil. 2UFRGS, Porto Alegre, Brazil
This paper presents the development and field testing of an innovative submersible guided wave monitoring system designed for the integrity assessment of subsea pipelines. The research addresses the critical need for non-intrusive, long-range inspection techniques in offshore environments.
The study focused on creating a robust electromagnetic acoustic transducer (EMAT) collar capable of operating in submerged conditions and through pipeline coatings. Through iterative design and testing, we developed a sensor configuration that optimizes signal generation and reception while maintaining functionality under high-pressure environments.
Key aspects of the research included:
The field trials validated the system’s capability for underwater installation and operation, with divers reporting ease of handling and rapid deployment. The collar’s design allowed for both wet-mate and dry-mate electrical connections, offering flexibility in installation methods.
Results from the field tests showed that the developed system could effectively distinguish defects and the performance indicates the potential for early detection of pipeline integrity issues in subsea environments.
This research represents a significant advancement in subsea pipeline monitoring technology, offering operators a non-intrusive, long-range inspection tool capable of continuous integrity assessment. The system’s ability to function through coatings and in submerged conditions addresses key challenges in offshore pipeline maintenance.
This paper provides valuable insights into the development and real-world application of guided wave technology for subsea pipeline integrity management, demonstrating its potential to enhance safety and efficiency in offshore operations.
Brett Davis1, Brian Patrick2, Liyu Wang1, Heather Watson1, Ted Zirkle3, Alexander Hudgins1, Yash Bhargava1
1Exponent, Menlo Park, USA. 2Pacific Gas & Electric, San Ramon, USA. 3Exponent, Philadelphia, USA
This work is motivated by the regulations in 49 CFR § 192.712(e)(2)(i)(E) that allow for use of “other appropriate values” to provide conservative Charpy V-notch (CVN) toughness estimates for crack-related conditions of pipeline segments in the absence of direct laboratory test data for the subject segment. This work extends previous efforts by investigating pipe features and characteristics (e.g., installation date, and seam type) that can inform the statistical determination of conservative CVN estimates for a given data set. Database sampling, documented trends in manufacturing and mechanical properties, and statistical analysis are leveraged to examine the significance of factors related to CVN measures. Results show that pipe vintage and seam type are two factors with correlation to CVN, which can be used for clustering and statistically evaluating a large material testing database. Furthermore, clustering analyses of a material testing database are used to evaluate the relationship of various pipe characteristics including vintage, seam type, pipe geometry, and chemical composition to CVN toughness of gas transmission line assets.
KEYWORD(S): Fatigue, strain, strength, toughness studies and management; Materials identification, verification; Charpy V-notch (CVN); Fracture mechanics; Engineering critical assessment
Benjamin Nowell, Thomas Dessein, Daryl Bandstra
Integral Engineering, Edmonton, Canada
Many North American operators are currently evaluating options to blend hydrogen into their natural gas systems. The introduction of hydrogen may impact the long-term structural integrity of steel pipelines, with particular influence on crack-like anomalies due to embrittlement of the steel and increased fatigue crack growth rates. Crack-like anomalies such as those found in seam welds should be assessed for hydrogen-blended service with a crack assessment model capable of handling low toughness failures such as API 579 or the PRCI MAT-8 model, with proper adjustments to account for the effects of hydrogen.
This paper illustrates the limitations of conventional fatigue assessment methods when assessing integrity and risk of crack-like anomalies in blended hydrogen service and provides a technical review of factors influencing the assessment. This includes a summary of suitable assumptions regarding the variability in pipe strength and vintage seam weld toughness properties, the expected density, depths, and lengths of the population of defects expected on uninspected pipelines, and a comprehensive review of historical mill test pressure requirements. A range of example analysis cases are presented to demonstrate the impact of embrittlement and accelerated fatigue crack growth rates due to hydrogen, and how this is affected by the operating conditions of the pipeline, such as the pressure loading history, current stress levels, and historical mill pressure tests.
h3 class=”paperno”>259
Rafael Wagner Florencio dos Santos1, Miguel de Andrade Freitas2, Lucas Braga Campos3, Guttemberg Coelho Da Silva2, Cesar Giron Camerini3
1Petrobras, Rio de Janeiro, Brazil. 2PUC-Rio, Rio de Janeiro, Brazil. 3UFRJ, Rio de Janeiro, Brazil
This paper describes the development of an instrumented pig that accommodates the diameter variations expected in sections of cladded rigid pipelines to ensure the detection of cracks in the cladded layer at the weld region of these pipelines, before the crack penetrates through and the carbon steel is exposed to the highly corrosive fluid. This development was motivated by the absence of a similar solution in the market to meet the demand. The benefits to be gained from using this pig include the optimization of operational availability through the mitigation of early failures or the extension of pipeline service life, and the reduction of inspection costs in the event of failure and the need for comprehensive assessment, as no vessels will be required.
The general methodology applied to this project can be described in four steps:
1. Development of a bench simulation of the pipeline, with cladded materials and liners containing artificial defects. Various activities were initiated from this bench, such as: mechanical design, electronic design, software development, execution of more complex tests, and simulation and processing of eddy current signals;
2. Prototype manufacturing, including fabrication, assembly, and laboratory testing;
3. Execution of full-scale tests, where field conditions are simulated, allowing the prototypes to be developed as close to reality as possible; and
4. Execution of real field inspections, with the issuance of reports and technical certificates.
This paper will present the results obtained throughout the project.
Jason Edwards1, Simon Slater1, Ann Reo2, Sean Moran3
1ROSEN, houston, USA. 2Williams, Tulsa, USA. 3williams, Salt Lake City, USA
Managing the threat of hard spots has been on the agenda of pipeline operators for several years. It is fair to say that the industry understanding of what hard spots are, how they are formed and how we can manage them has advanced rapidly but is still evolving. The industry knowledge has been recognized by PHMSA and an advisory bulletin was issued discussing the threat of hard spots. Industry now has a good feel for the susceptibility of different pipe types and vintages, and there is good appreciation that not all hard spots are the same and variations in morphology result in different types of hard spots and different ILI signal patterns. The current status is predicated on the significant amount of validation work that operators are performing in response to ILI. However, the industry is not standing still, and since the last PPIM conference more information has become available that has led to further improvements. This presentation discusses the recent experience, bringing together the latest results from ILI, non-destructive testing and research activities to continually advance assessment methods for managing the threat of hard spots.
Pablo Cazenave, Katina Jimenez, Ravi Krishnamurthy
Blade Energy Partners, Houston, USA
In March 2019, the U.S. Pipeline and Hazardous Materials Safety Administration (PHMSA) issued a Research Announcement to improve the detection and sizing accuracy of In-Line Inspection (ILI) systems for critical pipeline anomalies, aiming to improve safety and reduce unnecessary excavations. In response, Pipeline Research Council International (PRCI) launched Project NDE-4-19 in December 2019, a multi-phase initiative in collaboration with PHMSA and Blade Energy.
The project brought together Pipeline Operators, ILI Technology Providers (TPs), and Subject Matter Experts to assess and improve ILI system capabilities for challenging corrosion features. A data-driven approach was used, in which recent Root-Cause-Analysis (RCA) reports of corrosion-related pipeline failures were analyzed and a pipe test string was designed with complex corrosion profiles resembling those associated with the failures. The manufactured corrosion features were documented using advanced non-destructive evaluation (NDE) techniques.
Three ILI TPs tested their tools on the designed pipe test string in a series of blind pull-through tests. Following initial evaluations, the TPs received feedback on detection and sizing gaps and were provided with detailed 3D corrosion profiles to guide their improvements. A second round of tests measured the enhancements in detection and sizing accuracy, identifying improvements and remaining challenges.
This paper presents the findings from this 3.5-year long project, highlighting advancements in ILI technology and ongoing gaps in detecting and sizing problematic corrosion profiles.
KEYWORDS: Pipeline Integrity, ILI Validation, ILI Improvement, ILI detection capability, ILI sizing accuracy, corrosion integrity evaluation.
Gerardo Chavez1, Johannes Spille1, Keila Caridad2, Alvaro Vega2, Neil Shortt3, Aaron Schartner3
1ROSEN, Houston, USA. 2TCE, CDMX, Mexico. 3TCE, Calgary, Canada
Offshore pipelines pose unique challenges to their integrity management, particularly when standard in-line inspection tools cannot accommodate their complex conditions, such as heavy pipe walls, high pressures and high medium flows. The Sur de Texas-Tuxpan (SdTT) pipeline is a 42-inch natural gas system with two offshore segments spanning 310 miles (498 km) and 156 miles (251 km), wall thicknesses up to 1.8 inches (45 mm), pressures up to 1,700 psi and flows up to 10 mph that required innovative solutions beyond conventional inline inspection tool designs to perform a successful inspection.
To meet these challenges, ROSEN developed a custom ILI tool that combined Axial Magnetic Flux Leakage technology with Internal Eddy Current technology (IEC) in a single tool configuration. This tool was optimized for thick-walled pipelines, capable of detecting and sizing internal and external anomalies under high-pressure and high-flow conditions. A key enhancement was the Speed Control Unit (SCU) to maintain a consistent (slow) tool velocity ensuring optimum data quality.
Extensive simulations and validation tests have been performed to optimize magnet strength, brush configuration and speed controlling capabilities to tackle the three main challenges: heavy pipe wall, high pressure and high flow.
This paper presents the technical solutions and lessons learned from the SdTT project, highlighting the challenges and efforts to ultimately achieve a successful inline inspection. The advancements in ILI tool design provide valuable insights into managing the integrity of heavy wall offshore pipelines.
Rhett Dotson1, Liam Hagel2, Jing Wang2, Rob Greene1
1D2 Integrity, Houston, USA. 2TC Energy, Calgary, Canada
Over the past decade operators have used curvature-based strain assessments to assess the likelihood of cracking associated with dent formation in natural gas pipelines. Accurate curvature-based dent strain assessments require that the dent shape is captured with a high-resolution caliper tool, where high-resolution is defined by the number of sensors around the circumference of the pipe. However, the use of a high-resolution caliper tool can be infeasible due to restrictions such as multi-diameter passages, internal obstructions or small diameter. This paper presents a case study where multiple inspections were performed in an 8-inch line using low-resolution caliper tools. The initial conservative estimates of the dent strain identified a significant number of dents with exceptionally high strains. A multi-step process was developed to improve the dent strain assessment. First, methodologies to estimate upper and lower bound strains based on a single data set are presented. Next, a methodology is developed and presented to combine the low-resolution data sets from multiple inspections. Finally, the paper compares these results from the first two steps with the results of optical scans performed on excavated dents and the results of numerical analysis. This paper will be helpful for operators who have inspection scenarios that are limited to low-resolution caliper tools or may not have high-resolution data available.
Xuejun Huang, Bryan Feigel, Aidan Ryan, Intisar Rizwan I Haque, Ryan Lacy, Simon Bellemare
Massachusetts Materials Technologies, Natick, USA
The toughness of pipeline materials, particularly in fracture toughness, is important for assessing the fitness-for-service of pipelines. With the advent of ultra-high resolution inline inspection (ILI) tools, the demand for fracture toughness data has risen. Current approaches to obtain fracture toughness include performing cutouts and destructive testing, leveraging existing databases, and nondestructive evaluation (NDE). A previous PPIM paper demonstrated an innovative NDE method called planing-induced microfracture and validated the method for estimating fracture toughness using a lab prototype. Based on this successful validation, a portable field tool, Blade Toughness Meter (BTM), has been developed. Compared to the lab prototype which cuts and splits small specimens at the center, the field instrument can be directly attached to a pipe to perform surface preparation and testing. The instrument first creates raised testing surfaces by machining called “islands” on the pipe surface and then planes these islands with specially designed blades with a central opening. A true microcrack is introduced at the surface of the pipe and ligaments left on the chip and substrate are scanned. An in-depth characterization of the ligament profiles reveals features that exhibit varying degrees of correlation to fracture toughness. The fracture surface was also examined using a scanning electron microscope (SEM), which allows for a qualitative assessment of whether the material is ductile or brittle. Fracture toughness prediction models have been built using the outcome of BTM testing together with other material properties, showing accuracies of approximately ±20% comparing to lab-tested values. This paper will summarize the fundamental basis for the test, present details on the material response including fractographic evaluation and characterization of the fractured ligaments, and provide validation results. These findings may be used to evaluate the technology readiness for initial implementation as part of integrity programs.
David Cockfield
Pipeline Innovations Ltd, Cramllington, UK
Pathfinder is a soft foam bodied pipeline caliper tool capable of passing through a 40% reduction in the nominal pipeline bore. When it was time to inspect a critical pipeline constructed back in 1960, that had never been pigged before, was subject to modification in between time, and, with no original pipeline construction data, the operator needed a low-risk approach to prove piggability prior to implementing their ILI campaign. Crossing the Appalachian mountains like a rollercoaster, the last thing they wanted was a lost or stuck pig.
This paper outlines the pigging strategy and practice employed to ensure successful pipeline preparation ahead of metal loss inspection in 64-year-old pipeline that had never ran a pig. Using the Pathfinder foam bodied caliper tool to provide a baseline geometry survey supporting initial bore proving and debris mapping, identified, sized and located a lot of unknown and unexpected features and anomalies, including over 70 dents, several hundred bends and significant areas of debris build up. The survey data was used to provide assurance for pre-inspection cleaning pig selection, provide piggability assurance and qualify line cleanliness as part of the operators pipeline pigging strategy prior to running a metal loss inspection.
The presentation demonstrates the effectiveness of a progressive and innovative approach using a foam bodied caliper tool to qualify pipeline proving and cleaning resulting in a flawless ILI survey, executed safely without any unplanned operational deferment or constraint.
Patricia Varela, Alexander Mckenzie-Johnson
Geosyntec Consultants, Inc., The Woodlands, USA
Landslides are present in every state of the USA and every province in Canada, and the extensive transmission, distribution, and gathering pipeline network is vulnerable to impacts from landslides, including pipeline rupture. Based on PHMSA statistics, landslides are one of the most expensive causes of pipeline rupture and result in more onshore pipeline ruptures than all other natural force incidents combined. For these reasons, considerable focus has been put on managing landslide hazards, such as PHMSA advisories ADB-2019-02 and ADB-2022-01, and the recently released API RP 1187. The traditional framework to address landslide hazards, as summarized in API RP 1187, starts with a system-wide desktop screening of geohazards (Level 1) and ends with site-specific detailed investigations (Level 3).
To enhance the desktop Level 1 Assessment process, Geosyntec has partnered with several North American pipeline operators to develop three novel methods to produce landslide susceptibility maps and inform decision-makers about the exposure to this geohazard. These landslide susceptibility methods not only map existing landslide hazards as is traditionally performed at Level 1 as described in API RP 1187, but they also predict areas that may be more likely to experience future landslide activity in response to forcing events, such as significant precipitation (e.g., rainfall or snowmelt) or topographic change (such as from naturally occurring erosion or construction). These methods use various combinations of high-resolution LiDAR, soils, and geologic mapping produced by public agencies and subject matter expert (SME) input. This paper discusses these three methods, which combined to date, have been implemented along more than 18,000 miles of pipelines in the United States and Canada. Additionally, this paper discusses how the resultant landslide susceptibility maps are and can be used to design or refine pipeline management practices, such as pipeline integrity assessment, budgeting, risk modeling, and construction planning.
Lautaro Ganim1, David Classen1, Oscar Gualdron2, Jaime Aristizabal2, Edwin Moreno1
1Baker Hughes, Houston, USA. 2CENIT, Bogota, Colombia
Nowadays the use of inertial measurement unit (IMU) derived bending strain data to identify and assess pipeline movement events due to geohazards has become a standard process. Service providers and operators should also be aware of the limitations of this process and the complementary analysis that is required or necessary to provide a complete picture of the threat. Understanding the results of the IMU bending strain analysis (pipeline movement included) and going further to obtain a deep knowledge between what is shown in the graphical information and what is occurring in the pipe-soil interaction makes a real difference. For this reason, the interaction between pipeline operator and In Line Inspection (ILI) service provider is a crucial part of effective geohazards management.
In this paper, two case studies will be presented where the complexity of geomorphological conditions interacting with the pipeline dictates that more comprehensive investigation and assessment methods are necessary to ensure effective understanding of the pipeline condition and the impact of geohazards. Oil transportation through a mountainous region is a challenge, even more so if there are areas with known active landslides, extreme weather conditions and earthquakes. The use of special construction and mitigation techniques, like casings, supports or even concrete structures could lead to a more complicated scenario compared with a pipe-soil interaction only.
The first case study describes a section of a pipeline under a special type of casing built to mitigate pipe-soil interaction in an area with known landslide occurrences and monitored by the operator to identify and measure ground movement. Thanks to an expert assessment and additional interpretation of the strain plots combined with the use of high-resolution reporting thresholds, the extension of the displaced area was accurately correlated and measured. This specific case led to an improvement in the analysis process.
The second case study involves a pipeline running through the toe of a hill with no report of geotechnical activity (taking other inspection techniques into consideration) or need for any mechanical remediation. However, two wrinkle-type anomalies were reported by the ILI geometry analysis. After a detailed review of the tool angle variation from previous inspections, the nature of these anomalies was compared to the kinematics of ground movement, and the wrinkle-type anomalies were verified, with an axial load component, in subsequent on-site inspections.
Shenwei Zhang1, Rick Wang2, Ji Bao3
1TC Energy, Calgary, Canada. 2TCEnergy, Calgary, Canada. 3Pembina, Calgary, Canada
Mechanical damage poses a significant safety risk to the structural integrity of oil and gas steel pipelines. Fatigue due to cyclic loading is one of leading causal factors to failure for pipelines, particularly for oil pipelines, subject to mechanical damage in the form of dent or dent with gouge. Many fatigue assessment models were developed and published in the industry to evaluate the remaining life of dented pipelines. These models include the API 1156 model, EPRG 1995 and 2000 models, Petrobras model, BS 7608 model, API 1183 screening and assessment models as well as some most recently developed models through the PRCI projects. The objective of this paper is twofold. Firstly, it provides an overview of the existing models and the comparison of these models through parametric analysis. Secondly, it presents the accuracy and precision of these models by comparing the predicted fatigue life and the experimental fatigue life. The study reported in this paper will facilitate the application of the fatigue assessment models and benefit operators for optimizing their integrity management program of pipelines subject to mechanical damage.
KEYWORDS: pipeline, mechanical damage, dent, gouge, fatigue
Christopher Davies, Johannes Spille, Simon Slater
ROSEN USA, Houston, USA
Managing the assorted threats associated with pipelines is an evolving process. Selective seam weld corrosion (SSWC), while not a new threat, is now receiving increased scrutiny amid existing and new regulatory requirements.
SSWC tends to have a complex morphology, with a relatively high length-to-width ratio compared to general corrosion and a localized area of maximum depth described as a V-shape. SSWC creates a significant risk for operators because it is more difficult to detect, classify, and size using established in-line inspection (ILI) technology. Furthermore, well-established methods to assess the severity of the corrosion may not be appropriate. Operators often manage the threat through a combination of low specificity ILI assessments and in-ditch validation. However, when many ILI metal loss indications coincident with the longitudinal seam weld are identified, establishing an effective and efficient response can be challenging.
Over the past two years, a significant body of data from ILI, field excavations and metallurgical verification has been captured to evaluate and help improve technologies for detecting and characterizing SSWC. In combination with updated regulatory requirements and inspection specification improvements, this has brought renewed attention to the question of how the threat of SSWC can be managed.
This paper highlights the results of recent pull tests used to help develop an improved performance specification for the circumferential magnetic flux leakage Ultra tool (MFLC Ultra) currently offered to more effectively manage the threat of SSWC. Examples illustrate how collaborative efforts performed by operators have been used to refine probability of detection (POD) and probability of identification (POI), with a focus on differentiating SSWC from coincident corrosion crossing the long seam.
Leveraging existing guidance regarding the management of the threat of corrosion on the long seam, this paper also presents the results of extensive nondestructive and destructive testing of validated SSWC anomalies. The goal is to share learnings and discuss the considerations for assessing these anomalies in order to identify an appropriate response based on all the information available to the operator.
Simon Slater1, Christopher Davies1, Sean Moran2
1ROSEN USA, Houston, USA. 2Williams, Salt Lake City, USA
Since the introduction of guidance pertaining to Engineering Critical Assessment (ECA) in gas regulation, operators have been grappling with exactly what is required to complete an ECA and the question of what good looks like? Over the past few years, there has been intensive discussion between the regulator, operators and service providers. This open dialogue and collaboration, combined with operators actively working on ECA’s, has paved the way for a clearer understanding of what is required. The regulatory language has been digested to define a transparent laundry list of tasks and data requirements required to close an ECA. Engagement with the regulator has helped add color to the outlines given in regulation, with appreciation on the timelines and milestones expected to complete an ECA. There are several significant tasks that require focus early in the process to establish a successful path, and planning is key. This paper will discuss the current and established route for ECA’s used to reconfirm MAOP and conclude by identifying when an ECA can be considered complete and taken credit for in relation to the deadlines of 50% of 192.624 covered segments by 2028 and 100% by 2035.
Michael Rosenfeld1, Bill Amend1, Simon Slater2
1RSI Pipeline Solutions, New Albany, USA. 2ROSEN USA, Columbus, USA
Pipe body hard spots have been recognized as a pipeline integrity threat in certain types of vintage line pipe, causing ruptures, leaks, and near-miss events. Hard spots can now be managed within the template of Integrity Management, including susceptibility and threat assessment, whether and when to perform a baseline assessment, in-line inspection, prioritization of assessment response, field examination, acceptable hardness limits, repair decisions, reassessment decisions, and mitigations. This paper discusses key factors, recommendations, and pitfalls to consider in the integrity management process. However, industry knowledge and experience is evolving, and important gaps remain. Areas for further development to address current knowledge gaps are also discussed.
KEYWORDS: Hard spots, vintage pipelines, integrity management, threat assessment
Sheri Baucom
OneBridge Solutions, Durango, USA
With over 11,000 assessments on 400k miles of pipeline from 18 pipeline operators and 34 inline inspection (ILI) service providers, OneBridge Solutions (OBS) has amassed the largest and most diversified set of ILI data in the industry. This paper presents insights gleaned from the analysis of said ILI data, with the focused aim of determining what variables contribute to high ILI system performance i.e. ILI service provider, ILI technology, pipeline operator, product, experience of the ILI service providers, etc. These insights are presented to achieve the foremost goal of shared learnings amongst all stakeholders and provide valuable information that pipeline operators can utilize to improve their pipeline integrity program.
Simon Slater, David Bastidas
ROSEN, Houston, USA
The energy transition has gathered momentum stimulating the natural gas industry to swiftly adapt to the evolving energy ecosystem, driven by the need to reduce carbon footprint and seek alternative fuels like H2. In the last five years, there has been a significant increase in industry focus and research within the natural gas and hydrogen pipeline sectors. Gaps have been identified in the current technical standards for repurposing of natural gas pipelines for hydrogen gas. Neither ASME B31.8 nor ASME B31.12 effectively address the issues faced by transmission and distribution pipeline operators seeking to integrate hydrogen gas into the existing natural gas infrastructure. In this regard, Consensus Engineering Requirements (CERs) have been elaborated to provide practices for H2 and H2 blends pipeline services, aiming to be the basis for new guidance within ASME B31.8 code. The intent of the approach is to provide a robust analytical method for users to qualify pipelines for safe operation in H2 commensurate with the asset specificities, alongside operational envelope, rather than using prescriptive approaches. This paper will discuss the guidelines created for repurposing within the CERS, which are proposed for inclusion in the 2026 version of ASME B31.8.
Carlos Diaz, Rick Desaulniers
ENTEGRA, Indianapolis, USA
Hard spots are typically associated with older pipelines. A recent joint industry research initiative, however, is revealing that hard spots may occur in a wider variety of pipeline vintages, sizes and manufacturing sources than previously thought.
Hard spots can pose a major threat in pipelines, and some have led to dangerous ruptures. Legacy ILI technology was unable to detect hard spots or characterize them with confidence. Inconclusive data might mean hardness is underestimated, leaving pipes unexpectedly vulnerable to cracking in the presence of other corrosive factors. This can be especially concerning as many lines transition to hydrogen transmission.
Carlos Diaz, ENTEGRA Account Manager, and Rick Desaulniers, ENTEGRA Chief Data Scientist, will discuss preliminary findings from this joint research program, which was undertaken in partnership with multiple operators and utilized the Pipeline Research Council International (PRCI) technology center.
They’ll showcase how the ENTEGRA® Ultra High Resolution (UHR) ILI system aids in detection and detailed characterization of hard spots, including assigning more accurate Brinell ratings. They will also share the importance of looking for hard spots in pipes that aren’t often associated with this anomaly, explore how this project uncovered different types of hard spots, and how the findings from this research may lead to changing protocols for hard spot detection.
KEYWORD(S): ILI Analysis, Hard Spots, Pipe Vintage, Manufacturing Anomalies, Emerging Research
Omar Al Ghamari, Madjid Afshari
OQGN, Muscat, Oman
OQ Gas Networks (OQGN) is the exclusive operator of Oman’s natural gas transportation system comprising a network of around 4,500 Km of pipeline that supply gas as fuel and feedstock to many customers across Oman. One of OQGN pipelines, is a 10" pipeline that is crossing the capital city (Muscat) to one of the customers in high population area. The pipeline was commissioned in 2007, with a total length of 40 Km. Throughout the years, the pipeline has been suffering from external corrosion which resulted in a deration from 92.0 Barg original design to 66.0 Barg. All the locations affected by external corrosion are located at the field joint area due to Heat Shrink Sleeve failure.
Since construction in 2007, the first heat shrink sleeve failure was observed on 2014 ILI, that is after 7 years in operation only. The corrosion rate of those defects various from one location to another, however the maximum localized corrosion rate was calculated approximately 0.3 mm/y. As the pipeline has a low thickness of 4.6 mm, operating the pipeline with this corrosion rate make it critical in terms of inspection, integrity assurance and repair strategy.
Since 2014, a total number of 4 ILI runs were done. Analyzing defects growth based on consecutive runs didn’t show any trend as corrosion rate was not linear and even in some cases no growth detected therefore corrosion growth rate is difficult to predict. The used heat shrink sleeve material was approved as per ISO 21809-3 system 14B (cross-linked heat-shrinkable polyethylene-based material). While the same product has been applied in other pipelines, only this pipeline suffers from premature HSS failure mainly due to application qualification issues.
Subject pipeline protected by impressed current cathodic protection however, the disbandment of HSS results in a creation of corrosion cell beneath the coating, and as PE is shielding the CP current, no protection provided to the pipeline, hence, the pipeline is experiencing accelerated soil corrosion rate.
This paper is focusing on the current approach that OQGN is adapting to maintain the 10" mechanical integrity by interfacing both ILI frequency optimization, corrosion rate monitoring and field joint coating rehabilitation program.
KEYWORDS: Pipeline ILI, Heat Shrink Sleeve Failure, Pipeline Repair, Defect Assessment, Coating Rehabilitation
Anthony Tindall1, David Classen2
1Baker Hughes, Cramlington, UK. 2Baker Hughes, Houston, USA
Magnetic Flux Leakage (MFL) inspection was the first technology introduced in the 1980’s to routinely inspect oil and gas pipelines for corrosion defects, and today it remains the most trusted In-line Inspection (ILI) technology for that purpose. Thousands of MFL inspections are carried out by ILI vendors each year ensuring pipeline operators can effectively manage their corrosion integrity programs.
Since the introduction of high-resolution axial MFL inspection vehicles, there has been a substantial number of improvements in capabilities. These include inertial mapping units (IMU), speed control, increased sensor density and combination sensing (caliper, eddy current, transverse MFL and triaxial MFL measurement).
Even with these advances, surprisingly most MFL inspections only measure and use one of three components of magnetic flux field leakage that occur at a corrosion feature when magnetized by the inspection tool at a localised thinning of the pipe wall. However, it is well proven that different corrosion morphologies will trigger significantly different leakage in these components. These characteristic signatures consequently provide an additional and robust means to identify corrosion profiles and interactions that in many cases are not detectable or distinguishable when using only a single axis – no matter how high the sensing resolution the inspection tool may have. Optimising sensor resolution in combination with measuring all three leakage components offers clear advantages, particularly when defect morphologies become challenging.
This paper will provide a deeper insight as to how the three independent leakage components provide unique identifiers that can be used to accurately size pin holes, axial and circumferential slotting, and importantly de-construct complex morphologies and be used more effectively in the analysis process to improve POD, POI and POS. These identifiers not only ensure correct corrosion interpretation, but also that these defect types are identified correctly within the often hundreds of thousands of features within many miles of pipeline.
The paper will conclude with a demonstration of how, in combination with monitoring of data accuracy for every validated inspection conducted, the adoption of data accuracy results as a key performance indicator can be effectively employed to target and drive continuous improvement of even the highest performing inspection technologies.
Arnav Rana1, Sanjay Tiku1, Ali Roostaei1, Behrouz Shiari1, Vlado Semiga1, Aaron Dinovitzer2, Munendra Tomar3, Yohann Miglis4, Mark Piazza5
1BMT Canada, Ottawa, Canada. 2ADIM Consulting, Ottawa, Canada. 3TC Energy, Houston, USA. 4Kinder Morgan, Houston, USA. 5API, Washington DC, USA
Dents or mechanical damage in buried pipelines can occur due to a number of potential causes; the pipe resting on rock, third party machinery strike, rock strikes during backfilling, amongst others. The long-term integrity of a dented pipeline segment is a complex function of a variety of parameters including but not limited to pipe size, indentation depth, dent or indenter shape, indenter support, pressure history at and following indentation. Operational experience and regulatory oversight have identified mechanical damage as a significant threat to pipeline integrity. In response to this threat, industry has sponsored mechanical damage research (i.e., PRCI, US DOT PHMSA, CEPA, and others) and industry lead by the American Petroleum Institute (API) developed a recommended practice for managing pipeline mechanical damage (API RP 1183). The first edition of API RP 1183 was assembled and published in 2020 by drawing together industry experience and engineering tools available at the time recognizing that improvements would be possible. With use, opportunities for improvement in API RP 1183 have been identified and thus a second edition of the recommended practice is being considered at this time.
This paper is offered to discuss the opportunity for improvement (OFI) observations that have been offered in the open literature related to the tools and techniques presented in API RP 1183. The observations are related primarily to the recommended practice (RP) restraint condition, indentation strain and fatigue screening and analysis tools. The paper will address a range of OFI’s, including but not limited to:
The objective of this paper is to provide engineering or science-based answers to the questions raised related to API RP 1183 mechanical damage management procedures and demonstrate while there are opportunities for improvement, the engineering tools presented in API RP 1183 provide a sound basis for mechanical damage management in pipelines.
Kachi Ndubuaku1, Brendan Eirich2, Kristian Olsen3
1Enbridge, Edmonton, Canada. 2ATCO, Edmonton, Canada. 3Stantec, Edmonton, Canada
Mild ripples may be introduced in pipelines prior to installation, during the process of forming field bends. Wrinkles/buckles may also develop in pipelines under monotonic displacement-controlled loading conditions, such as permanent ground deformation. Many pipeline industry codes define the acceptability of surficial deformations in energy pipelines based on generic serviceability limit criteria such as adverse effects of wrinkles on the integrity of pipe coating or impairment of in-line inspection. However, the codes do not provide explicit guidance on the acceptance standards with regards to the effect of surficial deformations on the structural/mechanical performance and long-term integrity of pipelines. A powerful transformation tool is presented in this paper to approximate the deformed centerline profile, as well as surface deformities, of pipelines using high-resolution ILI IMU/caliper data. The tool provides interactive 3D visualization of the deformed pipeline therefore allowing proper categorization of the observed deformities, and also evaluates the longitudinal and circumferential bending strains over the full pipeline surface. The tool also generates the 3D surface mesh needed as input for more advanced finite element analysis (FEA), including pipe-soil interaction properties required to properly simulate buried conditions if applicable. Ultimately, a systematic approach is outlined herein for using the analytical strain estimates generated by the transformation tool, combined with the results of FEA, as input for performing level 3 fitness-for-service fatigue-life assessment of wrinkled pipelines.
Rick Wang
TC Energy, Calgary, Canada
Pipeline dents, caused by external indenters applying force to the pipeline surface, are a major integrity concern due to their potential to cause immediate or delayed failures, depending on their severity, operating conditions, and other factors. Traditionally managed by In-Line Inspection (ILI) tools, evaluating and prioritizing critical injury dents that require immediate action remains challenging. This paper presents a practical assessment approach for operators, combining a dent strain-severity criterion with Magnetic Flux Leakage (MFL) signal recognition to identify dents with corrosions, gouges and cracks. Additionally, an enhanced method for distinguishing between plain dents and those with gouges or cracks, particularly for topside dents, is discussed. Case studies are provided to demonstrate the effectiveness of this approach in identifying critical injury dents that necessitate immediate investigation.
Travis Cust1, Neil DeVetten2
1Quest Integrity, Calgary, Canada. 2TC Energy, Calgary, Canada
Small-diameter, difficult-to-inspect, or unpigable pipelines have limited inspection options in their Integrity Management tool kit. When the threats of concern are cracking-related, such as Stress Corrosion Cracking (SCC), the available options are usually limited to Hydrotest or Direct Assessment (SCCDA). This paper presents a case study on the pivotal role that bidirectional tethered In-Line Inspection (ILI) tools can bring to pipeline integrity programs. It will provide an overview of a recent tethered inspection of an 11.9 km NPS10 lateral natural gas pipeline, employing multiple cut points and a bidirectional EMAT (Electromagnetic Acoustic Transducer) ILI tool.
Designed for pipeline operators, integrity engineers, ILI coordinators, planners, and construction managers with intermediate to advanced technical expertise, the session will first address the operational challenges that bidirectional tethered ILI solutions can effectively resolve. Following this, the EMAT technology and its application in performing a multi-cut point bidirectional tethered inspection will be reviewed, along with the challenges encountered during the process and the key lessons learned. This examination aims to provide actionable insights and advancements in pipeline inspection technology utilization and threat detection.
KEYWORDS: EMAT technology, “Unpiggable” inspections and technologies, SCC assessment and management
Xavier Ortiz, Sean Prestie
Imperial Oil Ltd, Calgary, Canada
Pipeline operators face several challenges during the implementation of a seam cracking integrity management program (IMP). Some of these challenges are related to improving the confidence on NDE dig data, ILI tool data analysis and crack sizing, and implementing crack assessment methodologies under a risk-based assessment framework. Overcoming those challenges is key for the development of an effective and efficient dig program and long-term asset management strategy.
As part of the seam cracking IMP enhancements, Imperial Oil Ltd used a new and innovative crack detection tool that was developed and recently presented by ExxonMobil at the 2024 European Pipeline Technology Conference. Although the new ILI tool has shown to be highly accurate, the success of the enhanced seam cracking IMP was the result of the implementation of supporting integrity programs to ensure the right information and assessments were being used.
This paper and presentation will discuss the steps that were followed for the implementation of a successful ERW seam cracking IMP. Details about the new ultrasonic ILI technology with consistent and reliable tip diffraction sizing capability, the implementation of a structured NDE and validation program, the deterministic and probabilistic evaluation of reported seam weld anomalies using the PRCI MAT-8 methodology, and the implementation of a risk-based approach for dig selection and definition of a long-term seam cracking management plan, will be included in this document.
Katherine Hartl, Christoph Jaeger, Santiago Urrea, Christoph Seeber
NDT Global, Stutensee, Germany
In pipelines experiencing significant corrosion growth, frequent wall thickness measurements using In-Line Inspection (ILI) are beneficial. This paper defines ‘frequent inspections’ as those conducted less than a year apart. Increasing the frequency of these measurements allows for rapid assessment of mitigation measures’ effectiveness without the need for costly excavations. Ultrasonic ILI data enables evaluation on both a feature-specific and global scale. As corrosion rates decrease due to effective mitigation, inspection intervals can be extended. This paper explores three case studies at different stages of this approach.
The first case study addresses channeling corrosion, where frequent inspections were conducted until a reduction in corrosion growth rates was observed. The second case study examines pinhole corrosion, and the third case examines general corrosion. Both pipelines continue to be monitored frequently. Each case study is presented with statistical analysis of corrosion growth rates.
Additionally, operators rely on feature information spreadsheets as their primary view into the pipeline, which can be distorted by reporting practices. In the context of ultrasonic data, reporting only the deepest spot within a box may not adequately capture the extent of corrosion. This paper discusses reporting strategies for general and channeling corrosion to provide a more accurate representation.
KEYWORDS : ILI Analysis, ILI Applications, Corrosion Studies, Repair and/or Rehabilitation, Integrity Management Plans (IMP)
David Kania1, Ron Thompson2, Richard Kania3, Guillermo Solano2, Andrew Corbett2
1Novitech Inc., Calgary, Canada. 2Novitech Inc., Vaughn, Canada. 3KanEnergy Partners Inc., Calgary, Canada
The discovery of axial stress corrosion cracking (ASCC) in the 1990’s motivated the development of inline inspection (ILI) technologies capable of identifying and sizing these features with sufficient accuracy to support integrity programs. Along with ASCC, the discovery of Selective Seam Weld Corrosion (SSWC) has emerged in the past decade as a threat that sometimes exhibits crack-like behavior. In the case of both ASCC and SSWC, current ILI technologies continue to be challenged with the detection, characterization and accurate sizing of these features.
Novitech with its Micron ILI Technology® has designed and developed six primary sensor systems to address ASCC and SSWC anomalies. These sensor systems include CMFL-MF℠ (Multi-field Circumferential Magnetic Flux Leakage), AMFL-640℠ (Axial Magnetic Flux Leakage), IDD-SM℠ (Internal Depth and Stress Measurement), Micron-RF℠ (Residual Field for Crack Detection), Px2℠ (Precision Geometry Measurement) and industry standard Inertial Mapping unit.
The advanced flaw diagnostic approach with CMFL is combined with the extensive experience detecting and sizing other threats (metal loss, circumferential and off-axis cracking), demonstrating the ability to simultaneously detect, characterize and size both ASCC and SSWC threats in the same inspection campaign.
This paper explores the new CMFL-MF℠ multi-field sensor technology, which uses varying levels of magnetization with the mid-field part of the system used to mitigate the effects of flux leakage from shallow surface corrosion. By comparing the results from the full-field and the mid-field CMFL-MF℠ data, accurate characterization and sizing can be achieved.
Both the full-field and mid-field CMFL sensor systems have sampling densities of up to ١,٠٠٠ readings per square inch. When combined with the AMFL and other sensor systems the sampling density of the complete tool can exceed ٣,٠٠٠ readings per square inch.
Using the multifield CMFL approach along with the supporting data from AMFL-٦٤٠℠, high precision geometry, IDD-SM℠, Residual Field, and IMU mapping greatly improves the probability of detection (POD) and probability of identification (POI) of ASCC and SSWC, achieving very high probability of identification.
Detection and characterization of ASCC and SSWC from ٢٠٪ in depth and ١" (٢٥ mm) in axial length have been demonstrated in laboratory testing, pull testing, and in most recent live runs.
Dane Burden1, Adrian Belanger2, Ron Lundstrom1, Miguel Maldonado1
1TD Williamson, Salt Lake City, USA. 2TD Williamson, Houston, USA
The evolution of in-line inspection (ILI) tools over the last six decades has provided pipeline operators with continual growth of integrity management capabilities. While the core physics of many of these systems have remained fundamentally unchanged, there has been a significant progression from single-technology solutions to sophisticated, multi-technology frameworks. The last decade has increasingly enabled the integration of multiple, high-resolution sensor systems and coupled them with advanced digital technologies such as machine learning and artificial intelligence.
This paper will explore the progression of multi-technology ILI tools combined with the implementation of advanced computing techniques and how they have addressed complex and multifaceted problems within the pipeline integrity industry. Several case studies will be presented to illustrate the current capabilities for assessing common, complex, and unique integrity threats highlighting the value they bring to operators and the industry. Among these cases will be selective seam weld corrosion, mechanical damage (i.e. gouging and restrained vs unrestrained dents), hard spots, stress corrosion cracking and pipe material properties verification. Finally, the paper will explore potential future developments, looking at emerging trends, innovative integrations, and the anticipated impact on the industry.
Jeff Haferd1, Sylvain Cornu2
1Marathon Pipe Line, Findlay, USA. 2NDT Global, Stutensee, Germany
Pipeline geohazard identification, assessment, and mitigation remain critical areas of focus in the industry, with continuous advancements across multiple technologies. Effective geohazard management exemplifies the necessity for integrating new technologies to mitigate risks more effectively. Traditional approaches to geohazard management rely on a combination of IMU (bending strain), LiDAR, InSAR, Strain gauges and deformation platforms. Recently inline inspection (ILI) vendor(s) have developed novel strain measurement technologies designed to detect and measure the external loading caused by geohazards.
This paper reviews the successful technology validation to address the threat of geohazards to pipelines. A case study of a pipeline currently monitored for geohazard activity at multiple locations is included. The pipeline was inspected using a newly developed ILI strain tool (ETEC), with a specific focus on assessing how the inclusion of axial strain data can enhance the overall geohazard management program. The current program utilizes ground surveys, Lidar, ILI IMU bending strain, and strain gauge monitoring.
This review will demonstrate how the ILI strain tool data correlates to existing ILI IMU bending strain, with correlation to known geohazard sites currently being monitored using strain gauges. The ILI strain tool is capable of measuring bending strain based on curvature (IMU) and Magnetostrictive effect (ETEC). A distinction can then be made between loads induced by the environment versus those induced by construction. The subject pipeline undergoes regular inspections using ILI IMU, with pipeline movement/strain change analysis such that previous strain mitigation efforts can be assessed based on historical data. This historical data has also provided valuable insights into the pipeline’s current loading conditions.
The new ILI strain tool identified additional axial strain loading at known bending strain sites offering insights that were previously only inferable through simulation of the pipe at known bending strain areas. The second part of the review will show how the axial strain measurement identified additional geohazard locations where the bending strain was not present. The axial strain was predominantly detected over longer pipeline spans affected by landslides acting longitudinally, while bending strains were more common in shorter lengths where landslides moved transversely or oblique to the pipeline orientation.
Correlation between technologies allowed us to further refine the risk assessment across the potential geohazard sites and better estimate the strain demand on the pipeline. Finally additional correlation to known susceptible features, for example, circumferential cracks in tensile strain area, can be conducted to relate strain demand and strain capacity and help in prioritization of potential repairs.
KEYWORD(S): Geohazards, Strain, Bending, Eddy Current
Keith Leewis1, Daniel Ersoy2
1L&A Inc, Bragg Creek, Canada. 2Element Resources LLC, Princeville, USA
Previously, rule of thumb suggested that leaks only occur below 30% SMYS. Unfortunately, there have always been outliers below 30%. Catastrophic rupture conservatism was therefore assumed, and a high corresponding thermal radiation dosage in the PIR was estimated for static and non-static receptors. However, many breaches occur as leaks with a much reduced risk. This new methodology provides a reliable method to determine if the breach is a leak or rupture.
This Basic Rupture Framework (BR) methodology collapses a detailed seven-dimensional engineering analysis of more than ٣x١٠5 combinations into a simple two-dimensional plot. The BR methodology requires the operating pressure (default = MAOP) and an estimated a failure pressure (default = SMYS) to determine if the failure will be a leak or rupture. If a leak, then the BR consequence methodology will estimate a smaller, more realistic PIR and provide a better estimate of the actual consequences. This paper summarizes our PHMSA engineering report, describing how the BR Framework was developed and used to evaluate and plot >300,000 combinations of actual pipe attributes and operating conditions over decades of pipe to simplify the leak or rupture outcome.
Guanlan Liu1, Dan Rowe2
1DNV, Dublin, USA. 2NiSource, Fort Wayne, USA
Pipelines play a critical role in transporting fluids, and the assessment and mitigation of associated risks are paramount. Over the past decades, pipeline risk models have evolved from empirical, index-based approaches to more quantitative, data-driven models, providing insightful results for operators to make decisions regarding inspection, mitigation, repair, or replacement efforts. However, data uncertainty and limited data availability have consistently posed challenges in quantitative or probabilistic risk assessment models. Therefore, efficiently improving data quality and completeness becomes necessary, which requires a judicious decision on allocating limited resources for data collection efforts. To meet this goal, a sensitivity assessment on pipeline risk models becomes critical.
This research focuses on identifying and understanding the sensitivity of crucial input factors spanning from pipeline specifications to environmental conditions. A data-driven probabilistic risk assessment model was selected, and the baseline parameters were set up based on a selected pipeline. By systematically varying the model parameters in a reasonable range, and observing their impact on the likelihood of failure, the study aims to prioritize factors significantly influencing the likelihood of failure. After determining the range of the selected factors, a Monte Carlo simulation up to a million iterations was conducted with random sampling inside the defined distribution, and the correlation coefficients between these factors and the risk results were analyzed. As a result, a ranking of the criticality of these factors is summarized. Additionally, a threat-based sensitivity analysis was conducted, specifically on pipeline threats such as corrosion, mechanical damage, incorrect operation, etc., to evaluate which factor affects the likelihood of a specific threat more.
The results contribute to informed decision-making and resource allocation for risk mitigation strategies. Additionally, the research emphasizes the importance of iterative sensitivity analyses, considering uncertainties, and continuous refinement of the risk assessment model to enhance its accuracy and relevance in dynamic operational environments. The findings of this study offer valuable insights for stakeholders involved in pipeline management, safety, and regulatory compliance.
Nathan Leslie1, Jake Haase2, Jonas Butterer3
1NDT Global, Houston, USA. 2Colonial Pipeline Company, Alpharetta, USA. 3NDT Global, Stutensee, Germany
Ultrasonic Inline Inspections (ILI) have been extensively utilized by liquid pipeline operators for many years, facilitating the accurate detection, sizing, and characterization of pipeline features. Over the past two decades, significant investments in the innovation of ultrasonic ILI tools have resulted in higher data fidelity, advanced analysis techniques, and increased detection and measurement capability. However, these advancements have also led to an increase in the length of ILI tools. While many pipeline operators can accommodate the extended tool length in order to leverage these advancements, trap extensions were not a realistic option for Colonial Pipeline. To benefit from these advancements in their Integrity Management Program, Colonial Pipeline required a novel solution that could provide high-quality ultrasonic crack and metal loss inspection data without exceeding the dimensions of their existing tray-style launching and receiving traps.
This paper explores the development, testing, qualification, and application of a 36-inch combination crack and metal loss detection tool, developed in collaboration with Colonial Pipeline. The new design not only meets the compact length requirement but also offers enhanced field reconfigurability, allowing it to adapt to a wide range of pipeline diameters (30" to 40") and easily deploy multiple crack detection technologies. Engineers from both organizations collaborated from the initial problem statement and preliminary designs through to the assembly, testing, and qualification of the ILI tool. This paper addresses the unique challenges during the project. This case study illustrates how ILI service providers and pipeline operators can work together to continuously adapt emerging ILI technology to the benefit of pipeline safety.
KEYWORDS: Ultrasonic ILI; UT Crack Detection; UT Metal Loss; Combination ILI; Operator / ILI Provider Collaboration
Alan Morton, Jim Kay, Dick Williamson
R.B. Williamson Energy Advisors, Tulsa, USA
Pressurized hydrocarbon is a formidable entity. While pipeline operators and service providers have developed safe and accepted procedures for managing it, some threats may be dynamic and require efforts beyond the checklist.
For example, the safe management of pressure and vapors during the launching and receiving of cleaning pigs and inspection tools requires continuous monitoring and mitigation. That includes knowing how to manage hydrocarbon, oxygen and ignition sources to keep field personnel safe and assessing the integrity of the pig trap assembly and its components to ensure they can hold pressure and operate as expected.
Over time, a phenomenon known as normalization of deviation has allowed field practices, culture and tribal knowledge to become the standard for a given process. Understanding the threats that drove the establishment of safe pig trap procedures will help bring awareness to field practices that may deviate from the approved practices.
The purpose of the paper is to show how products and processes for the operation of launchers and receivers have evolved over time based on feedback from the field. This paper will discuss pressure management with the trap, management of gases and liquids within the trap, managing potential ignition sources, ensuring trap integrity and safety practices for traps, components and closures under both normal and abnormal operating conditions.
Key words: normalization of deviation, traps, tribal knowledge, safety, launcher, receiver, threats, hazards
Paul Chittenden
TSC Subsea, Houston, USA
Ensuring the integrity of pipeline systems is critical for optimizing operational efficiency, minimizing environmental impact, and safeguarding personnel and public safety. Neglecting pipeline maintenance can lead to reduced production and, in worst cases, catastrophic failures due to undetected cracks or corrosion.
Traditionally, pipeline operators rely on in-line inspection (ILI) pigging solutions, which require specific pig launching and receiving facilities. When such facilities are unavailable, pipelines are often deemed non-piggable or challenging to inspect. In these cases, external surface inspection becomes the alternative, although this approach is not always feasible due to pipeline material or external obstructions.
This presentation introduces two case studies that showcase the evolution of a new crawler-based inspection delivery method. This method enables spot inspections using remotely operated scanning technologies, and represents the next step towards full integration with ILI scanner systems for comprehensive pipeline inspection.
The first case study involves an internal corrosion and crack assessment on a 14-inch duplex riser located on an offshore platform in the North Sea. Initially installed as a spare, this 110-meter riser, with recessed welds every 10 meters and three complex 3D bends, had never been operational. The client required definitive assurance of its integrity before commissioning the riser for an upcoming development project. The riser, filled with anti-corrosion fluid at elevated temperatures, presented significant inspection challenges due to its single entry and exit point.
To address these challenges, a robotic bidirectional tethered crawler was deployed, capable of navigating through the riser, precisely stopping, stabilizing, and performing detailed corrosion and crack assessments as required.
Advanced NDT technologies were crucial for this complex inspection. The methods employed included Alternating Current Field Measurement (ACFM) for detecting surface-breaking cracks in recessed welds and Subsea Phased Array (SPA) for volumetric weld inspection and corrosion detection and mapping.
The inspection was successfully completed, allowing the client to proceed with their development project and re-commission the riser. The tethered ILI solution played a pivotal role in enabling the client to return the riser to service and meet project timelines.
A major engineering challenge involved designing the delivery vehicle to navigate vertical pipe sections with multiple bends and to precisely stop at areas of interest. The vehicle was also required to rotate 360 degrees while maintaining consistent probe pressure on the inspection surface.
Following the successful delivery system design, the next phase involves full integration with an ART Scan module to assess wall thickness for two 4,000 ft. long non-piggable pipelines. This paper will further explore the development process and the upcoming field trial, scheduled for completion by the end of 2024.
Alan Morton, Larry Alspaugh, Dick Williamson
R.B. Williamson Energy Advisors, Tulsa, USA
The use of in-line inspection (ILI) tools and cleaning pigs is a common and successful way to manage the ongoing integrity of operational pipelines.
However, even with thorough planning, in some instances these tools and pigs can become damaged or, worse still, lodged in the pipeline. A lodged tool can disrupt flow and recovering it may result in the suspension of normal operations.
Conditions that can contribute to a failed pig run include excess debris in the pipeline; unknown pipeline bends or wall thicknesses; intrusive equipment, such as pig signalers, corrosion coupons or sensing equipment not addressed prior to the run; improper management of pumps and compressors, the style of the pig or inspection tool; and incompatible valves or fittings.
The options for mitigating a lodged tool or pig are just as unique as the interactions between the pig, the physical pipeline and the operating conditions and depend upon whether the pig is truly stuck in place or has just stopped or stalled. They include temporarily increasing pressure to the pig’s drive cups, surging the line —which involves rapidly closing then opening a valve to send short bursts of pressure to help dislodge the pig — reversing flow or using a recovery tool to push the ILI tool to the receiver.
If all other measures fail, the tool must be removed from the line by a cutout project. This involves accurately locating the tool inside the pipeline, isolating the affected pipeline section, cutting into the pipeline, retrieving the lodged tool and repairing the pipeline.
This paper will review the reasons a tool or pig can stop in a flowing pipeline, discuss how tool and pipeline conditions affect run success and provide guidance into planning a successful run. It will also describe the mitigation steps involved in locating a lodged tool, including using pipeline and tool data to evaluate why the tool stopped and evaluating the options to safely get the tool moving again. This paper will also explain the processes for retrieving the tool or pig, incorporating lessons from fields around the world.
Key words – pig, recovery, tracking, flow management, integrity, abnormal operating condition, ILI tool, launcher, receiver, trap
Christopher Newton1, Jordi Aymerich2, Sayan Pipatpan3, Tannia Haro4, Santiago Urrea3, Alex Hensley4
1Phillips66, Houston, USA. 2NDT Global, Calgary, Canada. 3NDT Global, Stutensee, Germany. 4NDT Global, Houston, USA
Pipeline operators rely on a variety of strategies to maintain the safety and integrity of their pipeline systems, with inline Inspection (ILI) and Non-destructive Examination (NDE) being crucial components. However, these methods can encounter challenges and limitations when identifying and sizing complex features, such as off-axis cracking. What happens when NDE evidence suggests a systematic measurement bias relative to ILI? Can operators still use this data within their Integrity Management Programs (IMP)? Moreover, can this NDE data be effectively leveraged to develop new rules for ILI analysis processes?
Last year, NDT Global, in collaboration with Phillips 66, developed a Phase I systematic method to identify crack complexity in previously detected and undersized features based on NDE campaign results. This novel methodology integrated years of accumulated knowledge from ILI survey data from various pipelines with insights from applying sophisticated in-ditch NDE techniques developed for complex features.
In Phase II, as discussed in this paper, the investigation advances further by validating the Phase I methodology using destructive lab testing results. The metallurgical evaluation includes nine ILI-reported linear anomalies that were previously examined non-destructively in a 6" pipeline. The destructive testing aims to determine whether NDE accurately identified and sized these anomalies and whether the original ILI results were biased in the first instance. Additionally, this phase explores methods to assess the Probability of Sizing (POS) for out-of-specification features and suggests potential adjustments to ILI tool sizing curves when truth data is available.
This study highlights the successful partnership between NDT Global and Phillips 66 in advancing pipeline integrity management, offering valuable insights for the future of pipeline safety and reliability.
KEYWORD(S) FOR SUBJECT AREA
ILI verification, validation; ILI analysis; Crack assessment and management
Thomas Hennig, Michael Haas, Katja Traeumner
NDT Global GmbH, Stutensee, Germany
Gas transmission lines, especially those constructed between the mid 20th century and early 1980s are often affected by external stress corrosion cracking (SCC). Traditionally, Operators have used Electromagnet Acoustic Transducer (EMAT) based inline inspection tools to detect and characterize these flaws, ensuring the integrity of the asset.
However, EMAT technology is not only sensitive to SCC or other types of cracking, but it also delivers a high incidence of false positives, posing significant operational challenges. To overcome this, a circumferential magnetic flux leakage tool (MFL) is used in addition to the EMAT inspection enhancing the accuracy of crack identification and characterization.
To enhance and refine crack inspection of gas pipelines and reduce the risk of unnecessary digs, NDT Global has developed CIGMA- x an advanced technology for crack detection, identification, and sizing. based on directional gas-coupled guided wave generation in the pipe wall, CIGMA-x allows us to inspect an asset without any contact of the sensors to the internal pipe wall.
The small size (compared to EMAT) of the sensors allows for a high sensor density, delivering high resolution and accurate data which ensures detection, identification and sizing of SCCs and other types of cracking.
The authors will present the outcomes of an industry-funded development project, including the results of small-scale laboratory testing and full-scale evaluations conducted in a nitrogen-filled pressure chamber on 20" and 30" pipeline sections. Additionally, the paper will discuss the optimization of sensor designs tailored to varying pipeline wall thicknesses, as well as insights into the data analysis methodology and the necessary infrastructure for implementing this cutting-edge technology.
Greer Simpson1, Corey Richards1, Carlos Costa1, Aaron Schwing2, Jeremy K Holifield2, Jason M Moritz2
1DarkVision Technologies, North Vancouver, Canada. 2Flint Hills Resources, Wichita, USA
Pipeline operators are gaining significantly more intuitive results with a novel In-line Inspection tool that comprehensively evaluates every major anomaly type – metal loss, axial cracks, and dents – in a single run. This technology represents a fundamental improvement in resolution and the ability to understand combined threats impacting pipelines. Direct 3D measurements reveal the shape and orientation of anomalies that enable operators to better understand the root cause and context of the anomaly. This direct imaging method is not only more intuitive for industry, but it also overcomes legacy amplitude-based inferred measurement methods that have limitations when measuring crack morphologies.
The tool leverages the latest developments from phased array in-ditch based handheld systems, medical imaging, and upstream oil and gas ultrasound imaging technologies to bring ultrafast imaging rates with 0.5mm axial resolution, and 0.25mm circumferential resolution at line speeds exceeding 3 meters/second. Over 6,000 independent sensors mounted on encoded carriers detect and size metal loss, axial cracks, and dent information from a single registered pass.
This paper presents and validates the technology in accordance with API 1163. A 400-meter continuous flow loop was engineered and constructed to test the tool’s endurance and validate the tool’s performance over a variety of anomalies including electrical discharge machined (EDM) notches, manufactured cracks, and wall loss. These results are validated against industry standard tools including a metrology-grade laser scanner and a phased-array ultrasound handheld tool. Additionally, the results related to identification and measurement of challenging anomalies such as stress corrosion cracking (SCC), hook cracks and lack of fusion that were removed from Flint Hills Resources pipelines are presented. Lastly, findings from a full-scale deployment in a segment of Flint Hills Resources 16" transmission pipeline are summarized.
Tom Alexander1, Benjamin Mittelstadt, P.E.2, Stephen Barnet2, Peter Seydewitz3
1Dynamic Risk, Toronto, Canada. 2Dynamic Risk, Houston, USA. 3Enbridge Gas Transmission, Houston, USA
The integrity of pipeline systems relies heavily on the accuracy and completeness of records that are Traceable, Verifiable, and Complete (TVC). As regulatory scrutiny increases, the need for reliable validation methods becomes of paramount importance. This study focuses on leveraging In-Line Inspection (ILI) data to enhance the validation of existing records, ensuring that operators can confidently manage pipeline integrity and meet regulatory requirements.
TVC records play a key role in pipeline integrity and operations, including tasks such as Maximum Allowable Operating Pressure reconfirmation (MAOP-R) through Engineering Critical Assessment (ECA), quantitative risk assessments (QRA), and establishing accurate class locations. These records will also be important for the potential application of the proposed methods under 192.618.
TVC records form the foundation for all analysis and conclusions and will be a primary focus during regulatory audits. Recent experience has highlighted the potential for gaps, particularly where TVC status was established prior to recent amendments under 49 CFR 192. The pipeline industry has invested significant time and effort in establishing TVC records and duplication of that effort is unnecessary, however understanding and resolving remaining data issues (i.e. TVC the TVC) is required. Manually addressing such issues would be a complex and labor-intensive process involving extensive data review and verification, however, ILI technology offers a powerful and efficient way to confirm confidence in records that may be considered vital in establishing the integrity and safety of the pipeline system.
Recently emerging Material identification ILI technologies offer valuable insights or the confirmation of material properties. The value of ILI data for material identification is however not limited to such advanced technologies. Conventional ILI dimensional information such as joint lengths, wall thickness changes, and other attributes are visible in diagnostic ILI technology data. When these data points, are correlated with existing records, they can significantly streamline the validation process, reducing the burden of manual verification and enhancing the reliability of TVC records. This approach not only ensures compliance with current and proposed regulations but also supports the integrity and reliability of pipeline operations.
Integrating ILI data with Geographic Information System (GIS) data and historical TVC records can significantly enhance confidence in the accuracy and completeness of TVC records, as well as in the GIS data’s ability to accurately represent the materials in the pipeline. This approach involves a detailed analysis of ILI data to identify discrepancies and gaps in the existing GIS data and records, thereby providing a solid foundation for regulatory compliance and effective risk management.
Shree Krishna, Udayasankar Arumugam, Ryan Milligan, Ravi Krishnamurthy
Blade Energy Partners, Houston, USA
This paper introduces a methodology aimed at analyzing failures in buried pipelines exposed to significant geotechnical displacement. The occurrence of ground movement and heave generates substantial longitudinal strain through elongation and bending, potentially leading to buckling in the pipeline segment. Buckling, in turn, can compromise the pipeline’s elastic stability, allowing further elongation with soil movement. The girth weld’s presence acts as a potential weak point, susceptible to either brittle or ductile failure. Conventional analyses using standards such as ASME B31.8 or API 1104 tend to provide conservative estimations and often fail to fully elucidate the extent of geotechnical displacement or the root cause of failures. Moreover, these approaches overlook addressing failures that may occur when the girth welds are ductile in nature as specified in API 1104. This is especially true for modern steels.
To effectively tackle extensive geotechnical displacement, this paper advocates for strain-based damage methodologies utilizing critical strain as a pivotal material parameter. Understanding the true stress-strain behavior, particularly the critical strain parameter of base metal, Heat Affected Zone (HAZ), and weld, is crucial in predicting potential failure. The paper’s approach involves reviewing existing strain-based failure methodologies in literature and then delving into analyzing the geotechnical movement of buried pipeline segments using a critical strain-based failure criterion. The pipeline’s lateral displacement is analyzed through a finite element approach that integrates global and detailed local sub-modeling. This examination includes showcasing the impact of weld misorientation and the presence of planar defects related to welding. The paper also discusses the evolution of damage at the local girth weld, emphasizing the significance of the “Ductile Failure Damage Indicator (DFDI)” parameter. Finally, a series of finite element analyses illustrate the loss of elastic stability due to buckling in pipes subjected to pure bending and internal pressure. It concludes by outlining the limitations of other geohazard fitness-for-purpose approaches relying on parameters like CTOD (Crack Tip Opening Displacement) and demonstrates the successful application of the methodology in analyzing a buried pipeline failure.
Pooya Delshad1, Peter Martin2, Emily Brady3, Jeffrey Kornuta3, Jonathan Gibbs1, Peter Veloo1
1Pacific Gas and Electric Company, San Ramon, USA. 2RSI Pipeline Solutions, New Albany, USA. 3Exponent, Houston, USA
Instrumented Indentation Testing (IIT) is a non-destructive technique used to estimate mechanical properties such as yield strength and ultimate tensile strength of materials, making it a useful tool in the assessment of pipeline steels. Although the importance of surface preparation for accurate IIT measurements is widely recognized, published systematic studies evaluating the specific effects of varying surface finishes on IIT results are rare. Identifying the potential implications of over- or under-preparation could help ensure more efficient and accurate IIT.
In this study, the impact of different surface finishes, ranging from 280 grit to 2000 grit, on the yield strength measurements of pipeline steel using IIT was investigated. Various locations on the pipe were ground and polished to these target surface finishes, and IIT was performed at each location. Metallographic cross-sections were prepared from the locations of different surface finishes with IIT indents to analyze the influence of surface preparation.
Preliminary results indicate that IIT measurements taken at a 1200 grit surface finish are more consistent with the yield strength values obtained from destructive transverse tensile tests. In contrast, IIT results at 280 grit exhibited yield strength values significantly higher than those from tensile testing, while measurements at 2000 grit showed lower yield strength values in some cases, which could be attributed to polishing parameters such as the pressure applied during the polishing process and the polishing time. Metallographic analysis suggests that the rough surface at 280 grit and the formation of surface voids at 2000 grit may have contributed to these discrepancies.
This ongoing experimental work aims to establish a conclusive understanding of the relationship between surface finish and IIT measurements, potentially identifying an optimal surface preparation technique that ensures reliable IIT data without unnecessary refinement efforts.
KEYWORDS: IIT, Surface Preparation, Polishing, Yield Strength, Material Properties Verification
Travers Schwarz1, Steven Kinikin1, James Fetherolf1, Davie Peguero2, Jackson Herrod2
1Sacramento Municipal Utility District, Sacramento, USA. 2Henkel Corporation, Riviera Beach, USA
Pipeline operators continue to rely on acceptable methods of repair outlined in ASME B31.8S when making decisions to repair their pipeline in the field. The damage is most often attributed to one of the nine defined threat categories listed in B31.8S: External Corrosion, Internal Corrosion, Stress Corrosion Cracking (SCC), Manufacturing defects, Welding/Fabrication defects, Equipment defects, Third-Party Damage, Incorrect Operations and Weather or Outside Force. Although not all pipeline damage can be repaired, options are available and can be utilized by the operator to mitigate the threat and keep the pipeline in operation.
Sacramento Municipal Utility District (SMUD) encountered a recent incident where third-party damage occurred on a section of their gas transmission pipeline system; located inside a High Consequence Area (HCA). The pipe damage was caused by an unmarked bore crossing, gouging the top of pipe near the girth weld and long seam weld. Decision was made to use an engineered, approved carbon fiber composite wrap to repair the pipe; this ensured the pipe maintained its full-strength integrity while allowing the operator time to plan, and schedule resources for the replacement of the damaged section of pipe.
SMUD worked with the composite manufacturer and performed a cyclic pressure test, a hydrostatic burst test and an adhesion test on the damaged segment of pipe. This paper looks at the design characteristics of the carbon fiber composite wrap which was tailored for this specific type of repair in accordance with ASME-PCC-2 standard, and the actual findings when the repair underwent a stressed condition. The expected results intend to provide operators with better insight and confidence when using this repair method on their pipeline systems in the future.
Zahra Lotfian1, Michiel Brongers2
1Kiefner and Associates, Houston, USA. 2Kiefner and Associates, Columbus, USA
While pressure cycle fatigue may not typically be a significant concern in conventional gas pipelines, introducing hydrogen changes the dynamic. This makes pressure cycle fatigue analysis a critical factor in ensuring mechanical integrity. Hydrogen can significantly alter material properties through embrittlement, accelerating crack growth rates. As the industry shifts towards hydrogen blending in natural gas pipelines, accurate remaining life assessments become essential for effective integrity management. This is especially true for small flaw sizes that may not be detectable by ILI or other NDE tools.
As part of ongoing research for the United States Department of Transportation (USDOT) Pipeline and Hazardous Materials Safety Administration (PHMSA), this paper addresses the challenge of assessing flaws just below the detection limits of ILI and NDE tools. Through a series of case studies, the remaining life of these subcritical flaws is estimated, considering variables such as flaw size, location (e.g., pipe body, seam weld), pipeline grade, and the severity of pressure cycles. Unlike the traditional Paris Law approach commonly used for Region II (stable crack growth) fatigue analysis, this study employs advanced models to capture a broader range of material behaviors, including Region I (threshold) and Region III (rapid crack growth), while also accounting for pressure cycle severities. Experimental data is directly incorporated into fatigue crack growth calculations to further reduce conservatism instead of relying on standard fatigue design curves.
Operators will gain insights into how hydrogen exposure impacts pipeline remaining life and can use this knowledge to make informed decisions for setting reinspection intervals and extending the operational life of pipelines in hydrogen environments. While the findings provide important guidance, they also emphasize the need for ongoing research and thorough technical assessments.
KEYWORDS: Pipeline, Hydrogen, Fatigue, Remaining life, Crack, ILI, NDE, PHMSA
Peter Martin1, Nathan Switzner1, Owen Lopez-Oneal2, Sophia Curiel2, Peter Veloo2
1RSI Pipeline Solutions, New Albany, USA. 2Pacific Gas and Electric, San Ramon, USA
It is widely accepted that the yield strength of low carbon and low alloy steels can be modeled as the sum of contributions from intrinsic lattice friction stress, solid solution strengthening, grain size effects, dispersion strengthening, and dislocation density. Dispersion strengthening can be neglected for hot-rolled steels that aren’t microalloyed with Nb, V, or Ti, while models for solid solution (Pickering), grain size (Hall-Petch), and dislocation density (Taylor) effects have been extensively validated in published research dating back as far as the 1930s. These models have been shown to be accurate and effective, but line pipe applications have been limited because the quantitative metallography required to determine grain size has historically been time consuming and resource intensive. The recent development of a machine learning model to perform rapid, reliable grain size measurements warrants revisiting these models.
In the current work, the yield strengths for a set of 39 hot-rolled, non-microalloyed steels are estimated from the %Mn, %Si, %Cr, %Cu, and grain size using the model published by Pickering in 1978.[1] The model calculates the grain size and solid solution contributions using only the original coefficients published in 1978, while the contribution of dislocation density is estimated by assuming a constant, average dislocation density for all hot rolled, non-microalloyed pipes. Comparison of model predictions to yield strengths from tensile testing resulted in a mean absolute percent error (MAPE) of 8.0% with a 95% prediction interval of ±11.8 ksi. This performance compares favorably to the instrumented indentation test (IIT), where comparison to tensile testing for an expanded set of 83 pipes yields a mean absolute percent error (MAPE) of 8.6% with a 95% prediction interval of ±12.2 ksi. In a direct comparison of 30 pipes for which both sets of data were available, yield strengths estimated by the model and by IIT predicted the results from tensile testing with MAPE values of 8.2% and 6.8%, respectively, and 95% prediction intervals of 12.0 and 12.5 ksi. The results suggest that this model may be a useful tool to confirm strength testing by IIT, provide strength estimates where IIT is not practical, or replace some fraction of strength testing altogether.
[1] Pickering, F.B. Physical Metallurgy and the Design of Steels; Applied Science Publishers: London, UK, 1978; p. 63.
Colin Scott
AP Dynamics, Calgary, Canada
Pipeline operators routinely carry out inline inspections to identify deformation on their pipelines, and specifically dents. Dents represent time dependent failure mechanisms, as the flexing of a dent under pressure cycling conditions can result in crack initiation and fatigue growth. Recently developed dent assessment techniques have exposed various challenges to analysts, with industry finding difficulty in reaching consensus on an optimum methodology (Leis PPIM 2023).
In this work, we review the extensive published industry laboratory data. Various key parameters are investigated, including pipeline diameter and wall thickness, dent depth, pressure cycling magnitude and R-ratio, and restraint conditions. Numerical analyses are used to focus on the key parameters of interest to the remaining life assessments. More importantly, we also highlight the key parameters that do not appear to play a significant role in predictions.
The result of the project is a simplified dent remaining life assessment methodology that focusses on a single key parameter to the assessment. The less-relevant parameters are disregarded, as they bring a complexity to the assessment with no apparent benefit. Preliminary analysis suggests an improvement in model reliability and the possibility of improved program efficiency for operators.
Justin Oliveira, Sunil Chintalapati
Boston Geospatial, Boston, USA
Energy infrastructure is exposed to an active and ever-changing geohazard landscape, and regulators are raising the bar for operators to better quantify, prepare for, and mitigate potential impacts from these threats. On June 2, 2022, PHMSA released its updated advisory bulletin reminding owners and operators about the seriousness of geohazards. In this update they highlight various case studies involving failures due to or likely due to subsidence, landslides, seismicity, and more. Furthermore, the bulletin offers various suggestions for abatement including ILI surveys, in situ sensors, remote sensing, geotechnical surveying, and more. Because these hazards are so diverse, no one technology can adequately address them. Instead, a concert of solutions must be combined together to ensure pipeline integrity and achieve the desired performance. This paper will explore case studies referenced in the bulletin using a GIS-based geohazard tool funded in part under the PHMSA Pipeline Safety Research and Development Program. The paper will combine terrestrial, airborne, and satellite measurement phenomenologies to explore the case studies and demonstrate the tools use for identifying and measuring geohazard risk and estimating the anticipated mechanical loading.
Syed Aijaz1, Clifford Maier1, Michael Gloven2
1TC Energy, Houston, USA. 2Pipeline-Risk (PLR), Denver, USA
Big data, machine learning and artificial intelligence: these buzzwords invariably create a lot of hype but do they actually live up to it? TC Energy’s threat management team set out to answer that question by curating a comprehensive dataset of pipeline integrity digs in-ditch findings to create a machine learning model for predicting SCC on its transmission pipeline assets. In collaboration with Pipeline-Risk (PLR), results from 1800+ digs since 2012 containing approximately 27,000 data points were consolidated. A classification-based machine learning model was trained on a subset of the consolidated dig data, and its performance was then evaluated using the remaining, unseen portion of the dataset. The results exhibited an impressive predictive efficacy of up to 90% for predicting likelihood of SCC on TCE transmission pipelines. This model is now utilized in assisting in SCCDA dig site selection workflows and prioritizing ILI assessments resulting in significant efficiency gains. The most important factors contributing to the success of this model were a robust, and highly organized enterprise data infrastructure, SME-driven criteria and an effective team structure allowing a comprehensive threat management approach. This paper will present key data strategies to ensure your organization is optimally positioned with people and processes to maximize value created by the computational prowess of machine learning.
KEYWORDS: SCC Threat Management, Machine Learning
Ryan Holloman1, Lyndon Lamborn2, Greg Thorwald1, Michael Turnquist1
1Quest Integrity, Boulder, USA. 2Lamborn Engineering, Inc, Edmonton, Canada
This paper summarizes a study in which Quest Integrity and Enbridge investigated the impact of grinding repair on the stability of axial and circumferential cracks as the griding is taking place. This study was conducted in response to a 2017 PRCI project that experimentally investigated grind repairs on axial cracks manufactured on the surface of vintage pipeline material. The 2017 PRCI project aimed to demonstrate that a reduction in stress intensity would take place during the grinding process. However, these experiments captured an apparent decrease in remaining strength after partial grinding of the crack had occurred.
Interpretation of the data from the 2017 PRCI project was challenging due to the limited number of experimental tests, thus inhibiting statistical relevance. The study presented in this paper utilized elastic-plastic finite element analysis (FEA) to replicate the experimental tests and determine whether there is any theoretical basis to explain a reduction in stress intensity after partial grinding of the crack had occurred.
The same geometry and material values were applied to the models for direct comparison to the experiments. Because FEA is less cumbersome than full-scale testing, more fidelity was added to the existing experimental data points. The grind depths were analyzed in increments of 1/10 of the full-grind depth until the crack was fully removed from the pipe geometry, resulting in a region of metal loss where the crack was previously located. The FEA study was then extended to investigate circumferential cracks subject to both load-controlled and displacement-controlled loading conditions.
The simulations of the axial crack grinding showed a gradual increase in burst capacity, which contradicts the 2017 PRCI study. Based on the results presented in this paper, the decreased experimental burst capacity was likely due to experimental variability from using different vintage pipe spools for individual tests. The circumferential crack analyses also demonstrated no obvious reduction in remaining strength as the grinding took place. The results provide computational proof that the common practice of grinding axial and circumferential cracks is not expected to cause any decrease in remaining strength as the repair takes place.
Noel Nelson1, Pete Weber2, Soek-Bong Lee3, Tim Ross4
1DoC Mapping, San Diego, USA. 2DoC Mapping, New Orleans, USA. 3Doc Mapping, New Orleans, USA. 4DoC Mapping, Calgary, Canada
This paper presents a new and state-of-the-art approach to 3D scour and flood modelling specifically for pipeline water crossings, with a particular focus on simulating and analyzing the effects of record flood events and their effects on potential pipeline exposure and free-span lengths. The technique is major improvement over existing 2D analysis techniques looking at a cross section directly above a pipeline water crossing.
Pipelines traversing water bodies are susceptible to scour, which can result in structural damage and significant economic losses not just from damage to the pipeline but from premature shutdown of the pipeline due to conservative desktop scour modelling. Our research integrates cutting-edge computational fluid dynamics (CFD) techniques and advanced sediment transport modeling, combined with high-resolution bathymetric and topographic field inspection data to provide a comprehensive assessment of scour and span potential in pipeline water crossings under a variety of statistical flood recurrence intervals.
We introduce a novel 3D scour modeling methodology that considers the complex interaction between water flow, sediment transport, pipeline geometry and depth of cover. This approach leverages high-resolution bathymetric and LiDAR data sets, hydraulic parameters, and sediment properties to accurately predict the scour depths and patterns during various flow conditions. Furthermore, the study explores the extreme scenarios by simulating record flood events, which are essential for assessing the pipeline’s resilience and safety under extreme hydraulic conditions. The outcomes of these simulations are presented in interactive 3D models and offer invaluable insights for optimizing pipeline design, maintenance, and risk mitigation strategies, ensuring the long-term integrity and reliability of pipeline infrastructure in challenging water crossing environments. This research contributes to the advancement of pipeline engineering practices, with the potential to enhance the safety and sustainability of critical waterborne transportation systems.
Robert Smyth
PetroSleeve, Nisku, Canada
A joint industry project including both industry and government, organized by C-FER, has been undertaken to determine if a non-welded repair technology can be used to repair circumferential defects.
With the development of advanced internal inspection tools, industry is now capable of locating circumferential cracking. Obviously, having developed the ability to locate cracking, industry is required to return the integrity of the defect joint back to its’ original level.
Repair methods currently available include removing the affected pipe section (cut out) or installing a welded steel sleeve around the defect (Type B sleeve). The first case is extremely costly, and the second case introduces additional concerns considering the in-service weld.
Consequently, this JIP was instigated to determine whether a non-intrusive repair such as a wet lay-up, composite fabric, preformed composite coil, steel sleeve, or bolt-on repair sleeve/collar could, when installed, prevent the circumferential crack from extending. This project, broken into 4 phases, consists of the evaluation of current non welded technologies and testing those technologies that have promise to repair circumferential cracking.
Phase 1 consisted of Non-destructive tensile testing. This consisted of, after having researched repair types, inviting potential participants (6) identified as Repair A to Repair F to install their repair technology. Each was to install their repair on three sections of 24" pipe pressurized to 785 psi (5400 kPa). In each case, each participant, separately, installed their repair type. There was no information exchanged between the participants, for all Phases.
Following repair installation, the three 24" vessels were pressure cycled and then put under tension to yield of the pipe parent material.
Phase 2 considered the effect of installation pressure. This consisted of having three of the six participants install their repair technology on seven vessels pressurized at 30%, 50%, and 70% of SMYS. The vessels then were pressurized to various levels, put under tension, and then, at 72% SMYS, put under tension until failure.
Phase 3 consisted of destructive tensile testing with a circumferential flaw. In this phase, the repair types were Vendor 1, Vendor 2, and a type B sleeve. In all cases, the repairs were installed at 50% SMYS, initially exposed to pressure cycling, and then setup for the tensile test. At 72% SMYS (1482 psi; 10,200 kPa) the vessels were put under tension until failure occurred.
Phase 4 consists of a long-term performance of repairs test. In this test two participants are involved. The test vessels will be put under tension and load, to simulate field conditions. Phase 4 commenced August 2024, with one of the participants having installed their repair on three 12" vessels pressurized to 1030 psi (7100 kPa) and each containing an 80% circumferential crack.
One of the technologies that was selected for testing was the Steel Compression Reinforcement Sleeve (Repair F) that is participating in Phase 4.
This paper describes the JIP, as it pertains to the Steel Compression technology.
KEY WORDS
circumferential cracking, non-welded repair, testing, repair technologies
Susannah Turner, Fraser Gray, Timothy Turner
Highgrade Associates Ltd, Newcastle upon Tyne, UK
Inspection is used as part of a pipeline integrity management program, to control the risks associated with pipeline failure. Risk based inspection (RBI) methods are commonly used to schedule pipeline inspections. However, the RBI methodologies and approaches which are applied in the pipeline industry are many and varied.
This paper presents and discusses practical application of a pipelines RBI process which provides a direct link between the inspection interval and the risk associated with a loss of containment failure from a pipeline. The RBI methodology considered applies reliability engineering methods to account for the perceived increase in risk over time, due to both degradation-related time-dependent threats and randomly occurring event-driven threats. The presented approach is flexible, allowing detailed, quantified engineering relationships and historical incident rate data to be used where available, with more subjective input from subject matter experts and engineers when required. The uncertainty associated with the assessments is accounted for explicitly, allowing different levels of analysis complexity to be accommodated within the same overall pipeline system RBI study.
The RBI approach schedules inspections such that they are completed before risk reaches a tolerability limit. This ensures that inspections are targeted appropriately to control the risk of pipeline failure. The RBI process also identifies when additional risk mitigation is required to control risk, for example this may be the case if inspection would be required at an impractical frequency, or if no suitable inspection method is available. The assessment process can be further used to investigate the effect on the assessed risk level of changes in the inspection schedule.
This paper builds upon and updates a methodology and process first developed twenty years ago. The study presents an improved development of the methodology and discusses the authors’ experience of practical application and implementation of the RBI process, for large offshore pipeline systems. This practical experience includes elements such as dealing with requirements to combine inspections into optimised campaigns, as well as accounting for the time required to review, assess and act upon inspection findings. The review of experience also considers alignment of the RBI with corporate systems, procedures and risk matrix definitions. The paper concludes by identifying the key elements leading to successful development of an RBI schedule for offshore pipeline systems.
Michael Manahan
MP Machinery and Testing, State College, USA
MPM developed the Instrumented Indentation System (I2S) for measurement of yield stress (YS), ultimate tensile strength (UTS), hardness, and ductility of in-service pipes. The I2S nondestructively indents the pipe surface while measuring applied load/deflection to determine the Brinell hardness. The pipe surface preparation is completed in less than 5 minutes and multiple data points for base, weld, and heat-affected-zones can be acquired in a few minutes. The I2S material model software displays the YS, UTS, and ductility on the portable computer immediately after measurement. The efficacy of the I2S data has been demonstrated by comparison with benchmark laboratory data obtained in the Pipeline Research Council International (PRCI) study and also with the Gas Technology Institute (GTI) benchmark data. For pipes that require plane-strain fracture toughness data, MPM has developed a miniaturized Charpy V-notch (MCVN) impact test that provides Charpy and fracture toughness data from a dynamic test measurement. It will be necessary to trepan small pieces of material (~0.2 inch x~ 0.2 inch x ~1.0 inch long) from the pipe and perform a weld repair as needed. MPM’s test machine is equipped with an instrumented striker for acquisition of the dynamic load and deflection. The advanced mechanics model uses the load/deflection data to determine the material J-resistance (JR) curve and the fracture toughness (JIC and KIC). While it is recognized that other researchers have proposed correlations between Charpy energy (or tensile data) and plane-strain fracture toughness, MPM’s experience shows that these correlations are only valid over limited materials and conditions. The robust approach is, therefore, to make a direct measurement of the fracture toughness.
Chad Haegelin1, Luke Whitrock2
1Integrity Solutions Ltd, Houston, USA. 2Integrity Solutions Ltd, Denver, USA
Many pipeline operators are still experiencing internal corrosion issues despite implementing industry best practices. Due to the ever-expanding regulations, operators are required to be more proactive in preventing corrosion on lines not previously regulated.
PHMSA and API have both implemented industry best practices and advisories to move closer toward a predictive approach to integrity management, with the ultimate goal of improving corrosion detection and identifying mitigations.
This presentation examines multiple real-world operational scenarios where the application of a quantitative internal corrosion (QIC) model has proactively helped pipeline operators working in field operations, chemical teams, and integrity management departments, risk-optimize mitigation, inspection, and monitoring activities as a strategy for eliminating failures.
The QIC Assess (pronounced Quick Assess) model is designed to effectively predict location-specific internal corrosion rates throughout a pipeline in a time-based cumulative degradation prediction. This model employs pipeline-specific flow parameters derived from a detailed pipeline hydraulic model designed to disentangle the complexities of multiphase fluid flow influence on the internal corrosion growth mechanism.
We’ll present case studies demonstrating how an operating company went from leading the industry in pipeline failure frequency rate to eliminating all pipeline leaks within 4 years of implementing our QIC Assess model and embracing the mitigation recommendations. In another implementation of the model, we’ll discuss how the model accurately predicted moderate bottom-of-pipe internal corrosion and severe top-of-pipe internal corrosion.
Douglas Sahm
ZEVAC, Tulsa, USA
An impact-based approach to integrity management in the context of the EPA’s new “Super Emitter” program is detailed with case-study and practical guidance for operators to navigate their IMP operations while avoiding the 100kg/hr methane emission threshold for super emitter classification. The EPA’s new OOOOb/c rules have established a 3rd party reporting mechanism that will impact nearly all blowdown or purge operations within an operators’ integrity management program. Pigging, line blowdowns, hydrotesting, and cutouts will all be considered super emitters if procedures are not updated to avoid the associated gas releases. Many techniques that have been developed in the sour gas, refrigerant, and volatile liquids industries have been adapted to allow for minimal release during gas line integrity operations.
Dr Tom Bubenik is a Vice President at DNV USA, where he is responsible for developing, managing, and implementing projects related to all aspects of pipeline integrity management, including but not limited to ILI, SCC, fracture control, seam weld integrity, and mechanical damage. He has over 45 years of related pipeline experience. Dr Bubenik is an internationally recognized expert in technologies related to in-line inspection and the effects of defects on pipeline integrity. He received his PhD in Theoretical and Applied Mechanics from Northwestern University.
Willem Vos, Jan Ove Toskedal, Gary Dye
NDT Global, Bergen, Norway
In the early 21st century, a team of researchers in DNV (Norway) developed an ultrasonic technology for the inline inspection of gas pipelines without liquid batch. The dry-ultrasound technology has subsequently been used to inspect more than 10,000 miles of operational gas and liquid pipelines around the world.
The authors present lessons learned during the deployment of this new technology and reflect on the advantages and limitations.
Several different use cases are considered; one being deployment of acoustic resonance ILI for the base line inspection of newly constructed gas pipelines. In particular, the others will highlight a number of long-distance gas transmission pipelines that have been inspected using acoustic resonance ILI, and highlight the benefits of ultrasonic baseline for pipelines.
Furthermore, the tools have shown notable flexibility in the field of difficult-to-inspect gas and liquid pipelines. Notably, large diameter variations have been traversed, and bidirectional inspections have been performed, as well as extremely long duration runs.
A summary of completed work will be of value to all pipeline operators of challenging pipelines, in particular offshore, demonstrating challenging pipeline inspection projects which have been completed successfully.
Ian J. Duncan1, Alex Lange2, W. Kent Muhlbauer3
1Univ. of Texas-Austin, Center for Assessment and Management of Risk (CAMR), Austin, USA, 2Summit Carbon Solutions, Ames, USA 3WKM Consultancy, Austin, USA
There are significant misunderstandings surrounding transport of CO2 in pipelines. Robust risk assessments, including proper dispersion modeling and characterization of possible health effects, are essential to proper understanding of the actual safety of pipelining CO2. As part of a national initiative related to climate change, it is imperative that real information is readily available, especially to technical audiences. This paper explores several of the more significant points of confusion/controversy.
Nikolaos Salmatanis1, Amit Rajput2, Praveen Kumar2, John O’Brien3
1Chevron, Houston, USA. 2XaaS Labs, Sunnyvale, USA. 3itcSkilla, Houston, USA
Reliable detection and accurate localization (especially) of small leaks tends to be the weak link in Leak detection programs for oil & gas pipeline operators. The paper presents the results of a study aimed at assessing the feasibility of reliably identifying pipeline leaks using inline approaches based on minimally intrusive sensing devices that are now available to pipeline operators. These low form-factor sensing devices incorporate sensors based on Audio, Magnetometry, Pressure and Velocity. A test pipeline flow loop was leveraged to create a customized test setup and a test execution methodology was developed and executed towards this end. Sensing equipment from two different suppliers were used to collect various sensor datasets on separate test runs In test scenarios where leak signatures were identified, the team investigated the feasibility of ascertaining the limits of detection using such approaches. Key findings and Lessons learned are summarized
Click the button below to download all the PPIM 2024 Conference Papers in one pdf file
(file size: 402MB)
Rick Wang1, Ming Gao2
1TC Energy, Calgary, USA. 2Blade Energy Partners, Houston, USA
In API1183, the EPRG 2000/API579 Level 2 model is adopted as an alternative approach to BMT shape-parameter method for Level 2 fatigue severity assessment of unconstrained single peak plain dents in pipelines This model along with its earlier version, EPRG 1995, has been commonly used for dent integrity assessment in North American and worldwide because it is recommended by the highly recognized pipeline defect assessment manual. However, Pipeline industry practice in North America found that the EPRG equations provide conservative, in many cases, very conservative predictions that may have resulted in unnecessary excavations and repairs. Therefore, the objective of this paper is to improve the model accuracy and less conservatism. A critical review of EPRG/PDAM fatigue life prediction models (1995 model and its 2000 update) and other models including PRCI/BMT shape-parameter fatigue severity model (Level 2) and FEA/BS7608 fatigue life prediction (Level 3) are essential and given first, which provides a basis for improvement of EPRG equations from both safety and cost-effective perspectives. The newly improved and simplified model is then developed with PRCI MD 4-2 full-scale fatigue testing data and validated using PRCI MD 4-11, MD 4-14 and MD 4-15 full scale fatigue test results. Finally, a comparison among the newly improved model, EPRG 2000/API 579 Level 2 model, and PRCI/BMT/API 1183 Level 2 and Level 3 models is made, which provides a framework to further carry out the study of dent-interacting with welds, gouge, cracks, and corrosion.
Kah Soon grew up in the oil & gas city of Miri, Sarawak (Borneo-Malaysia). He graduated from the University of Manchester (UK) with a MEng in Mechanical Engineering with Management. He started his career as a subsea and pipelines design engineer and was involved in various offshore field development and installation projects across the African and Asian regions. Currently as a Technical Solutions Specialist for ROSEN focusing on pipeline integrity, Kah Soon hopes his experience in design & engineering will bring a different approach to integrity assessments that are largely anomaly-focused.
After participating in various conferences, Kah Soon noticed a gap in the energy industry: there was a lack of focus on pipelines in Southeast Asia (SEA). Aligning with YPP Malaysia’s mission and as one of its founding members, he has organized various pipeline-based technical and networking events. As the current Chair of YPP Malaysia, Kah Soon hopes that these events will create an increased level of industrial awareness and appreciation towards pipeline assets and its professionals in SEA.
Blake is a passionate advocate for the oil and gas industry and has spent more than 10 years in various technical and project management roles in the midstream sector. He currently works for Audubon Companies in New Orleans, LA as a Project Manager. Blake received his Bachelor of Science in Civil Engineering from Louisiana State University in 2014, his Masters in Business Administration from the University of Houston in 2018 and is a certified PE in several states. He is known for his enthusiasm and dedication to sharing his positive messages and insights with others. He is an active leader of Young Pipeline Professionals (YPP) USA and has been engaged in several other young professional organizations throughout his career. Blake is also active within the INGAA Foundation, the Southern Gas Association’s Multi-Generational Leadership Committee and serves on SGA’s Executive Council. Blake’s passion for the industry and his commitment to knowledge transfer and young professional advancement have earned him respect and recognition both within and outside of his organization. He is a valued member of the industry, and his contributions continue to make a positive impact on the industry and the communities he serves.
James Dean
Plastometrex, Cambridge, UK
Indentation Plastometry is a novel approach for measuring stress-strain curves from indentation tests. It differs from scratch testing and Instrumented Indentation Testing (IIT) in several important ways – all of which are covered in the presentation. The underlying scientific methodology (an accelerated inverse finite element analysis) is also discussed in detail. A new tool for in-ditch Material Verification that employs Indentation Plastometry is now available and in use, but to support its adoption on oil and gas transmission pipelines, the tool has recently been subjected to a period of intense validation in cooperation with several network operators, several service providers, and the PRCI. By June 2023, 125 pipes had been tested. Those test results indicated that the tool has industry-leading accuracy levels (MAPE numbers) which is expected to be of interest to pipeline integrity management teams. These assertions have been corroborated through independent analyses of the validation testing data by RSI Pipeline Solutions LLC. In addition to MAPE numbers, alternative metrics for characterizing the accuracy of this and other tools for material verification were also examined (through tests conducted on the same pipe samples). These statistical methods included Clopper-Pearson, Hanson-Koopman, a one-sided prediction interval method, and a linear regression method, with the outcome being that Indentation Plastometry is extremely well suited for fast, accurate and repeatable measurement of pipeline material properties.
The presentation will cover the details of the validation testing journey, the validation test results, and the statistical analyses that were conducted. Further results obtained between June 2023 and February 2024 (predominantly through blind network qualification tests) will also be covered.
Morgan Dormaar1, Derrick Hunter1, Cory Solyom2, Dixit Patel3, Wade Forshner4, Michael Callan5
1PureHM, Edmonton, Canada. 2PureHM, Calgary, Canada. 3TC Energy, Calgary, Canada. 4Pembina Pipeline, Calgary, Canada. 5Keyera Corp, Grand Prairie, Canada
Although a lost or stuck pig is rare, when it does occur, the costs can be extremely high, raising the location efforts to the highest priority.
A lost or stuck pig in a pipeline can have a serious impact on an operator’s ability to transport product. While uncommon these days, this does still occur, and when it does it can be detrimental to the safe and efficient operation of an Oil and Gas pipeline. Therefore, the ability to identify the location of the obstruction quickly is of utmost importance and can become a singular highest priority for the pipeline operator. Recent advancements in technology have facilitated such locating efforts, and saved operators time, expense and aggravation.
Oil and Gas pipelines are comprised of ferromagnetic materials, such as iron, nickel, steel and other materials. Large Standoff Magnetometry (LSM) technology is known to be used to identify and locate elevated levels of stress through the measurement of the magnetic field surrounding steel pipelines. LSM detects inverse magnetostriction (also known as the Villari effect) which is the change of the magnetic susceptibility of a material when subjected to mechanical stress. LSM technology has been used to detect defects as they appear as changes in the magnetic field around the pipeline which can indicate the presence of stress on the pipe. Thus, LSM can identify stress concentration caused by full pipeline blockages.
This paper will discuss how the XLI PWA technology works to locate lost or stuck pigs, and review 3 successful case studies.
Case Study 1 will discuss locating a lodged MFL tool in a 42” Gas pipeline. PureHM worked with TC Energy to locate an MFL tool that had become lodged in their line. TC Energy was ready to excavate and cut the tool out but required confirmation that they were in the right area before investing significant resources into the tool retrieval process, PureHM was able to mobilize and confirm tool location in a single day.
Case Study 2 will explore a project where a pig was lost and was fully obstructing the pipeline. Pembina provided several potential locations where the pig was thought to have stopped moving. Within 2 days PureHM was able to locate the stuck pig and the front of the blockage. Pembina was able to free up the stuck pig by Hot-Tapping.
Case Study 3 will present a more complex project where PureHM worked with Keyera to identify the location of multiple stuck pigs that were being obstructed by a wax slug in a 4-inch pipeline. PureHM worked over a period of 4 days to identify the location of the 2 stuck pigs. Keyera was then able to heat the pipeline at the location identified by the XLI PWA Technology and melt the wax obstruction to get the pipeline operational again.
Brian Ellis1, Louise O’Sullivan2, J Aidan Charlton2, Ben Lowry3, John Norman3, Jake Opdahl3
1pipelinelogic, Lakewood, CO, USA. 2Penspen, London, UK. 3Teren, Inc., Lakewood, CO, USA
The integration of pipeline digital twins with geohazard modeling presents a groundbreaking approach to enhance the safety and resilience of critical energy infrastructure. This presentation explores the synergy between pipeline material data, inline inspection technology, and advanced geohazard modeling techniques to create comprehensive geohazard threat assessments.
Traditional geohazard assessments often rely on limited data sources, leading to potential vulnerabilities in pipeline systems. However, by combining detailed pipeline material information and high-resolution inline inspection data, a more accurate and robust representation of the pipeline’s condition and vulnerabilities can be achieved. These digital twins provide a dynamic and real-time view of the pipeline’s integrity, enabling proactive maintenance and risk mitigation strategies.
The core of this presentation delves into the following key areas:
In conclusion, the integration of pipeline digital twins and geohazard modeling represents a transformative paradigm shift in pipeline management. This presentation demonstrates how this innovative approach empowers pipeline operators to proactively identify and mitigate geohazard-related risks, ensuring the long-term reliability and sustainability of energy infrastructure.
KEYWORD(S) FOR SUBJECT AREA: Geohazards, Geospatial Systems and Data
Kirsty McDermott1, Andy Fuller2, Chris Lyons2, Andy Brealey3, Jeffery Stephen Jones3, Neil MacKay4
1National Gas Transmission, Warwick, UK. 2PIE, Newcastle, UK. 3DNV, Loughborough, UK. 4STATS, Aberdeen, UK
National Gas Transmission own and operate the National Transmission System (NTS), the backbone of British Energy. The NTS feeds homes and businesses the essential gas required for life today in the UK. When operating above 70 bar, like most of the network does, the potential of failure or downtime of these pipelines has a critical impact on how interventions are carried out. However, changing how we do these interventions isn’t as simple, but why can’t we just make it so?
In line isolation tools have never been used on downstream onshore pipelines in the UK before. Regardless of the experience of others, NGT must assure itself through a process of due diligence that the new technologies and techniques do not create an immediate threat, or future integrity threats to the remaining life of the pipeline. NGT has developed an approval process, and has been trialling and testing tools, to develop an unbiased viewpoint built on evidence on the operational acceptance and integrity implications for the pipeline.
NGT has conducted an Isolation Joint replacement using a Pipeline Isolation Tool, instead of traditional venting (emissions reduction) and the need for recompression operations or alternative more invasive options (stoppling and bypass). The technology provided a fail-safe, leak tight double block, and monitor isolation, keeping a 48” pipeline fully pressurized at 56bar for 56km to the nearest block valve upstream. This method can help to reduce NGT’s emissions and operators’ exposure to high hazard methods.
Colin Scott, Abu Hena Muntakim
Northern Crescent, Calgary, Canada
Stress corrosion cracks are typically found in colonies comprised of multiple parallel aligned cracks. However, they are usually assessed as individual (or single interlinked) cracks, assuming the deepest of the colony represents the crack driving force for failure. This common approach does not account for the effects of crack shielding. It is known that neighboring cracks may dissipate stress intensity and result in a lower crack driving force.
In this work we use FEA to estimate the stress intensity factors associated with crack colonies. Results demonstrate how stress intensities in colonies are decreased relative to those of individual cracks. This is consistent with recent industry model studies that tend to underestimate critical failure pressures of in-service SCC flaws. It also indicates a fracture mechanics contribution to the known phenomenon of crack dormancy, which is often attributed to electrochemical and kinetic factors. The findings can be used to modify fitness for service assessments and improve SCC integrity program efficiency.
Mick Ellem1, Mark Sigley1, Olivia Chung2
1First Gas Limited, New Plymouth, New Zealand. 2Quest Integrity NZL Limited, Wellington, New Zealand
First Gas operates the natural gas transmission pipeline network in New Zealand. In 2022, crack-like linear indications on the long seam of the pipeline were identified by non-destructive testing (NDT) carried out opportunistically during coating refurbishment of a length of pre-1971 pipeline. Quest Integrity were engaged to investigate these crack-like linear indications. Metallurgical analysis of coupons removed from the pipeline concluded that the crack-like linear indications observed were Selective Seam Weld Corrosion (SSWC). With knowledge of this new threat, First Gas initiated a work program to manage this risk in the pipeline.
The work program included a Like-and-Similar analysis of the three most recent Magnetic Flux Leakage (MFL) metal loss ILI data sets collected in the pipeline and metallurgical analysis results, and additional field verification using advanced ultrasonic methods to further characterize metal loss features interacting with the long seam. Corrosion growth rates determined from the Like-and-Similar analysis and characterization of features detected ultrasonically and/or metallurgically verified were utilized in a Fitness-for-Service and remaining life assessment of external metal loss features, both interacting with and away from the longitudinal seam weld.
First Gas used the results obtained from the above investigation to update their integrity management plan for their pre-1971 pipelines, now including management of the threat posed by SSWC. This paper presents the full scope of work performed by First Gas and Quest Integrity to manage the threat posed by SSWC for the pre-1971 pipelines and shares the learnings obtained from the process.
Keywords: ERW pipe, Pipeline integrity management, Corrosion, Selective Seam Weld Corrosion, Crack-Like Features
Kerstin Munsel1, Thomas Meinzer2
1NDT Global, Houston, USA. 2NDT Global, Stutensee, Germany
When a pipeline is inspected, recorded pipeline data is manually or automatically evaluated. Regardless of the pipeline condition (such as degree of corrosion), once the features meet performance specification requirements, the data analysis and its result are in no way affected.
But what about inspections that, for various reasons, do not correspond to the standard and feature complexities are at the limit of the performance specification or are completely below it? What if the feature is still detected but not recorded correctly and the data evaluation is permanently impaired or appears impossible at first glance? What if the relative position of the features further increases the complexity of the analysis? Is it still possible to extract the essential information from the recorded signals?
Even under difficult conditions, detailed UT data analysis can provide high-precision results. This was evident in a non-standard 6″ project, confirmed by field measurements, and will be presented in more detail in this paper.
KEYWORD(S): 6” pipeline, challenging internal corrosion anomalies, non-standard analysis
Seyed Hamed Fatiminia1, Eduardo Munoz2
1Dynamic Risk, Calgary, Canada. 2Dynamic Risk, Houston, USA
Sensitivity analysis is paramount for improving the accuracy and robustness of oil and gas pipeline quantitative risk models. As a result, sensitivity analysis of the risk models is now a requirement under §192.917(4)c of the Gas Mega Rule – Part 2 for gas pipelines. The inherent complexity and interdependency of factors influencing pipeline risk require an in-depth comprehension of the sensitivity analysis methods. Fitness-for-service calculators are integrated into some quantitative models; though extensive validation work has been reported, a proper sensitivity analysis has often been omitted in benchmark studies and reviews. The primary objective of this paper is to provide an in-depth review of various sensitivity analysis techniques, highlighting their strengths, limitations, and practical applications in pipeline risk assessment. The comparative analysis is conducted based on multiple criteria, comprising computational efficiency, accuracy, ability to capture interactions between risk variables, and suitability for handling uncertainties inherent to pipeline systems. The findings of the comparative study provide valuable insights into the strengths and limitations of various methods, aiding practitioners in selecting the optimal sensitivity analysis technique based on their modeling objectives and data availability. Real-world case studies are provided to illustrate the practical application and results of some of these techniques.
Woosik Kim1, Dongil Kwon2, Dongseong Ro3
1FRONTICS INTERNATIONAL Inc, Seoul, Republic of Korea. 2Seoul National University, Seoul, Republic of Korea, 3FRONTICS AMERICA Inc, Mount Prospect, USA.
US federal rules, DOT 49 CFR §192.607, require that records documenting physical pipeline characteristics and attributes, including diameter, wall thickness, seam type, and grade, must be maintained for the life of the pipeline and be traceable, verifiable, and complete. Specifically, the PHMSA report on the integrity verification of ERW seam pipelines highlights the significant impact of local properties on failure pressure and remaining life predictions and thus reinforces the development of inspection tools in routinely quantifying local strength and toughness of materials.
This paper investigates the effects of different ERW seam manufacturing processes on the local microstructure and mechanical properties of seam welds on operating pipelines using AIS system of FRONTICS Inc. The instrumented indentation technique, followed by additional microstructural observations, was utilized to assess hardness, tensile properties, and fracture toughness of LF ERW and HF ERW pipes with different manufacturing years. Ultimately, this paper will present a strategy for the non-destructive analysis of operating ERW pipelines, simultaneously providing a classification guideline on seam welding methods and pipe integrity assessment.
Russell Giudici¹, Ahmed Hassanin², Atul Ganpatye², Chris Alexander²
¹Advanced FRP Systems, Weymouth, USA, ²ADV Integrity, Magnolia, USA
ABSTRACT
Non-metallic, composite reinforcement systems for pipes have become a standard method for repairing a range of defects including corrosion, dents, gouges, cracks, girth welds and seam defects. Composite repairs for pipes are hand applied in the field, making application defects a potential source of concern, especially for larger repairs and hard to reach areas. The most common defects observed are air pockets trapped within the layers of the composite wrap.
This paper explores the effects of air bubbles of varying sizes and depths within the composite repair system. Specifically, we will look at the effects on the pressure capacity of repaired pipes with designed defects by performing live, hydrostatic pressure tests. We will also look at the effects of air bubbles on the liquid tightness of composite wraps that are applied on pipes with through wall failures. Finite element analysis was performed to analyze any additional stresses on the composite wrap system with air pockets of various sizes and at a variety of locations within the composite reinforcement system. Finally, we will look at the results of both the physical pressure testing as well as the computational analysis to help provide real world guidelines to determine when air bubbles require repair in the field.
Rhett Dotson1, Briant Jackson2, Matt Stevenson2, Chris Newton2
1D2 Integrity, LLC, Houston, USA. 2Phillips 66, Houston, USA
Many pipeline operators have performed bending strain assessments based on IMU data and received results that are challenging to interpret and properly sentence, especially if the assessment identified hundreds of features. These challenges can be compounded if the operator acquires a second IMU data set and elects to perform another bending strain assessment or a comparison assessment between the two data sets. In these situations, operators often observe significant variations in the number of reported bending strain features and the reported strain magnitudes associated with those features. These challenges can rarely be solved by comparing the final reports as the graphical information for the bending strain features is often rendered differently between vendors. This paper presents the results of a case study comparing four IMU data sets acquired over a decade on the same pipeline segment where the number of reported features varied from 195 to 384. The paper examines the causes of this variation in reported features including the influence of gage length, signal noise, and analyst judgement. The case study also identifies common challenges that occur when comparing multiple IMU data sets and provides strategies for recognizing and overcoming these challenges. The paper concludes by identifying how bending strain reporting requirements can be standardized and help operators minimize these challenges in future assessments.
Joel Van Hove1, Casey Dowling2, Pete Barlow3
1BGC Engineering Inc., Vancouver, Canada. 2BGC Engineering Inc., Golden, USA. 3BGC Engineering Inc., Edmonton, Canada
Well-structured geohazard management programs (GMPs) for pipeline systems have become common over the last two decades in North America as pipeline companies have become more aware of the risks presented by natural hazards and the value in adopting proactive approaches to manage risk. The case study presented in this paper represents the GMPs of 30 major pipeline companies in North America comprising approximately 100,000 miles of operating and actively managed pipeline. The performance of these GMPs has been measured to reduce pipeline failure rates from geohazards 4 times. Over the past 10 years more than 95% of the observed geohazard pipeline failures have been from slow-moving landslides. The study scope includes approximately 10,000 landslide crossings. The annual probability of failure given pipeline impact from a slow-moving landslide has previously been estimated at 1 in 50, meaning any landslide which is actively moving and intersecting a pipeline presents a potentially serious integrity concern. The primary challenge with managing slow-moving landslide hazards is that determining landslide activity without instrumentation is often not possible, and installing conventional instrumentation such as slope inclinometers at such a large number of landslides is prohibitively expensive. Slow moving landslides also cannot reliably be visually identified as movement rates are often low enough that visible surface disruption is subtle or undetectable, but those same movement rates will be enough to cause pipeline failure over the life of the pipeline. To address this challenge many forms of low-cost instrumentation have been pursued to measure ground movement and/or pipeline impact including Interferometric Synthetic Aperture Radar (InSAR), lidar change detection, and in-line inspection tools such as axial strain and inertial measurement unit (IMU). Over the last 10 years IMU has become a critical and frequently utilized tool for assessing landslide activity and has been integrated into the geohazard management programs of all the operators in the study scope. In 2022 IMU was credited for identifying 53% of the active landslides where operators completed critical interventions to manage risk (e.g., pipeline shut in, stress relief mitigation). Key lessons and observations for successfully integrating IMU into GMPs are presented from a case study spanning 10 years and 100,000 miles of pipeline.
Megan Grzelak1, Trevor Ortolano2
1NiSource, Merrillville, USA. 2Campos EPC., Denver, USA
The intent of this technical paper is to illustrate a repeatable approach to validating station assets through a complete records and material verification process to better understand MAOP Reconfirmation.
By utilizing modern technology, established best practices and detailed records research, one can generate a near complete understanding of the assets at a particular facility. Using the data gathered from records and subjecting it to effective tooling with the use of a file geodatabase, the operator can understand the compliance challenges of these assets spatially and better prepare for the execution of MAOP Reconfirmation. A final, but not to be overstated, aspect of this program is a demanding definition of Traceable, Verifiable and Complete records that is well understood by all parties involved.
To better aid the understanding of the results, a series of “one line” isometric drawings are also created to act as a visual aid relative to requirements like pressure test coverage, %SMYS, Work Order History, etc. These tools are especially effective when presenting large stations (multiple settings built and upgraded over many decades) to the various stakeholders for their input and support as this evidentiary process becomes a plan of action relative to MAOP Reconfirmation.
With these deliverables [file geodatabase (FGDB), single line isometrics and a final report with relevant information and appendices] an operator can assess gaps in Compliance Material and explore further material verification efforts to mitigate the impacts of MAOP Reconfirmation to their respective systems and budgets.
While the initial efforts of this program are geared predominantly at executing MAOP Reconfirmation, by introducing the FGDB at the onset, the operator can develop a living data organism that has many applicable uses to many departments within an operator’s organization over the life of that facility.
Categories: MAOP Verification and Materials Verification
Daniel Bahrenburg1, John Norman2, Jeffrey Haferd3
1ROSEN USA, Houston, USA, 2Teren 4D, Lakewood, USA, 3Marathon Petroleum, Findlay, USA
Landslide threats continue to be a prevailing concern for pipeline operators and the public. Although several methods and technologies exist to detect and monitor these geohazards, determining what strategies are most effective and efficient for integrity management can be challenging. High-resolution inertial measurement (IMU) data can be utilized to detect anomalous strains resulting from pipeline displacement. The knowledge of experienced geotechnical experts can then be leveraged to review and characterize geohazards coincident with these anomalies in more detail. Although this strategy is extremely effective, timely and detailed geohazard reviews can be challenging due to a manual analysis process and expert availability. However, without expert review, pipeline company integrity managers can be left with concerns regarding how to determine what results constitute an actual concern for the pipeline. To streamline efforts to prioritize landslide-affected pipelines, Marathon Petroleum has adopted an alternative, highly efficient approach to geohazard screening, which incorporates IMU-based bending strain assessments and automated geohazard detection/characterization using high fidelity LiDAR (Light Detection and Ranging) data. This paper will present a brief overview of the ROSEN method of pipeline movement detection using IMU data from multiple in-line inspections, followed by an outline of the Teren method for streamlined geohazard screening and severity assignment. To conclude, a review of several case studies will provide examples where a combination of high strain and/or pipeline movement was detected coincident with high-severity landslides based on an Absolute Geohazard Assessment (AGA) score for areas of confirmed slope movement.
Rhett Dotson1, Jeff Haferd2, Karim Kabbara2, Nic Roniger2
1D2 Integrity, LLC, Houston, USA, 2Marathon Pipeline, Findlay, USA
The use of bending strain analyses for identifying and managing pipeline geohazards has grown significantly in the last decade. While bending strain assessments are useful for identifying and prioritizing geohazard features impacting pipelines, it is understood that bending strain assessments cannot provide the total strain which is required for comparison to calculated tensile or compressive strain capacities in determining fitness for service. The inability to easily calculate membrane strain and the resulting total strain in impacted pipelines represents a gap in the industry. A few simplified methodologies have been proposed to estimate the membrane strain based on the displaced shape of the pipeline, and some newer ILI technologies are available for explicitly measuring the membrane strains. Level 3 numerical analysis is another method that can be used to estimate the membrane, bending, and total strain states in a pipeline impacted by a geohazard. This paper presents the results of a study covering nine finite element analyses completed on separate geohazards with varying characteristics. The paper discusses the methods used in the study to construct the models, including incorporating initial strains and estimating as-built conditions of the pipeline. Comparisons are provided between the membrane strains calculated explicitly in the models and membrane strains estimated using simplified methods. The study examines how membrane and bending strains develop and progress at larger pipeline displacements noting important differences in axially and laterally oriented geohazards. The conclusions from this study provide useful insights to operators on how to perform level 3 geohazard assessments, and how to properly use the results to make informed integrity management decisions for monitoring or mitigation or geohazards threats.
Mohamed Elseify, Jeff Sutherland
Baker Hughes, Calgary, Canada
Pipeline systems experience a range of strain conditions along their length. These are either factored into the pipeline design as known operational strains or as strain resulting from additional external loadings that are potentially unknown during the design or construction phases. Detecting, monitoring, and understanding these additional strains in combination with operational strains are a key part of a pipeline integrity management program. Surveying with inertial mapping tools have been commonly used since the late 1980’s for accurate measurement of bending strain – which unfortunately only provides a part of the picture. The development of the ILI axial strain measurement tool (AXISS™) was a response to fulfilling a pipeline operator’s need for axial strain measurement in combination with available bending strain information to enhance their geohazards risk management programs.
After a long period of comprehensive field testing and validation, supported by a number of partner customers, Axial Strain Inline Inspection transitioned from a developmental to commercial service more than 10 years ago. Since then, over 20,000 km of data has been collected with many high strain locations successfully identified and mitigated. While axial strain inspection is now established as a proven and important tool for a pipeline operator to assess geohazard and other strain related threats, that experience has provided key insights as to where the current technology strengths lie and of course where we need it to go next to provide the level of information truly needed to optimize our full understanding of strain-based threats. This paper gives a detailed overview of some of those experiences discussed, examples of the applications of the technology and the types of strain events identified. Secondly, and more importantly, this paper provides key insight into the latest developments of the technology that will address the remaining unmet needs of the geohazard and stress engineers tasked with establishing a complete picture of pipeline strain condition, allowing them to effectively optimize any mitigation measures or repair programs.
Tristan Jones, Ivan Thesi, Cesar Espinoza, Andres Gonzalez, David Bastidas
ROSEN, Houston, USA
According to 2018 PHMSA Stakeholder Communications Fact Sheet, an estimation of 18% of pipeline failures in the United States (from 1998-2017) were caused by corrosion. Calculating accurate remaining strength of corroded pipe with complex corrosion, such as axially aligned clusters with multiple pitting on pitting metal loss anomalies, has historically been a challenge for operators. Traditional Effective Area Methods (EAM) for assessing the remaining strength of complex corrosion anomalies, such as Modified B31G and Detailed RSTRENG can lead to overly conservative results and extensive repair campaigns. In these cases, it is difficult for operators to distinguish between the critical repairs and uncertainties, potentially preventing them from focusing resources into other pipeline mitigation activities. A more detailed evaluation of corrosion geometry through an advanced fitness-for-service method, known as Plausible Profiles (Psqr), can be used to gain a better estimate of the remaining strength of pipeline areas with complex corrosion. However, it is important to understand when this method is applicable and when it will yield the most benefits for pipeline operators. With proper selection criteria, ideal candidate corrosion anomalies can be identified for this method, which will add efficiency to the pipeline remediation process and provide more accurate results. This paper will discuss the criteria for selecting corrosion anomalies for implementation of the Psqr method in combination with a rationalized repair strategy. The selection criteria consider aspects associated with anomaly morphology, assessment depth, length/width ratio and potential failure mode. This paper will present how a number of excavations was reduced by more than 70%, with no impact to public safety, based on a case study of a natural gas pipeline. The remaining strength of 60 corrosion anomalies was extended, facilitating the optimization of the maintenance planning and expenditure, and supporting the pipeline Integrity Management Plan (IMP).
Casey Dowling1, Pete Barlow2, Joel Van Hove3, Teko Hanvi4, Jim Hart5
1BGC Engineering USA, Golden, USA. 2BGC Engineering, Edmonton, Canada. 3BGC Engineering, Vancouver, Canada. 4Enbridge. 5SSD, Inc.
Inertial measurement unit (IMU) bending strain data has been recognized as a crucial tool in detecting ground movement impact along operating pipelines. In Line Inspection (ILI) vendors produce bending strain and movement reports which often include impact from landslides and sinkholes, but also include a host of other causes. While these bending strain reports serve as a useful initial screening tool, previous studies have found that approximately 90% of these reported features are related to pipeline construction or operation, not ground movement impact. It is not uncommon for hundreds of bending strain features to be reported on a single 100-mile pipeline segment, and it is important for pipeline operators to be able to quickly differentiate ground movement caused bending strains. Unlike construction-related bending strains, ground movement tends to increase strain demand over time and often has a larger longitudinal strain component because of axial loading or pipe elongation. Often, landslides and sinkholes produce readily apparent signatures in IMU data that are evident during a cursory review. Drawing upon 10 years of experience using IMU data to characterize and monitor geohazard impact along pipelines and geotechnical assessment of more than 6,500 bending strain features, this paper provides examples of common IMU signatures indicative of landslide and sinkhole impact with the intent that operators can learn to spot the most obvious potential geohazard impact sites and prioritize those for further assessment or action. Examples of signatures from single run and run-to-run IMU data are presented along with a discussion of the basic mechanisms that produce the signatures. Key ground-movement signatures within other IMU outputs such as pitch, heading, and position are also discussed. Construction-related IMU signatures are provided to help operators understand how these differ from ground movement signatures.
Wes Gardner
STATS Group, Calgary, Canada
Operators can often encounter difficulties in isolating sections of their pipeline to facilitate essential safe repair or maintenance activities if appropriate valves are absent from the line. In-line isolation pigs provide fully proven and monitored dual seal barriers that ensure the safe breaking of containment on pressurized systems in compliance with the highest industry standards.
Unlike traditional Line Stopping activities, piggable isolation tools require no welding or cutting into live lines, leaving no residual fittings or hardware on the pipeline. This eliminates project costs associated with fittings, welding and inspection and reduces the risk of leak paths from buried pipeline flanges post operations.
Line stopping often requires pipeline excavation and site establishment including lifting and rigging operations which is usually eliminated by deploying inline isolation pigs. Tracking, operation and communication with in-line isolation pigs can be achieved remotely through ground and pipe wall preventing the need for costly site establishment and reducing the risk of digging and lifting operations around the pipe.
In-line isolation tools significantly reduces, and in some cases eliminates, the requirement to vent or flare harmful emissions into the atmosphere during maintenance activities. One of the most significant environmental advantages is the substantial reduction in greenhouse gas emissions vs venting the pipeline. In the case of long, large diameter gas pipelines, this can prevent the potential discharge of thousands of tons of methane into the atmosphere.
Following the completion of the maintenance activities, a reinstatement leak-test of the replaced valve or pipework can be performed while the isolation is still in place. And provides an alternative to golden welds.
Real world examples will be discussed where double block inline isolation tools have facilitated pipeline modification, resulting in reduced project costs and production downtime, while minimising the discharge of emissions.
The utilization of in-line isolation tools not only enhances the efficiency and safety of pipeline repair and maintenance but also aligns with increasing demand to reduce emissions and create a more sustainable energy infrastructure for the future.
Challenges for this technology will also be discussed, including long distance deployments in gas pipelines where the tools must be stopped midline with suitable accuracy. Also, a high degree of confidence of pipeline condition (bore, wall thickness) is required before inline isolation tool pigging as the hard OD of the tools is close to the ID of the pipe and good information is sometimes difficult to obtain.
Brian Cooper1, Matthew Moshier2, John El-Hallal2, David Anstead3, Lance Wethey4
1HT Engineering, Inc., Grand Rapids, USA. 2TC Energy, Chicago, USA. 3BP, Chicago, USA. 4ROSEN, Houston, USA
This paper presents the lessons learned by the team that planned, designed, and managed a project to run gauge pigs and in-line inspection (ILI) tools through an idled pipeline. The runs covered the multiple piggable segments of a nitrogen-filled 450-mile liquid hydrocarbon product line in preparation for its return to service. Running ILI tools in lines previously in liquid service and subsequently filled with nitrogen presents challenges. This study provides insight into the pipeline system characteristics, including human factors, that must be addressed to achieve successful tool runs in nitrogen.
For this project, the team synthesized requirements from management, technical, and operations stakeholders, and developed an execution plan. During planning, the team built a numerical hydraulic model to calculate the nitrogen flow rates and pressures required to successfully run the pigs. The team worked with local operations personnel and the ILI vendor to develop detailed work procedures. During operations engineers worked on site tracking procedure completion and monitoring operating conditions. Two ILI runs failed to meet acceptance criteria, one due to abnormal ILI tool drive cup wear and one due to inadequate nitrogen control procedures. The team identified the problems and designed solutions. After each operation, the team captured lessons learned and updated subsequent procedures accordingly.
The execution plan provided the company’s management with confidence that the project could be completed safely. The numerical hydraulic model allowed the team to optimize nitrogen injection and release locations, plan injection and release operations, and verify that pressures and pig speeds could be kept within acceptable operating ranges. The solutions for the failed runs (a revised ILI tool drive cup design and a new procedure for nitrogen control) prevented recurrence of the problems and resulted in successful reruns. The lessons learned process allowed the team to improve its numerical model and human performance as the project progressed. By monitoring and analyzing the operating conditions in real time, the engineers were able to provide the project manager with the information and recommendations needed to run the operations safely and recognize emerging problems quickly.
Pipeline operators are frequently faced with the need to respond to changing market conditions and must be able to safely inspect idled lines in a timely manner. The results of this study provide operators with insight into the factors that must be addressed to achieve successful tool runs in nitrogen. These results complement the findings of Bonner, D., Greig, A., Lindner, H., Becker, J., Roulston, B., (2018, September 24-28). REACTIVATING A LEGACY PIPELINE – SIMULATING ILI RUN BEHAVIOR, OPERATION OPTIMIZATION, AND PROJECT CHALLENGES. International Pipeline Conference, Calgary, Alberta, Canada.
Kevin Spencer1, Phillip Bondurant2, Haraprasad Kannajosyula2, Jabin Reinhold3
1Quest Integrity, Calgary, Canada. 2Quest Integrity, Seattle, USA. 3Quest Integrity, Traverse City, USA
Small diameter pipeline crack in-line inspection (ILI) has typically been an underserved industry segment, primarily due to the difficulties associated with the physical limitations of packaging sensors, electronics and power sources within a small housing which is then able to successfully navigate challenging pipeline configurations. New ILI technologies are often therefore introduced for larger diameter tools and then miniaturized as far as possible. This paper presents the development, testing and implementation of an Electro-Magnetic Acoustic Transducer (EMAT) inspection vehicle specifically designed to detect and characterize longitudinal cracks in small diameter and difficult to inspect gas pipelines.
The paper will present the initial tool development and subsequent implementation on to a free-swimming bi-directional inspection vehicle. Since then, the tool has successfully and safely completed its initial inspections which provided critical information in the tool’s performance and further design improvements. Secondly the paper will present, via case studies, the tool’s performance in detecting and identifying axially orientated cracking anomalies through both full-scale testing and field validations. The case studies include comparisons with additional inspection data streams, providing an integrated approach to the identification of complex morphologies or interacting anomalies.
Rogelio Guajardo1, Eder Prestegui2, Träumner Katja3, Victor Haro3
1NDT Global Spain, Barcelona, Spain. 2NDT Global Mexico, Mexico City, Mexico. 3NDT Global Germany, Stutensee, Germany
ERW penetrators are a subtype of lack of fusions. They are planar anomalies located in the bonding line. What differentiates them is that they are short in length (<1.0in) but deep e.g., >50% of the pipe wall. The integrity risk of these anomalies is the possibility to leak instead of bursting.
Ultrasonic Shear Wave (UTCD) technologies are the recommended ILI choice to address planar/linear anomalies such as the lack of fusions and therefore the penetrators. However, the minimum probability of detection (POD) dimensions from the UTCD tools in the long seam are 1.0in x 0.079in (length x depth) placing the penetrators below performance specification. This raises the questions: 1- What options do we have to address these features? and 2- What are the capabilities from UTCD ILI inspections?
The goal of the paper is to provide a comprehensive evaluation of 1- UTCD tool settings and configuration, 2- UTCD measurement techniques pulse echo and pitch & catch, and 3- Analysis procedure updates required to identify and size these features which will allow the reader to understand the shear wave capabilities when selecting and ILI UTCD technology to address these features.
Key words: ILI inspection, UTCD, Lack of fusion, ERW weld, crack detection, UT technology, Seam weld, ILI application, ILI analysis
Laurie Knape
API, Houston, USA
In November 2022, API and the joint Pipeline SMS Industry Team published Pipeline SMS: A Contractor’s Guide to give pipeline contractors and service providers an enhanced understanding of how the scope of their safety programs should be integrated with an operator’s Pipeline SMS. A tool has been created with industry collaboration, showcasing 56 key requirements of API RP 1173: Pipeline Safety Management Systems, that will help operators and contractors integrate their safety efforts. In this presentation, we will show how the newly developed tool will help contractors and service providers mature internal safety programs that support Pipeline SMS. The tool is scalable based on the size of the organization and the scope of work and can be a valuable tool in starting the PSMS journey. In addition to reviewing the tool, we will highlight good practices seen from a pipeline operator and a service company on the value gained from the integration of their safety programs. API and the joint Pipeline SMS Industry Team have created a Contractor SMS Assessment pilot program. We will review the Contractor Assessment program’s step-by-step details and discuss deliverables, scoring, and benchmarking.
Corey Richards1, Thor-Staale Kristiansen2, John Nonemaker3, Alvaro Patino3, Borge Hamnes2, Oyvind Gravdal2
1ROSEN Group, Calgary, Canada. 2ROSEN Group, Bergen, Norway. 3ROSEN Group, Houston, USA
In response to pipeline restrictions that prevent the use of common free-swimming in-line inspection equipment, self-propelled inspection solutions have emerged as a transformative alternative. Leveraging robotics, automation, and advanced sensing, these solutions can autonomously navigate complex pipelines without the requirement for conventional access points or product flow. The adoption of self-propelled systems enables operators to conduct comprehensive inspections in pipelines previously considered inaccessible. This paper outlines the utilization of a self-propelled tether approach supported by case studies. The paper will outline in detail the workings of the inspection tool, particularly: the ridged ring UT sensor unit, the modifications and testing to ensure the system could pass features in the line, and the electrically driven propulsion system.
The first case study introduces a self-propelled robotic Ultrasonic Wall Measurement (UTWM) solution deployed in a 16”/20” pipeline. While the focus of this case study is the deployment of this inspection solution in the 20” section, it will also compare a previous operational attempt with running a free-swimming 16”/20” tool in this line. Overall, the case study will outline not only how this solution better ensured the integrity of the line itself, but also how its execution reduced operational requirements while still collecting high-quality in-line inspection (ILI) data.
Case Study two will address the challenge of offshore pipelines situated in remote and rugged terrains. This case study presents a tethered self-propelled inspection device equipped with ultrasonic sensors. What was of particular interest in the case study was the tool’s ability to navigate over 11 complex bends. The study showcases the device’s technical abilities in conducting real-time assessments and overcoming access limitations inherent in such locations. Further the case study will also cover the extensive testing required to safely complete such inspections.
Paige Chenevey1, Eric Bergeron2, Alexandre Thibault2
1Marathon Pipe Line, Findlay, OH, USA. 2Flyscan Systems, Quebec City, Canada
Since the end of 2022, Marathon Pipe Line has been using and testing Flyscan Systems’ remote sensing technology over their liquid pipeline Rights-of-Way (ROWs) to benchmark and validate the use of machine learning (ML) algorithms, photogrammetry and hyperspectral imaging to perform real-time threat detection, liquid leak detection of crude oil and refined products, and other advanced imaging features related to geo-hazards.
This paper will present scientific approaches used, and real-life results from 198 patrols between November 2022 and August 2023 which identified 2,594 threats across 35,706 miles of ROW from Alaska to Texas, including the Rockies and the Mid-west.
Examples will include, what is potentially the first ever detection of a diesel seeper leak, identified below computational pipeline monitoring system detection thresholds using a hyperspectral imaging system during routine aerial patrols. Other examples will include detection of contaminated soils from third party activity, detection of real encroachments and documentation of various types of objects and activities on the ROW of interest to pipeline operators. Finally, examples of new imaging capabilities will be presented, including detection of exposed pipes after serious weather events, vegetation analysis, and erosion monitoring.
Richard Mcnealy1, Vahid Ebrahimipour2, Duran Mendoza1, Praveen Kumar3
1Chevron, Houston, USA. 2Chevron, Malongo, Angola. 3Xaaslabs, Sunnyvale, USA
While many upstream pipelines and flowlines are piggable, their operating characteristics may render them not smart piggable because they cannot be practically cleaned or configured to enable successful conventional high resolution in-line inspections. Minimally intrusive sensors are now available to pipeline operators that manage in-line navigation risks while recording full length data used to understand the condition of the pipe wall equivalent to a hydrostatic integrity assessment and detecting leak points-of-interest (POIs). This paper presents the results from a pilot deployment of a multi sensor device comprised of large standoff passive magnetometer sensors coupled with acoustic, pressure and temperature sensing capability all integrated into the form factor of a minimally intrusive maintenance pig. An understanding of fundamental magnetic theory is applied to the sensor data to characterize the interaction of a ferro magnetic body, i.e., steel line pipe, within a native magnetic field to conclude relative changes in the mass or changes in pipe wall thickness along the full length of the pipeline. The pilot also illustrates a method that leverages multiple sensor datasets using 1st principles equations to calculate various parameters for characterizing leak location and severity. Comparison of fundamental magnetic, acoustic and temperature quantities, measured by the sensors, with physical pipe wall truth data illustrates the basis for models developed to conclude pipe wall condition and integrity management actions consistent with equivalent understanding derived from a hydrostatic integrity assessment and effective loss of containment risk management using cloud-based software applications.
Anthony Tindall1, Steve Farnie1, Jeff Sutherland2, Stuart Clouston2
1Baker Hughes, Cramlington, UK. 2Baker Hughes, Calgary, Canada
It is well known that when corrosion pits interact, the interpretation of inspection data gathered by Magnetic Flux leakage tools (an indirect measurement technique) becomes challenging due to the nature of the overlapping and superimposing signal responses across the multi-defect profiles. Such “complex” corrosion is of particular concern to pipeline operators as it is these areas, particularly axially oriented, that are often the most critical to pipeline integrity. And then, being the most difficult to both interpret and size accurately, these can lead to “outliers” relative to conventional ILI specifications and industry guidelines (e.g. API 1163). Such outliers are increasingly grouped into two types, namely Safety Outliers (where defect severity is under called leading to underestimated remaining strength) or Resource Outliers (when defect severity is overcalled potentially leading to unnecessary digs).
The goal of any in-line inspection method is to represent corrosion fully and accurately on the pipe. To achieve best performance, we must be able to first detect when these complex or interacting signals occur and then, more importantly, interpret them correctly. In physics terms, the nature of MFL field leakage is a 3-dimensional vector and predictable, yet different signal responses to metal loss (and other features) are observed in each of these 3 vectors which can be quantified and characterized as an improved means to translate leakage signals to the corrosion they more accurately represent.
Single axis MFL, whether conducted with axially or circumferentially oriented magnetizers, will reach limits in its capabilities regardless of sensing resolution. MFL is a mature technology, and an operator today should expect most tools to perform to specification on isolated corrosion. However, the adoption of long proven Triaxial sensors, at optimal resolution, on Magnetic Flux Leakage inspection vehicles provides an integrity engineer significant advantages to minimize potential outliers when things are not so straight forward.
This paper will outline how the three independent components of the triaxial flux leakage response provide unique identifiers for cases of axial corrosion, highly asymmetrical defects, corrosion in corrosion, wide area erosion/corrosion with pitting, to name but a few. At the same time, the additional signal components provide independent measures that enable better performance in latest generation algorithm techniques and development than those trained on fewer inputs.
The authors will present real world examples of these unique identifiers being used in practice to interpret highly complex corrosion and the latest work Baker Hughes has been conducting in close partnership with our customers with the common goal to best manage these “complex morphologies” successfully and efficiently with one inspection.
Emmanuel Valencia, Atul Ganpatye
ADV Integrity, Inc., Magnolia, USA
Traditional dent assessments involve calculating deformation strains and stress concentration factors (SCF) as proxies for the severity of the dent. Typically, the determination of SCF requires advanced computational methods (like finite element analysis) with specialized software and skillsets. This can be time-consuming and subjective, greatly depending on the engineer’s skill level using the approach.
Of the two factors described above, deformation strain calculations have been well-established and definitive because strains can be directly and readily interpreted from the deformation geometry. Therefore, this paper only focuses on the SCF aspect where the proposed approach, using machine learning (ML), can significantly reduce the efforts and resources needed to determine the SCF.
Due to the non-linear relationship of the dent shapes and their corresponding SCF values, multiple deep learning ML methods were considered in this study. The final model architecture involved Convolutional Neural Networks (CNN) due to their ability to extract features, group objects, and discover valuable data patterns from unknown elements.
The CNN model was trained on 4,667 raw ILI data files containing dent shapes which underwent significant preprocessing, such as data normalization, filtering, and smoothing. The final model was selected after careful fine-tuning of the hyperparameters and comparison of 180 CNN model variations where it successfully predicted SCFs ranging from 1.04 to 10.69 with a root mean squared error (RMSE) of 0.418 and a coefficient of determination (R2) of 0.929, indicating a high level of accuracy and goodness of fit, respectively.
Although the results are favorable, the training dataset is biased toward a single pipeline operator and therefore does not represent the global statistics of dented pipelines. Along these lines, the paper discusses ideas and proposals for a more robust implementation of the approach for wider applications. The work demonstrates that the model has the potential to serve as an assessment tool to provide immediate, in-the-ditch guidance to pipeline operators, therefore reducing downtime and limiting resources.
Zain Al-Hassani1, Simon Slater2, Chris Davies3
1TC Energy, Houston, USA. 2ROSEN, Columbus, USA. 3ROSEN, Houston, USA
Gas transmission operators are now required by regulation to reconfirm the MAOP of pipelines lacking traceable, verifiable, and complete (TVC) pressure test records. TC Energy operates a 20” natural gas transmission pipeline in Northern Ohio, which has 54 individual segments that meet the requirements of a covered segment as per §192.624 (a)(1). TC Energy performed an Engineering Critical Assessment (ECA) of the pipeline to reconfirm the MAOP. The foundation of the ECA was a full suite of in-line inspection (ILI) technologies to detect, identify and size the anomalies that remain in the covered segments. This included ILI technologies capable of detecting crack-like anomalies, selective seam weld corrosion, and hard spots. ILI was also used to measure material properties and attributes when these were not known. Using the material data together with other data sets, the different populations of pipes within the covered segments were identified. TC Energy used this full suite ILI approach for ECA as pilot project. As such, a pressure test was also performed to confirm the applicability of the ECA approach. The ultimate aim of the exercise was to compare the two methods holistically across one example line to help develop a better understanding of which method should be used and when. This paper provides a walk-through of the ECA process performed by TC Energy and ROSEN. It provides a description of the documentation and specific content required by §192.632. It is intended to provide operators with an example of how an ECA is performed and highlight some of the critical aspects that have to be considered.
Jeff Sutherland, Melissa Gurney
Baker Hughes, Calgary, Canada
Since the introduction and validation of ILI Magnetic Flux Leakage (MFL) specifications for pinhole corrosion defects more than 10 years ago, industry has benefited greatly with gained experience with such capabilities.
This paper provides a brief review of the nature of “pinhole” ILI performance particularly for MFL inspection including the influences in providing accurate inspection results, as well as technical development steps to date regarding pipeline corrosion inspection and reporting.
The interpretation of API 1163 guidance has played a role in such perceptions and specifications that will be outlined in this paper. Similarly, the nature of “hard boundaries” behavior related to corrosion type categories (the “POF (Pipeline Operators Forum) categories”) plays a role. The need to address such perceptions will be described and real examples of features will be presented with case examples of isolated and complex corrosion morphologies.
Industry feedback, both in the field measurement improvements and volume of feedback features, has led to further improvements and possibilities beyond current ILI conventions.
The paper will then describe with examples of alternatives and with some description of new conventions of ILI performance for the future.
Michael Byington1, Facundo Nahuel Ignacio Lamas2, Rodolfo Eduardo Rodríguez2, Celeste Vera2
1INGU, Houston, USA. 2Pan American Energy, Cerro Dragón, Argentina
The development of conventional inline inspection technology has been geared towards ultra-high resolution tools requiring a completely cleaned pipeline and coming with increasing costs and data handling time. By comparing data between inspections, unconventional inline inspection tools equipped with off-the-shelf micro-electromechanical magnetometers provide actionable information on the best allocation of resources for digs and high resolutions tools as well as the location of unexpected changes such as illegal hot tap installations. To ensure an accurate comparison between inspections, the data of subsequent inspections must be perfectly aligned. This presentation will discuss a fully automated approach to align inspection data using Monte-Carlo based time warping strategies.
We will illustrate the method with a case study conducted by Pan American Energy. They installed a hot tap at an undisclosed location along a nearly 3,000-meter steel pipeline and asked INGU to locate it. The hot tap was unambiguously identified and Pan American Energy confirmed that the provided location was within the 6 meter acceptance criterion for the project.
KEYWORD(S) FOR SUBJECT AREA: ILI Analysis; Emerging issues, technology; Unpiggable Inspections and Technology
Amir Behbahanian1, Adrian Belanger2, Robert Coleman1, Paul Dalfonso1, Ron Lundstrom1
1T. D. Williamson, Salt Lake City, USA. 2T. D. Williamson, Houston, USA
Machine learning tools have been used for over a decade to process the large amounts of in-line Inspection (ILI) data and to report accurate sizing of metal loss features. With the explosion of software solutions that came with the advancement of graphic processing units, (GPU) power and memory available to the commercial market, the use of machine learning in processing magnetic flux leakage (MFL) tools for corrosion sizing now standard in the industry. An aspect of automation that does not get as much attention is the identification of features such as fixtures. Traditionally this task has been done either manually or with a semi-automated process based on signal pattern recognition by utilizing operator provided survey data. As fixtures are commonly used as a reference point when performing dig verifications, fast and effective methods for locating them are helpful.
This paper will present an approach using a machine learning method called semantic segmentation. There is an enormous amount of information contained in an MFL survey that has an image like structure with magnetic measurements sampled both axially and circumferentially on a grid. The powerful technique of semantic image segmentation, which is used in applications like autonomous driving, medical imaging, urban planning, manufacturing, robotics, etc., is ideal for analyzing this data.
Four different models will be presented to demonstrate how a combination of them can perform the task of identifying and classifying pipeline features. This work will lay the foundation of not only automating a semi-manual task but training models to focus on features of concern to the operator. Due to concerns about aging infrastructure, identifying certain types of fixtures can help with integrity threat management. The use of these models has the potential of identifying specific features that have known integrity concerns and facilitate a pipeline owner’s remediation plan.
Michael Turnquist1, Yohann Miglis2, Yanping Li3
1Quest Integrity, Boulder, USA. 2Kinder Morgan, Colorado Springs, USA. 3Enbridge, Edmonton, Canada
A critical factor in determining the remaining strength of a corrosion feature intersecting a longitudinal seam weld (LSW) is whether the corrosion is preferential to the weld (often referred to as selective seam weld corrosion or SSWC) or coincident with weld yet no preferential attack of the bondline is occurring. SSWC is a form of corrosion that most often occurs in the bondline of electric resistance welded (ERW) and electric flash welded (EFW) pipe and typically has the appearance of a V-shaped groove. Past research supports that if no preferential attack of the LSW bondline is occurring and the weld has adequate ductility, the presence of the LSW does not reduce the remaining strength of the feature when compared to features not intersecting the LSW, and that industry accepted corrosion assessment models are suitable.
This paper provides an overview of additional full-scale destructive testing and detailed engineering analysis that further supports the observation that under most realistic conditions, the presence of a LSW does not negatively impact the remaining strength of corrosion feature. Potential exceptions to this behavior are related to the ductility of the weld, the constraint effects and morphology from the feature geometry, the operating stress of the pipe, and whether or not preferential attack of the LSW bondline is occurring.
The work presented in this paper is part of the Pipeline Research Council International (PRCI) project EC-02-13 “Response to Corrosion Interacting with the Longitudinal Seam in Liquid Pipelines”. The objectives of this project are to clarify which analysis methodologies are appropriate to assess corrosion coincident with a pipeline LSW and to support the development of recommended guidelines to effectively manage these types of features. This work is being executed in parallel with sibling projects EC-02-12 “Evaluation of Selective Seam Weld Corrosion Susceptibility”, NDE-4-13 “Selective Seam Weld Corrosion Detection with In-line Inspection Technologies”, IM-3-03 “Comprehensive Review and Assessment Guidelines for SSWC”, and IM-1-08 “Pragmatic Application of MegaRule RIN 1 – 192.712 Toughness Values”
Brian Leis1, Amin Eshraghi2
1Consultant, Worthington, USA. 2Acuren, Calgary, Canada
API’s release of the first edition of its Recommended Practice (RP) 1183 titled “Assessment and Management of Pipeline Dents” in November 2020, and Errata 1 a few months thereafter, marked the culmination of 14 plus years of related work. Against that backdrop, the PRCI, in collaboration with the PHMSA initiated Project MD-5-1, which sought to assess that activity, to identify technology gaps and aspects of that work that could enhance the RP, or broaden its capabilities. Concurrently, PRCI in collaboration with PHMSA initiated Project MD-5-2 seeking to enhance the tools being adopted in the RP. Aspects of these developments were evaluated rather critically at PPIM2023 in a paper that discussed what it termed “enhancement of indentation crack formation strain estimation” in PRCI’s reporting MD-5-2. Independently, about the same time a four-part series of papers was being planned with a similar but much broader intent and complexity, which is now in part in print in a refereed journal. This paper is the practical synthesis of that breadth and complexity, distilled with guidance and with takeaways concerning the issues and limitations of the current RP 1183.
This paper identifies many of the key assumptions latent in the Level 1 and Level 2 practices of API RP 1183, and truth-tests them by comparison with results generated using full-scale-validated Level 3 analyses. Where issues emerged with those assumptions, guidance and takeaways are presented to help mitigate their practical implications. Results for smooth single-peak symmetric and asymmetric dents formed in geometrically stiff versus compliant pipes over a range of depths from less than 1% OD up to 10% OD are considered. It is shown that the Level 1 and 2 practices can be effective for shallow large-radius single-peak dents, as might be formed by smooth rounded field boulders. However, the viability of those Level 1 and 2 practices diminishes as the dent depth and its curvature increase — with major issues emerging at depths as shallow as 1% OD when dealing with smooth flatter asymmetric dents. The RP’s concept of dent ‘restraint’ was truth tested and found problematic at dent depths typical of the shallower populations typically evident in many ILI surveys. The results discussed show that the Level 2 practices of API RP 1183 can underpredict the severity of smooth asymmetric dents by in excess of 100%. Finally, the RP’s provisions when dealing with skewed-dents have been truth-tested. For the cases considered it was evident that the peak strain was dictated by the shape of the contact, far more so than by the skew-angle. Because this outcome will be dependent on the shape and size of the dent formed, even low skew-angle dents likely should be evaluated at Level 3. Guidance and takeaways are provided to help manage skewed and other single-peak dents, whereas multipeak dents and those near possibly interacting features are deferred.
Jason Weiss1, Brett McNabb2, Alisdair Blackley1
1Argus, Edmonton, Canada. 2Apache Pipeline Products, Edmonton, Canada
The efficient and safe transportation of fluids through pipelines has been a cornerstone of modern infrastructure for decades. However, pipeline operators often face challenges when it comes to inspection, maintenance, and cleaning. These challenges are often addressed through pigging programs, however a large portion of existing pipelines are considered “unpiggable”. This is primarily due to pipeline size, complex geometry, or unique operational conditions. In recent years, the need to maintain and ensure the integrity of all types of pipelines, including those previously considered unpiggable, has grown significantly. The paper begins by defining what makes a pipeline “unpiggable” and delves into the common reasons for this classification. It will then explore the challenges associated with pigging previously unpiggable pipelines and some innovative solutions for pigging this type of infrastructure.
One of the primary challenges in pigging unpiggable pipelines is the development of suitable pigs and technologies. Traditional pigs are often designed for pipelines with standard dimensions and features. The paper discusses how the industry has responded to this challenge through the development of specialized pigs tailored to the unique requirements of unpiggable pipelines. This includes a summary on the development of various cleaning and product recovery solutions, such as foam pigs and swabbing devices, designed to address the unique challenges posed by unpiggable pipelines. Additionally, the paper includes information on the use of small, single body inspection tools that have been developed by industry to allow for in-line inspection in these applications.
Another large challenge surrounds the changes required to update and modify existing pipelines to include the necessary pig launching and receiving infrastructure and remove or update features that hamper successful pig runs. The paper highlights the challenges associated with collection of data on existing historical pipelines, along with some of the changes required to ensure successful pigging operations. Specifically, the paper outlines how the use of pipeline Pigging Valves and Multi-Pig Launchers can be used as an innovative alternative to traditional barrel-style pig launchers or receivers in previously unpiggable applications.
In addition to technological advancements, the paper delves into the operational, regulatory, and environmental considerations faced during pigging activities in unpiggable pipelines. These challenges include access to the pipeline, transportation and deployment of pigging equipment, high frequency pigging, emissions regulations, and safety considerations.
In conclusion, the pigging of previously unpiggable pipelines presents a compelling challenge that demands innovative solutions. This paper provides an overview of the challenges faced and the technological advancements, operational strategies, regulatory compliance, and economic factors that must be considered. By understanding these complexities, pipeline operators and industry professionals can make informed decisions and effectively address the unique requirements of pigging previously unpiggable pipelines, ensuring the continued safe and efficient transportation of vital fluids in our modern infrastructure.
Pablo Cazenave1, Sergio Limón1, Ravi Krishnamurthy1
1Blade Energy Partners, Houston, USA
An onshore/offshore pipeline in South America transporting brine solution experienced a failure initially attributed to external circumferential cracking in an onshore section of the pipeline. The failed pipeline rested above ground in a concrete ditch exposed to ambient conditions. Field assessments and land surveys of the failed site indicated possible nearby land movement.
This paper outlines the work conducted to review the Failure Analysis results, the aggregation of historic and recent in-line inspections (geometry + inertial + axial MFL), above-ground land movement survey data, and the identification of the cause of the circumferential cracking for the development of a short- and long-term remedial plan to address the effects on land movement on the integrity the pipeline.
Kathrin Schroeer1, Andrew Wilde2, Morry Bankehsaz3
1ROSEN Technology & Research Center, Lingen, Germany, 2ROSEN UK, Newcastle, UK, 3ROSEN USA, Houston, USA
Increases in pipe diameter, either in the form of localized bulges or expansions that affect the entire pipe circumference are reported infrequently by in-line inspections but they can indicate issues relating to the pipe manufacturing, construction or commissioning process that could compromise the future integrity of the pipeline. Typically diameter changes are small and below the detection and / or reporting threshold of high resolution caliper tools. However, as noted within PHMSA advisory notice ADB–09–01, pipe expansions can be indicative of material property deviations, including yield strengths that are significantly below specified minimum requirements, and can pose a credible threat to the integrity of a pipeline. Consequently, it is important that such anomalies are reliably detected and sized and that their severity is assessed appropriately.
This paper provides a summary of ROSEN’s experience of detecting pipe expansions and bulges including a review of typical anomaly characteristics and discussion on the capabilities of ILI tools to detect and size them. The potential causes of ID increases are reviewed and a phased integrity assessment approach is provided using a recent example of a pipe expansion identified in a pipeline in Canada. Finally, possible issues relating to the coincidence of pipeline expansions with other forms of pipeline damage including environmental cracking, corrosion and geometric anomalies are considered.
David Scharff1,Dr. Kaushik Parmar1, Adrian Banica1
1Direct-C, Edmonton, Canada
Underground vaults are employed along pipelines to accommodate pumping and shut-off systems that require a large volume of space around the pipeline. Within each vault a number of flanges, valves, and other potential leak points are present. Monitoring vaults for leaks presents numerous challenges: a) aerial surveys are not an option, b) they are often in remote locations, c) they are prone to flooding due to rain and snow run-off. This paper describes the development of an Industrial Internet of Things (IIoT) vault monitoring system that detects an unexpected release of liquid hydrocarbons within the vault and monitors the presence and level of water. A case study on the deployment and operation of this new multifunctional system in underground vaults at multiple northern locations is described. Ground movement monitoring is currently under development as an additional monitoring capability within the same IIoT system and some initial trial data will be presented.
Chris Alexander1, Tony Rizk2, Rodney Clayton2, Ahmed Hassanin1, Josh Wilson3
1ADV Integrity, Inc., MAGNOLIA, USA. 2Boardwalk Pipelines, Houston, USA. 3Allan Edwards, Tulsa, USA
ABSTRACT
Composite materials are commonly used in the reinforcement of hoop-oriented defects such as corrosion, dents, seam-weld anomalies, and gouges within pipelines. Additionally, they can be designed to reinforce features susceptible to cracking when subjected to bending and tension loading, including girth welds and wrinkle bends. Of particular interest, given historical failure patterns, is when wrinkle bends are subjected to high strain-low cycle fatigue loads.
This paper presents results and findings of a study that involved full-scale testing of wrinkle bends. The test program encompassed three distinct tests on 26-inch x 0.281-inch, Grade X52 pipes, all of which had wrinkles removed from service. The test program comprised testing an unreinforced wrinkle bend sample, as well as two additional samples that were reinforced with custom-designed E-glass-epoxy and carbon-epoxy composite technologies with axial-dominant fiber architectures.
In the case of the unreinforced wrinkle sample, the maximum recorded axial strains in the wrinkle feature were +/- 1%, in which the sample failed after 107 bending cycles. The two composite reinforced samples utilizing the E-glass-epoxy and carbon-epoxy technologies failed after 1,774 and 863 bending cycles, respectively. These results demonstrate that both systems were able to increase the life of the unreinforced wrinkle sample by as much as 16 times.
From an operational standpoint, these findings imply that the service life of existing wrinkle bends could be substantially prolonged, potentially by decades, assuming that such bends are subjected to loads of similar magnitude 5-10 times per year, as examined in this study. This research offers valuable insights into the transformative role of composite materials in enhancing the longevity and durability of wrinkle bends in pipelines.
David Futch¹
¹ADV Integrity, Inc., Magnolia, USA
ABSTRACT
Type B sleeves are a proven repair technique and are typically installed tight fitting with the ends fully welded. The sleeves are configured in a way to allow for load sharing from the carrier pipe to the sleeve and provides pressure containment when/if the underlying carrier pipe leaks. Once a leak occurs, the annulus space becomes pressurized which increases the stress on the side seams and fillet welds. Prior research has shown a resulting finite life of the sleeve as those welds can leak after some period based upon cyclic internal pressure loading and weld quality.
The use of filler material applied to the carrier pipe prior to applying the Type B sleeve is a common practice to increase load transfer, however, not required by any code and standard as the sleeve is pressure containing. While seemingly straightforward, the inconsistent application of filler material could result in unexpected results. This study examined and attempted to standardize the application of filler material, both locally applied and when the annulus space is pumped using a commercially available grout material.
The test program consisted of the repair of longitudinal seam weld features repaired by various sleeve configurations. These configurations included one installed without fill, with a locally applied fill, and a grouted annulus space. Each sample was repaired and cycled (until runout of 100,000 cycles). The grouted sample was the only to achieve runout reaching 100,000 cycles, 20x more cycles than any other sample. Metallurgical examination confirmed little, if any, growth occurred after repair, indicating the most advantageous load transfer and repair life.
Peter Martin1, Nathan Switzner1, Joel Anderson1, Joshua Stuckner2, Owen Lopez-Oneal3, Sophia Curiel3, Peter Veloo3
1RSI Pipeline Solutions, New Albany, USA. 2NASA, Cleveland, USA. 3Pacific Gas and Electric, Oakland, USA
ABSTRACT
Pipeline operators in the United States are increasingly relying upon materials verification programs (MVP) to establish the properties of pipelines lacking reliable records. The ongoing MVP at the Pacific Gas and Electric Company (PG&E) applies external nondestructive testing (NDT) to exposed line pipe to gain insight into the grade, vintage, and manufacturing method of the pipe. PG&E supplements the standard NDT methods for composition, strength, and geometry with the nondestructive collection of surface microstructures using metallographic replicas. The microstructures are quantitatively evaluated for ferrite grain size and fraction of pearlite. These are then used in conjunction with other measured characteristics to support determination of grade and vintage, and to identify populations of similar pipes. Automating these analyses is of interest because the manual evaluations are labor intensive and subject to variability associated with evaluator skill, judgement, and fatigue.
Traditional methods for automating microstructure analyses are often challenged by small variations in sample or image quality. Machine learning (ML) models have been shown to be more robust, but training these models typically requires hundreds of manually pre-processed images. This creates a high initial investment that impedes practical implementation in an operational environment. Recently, pre-training ML models on a large number of generic images has been shown to substantially reduce the required number of application-specific training images.
This work will describe the performance of an open-source ML model pre-trained on a database of over 105 microscopy images and subsequently trained on fewer than 20 line pipe microstructures. The training and validation of the model will be presented, along with a comparison of ML and manual evaluations of more than 150 microstructures from more than 50 line pipes. The results will show the performance of the ML model to be comparable to that of manual evaluations.
Joel Anderson
RSI Pipeline Solutions, Oklahoma CIty, USA
ABSTRACT
The regulations published by PHMSA in October of 2019 require non-destructive examination (NDE) to determine the material properties of pipelines that lack traceable, verifiable, and complete (TVC) records. To meet this requirement, operators must conduct verification of pipeline material properties in accordance with 49 CFR 192.607. Inherent in these requirements are requirements to achieve a 95% confidence level and the use of “statistically valid basis”. But absent in the regulations is how to determine if this has been met. Consequently, this leads to uncertainty on the part of the operators if they’ve done enough and are the observed differences indicate that the samples truly are different.
Differences will always exist between the measured value and the true value since perfect measurements are impossible. Errors of varying magnitude will always exist due to random effects from any number of sources. The inevitable question arises is whether these observed differences are enough to be significant and have enough samples been completed to be able to tell the difference.
This paper will discuss how to set up a sampling plan to meet the necessary goals. Including how to determine if a sample is inconsistent with some value, determining sample size and comparing two samples.
Kelly Thompson¹
¹Williams, Tulsa, USA
Hard spots are a pipeline defect created during original manufacturing. These are typically considered stable unless acted upon by coincident environmental factors including coating degradation, atomic hydrogen, and stress. As a result of industry lessons learned and recent hard spot related failures on its system, Williams is executing a hard spot mitigation program that encompasses improvements to our risk assessment model to account for hard spot defects. In this presentation, we will share how we are incorporating this risk into our modeling approach and how those results influence the mitigation effort. Additionally, this presentation will discuss the benefits that can be realized through broader industry collaboration, current collaborative studies underway, and key metrics to advance industry understanding of the hard spot risk that ultimately will improve overall pipeline safety.
Scott Olson¹, Andy Studman², Jim Evans³, Aidan O’Donoghue⁴
¹Shell Trading & Supply Operations, Trinidad & Tobago, ²Shell International Ltd, Aberdeen, UK, ³Pigtek Limited, Temple Normanton, UK, ⁴Pipeline Research Limited, Glasgow, UK
Abstract
A routine sphering operation to control liquid hold up on a 30-inch trunk pipeline transporting wet gas was interrupted when a sphere became damaged and stalled in the pipeline following interaction with a subsea isolation valve inadvertently stuck in the partially closed position. Rectifying the valve to the fully open position followed by rescue pigging was selected as the remediation strategy. The offshore platform topsides facilities however were only designed to launch spheres, through the side branch of an unbarred tee and included a 30-inch to 36-inch reducer and 1.5D bend. The rescue pig required careful selection and onshore pigging trials were undertaken resulting in extensive modifications to the rescue pig design and set up to demonstrate the rescue pig could successfully traverse all the features in the topsides pipework. Following a successful subsea campaign to fully open the subsea valve, the rescue pig was deployed and successfully recovered the damaged sphere from the pipeline. This paper and associated presentation describes the details of the various challenges and solutions that enabled a safe and successful rescue pigging operation.
Chris Alexander1, Aquiles Perez2, Casey Whalen3
1ADV Integrity, Magnolia, USA. 2ECA Solutions, Houston, USA. 3CSNRI, Houston, USA
Over the past 30 years composite repair technologies have changed the landscape of pipeline rehabilitation and are used to reinforce a wide range of defects including corrosion, cracks, dents, and vintage girth welds. Composite crack arrestors have also played a role in this time period, although their use in this capacity has not been as widespread as their role in structurally reinforcing pipelines as part of integrity management programs. Interestingly, the Clock Spring technology was originally developed as a crack arrestor; however, the pipeline industry was able to conceive alternative uses for composite reinforcing technologies that spawned one of the fasting growing technology applications in the pipeline industry.
Composite crack arrestors have been proven to effectively arrest brittle and ductile running fractures, primarily focused on high pressure gas transmission pipeline systems. This has been validated via full-scale testing on high-energy pipe. For the most part there has been little design guidance provided to the pipeline industry for how a composite crack arrestor should be designed. The approach employed by most researchers has been to design and install a robust arrestor and then conduct testing to experimentally validate its ability to arrest running fractures. The composite crack arrestor design is considered a “success” if it stops the running fracture. Although the science behind modeling fracture is well understood, gaps exist in terms of how to arrest running fractures using composite materials using a well-thought-out design process. Methodologies have established a “qualified” approach rather than a “quantified” approach for design. This paper presents a framework for using composite materials as crack arrestors to arrest running fractures in CO2 pipelines that will be useful for pipeline companies seeking to build new pipeline systems or convert existing assets to CO2 service.
Daryl Bandstra1, Alex Fraser1, Miaad Safari2, Kai Ji2
1Integral Engineering, Edmonton, Canada. 2Enbridge Gas, Toronto, Canada
The transmission pipeline industry is increasingly utilizing probabilistic models for assessing the probability of failure of anomalies measured during in-line inspections such as corrosion and cracks. PHMSA (Pipeline and Hazardous Materials Safety Administration) has recently classified probabilistic models as best practice, suitable for supporting all types of decision-making, as these models effectively represent the uncertainty in input data using probabilistic distributions. When modeling corrosion using a probabilistic model, the in-line inspection data includes measurements of individual corrosion anomalies. When these anomalies are in close proximity, there is potential for interactions that reduce the overall burst capacity, and the effect of these interactions can be considered by modelling these individual defects as a cluster.
Some probabilistic analyses idealize the clusters as single, large anomalies while others address the added complexity of considering all possible combinations of the individual anomalies that comprise the cluster. This presentation will investigate the differences in the estimated probability of failure of these two approaches by evaluating a range of test cases and real-world clusters. These cases will illustrate scenarios where significant discrepancies exist and areas where both approaches yield comparable results. Additionally, we compare the effects of different approaches for modeling the correlation of measurement errors associated with anomalies within a cluster.
Carlos Madera1, Sean Knight2, Austin Guerrero2, Simon Slater3
1Dow Chemical, Houston, USA. 2ROSEN Group, Houston, USA. 3ROSEN Group, Columbus, USA
With the passage of §192.607 and PHMSA’s subsequent responses in FAQ’s 21 and 22, ILI is an approved method for measuring properties and delineating pipe into populations with similar characteristics. In cases where material properties remain unknown, ILI populations can be leveraged to optimize decision making and test locations to close out material property verification. To enable this, the process must achieve the required confidence without necessarily having to test one sample per mile, which is defined as the default in regulation. §192.607(e)(5) states that an alternative statistical sampling approach can be used if it can “achieve at least a 95% confidence level that material properties used in the operation and maintenance of the pipeline are valid.” This paper will provide details on two alternative sampling approaches that have been approved for use by PHMSA on Dow Chemical’s 8” Mossville to Kaplan line segment. The approaches are based on a combination of ILI and test data using statistical analysis to satisfy the 95% confidence level. The efficacy of these approaches will be demonstrated using the assessment program performed by Dow Chemical to define the status of existing material properties and produce a plan to close out unverified material property values and fulfill the requirements of §192.607. The discussion will provide specifics of the approaches used by Dow Chemical, including the scope of documentation required to support its implementation and acceptance by the regulator.
Bernardo Cuervo
EN Engineering, Houston, USA
As in-line inspection (ILI) yields the highest-per-mile discovery of anomalies, running cleaning pigs and ILI tools are an important part of most integrity management programs. However, not without their risks. On June 28, 2021, a natural gas explosion occurred after workers inserted a gauge plate in a launcher trap as part of a routine pigging activity. The explosion went through the open launcher enclosure, ejecting the pig from the barrel, injuring two workers and killing two more. On November 15, 2021, PHMSA published the Final Rule: Safety of Gas Gathering Pipelines (86 FR 63266). With this rule, more than 400,000 additional miles of gas gathering pipelines are now covered by Federal reporting requirements. Proactive operators are beginning to ascertain the ILI feasibility of thousands of miles of gathering pipelines for future ILI. Many of these pipeline operators are beginning to audit and review their pigging procedures to prevent catastrophic incidents. This paper describes the entire process from the perspective of a pipeline operator; including the experiences of maintenance personnel, and the challenges faced by field operations during the implementation and use of a new methodology.
Atul Ganpatye1, Chris Alexander1, Rodney Clayton2, Tony Rizk2
1ADV Integrity, Inc., Magnolia, USA. 2Boardwalk Pipelines, LP, Houston, USA
Traditional code-based approaches for assessing crack-like flaws in pipelines rely on several idealizations/assumptions regarding flaw shape and orientation, material properties, and applicability of the analytical framework used to estimate pipe performance. The uncertainties in these assumptions often result in an underestimation of pipe performance in terms of failure pressure prediction. Full-scale tests with pipe containing crack-like flaws have shown that the actual failure/burst pressures can be as high as 50% over the predicted failure pressure. This paper outlines an experimental approach to quantify the “effective” fracture resistance for crack-like flaws as it correlates to the results from full-scale testing. Using effective fracture resistance for failure pressure prediction is discussed as an alternative approach to providing better alignment with observed failure pressure data.
The study included full-scale burst testing of 12 samples of 26-inch OD x 0.281-inch wall, Grade X52 pipe, and four samples of 30-inch OD x 0.299-inch wall, Grade X60 pipe, containing crack-like features. Cracks were generated in the base pipe having depths ranging from 20.9% to 69.0% of the pipe’s nominal wall thickness. On average, experimental results showed that the actual failure pressures were between 20% and 40% higher than those predicted using analytical assessment methods. Analytical assessment was performed using three different fracture models: Modified Ln-Sec, MAT-8, and API 579. The paper discusses the interpretation of the discrepancy between the predicted and observed results in terms of effective fracture resistance of the pipe. This resistance is explored as a manifestation of lower crack tip constraint in a full-scale pipe-geometry sample, compared to traditional measures of fracture toughness using sub-scale specimens. Results are also discussed from a practical perspective of the potential reduction in the number of digs based on reinterpretation of failure pressure ratios using the effective fracture resistance.
The study results have the potential to provide a more robust predictive capability for estimating burst pressures of pipes containing crack-like flaws. Using the reinterpreted effective fracture resistance based on actual test data allows a systemic incorporation of almost every single detail in the pipe performance “system” – in this context, the “system” is the collection of all parameters/factors that directly or indirectly influence the pipe performance, such as: pipe properties, flaw morphology, stress intensity due to the presence of the feature, etc. Improved confidence in the predicted pipe performance using full-scale test data has the potential to meaningfully impact integrity management approaches by reducing the number of digs that may be flagged when using the traditional approach.
Pablo Cazenave, Ming Gao, Katina Jimenez, Ravi Krishnamurthy
Blade Energy Partners, Houston, USA
The possibility of hydrogen-induced cracking and hydrogen-assisted cracking as interactive threats is increasingly becoming a safety concern to pipelines. While few cases exist of fully documented onshore transmission pipeline failures due to CP-related hydrogen-assisted cracking, the possibility of hydrogen-assisted failures needs further investigation, particularly hydrogen interacting with stress corrosion cracking in corrosion potentials more negative than -850 mV CSE.
This paper presents a case study of a 22-inch onshore natural gas transmission pipeline that experienced in-service leaks and a rupture associated with axially and circumferentially oriented crack colonies initially thought to be traditional stress corrosion cracking. In-depth metallographic examination revealed cracking fracture paths consistent with hydrogen-assisted cracking. Further investigation of potential sources of hydrogen concluded that the source is the impressed-current cathodic protection system operated for decades at near the P/S potentials of −1200 mV CSE.
An approach to mitigating the threat of hydrogen-induced cracking in onshore pipelines is also outlined.
Frank Micheli1, Ken Maxfield2, Phil Tisovec2
1Bridger Pipeline, Casper, USA. 2KMAX Inspection, Millcreek, USA
Bridger Pipeline operates a crude oil gathering system, of approximately 3500 miles, in the Williston Basin of western North Dakota, eastern Montana and the Powder River Basin of Wyoming in the USA. The Bridger system contains many small diameter (3” to 6”) gathering lines that are a challenge to inspect with ILI tools. These challenges include low flow conditions, line cleanliness and paraffin build up. Many are first time inspections of pipelines with limited or unknown records, trap configurations, and fittings such as heavy wall tees and elbows. Also of concern are weather constraints with the seasonality of ILI inspection projects for pipeline repair and access. This paper presents how these challenges are addressed to successfully run ILI to comply with Bridger’s integrity management program.
Ali Ebrahimi1, Arash Mosaiebian2, Amir Ahmadipur1
1Geosyntec Consultants, Inc., Houston, USA. 2Enbridge, Inc., Calgary, Canada
Pipelines are linear structures that cross various slope geometries and geologies and are susceptible to geohazards such as landslides. The ground movements from the landslides can potentially induce axial, bending, and torsional stresses in pipelines. Inertial Measurement Unit (IMU) bending strain data are commonly used for assessing the pipeline integrity in the area impacted by a landslide.
Ground movement by landslides oblique to the orientation of the pipeline can cause lateral deflection as well as localized axial elongations/contractions in the pipeline, which will result in accumulation of bending and axial strains on the pipeline. Common factors impacting the magnitude of strain accumulation are pipeline deflection (or out-of-straightness), deflected pipeline length (engaged part of the pipeline within the body of the landslide), pipeline diameter, and orientation of the pipeline relative to the direction of landslide movement.
This paper will review and present the above information for more than 70 landslide sites within the Appalachian region of the USA. This paper will also present a correlation between the measured bending strain from the IMU tool runs and the pertinent pipeline features such as pipeline out-of-straightness, deflected length, pipeline diameter, and pipeline orientation relative to the landslide direction.
This paper is intended to assist pipeline geohazard practitioners in performing the first round of induced bending strain screening under conditions where IMU bending strain data may not be available.
Michiel Brongers
Kiefner and Associates, Inc., Columbus, USA
Operators with existing pipelines with laminations may have the desire to perform welding to install fittings or other appurtenances. This paper presents the results of an evaluation of the potential threat of lamellar tearing under in-service fillet welds. The research included modeling to determine the minimum recommended distance for welding at or near laminations, and a full-scale hydrostatic pressure-hold test on laminated pipe with welded fittings to demonstrate if the presence of laminations would interfere with the welds. Four different scenarios were investigated: (1) fitting welded over laminated area, (2) portion of weld bead place on top of a localized lamination, (3) weld bead some distance from localized lamination, and (4) fitting welded on non-laminated area of pipe with laminations elsewhere. The developed approach was a unique and innovative way to evaluate welding on pipe with laminations. The results from this project and the provided guidance that was developed will benefit the pipeline industry as a whole.
Intisar Rizwan i Haque, Ryan Lacy, Simon Bellemare
Massachusetts Materials Technologies, Natick, USA
Growing use of advanced In-line Inspection (ILI) for detecting seam anomalies has increased the demand for Engineering Critical Assessment (ECA) to differentiate the many non-severe features that do not need repair from features in certain assets where repairs are warranted. To perform the ECAs and reduce the number of unnecessary excavations of vintage lines, pipe cutting for laboratory testing has become more common to obtain Charpy V Notch (CVN) toughness, which is often unavailable when legacy manufacturing standards did not require such testing. Non-destructive evaluation (NDE) of pipe seam toughness as a part of opportunistic data collection is an attractive alternative to pipe cutouts and can be applied to prior excavations with sufficient NDE data. An NDE process using the frictional sliding method and other surface measurements has been recently validated for assessing the seam toughness of vintage electric resistance welded (ERW) pipes. This paper details this NDE process and its validation, along with results from case studies of its initial field deployment. The field instrumentation is the same as used for pipe grade determination using the frictional sliding method. When certain conditions are met for a given ERW pipe population, a ductile fracture initiation and an associated CVN toughness of 10 ft-lbs can be positively confirmed when conservatively accounting for measurement uncertainty. Utilizing a toughness of 10 ft-lbs is a significant advantage over conservative values such as 4 ft-lbs for gas transmission pipelines with no history of failure. Field deployment of this process has successfully reduced the total number of excavations on projects. The NDE process capabilities can be further enhanced when combined with an NDE determination of pipe body toughness, using a separate, but complementary, technique.
Matt Ellinger, William Harper, Pam Moreno, Stacy Hickey, Adriana Nenciu, Preston Galloway
DNV, Dublin, USA
Results from magnetic flux leakage (MFL) in-line inspection (ILI) surveys provide valuable information that help pipeline operators make informed and defensible integrity management decisions. When subsequent ILI survey data are available, meaningful, and data-driven corrosion growth rates can be derived along the length of a pipeline by performing a comprehensive ILI-run-to-run comparison. A comprehensive ILI run-to-run comparison should include the following components:
ILI vendors typically identify metal loss anomalies that are on (i.e., crossing) the longitudinal seam weld or near (i.e., adjacent to, or in the heat affected zone) of the longitudinal seam weld versus those that are in the pipe body (i.e., away from the longitudinal seam weld). During a comprehensive ILI run-to-run comparison analysis, the authors of this paper observed a trend in which ‘spreadsheet-based’ corrosion growth rates for metal loss anomalies reported on or near the longitudinal seam weld were consistently higher than those reported in the pipe body. Following this observation, the authors performed an in-depth analysis to better understand this trend. The following tasks were completed as a part of the analysis:
This paper will detail the methodology and results of the authors’ analysis. Key findings and practical applications will be presented. The paper will provide valuable insights into managing pipeline integrity with respect to ILI-reported metal loss anomalies at or near the longitudinal seam weld.
Tom Bubenik, Steven Polasik, Benjamin Hanna
DNV, Dublin, USA
Effective area calculations are used to identify which corrosion depth measurements control the failure pressure of a cluster of metal-loss anomalies reported by an in-line inspection (ILI). The depth measurements usually correspond to individual anomalies that are grouped together based on defect interaction criteria. The effective area calculations determine an effective length and depth based on the ILI reported cluster and box lengths and depths at the time of the inspection. As corrosion growth occurs, though, the depths of some or all of the individual anomalies within a cluster can increase. As a result, the effective length of the cluster can increase or decrease.
Growth of individual anomalies within a cluster is often non-uniform, with some anomalies increasing in depth (and possibly length) more quickly than others. As a result, local “hot spots” can develop and eventually dominate the effective area calculations. Understanding how corrosion growth affects the effective dimensions of a cluster is important in estimating remaining lives and determining which clusters are most likely to fail first. The flaw geometry at failure depends on the local operating pressure, the corrosion growth rates, and the initial cluster geometry.
Remaining life calculations depend on reliable estimates of both initial and final metal loss depths and lengths. Because differences between individual metal loss box corrosion growth rates can affect effective flaw dimensions, accuracy is important. Initial corrosion depths and lengths are reasonably well known from typical ILIs. Overestimating or underestimating the flaw geometry at failure under operating conditions can lead to overly conservative or unconservative remaining life predictions.
This paper evaluates the effects of corrosion growth on the effective dimensions, flaw geometries at failure, and remaining lives of clusters. The authors examine 20 real-world clusters ranging in length from short to long and containing few to many individual anomalies. The authors determine when and how each cluster’s effective length and critical depth changes as corrosion growth takes place along the cluster until it reaches a failure condition at the local operating pressure. Then, they evaluate how the changes in effective lengths and critical depths affect remaining life predictions. Conclusions regarding how to best estimate remaining lives of clustered anomalies are developed and documented.
KEYWORDS: Engineering analysis, ILI analysis, ILI applications, Corrosion studies
Greg Zinter1, James Staszuk1, Cory Solyom2, Brianna Bossio3
1PureHM, Edmonton, Canada. 2PureHM, Calgary, Canada. 3Enbridge Inc., Edmonton, Canada
Inline inspections tools and cleaning pigs are routinely used to ensure the safe and economical operation of oil and gas pipelines. While in the pipeline, all ILI tools and pigs must be tracked on a real time basis so that the pipeline can be operated safely. Recent developments in remote ILI tool tracking technology have improved the safety of ILI projects by eliminating the need for field technicians to travel to site to witness the tool passage. These improvements have also made tool tracking more reliable and, most often, lower cost.
Remote tracking offers operators a way to track their inline inspection tools without the need to constantly have field personnel actively on the ROW, effectively reducing risks to personnel and the project. This is of particular increased benefit when tracking overnight and over difficult to access terrain. Traditionally, the solution for difficult access has required the aid of helicopters for AGM deployments, and retrievals, meaning significant effort is required to facilitate tracking for every single project. As pipeline owners look to enhance their inspection programs through increased inspection frequency, these issues of accessibility are exacerbated. Advancements in tracking technology and services are addressing this issue and making it easier and cheaper to track their critical ILI tools.
For example, Enbridge has installed a permanent remote tracking system across large inaccessible sections of its Athabasca pipeline network. This system consists of a series of AGMs, strategically located to ensure full tracking coverage. These remote systems are permanently installed and powered by solar energy. Pure HM has partnered with the Enbridge to monitor this system 24/7, year-round to ensure consistent and reliable tracking of any tool used in the line, eliminating the need to mobilize field technicians or helicopters.
This paper will explore the innovative approach Enbridge has taken to mitigate risk and drive a cost saving of over $4,000,000 over the duration of the 5-year program.
Xiang Peng1, Kevin Siggers1, Johannes Palmer2, Gurwinder Nagra3
1ROSEN Technology Canada Ltd., Kelowna, Canada. 2ROSEN Technology and Research Center GmbH, Lingen, Germany. 3Enbridge Liquids Pipeline, Calgary, Canada
The inspection capability of magnetic flux leakage (MFL) is subject to the angle between its magnetic field and the defect. To get a comprehensive assessment on corrosion defects, more and more pipelines are inspected with two MFL techniques with perpendicular magnetic fields, i.e., axial MFL (MFL-A) and circumferential MFL (MFL-C). Currently, inspection data from each MFL tool are analyzed separately, and two inspection reports are generated respectively. In this paper, we propose a model which aligns the data from two magnetic field orientations and fuses the respective signals into a single inspection result to achieve a 3D metal loss profile with laser-like precision. The alignment of the signals is achieved through conversion into the same modality i.e., MFL-A converted to MFL-C and vice versa. The fusion model is a neural network trained on historical MFL and laser scan data. It takes the aligned MFL-A and MFL-C signal data as the input and produces 3D metal loss profiles with high resolution. In this case study with Enbridge Liquid Pipelines, the proposed model is validated on the field data from an operational pipeline. The depth comparison of the derived 3D metal loss profiles versus laser scan profiles has very promising results. The 3D metal loss profiles are also used as inputs to RSTRENG as well as P² methodologies. The detail of the fusion derived profiles, compared to the box derived profiles, leads to a more accurate estimation of pipeline burst pressure.
Shanshan Wu1, Joseph Bratton1, Jing Wang2, David Kemp1, Luyao Xu1, Greg Quickel1
1DNV, Dublin, USA. 2TC Energy, Calgary, Canada
The Pipeline and Hazardous Materials Safety Administration (PHMSA) issued RIN2 of the Final Rule (frequently referred to as the “Mega Rule”) on August 4, 2022, which will impact the pipeline industry’s approach to the assessment of dents and other mechanical damage. The Mega Rule provides detailed requirements in the Code of Federal Regulations (CFR) Title 49 Part §192.712(c) regarding how to perform a dent engineering critical assessment (ECA). With the Mega Rule taking effect in 2024, it is expected that more dents will be considered for ECA to determine the response plan and timeline.
This paper will share guidance on selection criteria for dent ECA through five case studies. The case studies include Ductile Failure Damage Indicator (DFDI), Strain Limit Damage (SLD), and dent fatigue analysis using finite element analysis (FEA). Additionally, findings from field investigations, laboratory results, and other pertinent information associated with the respective dents will be presented. Guidance regarding best practices to assist operators in selecting suitable locations for dent ECA versus excavation will be provided from the case studies.
The primary objective of this paper is to share experiences to the industry ahead of the upcoming dent ECA requirements outlined in Part §192.712 (c). This paper will share lessons learned for things to consider when evaluating the suitability of performing an ECA and to help avoid sole reliance on ECA results when other factors demonstrate that the results may not be reliable.
Mark Wright, Amin Singh, Tanner Jones
ROSEN USA, Houston, USA
Achieving zero incidents has been a key safety objective across the pipeline industry. The relationship between the pipeline industry and pipeline regulations has seen several iterations since the first regulations were introduced in 1968. Significant changes and rigorous regulations enacted in 2002 required pipeline operators to create a structured framework for risk and integrity management programs. However, subsequent safety performance has been static, as detailed in the preamble to more recent updates in 2019. Pipeline regulations serve as minimum requirements for achieving operational safety by reducing incidents, and there should be hope of a more substantial impact with the effects of rule changes to both gas and hazardous liquid pipeline regulations in 2019.
Failures of pipelines are often complex, involving primary, secondary and even tertiary contributory factors, while rulemaking must be discrete and realistically achievable for compliance. Thus, failures and rulemaking are not completely associative, but neither are they mutually exclusive. The preamble to the 2019 rules identified clear lineages between a subset of significant events and rulemaking i.e. measures that directly address some of the causes of significant events. Whilst this seems intuitively sensible, where do these solutions lie in the spectrum between causality and mutual exclusivity on a wider scale?
All pipeline failures are undesirable, but each provides an opportunity to learn and highlights systemic vulnerabilities by identifying areas for improvement. This paper explores reported failure data for both gas and liquid transmission pipelines in the U.S. between 2003 and 2022. The paper will identify trends and thus residual gaps in understanding of failures within the industry for proactive measures to prevent future incidents. The complexity of failure will be explored by review of supplementary NTSB investigation reports and commentary on the combination of factors at play. The primary goal of integrity management is to operate assets such as pipelines safely. Inherent is that integrity management cannot be about doing everything possible, rather maximizing everything practicable. This paper hopes to identify what practicable may look like now and in the future.
David Kemp1, Shanshan Wu1, Joseph Bratton1, Luyao Xu2
1DNV, Dublin, USA. 2DNV, Calgary, Canada
With PHMSA’s issuance of RIN2 of the Final Rule, Engineering Critical Assessments (ECA) have become increasingly important in assessing not only the fatigue life of dents and other integrity threats, but also reinspection intervals. ECA’s can be performed for a variety of complex dent features identified from in-line inspection (ILI) or direct examination by following assessment methodologies prescribed in API 1183 along with the fatigue life assessment procedures outlined in API 579.
For those cases requiring a level 3 assessment, finite element analysis (FEA) is often necessary to account for interactions between dents and additional features (i.e., metal loss, bending strain, seam welds, etc.), which can then be used to determine the fatigue life of the dent. A more accurate fatigue life can be calculated using the FEA results to obtain a stress vs. pressure relationship, which is then paired with the pressure history of the specific line segment being assessed. This stress vs. pressure relationship is extracted from a specific location in the vicinity of the dent from the finite element model, and for the sake of conservatism in the assessment, is either taken from the location of maximum stress or the location of maximum change in stress between pressure cycles. Both stress locations are critical to dent integrity, the former is usually associated with crack generation during the dent formation process, while the latter contributes to the fatigue crack initiation and growth. Depending on the dent conditions (i.e., constrained, unconstrained, dent depth, shape, feature interactions, etc.) these two locations are not always coincident and the resulting fatigue stress range could be significantly different in some scenarios.
For this paper, a collection of over 30 dent ECAs are examined to determine under what conditions, such as constraint condition, shape, stress/strain level, etc., the locations of maximum stress and maximum change in stress are not coincident as well as the extent to which these differences impact the overall fatigue life of the dent features.
Gemma Simpson1, Nancy Thomson1, Courtney West1, Jane Haswell2, Andrew Cosham3, Gary Senior2
1SGN, Edinburgh, UK. 2PIE, Newcastle, UK. 3ninthplanet, Newcastle, UK
The Local Transmission System (LTS) is the backbone of the UK (UK) energy network, delivering natural gas from the National Transmission System (NTS) to towns and cities across the country.
The four Gas Distribution Networks (GDNs) operate approximately 11,000 km of high-pressure pipelines, operating at pressures above 7barg. The pipelines were originally designed to transport and store natural gas.
The UK Hydrogen Strategy states that: “Low carbon hydrogen will be critical for meeting the UK’s legally binding commitment to achieve net zero by 2050”. Hydrogen behaves differently to natural gas, therefore it is necessary to assess how it affects the existing LTS infrastructure.
The LTS Futures Project is a first-of-a-kind, £30 million, joint funded project between SGN, the UK energy market regulator OFGEM, and the other UK GDNs. The project is led by SGN and looks to repurpose a 30 km natural gas transmission pipeline to hydrogen for a live demonstration trial, which will inform the development of a Blueprint methodology for repurposing the LTS. The LTS Futures Project is researching, testing and collating evidence to understand the compatibility of LTS assets, pipelines, associated plant and ancillary fittings in hydrogen which will be captured in the Blueprint.
The aim of the Blueprint is to provide a methodology to determine if a natural gas LTS asset is fit for hydrogen service and identify any data gaps, or further work needed for repurposing for hydrogen service.
This paper provides details on the technical approach adopted by the project, the progress to date and the plan going forward.
Keywords: Repurposing. Hydrogen.
Tristan MacLeod
Kiefner and Associates, Inc., Ames, USA
Cyclic fatigue of crack-like anomalies is a well-known threat to pipeline integrity. Manufacturing defects in the longitudinal seam (especially in pipe manufactured prior to 1970) as well as stress corrosion cracks in the pipe body may enlarge and fail in service due to pressure-cycle-induced fatigue. In fact, the current U.S. pipeline integrity management regulations require crack growth and remaining life assessments for natural gas pipelines in high consequence areas and segments known to be susceptible to cyclic fatigue.
To manage the risk of failure from pressure-cycle-induced fatigue, pipeline operators should employ integrity assessments either via hydrostatic testing or in-line inspection using a reliable crack-detection tool. The appropriate period for reassessment depends on the sizes and growth rates of potential defects that may still exist after an initial hydrostatic test or in-line inspection. The pressure-cycles applied to the pipeline may cause the just-surviving defects to grow at a rate inherent to the material and its environment. Long-established principles can be used to predict remaining life. Pipeline operators can use these methods to plan timely reassessments to prevent failures.
This paper describes one approach to predicting reassessment intervals. This approach has evolved over a period of more than 30 years. Careful analysis of all of the known data can avoid pitfalls and inappropriate remaining life predictions. The purpose of the paper is to show that while the well-known and widely available basic principles are sound, their application to pipeline integrity management requires an in-depth understanding of the particular pipeline being assessed.
Lucinda Smart, Benjamin Wright, Dyke Hicks
Kiefner and Associates, Inc, Ames, USA
Within the last few years, there have been increasingly more vendors and operators looking into ways to improve the accuracy of ILI data correlations with both in-ditch validation methods as well as across consecutive ILI runs. It may seem obvious, but it is important to ensure the defects that are being correlated from one data source to the other are, in fact, the same defect. ILI data correlations can be particularly difficult when differing vendors or tool technologies are applied, or if location conventions are not applied similarly from one run to the next. If there are inaccuracies in the locations and orientations provided by the vendor, or if the dig site location is not verified and reference locations are not correct, this leads to meaningless data results. This paper will go into detail in the discussion for guidance of ILI data correlation from both successive ILI assessments for growth rate assessments, as well as in-ditch NDE data to ILI data for tool validation practices. The primary method discussed will be a pattern-matching approach, where sources of error can be reduced by aligning overall patterns of reported defects using modern software tools along with insight from experienced analysts. Applying expertise in this manner leads to more accurate outcomes for tool validation, corrosion growth rate (CGR) assessments, and probability of identification or detection (POI or POD), which then ultimately lead to better and more informed integrity management decisions.
Christopher De Leon1, Rachel Brossman2
1D2 Integrity LLC, Houston, USA. 2PBF Energy, Cerritos, USA
In-line inspection (ILI) continues to evolve and prove to be a high-value solution for performing pipeline integrity assessments. Industry has seen ILI promoted through NTSB recommendations, Federal Pipelines Safety Statutes by Congress, and PHMSA’s recent updated pipeline federal regulation. However, each ILI technology and its application by ILI service providers must be vetted by pipeline operators to ensure it is qualified for the inspection goals and objectives. Unfortunately, some ILI technology is not properly vetted commensurate to the risk associated with the integrity assessment for a given pipeline. As governance, PHMSA has now incorporated by reference API STD 1163 In-line Inspection Systems Qualification (API 1163) into both 49 CFR 192 and 195. While API 1163 is generally understood, details can be overlooked, leading to non-compliance. This paper uses two case studies to highlight the topic of ILI System Selection within the API 1163 standard and its importance in performing a sound integrity assessment. The process used for selecting an appropriate ILI system for corrosion and cracking threats will be reviewed, and how compliance with new regulations was specifically considered.
Topics: Regulation and Compliance, Codes and Standards, ILI Applications, ILI Analysis
Christopher Davies1, Cameron Cooper1, Lee Sellers2
1ROSEN USA, Houston, USA. 2ENERGY TRANSFER, Houston, USA
In response to the discovery of Selective Seam Weld Corrosion (SSWC) on a 12-inch natural gas pipeline, an in-line inspection (ILI) was completed using an ultra-resolution circumferential magnetic flux leakage tool. The closer sensor configuration of this system allowed for a more detailed recording of the magnetic leakage profile and ensures that the peak value of flux leakage is recorded within complicated corrosion morphologies such as SSWC.
Through an optimized evaluation process, all corrosion anomalies considered to be associated with the longitudinal weld were subject to detailed review. The review provides a thorough understanding of the different signal characteristics and likelihood classifications of ‘likely’, ‘possible’ and ‘unlikely’ SSWC are assigned. The initial evaluation process resulted in the identification of 23 ‘Likely’ SSWC anomalies and 35 ‘Possible’ SSWC anomalies. All remaining corrosion anomalies associated with the longitudinal weld were classified as ‘Unlikely’ SSWC. Classification is critical as it pertains to integrity management. Understanding the pipeline’s susceptibility to SSWC, the detection capability of the ILI system and the confidence of likelihood classifications allows for process driven discrimination between SSWC and ‘general corrosion’ in the area of the longitudinal weld.
Validation of the evaluation and classification was achieved through a structured dig program. A total of 3 excavations were performed on the pipeline, which targeted a total of 24 anomalies associated with the longitudinal weld. Evidence of SSWC was observed for 11 of the 13 ‘Likely’ SSWC classifications. Of the five (5) ‘Possible’ SSWC calls investigated, three (3) were confirmed to be SSWC. No evidence of SSWC was observed for the ‘Unlikely’ SSWC classification subject to infield investigation. The results of these excavations were used to reclassify all remaining anomalies associated with the longitudinal weld.
A critical aspect of the likelihood classification process is iteratively incorporating information from field investigations. This paper presents the close collaborative efforts performed by a pipeline company and an ILI service provider, to help manage the threat of SSWC on a 12-inch pipeline. It is intended to present an ILI based approach to assess SSWC and share recent experience with the industry on a targeted approach in managing the threat of SSWC.
Santiago Urrea1, Jordi Aymerich2, Sayan Pipatpan1, Tannia Haro3, Alex Hensley3, Christopher Newton4
1NDT Global, Stutensee, Germany. 2NDT Global, Barcelona, Spain. 3NDT Global, Houston, USA. 4Phillips 66, Houston, USA
Pipeline operators employ various strategies to ensure the operational safety of their pipeline systems. A crucial element of this strategy involves In-line inspection (ILI) and Non-destructive examination (NDE). However, what happens when all available evidence points to a systematic limitation in the performance specification of these systems? How can the operator utilize this data within their Integrity Management Program (IMP)? Lastly, can this data be effectively utilized to derive new rules and analysis processes?
NDT Global, in collaboration with an operator, has been tasked with investigating, documenting, and delivering a novel approach to identifying crack complexity, specifically hook cracks, within a population of previously detected and undersized features. Currently, there is no ILI tool available in the specific required diameter and wall thickness range in the market that meets the requirements or performance specifications necessary to provide essential information for engineering assessments and the proper ranking of such features.
The primary objective of the research and validation is to develop an approach that provides a systematic method for identification and, potentially, a correction factor for depth sizing. These critical attributes can then be effectively used for engineering calculations, priority ranking and risk mitigation activities.
This innovative approach incorporates years of accumulated knowledge from other pipelines to develop a systematic analysis approach. Additionally, it involves the calibration of this approach through collaboration with the operator, utilizing advanced and non-conventional in-ditch NDE techniques to determine accuracy, and potentially employing destructive testing during lab testing.
This paper is a summary of the research and collaboration between NDT Global’s international experts and a USA pipeline operator.
Ron Thompson1, Xavier Ortiz2, Richard Kania3, Andrew Corbett1, Guillermo Solano1
1Novitech Inc., Toronto, Canada. 2Plains Midstream Canada, Calgary, Canada. 3KanEnergy Partners Inc., Calgary, Canada
In the late 1990’s, the discovery of stress corrosion cracking (SCC) in orientations other than the axis of the pipe triggered new studies into the factors associated with off-axial cracking. Since most of the crack colonies appeared to be close to 90 degrees to the axis of the pipe, the investigations focused on circumferentially oriented SCC (CSCC). Notwithstanding, there have been many documented cases of cracks at angles other than 90 degrees, notably at the same angle of the spirally applied tape in tape-coated pipelines. These off-axis cracks have been incorporated into the models developed to address CSCC.
CSCC management programs use of a combination of quantitative and qualitative data involving bend strain along with susceptibility criteria, geohazards and areas of pipe movement, and ILI where available. As CSCC investigative and remedial work continues, off-axis cracking is starting to be found in larger numbers, with skew angles to the axis of the pipe ranging from 45 to 90 degrees. These skew angles can exceed the specified detection range of ILI tools, leaving operators without a diagnostic option for modelling these types of features.
This study illustrates the successful management of both circumferential and off-axis SCC by using a magnetic based ILI system to determine crack depth, crack length and the primary crack colony skew angle. The determination of all these crack attributes, particularly the skew angle, enabled modelling the interaction between axial and hoop stresses, to calculate the pipeline’s remaining strength.
The diagnostic data for the program was obtained using ILI technology that included three sensor systems: AMFL, CMFL, and IDD-SM™. This technology reliably provided crack length and depth sizing with an accuracy of +/- 15% and, for this study, the measurements of the primary colony skew angle with a target accuracy +/- 10°.
The ILI’s crack sizing and crack skew angle measurements were corroborated through an extensive excavation campaign, which also established ILI detection (POD) and identification (POI) greater than 95%, this accuracy supported the use of crack model predictions that could be incorporated into reliability programs.
The ILI reported and verified CSCC locations also supported the management of geohazards as it was possible to identify potential ground movement locations that were not highlighted by geotechnical desktop and field investigations.
The lines used in this study had a nominal diameter of 8.625” and were investigated for occurrences of all threat types including off-axis and circumferential cracking. Field inspection data was gathered to support the finding of this study and the implementation of the model.
Chris Alexander, Chantz Denowh
ADV Integrity, Inc., Manolia, USA
One of the greatest challenges facing today’s pipeline integrity engineers is determining the threat level a given feature or defect poses to a pipeline system. The process employed by most pipeline integrity engineers starts with inspection measurements made with in-line inspection tools or in-the-ditch inspection technologies. If the measured data are deemed a threat to pipeline integrity, an assessment is conducted using either closed-form engineering equations or numerical modeling techniques such as finite element analysis. To supplement assessment efforts, a well-designed and conducted full-scale testing program can provide valuable insights about the true performance characteristics of a defect and improve the accuracy of failure prediction methods.
This paper includes examples of how full-scale testing can be used to provide a more accurate and complete picture of defect performance under various loading conditions including burst, cyclic pressure, tension, and bending. Included is a brief description of the types of tests that can be conducted, accompanied with photos from actual tests. Information is also included on the types of equipment and measurement devices that are used in full-scale testing. The goal of this paper is to demonstrate the inherent benefits in employing full-scale testing as a means for better understanding and predicting the threat levels associated with certain defects.
Chantz Denowh1, Robert Stakenborghs2, Liang Yu3
1ADV Integrity, Inc., Houston, USA. 2Advanced Microwave Imaging, Baton Rouge, USA. 3Baker Hughes Flexible Pipe Systems, Houston, USA
The use of spoolable composite pipe technologies in the onshore oil and gas industry has expanded significantly over the past decade. It is anticipated that interest will only continue to grow as oil and gas operators transition to transporting alternative fuels such as hydrogen and carbon dioxide. Currently, these technologies have been limited to non-regulated lines such as gathering lines or produced water transport, but the need is growing to expand into the high-pressure transmission pipelines. These lines will typically be in the 4-inch to 8-inch size range and rated up to 3,000 psig. There are several gaps in knowledge to address though before making this step. One gap is the need for viable inspection technologies that pipeline operators can for long-term integrity management.
This study works to address this gap by progressing the multifrequency microwave technology and evaluating its accuracy against simulated defects that commonly occur to spoolable composite pipes in the field. The phases of the study described in this paper include an initial calibration of the microwave technology to the pipe design, material types, and layer depths. Following calibration, an open inspection was completed on pipes with known defect location, size, and depth. This information was shared with the microwave vendor to improve sizing and location accuracy of equipment and software. Additional pipes with similar defects were then used for a closed inspection to evaluate the technology’s ability to accurately locate and size unknown defects. The pipe used in this study was nominal 4-inch with a nominal pressure rating of 1,500 psig.
The last phase of the study included inspection of pipe samples with simulated damage that commonly occurs in the field. Examples of recreated damage include pipe ovalization, overbending (kinking), and over-tensioning. This damage was recreated in a laboratory setting. The damaged pipes were subjected to destructive testing following the inspection (test results not included in this paper). Results and findings from each of the above phases are described in this paper including an evaluation of the location and sizing accuracy. Inspection of the simulated damage is discussed and compared to results of the destructive testing where damage indicated the presence of damage in the pipe reinforcement.
Michael Rosenfeld1, Richard Gailing2, Benjamin Zand1, Joel Anderson3
1RSI Pipeline Solutions LLC, New Albany, OH, USA. 2Retired, Sandy, OR, USA. 3RSI Pipeline Solutions LLC, Oklahoma City, OK, USA
To reconcile differing requirements for pipeline cover in various standards and regulations, an evaluation was performed of the effect of cover depth and consistency on susceptibility to damage, other threats, risk, cost-benefit, and construction, with some surprising results. Current and historical US and foreign gas and liquids standards and regulations were compared. US and international incident data were analyzed to determine the relationship between cover depth and mileage-normalized risk of damage, and risk of other integrity threats such as geohazards and corrosion. FEA was performed to understand how cover depth and trench design affects susceptibility to rock damage. A cost-benefit analysis of increased depth of cover was performed. Sensitivity of transported product (gas vs liquid) to the benefit of cover were determined. Recommendations were made for improved codes content.
Rick Sugden
Kiefner and Associates, Denver, USA
Modern hydrostatic testing is often seen as a “check the box” for new construction. It is required by code for most pipelines. In the fast-paced culture of “get ‘er done” world, is pipeline hydrotesting still needed? With so many technological advances, can we just remove this requirement? In the mind of the inspector, are discrepancies: “just temperature”, “not regulated”, “don’t matter?” This presentation is designed for the inspector that is signing off their name on a hydrostatic test. Do you believe that this pipeline is safe, that it is not leaking? I will discuss what is obvious, what is not so obvious and why You as inspector or engineer should verify all the data. By the way, what are you signing for? What should you be concerned about? How will the new regulations impact the future of hydrotesting?
Mick Collins
Intero Integrity Services, Houston, USA
Traditionally, Gulf of Mexico (GoM) Outer Continental Shelf (OCS) owners and operators have sought alternate methods to assess the integrity of their gathering lines than inline inspection. In April 2010, the Deepwater Horizon explosion, and subsequent blowout, brought significant scrutiny from both state and federal regulatory agencies.
A customer approached Intero Integrity Services in 2019, in order to evaluate feasibility of inline inspections of its liquid gathering system in the GoM. The feasibility included three areas: 1) Technical ability to inspect; 2) Cost of inspection; and 3) Value of reported results.
From a technical standpoint, the customer conditions challenged just about every aspect of standard inline inspections: Never pigged for maintenance nor integrity assessment; 1500 psi static pressure; limited operating space on platform; remote location (90+ miles offshore); inability to track during the inspection (2,000’ water depth); limited pipeline availability based on production schedule; 8” nominal x 0.812 wall thickness x 25 mile pipeline; back to back “jumpers” to loop pipeline; and pumped in sea water. This paper will explain how, working closely with the operator, flow conditions were tightly controlled.
From a cost perspective, the customer had limited assessment options. The field was initially developed in 1998 and has operated in multi-phase production for 20+ years. If pipeline replacement is required, the field will just shut-in based on ROI compared to the current production curve. External assessment methods are limited (ROVs and divers) and need to be more comprehensive. Other than inline inspection, a hydrotest was the only option. Again, not valuable information for the cost.
Corrosion was detected in an area that had limited access; therefore, the operator decided that an annual inspection would be conducted and detailed corrosion growth assessments completed, and also to quantify the effectiveness of corrosion mitigation methods. Data sets will be presented that show the challenges of detecting defects under external clamps, and the variability between said datasets.
With the 0.812” wall thickness, the only inline inspection solution was ultrasonic (UT) technology. Magnetic (MFL) tools would not be able to saturate the pipe wall to provide accurate measurements.
Xuejun Huang, Bryan Feigel, Victor Jablokov
Massachusetts Materials Technologies, Natick, USA
Material toughness is needed when analyzing the critical crack size that would fail at MAOP and when performing a fitness-for-service evaluation with cracks discovered during inspection. If toughness data is not available, gas transmission operators will be required to use conservative values or perform cut-outs for lab testing or other industry-accepted data, such as collected by nondestructive testing per 49 CFR §192.607. A portable, minimally invasive technique has been developed to provide pipe body toughness data using the planing-induced microfracture method. The material removal from the test is in the range of 0.010 to 0.030 inch deep. A crack is successfully introduced by the technique through a unique stretch passage feature. FEA simulation has confirmed a high triaxiality value in front of the generated crack that is comparable to the one in a compact tension specimen used in a conventional fracture toughness test. Toughness results obtained using this new technique were compared to lab test results using Charpy impact and fracture toughness tests. Preliminary results from a small test of 13 samples showed that the technique could predict KIc within ±15% of the lab values. The achieved accuracy was in a similar range as estimating KIc using lab CVN test data on the same samples. A more extensive validation test will be performed on 50 vintage pipe samples with various toughness values. This paper will give an overview of the planing-induced microfracture method, the new portable tool, the process to obtain fracture toughness from the test data, and results from the validation test. A prototype device based on this technique is being tested for pipe body toughness, as a complement to the existing frictional sliding technique to test for longitudinal seam toughness.
Janille Maragh1, Jonathan Gibbs2, Peter Martin3, Jeffrey Kornuta4, Peter Veloo5
1Exponent, Inc., Menlo Park, CA, USA. 2Pacific Gas and Electric Company, San Ramon, CA, USA. 3RSI Pipeline Solutions, LLC, New Albany, OH, USA. 4Exponent, Inc., Houston, TX, USA. 5Pacific Gas and Electric Company, Oakland, CA, USA
Nondestructive testing (NDT) of chemical composition is a critical component of the Pacific Gas and Electric Company’s (PG&E) materials verification program. Additionally, 49 CFR § 192.607 states that the operator must “conservatively account for measurement inaccuracy and uncertainty using reliable engineering tests and analyses.” Accurate and precise NDT composition data can be used to determine or verify certain characteristics of a pipe, for example vintage, grade, or manufacturing process. However, it has been observed that composition measurements may at times be inconsistent across various field analytical tools, possibly due to the variability of experimental, environmental, and other statistical (random) factors. Anomalous field NDT measurements are problematic because they could lead to the mischaracterization of pipe features during the materials verification process.
In this paper, we present a tool for the in-field checking of chemical composition NDT data for potentially erroneous or inconsistent measurements. The presented tool, which is spreadsheet-based and therefore easily and independently implemented by operators, identifies sets of measurements that exhibit two commonly observed irregularities in field data: large standard deviations, which usually indicate the presence of outliers or excessive scatter; and greater-than-usual differences between the chemical compositions at different test locations on the same pipe joint. For a given set of measurements, the tool flags the standard deviation as too large if it is high relative to standard deviations that have been previously observed for the tool/element combination of interest. Large differences between the chemical composition measurements at different test locations on the pipe joint, which may be the result of surface contamination, surface preparation issues, or environmental differences, are identified through comparison to compositional differences that have been observed on all previously tested pipe joints. Because this tool is designed to work with raw data from NDT chemical composition tools, it may be used to enable field technicians to identify potential errors in near real-time. The improved data reliability increases confidence in downstream analysis and reduces the need to return to a site to perform re-work, allowing for a more efficient and less costly materials verification process. The implementation and in-field use of this tool for live retesting to mitigate potential downstream issues are demonstrated for a set of portable X-ray fluorescence (XRF) data.
Joel Anderson1, Michael Rosenfeld2, Peter Martin2
1RSI Pipeline Solutions, Oklahoma City, USA. 2RSI Pipeline Solutions, New Albany, USA
The requirements of 192.607 state that if an operator lacks traceable, verifiable, and complete records they must implement procedures to verify the physical pipeline characteristics and attributes, including diameter, wall thickness, seam type, and grade. Since pipe grade can’t be directly measured, it must be inferred from measurable physical characteristics like strength, geometry, and composition. Because the minimum yield strength (YS) specified by the pipe grade factors directly into calculation of MAOP, there is a tendency to incorrectly use the measured YS as the sole indicator of the immeasurable grade. Though the two are loosely correlated, they are not equivalent. Grades are assigned labels that relate to ranges of allowable YS, composition, geometry, inspection requirements, and manufacturing practices. Additionally, a single YS can overlap up to four different adjacent grades. This makes YS a vague indicator of grade at best.
The mapping of YS into a single grade classification in the absence of additional information can be done quickly and with minimal effort, making it seem like an attractive approach. But this technique is fraught with potential issues that can lead to non-conservative assumptions that have a cascading effect. This paper will demonstrate the various challenges to pipe grade classification and why it is necessary to consider all the available information. Not just YS but consideration of operating history, design standards, chemical composition, and microstructure is necessary to provide a high level of assurance of a safe MAOP that will stand up to scrutiny.
Mike Kirkwood1, David Stordeur2, Neil McKnight1
1T.D. Williamson, Swindon, UK. 2T.D. Williamson, Nivelles, Belgium
As the industry transitions to renewables and de-fossilization of the energy sector, “new” products are being introduced into pipelines. Pipelines will remain a relevant and efficient way to transport energy over long distances, but this energy, and associated byproducts, could take some form other than natural gas. Such products as hydrogen, biofuels, ammonia, carbon dioxide, steam and hot water are the talk of the pipeline industry but, are these products new?
For many years, operators of transmission and distribution pipelines have focused on the development of expertise to safely operate natural gas pipelines. Operating a pipeline with other products will bring some new challenges but it may not be necessary to start from a blank page – these products are not completely new to the pipeline industry.
This paper will share some experiences of pigging, inspection, intervention and isolation in some of these challenging products. Each product has its own characteristics that make it difficult to work with but, over the years, technology and processes have been developed to ensure that these pipelines can be cleaned, inspected, accessed and repaired. The paper will also present the experiences in developing these solutions and how this knowledge can be applied to current and emerging applications today.
The paper will present the historic development of the solutions and use case studies to illustrate how these tools and techniques can be applied today. Areas where additional development is still needed will be highlighted and current industry response will also be discussed. The aim of this paper is to share previous learning to ensure that the move to de-fossilization happens safely.
Key Words: Energy Transition, De-fossilization, Hydrogen, Carbon Dioxide, Ammonia, Pigging, Inspection, ILI, Intervention, Isolation, Repairs
Tyler Tunic1, John Chekan2, Beau Gribbin3, Cailin Harrington4, Josh Harris1, Tyler King5, Quang Vo6, Scott Schubring1
1Williams, Houston, USA. 2Williams, Big Piney, USA. 3Williams, Pittsburgh, USA. 4Williams, Fort Lupton, USA. 5Williams, Connellsville, USA. 6Williams, Tulsa, USA
Natural gas-powered electricity generation enhances reliability in the U.S. electric power grid and provides the necessary backup supply that supports growth in renewable forms of energy. The nation’s natural gas supply continues to grow, leading to stable and affordable energy costs for customers. As demand for lower carbon energy intensifies, natural gas pipeline operators like Williams are exploring options to reduce greenhouse gas emissions during the transmission of natural gas. Improvements in operational efficiency and design have already led to a significant reduction in fugitive methane emissions. Pipeline operations also create carbon dioxide, the mitigation of which is distinct from that of methane.
One solution under consideration is the replacement of combustion-driven compression with electric-driven compression. This switch will lead to a significant reduction in station Scope 1 emissions, particularly carbon dioxide. It is important to consider the additional challenges and consequences that come with replacing gas-fired drivers with electric motor drives. For example, not only do electric drivers produce Scope 2 emissions, but their installation represents a coupling of two systems critical to the nation’s energy system, reducing redundancy across the value chain. In the interest of analyzing these challenges and consequences, Williams conducted a thorough examination of the potential impacts of transmission station electrification.
Electrification of compressor stations will expose the energy value chain to further reliability risks with highly regionalized greenhouse gas reductions. Installation of electric drives should be considered on a case-by-case basis alongside other decarbonization strategies to ensure the continued delivery of clean, reliable energy.
David Futch
ADV Integrity, Inc., Magnolia, USA
Charpy v-Notch tests are a common laboratory test to infer the toughness of a material. These tests are quick, relatively inexpensive, and allow for the development of a ductile to brittle transition curve. Standard geometry is specified with a cross section of 10 mm x 10 mm. This cross section is typically not achievable when testing pipeline steels unless it’s of thicker wall thickness and/or larger diameter so the curvature doesn’t impact the specimen. Half-size (or smaller) specimens are more often than not required for vintage smaller diameter pipes.
Although not specially mentioned in industry codes and standards, fabrication of the specimens may require flatting to obtain a larger wall thickness during testing. However, flattening these specimens results in additional cold work, which may locally alter the material properties of the specimen. In some cases, it’s necessary to flatten, however, in many cases a smaller subsize specimen is obtainable without flattening.
This study compares the results of flattened vs non-flattened specimens for varying vintage, seam type, and geometry (outer diameter and wall thickness). Results show both conservative and non-conservative shifts in the CVN transition curves when comparing flattened specimens to non-flattened specimens. Finally, these results are utilized to compare how the shift in CVN outputs affects a remaining life calculation where upper shelf CVN absorbed energy is an input.
Ryan Holloman1, Greg Thorwald1, Michael Turnquest1, Mark Neuert2
1Quest Integrity, Boulder, USA. 2Enbridge, Edmonton, Canada
Accurate evaluation of the remaining strength of crack-like flaws identified via pipeline inline inspection (ILI) or in-ditch non-destructive examination (NDE) is critical to ensuring continued safe operation of liquid and gas transmission pipelines. Modern pipeline ILI tools have sufficient resolution to detect longitudinally overlapping crack-like flaws that exist in the same radial plane, referred to as stacked cracks. Depending upon the crack sizes and pressure loading, stacked cracks can interact to reduce burst pressure below that of any of the individual stacked cracks.
Closely located cracks are often evaluated using interaction criteria, such as those provided by API 579-1/ASME FFS-1 Part 9 (API 579), which specify how and when multiple nearby cracks can be combined into a single crack for the purpose of an integrity assessment. When applied to stacked cracks, the interaction criteria can often lead to a more urgent response from the pipeline operator.
Here, improved interaction criterion was developed for stacked cracks based on the results of elastic-plastic finite element analysis (FEA) models of multiple combinations of stacked crack sizes and orientations, pipe material properties, and operating stress. These improved interaction criteria provide pipeline operators with an easy-to-apply methodology to analyze stacked cracks that reduces the excess conservatism associated with legacy methods.
Gavin Duncan
Online Electronics, Aberdeen, UK
Pig tracking using electromagnetic (EM) transmitters is not a new concept, yet we are still uncovering ways to improve detection. As an example, the industry standard frequency for EM transmitters used in pigging applications is 22Hz however after extensive testing and by applying the science, it is now becoming evident 22Hz is not the optimal frequency for pig detection. We can now look at the actual performance of different frequencies in a variety of pig tracking applications and how this affects the task at hand. We have always known that signal strength can be affected by project specific factors such as pipeline diameter, material & wall thickness, pig design, pig velocity and if the pipeline is buried or subsea. However, in addition to frequency, we now know that the specification and configuration of the transmitter itself can also have a significant impact.
This paper will detail the factors that have previously been overlooked when trying to optimize pig detection and will provide recommendations on how to positively impact the effectiveness of this task. It will evidence this using a recent example whereby we carried out comprehensive “real life” testing prior to a project to ensure that the EM transmitters were configured to ensure the highest probability and greatest efficiency of detection while meeting the battery life constraints. It will also answer the question…is there any logic in specifying an EM transmitter’s performance by distance through air?
Jane Dawson, Steven Farnie
Baker Hughes, Cramlington, UK
The determination of corrosion growth rates and their application in the prediction of future severity is a critical part of pipeline integrity management. Accurate corrosion growth rates are needed to predict pipeline reliability as a function of time, to identify the need for and timing of field investigations and/or repairs and to determine optimum re-inspection intervals. The consequences associated with both underestimating and overestimating growth rates can be significant in terms of both safety and resource performance.
The use of repeat ILI data to match and compare metal loss sites in order to estimate the corrosion growth rates at individual defects along a pipeline is a well-used and established practice in the industry. There are many ways that corrosion growth rates can be used in future integrity predictions with most approaches only accounting for corrosion growth in the depth dimension taking no account of surface area growth and potential interactions between adjacent corrosion areas over time.
Now that we have a wealth of historical data with 3, 4 or even 5 sets of ILI data for the same pipelines we are able to experiment with more advanced three-dimensional modelling and have the ability to test new approaches vs actual “truth” data. With the benefit of this progressive viewpoint, the methodologies employed for evaluating and applying ILI based corrosion rates are being further improved and refined to give more accurate predictions of the future pipeline condition, the response schedule and for setting the timing of re-inspections.
This paper describes a new approach that predicts how an area (cluster) or corrosion could grow over time combining with surrounding corrosion defects and with newly developing defects as well as in the depth dimension. The main differences between this and the more established approaches are:
The new approach is illustrated and compared to the more established methodologies via the use of case studies on real ILI data sets.
Fraser Gray, Susannah Turner, Jack Davies
Highgrade Associates Limited, Newcastle upon Tyne, UK
In-line inspection (ILI) is the primary technique used for detecting and sizing corrosion metal loss in pipelines. The Pipeline Operators Forum (POF) requirements state that ILI vendors should provide Probability of Detection (POD) and sizing specifications for metal loss anomalies of different sizes (classified by the detected anomaly length and width). However, these sizing classifications do not represent the often complex morphology of corrosion. For example, deep pits within shallower general corrosion may be simplistically categorized within the general sizing classification.
This paper explores the impact of corrosion morphology on ILI tool detection and sizing capabilities, using real life examples. The review considers corrosion validation data for three anonymized pipelines, with ILI data from three different vendors using two different tool technologies, Ultrasonic Wall Thickness Measurements (UTWM) and axial Magnetic Flux Leakage (MFL). Methodologies given in API 1163 (2021) have been used for the analysis of ILI tool performance and examples of validated corrosion and associated ILI sizing are discussed. The potential impacts on integrity assessment are also considered.
The review presented in this paper provides insight on the performance of both MFL and UTWM ILI detection and sizing capabilities for complex corrosion anomalies (such as deep pits within shallow general corrosion). The potential for integrity assessment of pipelines with this type of corrosion morphology to be non-conservative due to treatment of ILI sizing tolerance is also discussed, considering both through-wall leak and pressure-driven burst failures. The findings of this paper further support previous research stressing the importance of validating more than just the deepest ILI reported anomalies, to understand the corrosion morphology, the actual sizing uncertainty of the ILI, and the associated impact on integrity assessment.
Nikos Salmatanis1, Craig Champlin2
1Chevron Technology Company, Houston, Texas, USA. 2Upstream Vee, LLC, Golden, Colorado, USA
PHMSA has mandated that operators of hazardous liquid pipelines implement at least two technologically complementary forms of leak detection on all pipelines by October 1, 2024. This includes sections not part of high-consequence areas (HCAs). In-line acoustic leak detection multi-sensing inspection balls (MSIBs), a type of Small Inspection Device (SID), are a popular complement to conventional pressure monitoring because, with the right pipeline operational conditions, they are able to detect very small leaks that conventional pressure monitoring systems may miss. Further, MSIBs do not require a pipeline shutdown and require little to no modification of existing lines. This talk presents a patent-pending tool for extracting MSIBs from an operating pipeline without having to shut down the line or reduce its flow rate. This tool extracts the MSIB through a pressure-balanced 2 or 4-inch lateral tee, avoiding the expense and complexity of installing and operating a pig trap or pigging valve.
KEYWORD(S) FOR SUBJECT AREA: Emerging Issues, Leak Detection, NDE, Receivers, Traps, “Unpiggable” inspections and technologies
Sergio Limon, Ming Gao, Ravi Krishnamurthy
Blade Energy Partners, Houston, USA
An increasing number of in-line inspections (ILI) for assessing pipelines for cracking and seam weld anomalies are being carried out for the first time in more pipeline segments than before and reassessments are more common. These inspections have resulted in an increased need to evaluate and identify which planar defects pose an immediate or future safety concern to pipelines, since not all cracks and seam weld defects are injurious. For PHMSA regulated gathering and transmission pipelines, a prioritized response criteria for ILI reported indications now include response conditions based on failure pressure predictions. However, there is no unified single failure stress model nor method for estimating the failure pressure of pipelines with cracking and seam weld anomalies. The analyst is tasked with choosing from several failure stress models available to evaluate the rupture pressure capacity of a pipeline in the presence of planar defects and to estimate leak/rupture behavior.
In this paper, considerations for the selection of failure stress models are provided within the context of the type of defect being evaluated, the pipe known or expected fracture mechanism (brittle cleavage/quasi cleavage, or ductile/micro-void coalescence), fracture toughness data available or assumed, failure criteria, the fracture mechanics basis of the models and their solution space for cracks and seam weld defects. A miss-match between any of these factors can result in unreliable predictions or overly conservative results.
Johannes Keuter1, V Mackissack2
13P Services, Wietmarschen, Germany. 23P Services, Chicago, USA
An 18″, North Sea, heavy wall, offshore wet gas flowline with known debris interference, had to be inspected. The total length is 286km with up to 27.3mm nominal wall thickness. Potential corrosion had been detected in a previous 3rd party in-line inspection. However, the POI was limited and no clear differentiation between corrosion and debris was possible. Hence, the previous inspections were not fully successful, and the data couldn’t be used for a full evaluation of the client’s problems. 3P Services was asked to perform a metal loss inline inspection of the pipeline as soon as possible. Following on from a specific cleaning program, 3P proposed an 18″ GEO/MFL/DMR combo tool. This tool combines a heavy wall magnetizer with a geometry measurement segment and special DMR sensors, wall guided as well as in a stand-off configuration. The combination of these different sensor technologies allows an optimized differentiation between debris, internal corrosion, or internal corrosion with debris. This information was used to improve the POI and anomaly sizing. The challenges and solutions of this outstanding project are explained in this paper.
Jed Ludlow1, Adrian Belanger2, Ron Lundstrom1, Miguel Maldonado1
1T.D. Williamson, Salt Lake City, USA. 2T.D. Williamson, Houston, USA
Reliable assessment of pipeline corrosion remains an important concern for pipeline operators, especially when the corrosion presents itself in complex patterns and in large quantities. We present an approach to this problem using magnetic flux leakage inline inspection employing multiple magnetization directions simultaneously. The approach is accomplished in production data analysis and scales to large quantities of corrosion anomalies.
An axial magnetic flux leakage data set and a spiral magnetic flux leakage data set are gathered simultaneously during the same inline inspection run, and the signals from both data sets are also analyzed simultaneously. Detection, identification, and sizing of metal loss anomalies can be accomplished using one or the other magnetization direction and even a combination of both magnetization directions where appropriate. After sizing, metal loss clusters can be formed from applying interaction rules to combinations of the metal loss anomalies regardless of the data set from which they originate. This facilitates reliable failure pressure estimation using effective area methods even for narrow axial corrosion morphologies that would not be well addressed by conventional axial MFL alone and for other complex corrosion patterns. Application examples demonstrate that comparisons of failure pressures estimated from inline inspection data are in close agreement with those calculated using data from non-destructive evaluation in the ditch.
Keywords: inline inspection; magnetic flux leakage; corrosion; effective area methods
Jeff Sutherland
Baker Hughes, Calgary, Canada
This paper will discuss aspects of pipeline integrity, and a perspective of threats and the damage mechanisms of pipelines, namely the presence of defects and the susceptibility (threat) for such defects to initiate and occur, through their related mechanisms.
We start with the broad premise that damage mechanisms become accelerated with the presence of hydrogen in natural gas pipelines, while acknowledging that ongoing research is very active to refine and qualify specific parameters and situations.
Also, as a premise of treating this situation of a pipeline conversion as a change of service, with some common direct steps to establish a readiness for service. A key premise is the need to establish a baseline reference for defects and integrity and failure/leakage sources. Including some conventional defects that may become more prominent for integrity concerns due to their potential nature to concentrate H2. (Historically, a significant change would be a liquid to gas operation or vice versa – or a notable change in product like sour gas versus conventional gas).
And fundamentally from a conventional integrity perspective, we will describe aspects of what is the same and what is different for integrity data coming from ILI tools and achieving a state of readiness. This includes a perspective of what readiness means for ILI tools, their operation in hydrogen blended pipelines, and expectations for data reporting.
Ana Paula Gomes1, Marco Marino1, Giuseppe Giunta2
1Enivibes, Milan, Italy. 2Eni, San Donato Milanese, Italy
This paper focuses on detection of leakage occurrences, particularly those that occur on buried pipelines and can be caused by factors such as corrosion, wear, or illegal tapping. Such events can cause considerable harm to the pipeline operator and the environment, including critical damage to the pipeline and surrounding lands, leading to large remediation expenses and operational downtime.
The management of assets has the primary objectives of ensuring reliability and integrity of pipelines during their operations. To achieve these goals, procedures and technological systems are implemented to quickly detect and address any possible or real hazards to the integrity of the assets.
Vibroacoustic Technology presents a solution to this problem by detecting both the leakage and its precise location, as well as other anomalies involving the pipe and/or the transported fluid. This technology is currently operative globally, protecting thousands of pipeline kilometers, primarily on buried pipelines.
Initially developed for Leak Detection (LD) applications, the Vibroacoustic Technology has demonstrated excellent performance in detecting and localizing spillages and impact events in real-time. In certain conditions, it has also been shown to identify activities that precede a spill, such as illegal tapping preparation activities, corrosion, and wear. The present work highlights the outstanding performance of this technology in detecting illegal tapping in Italy, with multiple examples reported.
Before the implementation of this technology, Italian pipelines transporting refined products suffered numerous leakages due to fraudulent activities. However, after the extensive deployment of Vibroacoustic Technology across the pipeline network, illegal tapping almost ceased to exist. The use of this technology was later adopted as a prevention tool, and a complete presentation of the challenges and solutions put in place to overcome them is included in this work. The success of this implementation was due to a holistic approach and a high level of collaboration between multiple parties.
In conclusion, Vibroacoustic Technology presents a reliable solution to detect and prevent leakage occurrences, particularly illegal tapping, in pipelines. The technology has demonstrated outstanding performance in real-world scenarios, and its widespread deployment has resulted in a reduction of pipeline incidents, protecting both the operator and the environment.
The present work provides a comprehensive overview of the challenges and solutions involved in implementing this technology, highlighting the importance of a holistic approach and active collaboration between pipeline operator, local inspection teams and law enforcement to achieve successful results.
Hamza KELLA BENNANI1, Jim Hart2, Ali Fathi3, presented by Mehdi Laichoubi1
1Skipper NDT, Paris, France. 2SSD, USA. 3Enbridge, Canada
Buried pipelines are critical for infrastructure transporting large amounts of oil and gas products across long distance. Several integrity threats need to be monitored to avoid incidents, amongst which geohazard events are responsible for at least 16% of failures over the last 10 years. Geohazards result in permanent ground displacements, which may cause axial and/or lateral deformations that induce bending strains in these structures, leading to catastrophic consequences. To address this issue, Skipper NDT has developed a proprietary embedded system mounted on a drone, with the aim of generating a high-precision digital twin of buried pipelines. This technology enables the acquisition of position data with high data density, which can be utilized to assess bending strain. To validate the effectiveness of the technology, a series of tests were conducted in coordination with Enbridge in North America. The results of the drone-based technology runs were compared against those obtained with an Inline Inspection tool. The comparison showed good agreement in the trends detected in terms of bending strain profiles.
56. Risk Based Prioritization of Hard Spot Mitigation
Kelly Thompson1, Cassandra Moody2
1Dynamic Risk Assessment Systems, Inc., Calgary, Canada. 2Time For Change, LLC., Houston, USA
Abstract
Hard spots are a pipeline defect created during original manufacturing. These are typically considered stable unless acted upon by coincident environmental factors including coating degradation, atomic hydrogen, and stress. As a result of industry lessons learned and recent hard spot related failures on its system, Williams is executing a hard spot mitigation program that encompasses improvements to our risk assessment model to account for hard spot defects. In this presentation, we will share how we are incorporating this risk into our modeling approach and how those results influence the mitigation effort. Additionally, this presentation will discuss the benefits that can be realized through broader industry collaboration, current collaborative studies underway, and key metrics to advance industry understanding of the hard spot risk that ultimately will improve overall pipeline safety.
Topics of Discussion
Abstract: Pipeline Risk Forum
89. Enhancing EMAT Crack Detection Services Using State of the Art Deep Learning
Stephan Eule1, Thomas Beuker1, Neil Pain2
1Rosen EU, Lingen, Germany. 2Rosen USA, Houston, USA
Abstract
EMAT crack detection technology is used worldwide by many oil and gas operators to detect and size cracks in liquid and gas pipelines. By collecting data of increasingly higher resolution and quality, it is possible to achieve a more and more accurate representation of the integrity reality of oil and gas structures.
However, the prerequisite for gaining insights from this data is provided by Artificial Intelligence (AI) methods and a corresponding Research-First structure of a company. The AI division at ROSEN Research Center invested significant time and resources to apply powerful machine learning in particular Deep Learning methods to ensure timely and accurate inspection results delivered to operators. These efforts are directed towards building data driven applications to ensure reliability of inspection systems. Supported by a modern data engineering infrastructure, AI-powered data-driven applications can be used to enhance both the quality and efficiency of inspection data analysis.
This paper will provide an insight on how ROSEN uses AI-methods to enhance classification and sizing of metal-loss and crack indications in pipeline inspection data. Particularly, how Deep Learning methods help ensuring the quality of EMAT-Crack detection services.
KEYWORD(S) FOR SUBJECT AREA: Machine Learning, EMAT Technology
88. EMAT Lessons Learned Using Assessment Findings
Christopher De Leon, Rhett Dotson
D2 Integrity, Houston, USA
Abstract
The INGAA Foundation formed a joint industry project (JIP), on behalf of INGAA, to develop an industry technical guidance document specific to the use of Electromagnetic Acoustic Transducer (EMAT) in-line inspection technology for management of cracks, with specific emphasis on stress corrosion cracking (SCC). EMAT ILI has been used for over two decades and has reached a level of maturity where both the performance specifications and response planning can be systemized. However, the use of EMAT has mostly been limited to early adopters and requires implementation of processes and procedures particular to EMAT for it to be used as an integrity assessment. With recent changes to gas pipeline regulations in 49 CFR 192 associated with integrity assessments and MAOP Reconfirmation, the use of EMAT ILI for crack management is expected to increase by new and existing users. This technical guidance document was developed to benefit industry from the experience of the JIP members and provide knowledge sharing. This presentation will provide a knowledge transfer on this subject through an overview of how to use the published guidance document and the lessons learned from its development.
87. Inline Inspection Monitoring and Data Interpretation Using Fiber-Optic Sensing
Jerry Worsley1, Jason Reynaud2, Tony McMurtrey3, Adnan Chughtai4, Josh May4
1Schlumberger Midstream Production Systems, Dubai, UAE 2Schlumberger Midstream Production Systems, Houston, USA 3Midstream Integrity Services, San Antonio, USA 4Schlumberger Midstream Production Systems, London, UK
Abstract
Fiber-optic sensing systems are becoming more commonly used for leak and third-party intrusion detection on pipeline infrastructure throughout the world. This has been recognized by their recent inclusion in the latest editions of API 1130 and API RP 1175. Sensing systems also have a part to play in the operational aspect of pipeline management. This includes the monitoring of most pipeline pigs, ranging from typical batching or cleaning pigs that may be run frequently to the critical inline inspection tools that inspect pipelines less frequently.
Early adopters of fiber-optic distributed acoustic sensing (DAS) systems discovered that these solutions could identify the location of pigs as they traversed the pipeline as well as pinpoint the location of a stuck pig, enabling the pipeline operator to immediately take action to dislodge the stuck tool and even mobilize to the location to remove the pig through intervention. The latest evolution of DAS from qualitative to quantitative data means that the information gathered is richer, and the greater fidelity results in more precise and certain feedback for the operator.
This paper focuses on operational pigging data gathered by Midstream Integrity Services for a 720-mile pipeline in Texas and confirms that fiber-optic sensing can support and complement routine operational pigging as well as intelligent pigging by removing the risk and inaccuracy associated with traditional pig tracking methodology.
86. Inline-Inspection Crack Diagnostics for Gas Pipelines – A Novel Technology
Willem Vos, Thomas Hennig
NDT Global, Bergen, Norway
Abstract
Older gas transmission systems, specifically those built between the mid-20th century and the early 1980s can be affected by Stress Corrosion Cracking (SCC). A common methodology to address this threat is to utilize ILI tools using EMAT transducers to characterize the asset. It is common practice to utilize a magnetic flux leakage tool (TFI) in addition to the EMAT inspection to support identification and characterization of EMAT signals. Furthermore, EMAT tools have a limited operational envelope with regards to wall thickness and speed.
NDT Global has reached a significant milestone in the development of an alternative technology which addresses crack detection, identification, and sizing in gas pipelines. This new method is based on the generation of guided Lamb waves, using gas coupled ultrasonic transducers. The method allows inspection of the asset without any contact of the sensors to the pipe wall, allowing for higher inspection speeds and a wider range of wall thicknesses.
This paper presents some of the historic developments, starting with a gap analysis of existing solutions, small scale lab test results and full-scale pull testing. The developed solution combines newly developed gas coupled guided wave principles with several principles from the proven technology operated in liquids.
Keywords: Crack detection in gas, Stress Corrosion Cracking
85. Pathfinder Foam Caliper Pig Overcomes Severe Pipeline Conditions to Successfully Identify and Locate Geometric Deformations in Gas Pipeline, Mainland China
David Cockfield¹, Peter Ward¹
¹Pipeline Innovations Ltd, Cramlington, UK
Abstract
OBJECTIVE/SCOPE
This paper is to share the development of Self-Propelling Robotic In-Line Inspection technology that PETRONAS embark as OPEX optimization for un-piggable pipeline. Lack of conventional inspection methods to inspect un-piggable pipelines such as vent pipelines without pig traps facility and low flow pipelines, has prompted PETRONAS to embark on technology development journey for Self-Propelling Robotic ILI.
METHODS/PROCEDURES
The development of the Self-Propelling Robotic In-Line technology consists enhancement of robotic tethered crawler tool to a wireless robotic tool, testing and validation using actual full scale fabrication test loop. Fabricated test loop includes horizontal and vertical section with bends of 1.5D to simulate the inspection tool travel as per actual site condition representing vent line.
The enhancement consists of wireless connection range, optimum speed and distance, movement of slippery surface which grease was applied on the vertical section and emergency extraction of inspection robot.
RESULTS/OBERVATIONS/CONCLUSIONS
Robotic ILI qualification test which was successfully met PETRONAS requirement based on full scale factory acceptance test. The test was focused and able to meet below success criteria: –
Robotic ILI tool able to self-propel on vertical test spool.
Robotic ILI tool able to move with wireless connection for the intended travel length.
Emergency retrieval tool procedure and mechanism in the event of faulty robotic ILI or loss of connection.
Sensor detection capability at POD 90% and POI 80%.
Based on the evaluated technology, Robotic ILI solution is feasible in ascertaining the un-piggable pipeline integrity and recommended solution to tackle high operational costs that upstream operators face when inspecting their pipelines using current available methods. Deployment of this technology is estimated to provide up to 30% OPEX optimization.
The technology has been evaluated to be technically ready and pilot tested PETRONAS asset which will be shared in our detail paper covering below areas:
1. Robotic ILI tool able to travel successfully total length of pipeline.
2.Detection capability at POD 90% and POI 80% for anomalies covering metal loss and girth weld anomales.
NOVEL/ADDITIVE INFORMATION
Current approach to inspect un-piggable vent or low flow pipeline is Crawler ILI type technology which propelled by umbilical cable whereby the pipeline requires to be in shutdown mode. While, inspection using Self-Propelling Robotic ILI can be applied for un-piggable pipeline i.e. low flow pipeline and vent line with short duration or no requirement of shutdown.
84. Axial Flaw and Crack Detection in Multi-diameter Low-Pressure Gas Pipelines
Lance Wethey1, Pete Clyde2, John Nonemaker1
1ROSEN, Houston, USA. 2LG&E, Louisville, USA
Abstract
Louisville Gas and Electric (LG&E) owns and operates numerous natural gas transmission pipelines in the greater Louisville, KY area. Many were constructed during the 1950’s and therefore present extensive challenges to inline-inspection (ILI) efforts. Multi-diameter pipeline geometry and transient operating conditions combine to create an environment that proves difficult for running in-line inspection tools. LG&E has utilized high resolution geometry and metal loss detection solutions optimized for low-pressure multi-diameter pipelines ILI devices in their integrity management program. There was a desire to expand the technologies deployed to include technologies best capable of detecting axially oriented anomalies and cracking. To address these concerns, circumferentially induced magnetic flux leakage (MFL-C) and electromagnetic acoustic transducer (EMAT) technologies were suggested, however applying these detection methods in low-pressure multi-diameter pipelines was not available.
MFL-C & EMAT-C ILI devices capable of inspecting a pipeline with both 16″ and 20″ diameters in a low-pressure gaseous environment needed to be developed. In addition, traversal of all restrictive features, such as tight radius bends and minimal spacing between fittings, must be achieved with minimal differential pressure to facilitate stable run behavior and allow optimal data capture. ROSEN reviewed all known details regarding the targeted pipelines and compiled a list of challenging fittings to define the required mechanical passage capabilities. The conceptual design, manufacturing, and assembly stages of development resulted with redesigned low-friction ILI tools capable of full circumferential sensor coverage in 16″ – 20″ pipeline diameters. The tools were then pumped with water through a test loop that included the most restrictive features identified in the targeted pipelines. Performance results confirmed mechanical passage and determined the average ∆P’s necessary to pass the included restrictive features. Finally, validation pull tests occurred to confirm data capture functionality within established specifications. After mechanical and data capture performance were verified, the new low pressure multi-diameter 16/20″ MFL-C & EMAT-C were deemed fit for service and deployment.
This technical paper outlines the development process with examples and observations from the testing program. Difficulties related to MFL-C & EMAT-C technologies as related to low-pressure and multi-diameter environments are discussed in further detail. The paper includes real-world operational challenges and inspection results from two successfully inspected pipelines, as well as a discussion of iterative ILI tool improvements.
83. Validating and quantifying in situ NDT uncertainty of line pipe material properties
Jeffrey Kornuta1, Joel Anderson2, Emily Brady1, Janille Maragh3, Peter Veloo4
1Exponent, Inc., Houston, USA. 2RSI Pipeline Solutions, New Albany, USA. 3Exponent, Inc., Menlo Park, USA. 4PG&E, Walnut Creek, USA
Abstract
The federal rules governing the operation of natural gas pipelines allow operators to use nondestructive testing (NDT) technologies to verify pipeline material properties provided that these tools are validated against destructive test results and conservatively account for measurement inaccuracy and uncertainty. Any measurement methodology inherently has uncertainty due to both systematic and random effects: systematic errors being those that remain constant during repeated measurements, and random errors being those that vary randomly in repeated measurements. This combined uncertainty not only affects the estimation of material properties, but it may also propagate to downstream analyses, such as during maximum allowable operating pressure (MAOP) reconfirmation. Moreover, this uncertainty might adversely affect the accurate determination of comparable pipe segments when establishing sampling populations.
This paper presents Pacific Gas and Electric Company’s (PG&E) approach for the statistical inference of destructive laboratory values when in situ (field) NDT measurements are collected. This approach has been formulated from an in-house statistical validation of NDT technologies whereby NDT measurement results are compared against laboratory destructive test results. The types of material properties that PG&E has evaluated using NDT technologies include microstructure, hardness, chemical composition, yield strength, and ultimate tensile strength. In total, several thousand NDT measurements across approximately one-hundred pipe features have been evaluated against laboratory test results. The authors describe this statistical analysis approach whereby the lab results are compared to NDT measurements through a regression model to account for systematic errors. Once the regression is performed, the scatter of the data is quantified using a prediction interval to account for the random portion of the uncertainty. Finally, the total uncertainty is quantified and propagated to downstream analyses using a Monte Carlo methodology. Current challenges to this approach are presented, and alternate statistical approaches are described which have the possibility of yielding additional benefits.
82. Pipe Grade Classification: Groundbreaking ROI From Your UHR MFL Inspection
Max Harrisson
Entegra, Reading, United Kingdom
Abstract
Operators must be able to see more and know more about the overall condition of their pipelines to keep their operations running safely and efficiently. This paper will show why the delivery of a complete and accurate Materials Classification Report is one of the most significant outcomes of employing the latest in UHR MFL technology.
This paper will take a holistic look at Ultra-High Resolution MFL and how a system incorporating the latest in UHR technology, combined with human-experience based data analysis, can provide an integrity assessment that goes well beyond POD and POI. Understanding the impact of pipe grade, maximum operating pressures, current and projected metal loss and the accurate and cost-efficient confirmation of historical pipeline data are all benefits of a truly integrated system of technology and data analysis.
We’ll look at these factors as well as how they relate to the Mega Rule and its impact on an operator’s ability to maximize throughput, ROI and pipeline integrity.
81. Know your Materials! On-site Non-Destructive Materials Testing for Gas Transmission Pipelines
Travers Schwarz1, Trevor Foster1, Steven Kinikin1, Aaron Crowder2
1SMUD, Sacramento, USA. 2Massachusetts Materials Technologies LLC, Natick, USA
Abstract
The new Mega Rule now requires pipeline operators to have Traceable, Verifiable and Complete (TVC) material records for their pipeline systems. Operators that do not have TVC records for any portion of their pipeline, must develop and implement procedures for non-destructive testing (NDT), destructive testing, examinations and assessments in order to verify these material properties for above ground line pipe and components, and of buried line pipe and components. Because of the recent ruling, Sacramento Municipal Utility District (SMUD), an operator of 76 miles of gas transmission pipeline, recently contracted Massachusetts Materials Technologies (MMT) to conduct three in-situ pipeline evaluations where they implemented positive material identification (PMI) technologies to verify and confirm the pipeline hardness, strength and ductility (HSD) properties for their pipeline. Massachusetts Materials Technologies (MMT) performed this work in compliance with [49CFR192.607]. MMT’s proprietary equipment and test procedures were able to predict pipeline yield strength, ultimate tensile strength, base metal chemical composition characteristics, and pipeline hardness to show material ductility. The technologies also gathered hardness data across the long seam weld to classify the pipe seam weld type. MMT was validated within the industry and selected based on the results of PRCI NDE 4-8 report (Catalog No. PR-335-173816). The destructive test method data attained from SMUD’s original heat analysis, further confirmed the predicted values MMT acquired for each material grade that was investigated at each site. MMT’s predicted test results were found to be conclusive, aligning closely with SMUD’s original pipeline Material Test Reports (MTR’s). This NDT method has further validated SMUD’s original pipe material records and should be considered by pipeline operators that are looking for a proven technology and test method to help confirm pipe populations that do not have TVC records.
80. New Repair Technology – the Path to Field Deployment
Shawn Laughlin
Pipe Spring LLC, The Woodlands, USA
Abstract
Pipe Spring™ technology utilizes the well know material properties of steel with the installation methods and techniques associated with various composite repair products. Thin layer steel is utilized to wrap around the pipe and secured via modern toughened adhesive to fabricate a non-welded steel sleeve. This method removes the long -standing concerns regarding the vast material property differences between steel and various composite architectures and constituent components. It also eliminates welding. This paper will address US DOT, PHMSA regulatory requirements of repair methods. The paper will provide a brief review of the full-scale validation testing completed following ASME PCC-2 guidance. MFL based ILI inspection of the sleeve is reviewed. Data from two ILI service providers will be reviewed. This paper discusses field crews, installation methods and the training and documentation required to satisfy Operator Qualification (OQ) requirements. The simplicity and facility of installations is discussed based on actual operator training efforts.
Key Words: Emerging issues/technology. Repairs and Rehabilitation
79. Composite Repairs Evaluation for Axial and Bending Loads to Simulate Girth Welds Under Risk of a Geohazard Event
Omar Ramirez, Casey Whalen
CSNRI, Houston, USA
Abstract
Pipelines are exposed to environmental induced damage due to corrosion, erosion, and potential Geohazard activities that include earthquakes, floods, landslides, and any other geological or hydrological disasters. These activities could threaten a pipeline’s structural integrity. This paper will focus on geohazard risks as the consequences and risks are generally higher and more immediate than that of wall-loss type defects.
Repair of damaged pipelines has traditionally been accomplished using welded repairs, where a patch material is attached to the substrate over the damage. During the past twenty years, composite materials used to repair damaged pipelines have experienced a considerable increase as these repairs have become more cost effective, efficient, and reliable due to extensive testing.
This paper will focus on describing a test program to evaluate the performance of a composite repair under bending or axial loads to simulate the impact of a potential Geohazard. These repaired specimens will be tested in different configurations of installation pressure, internal pressure cycling and axial force cycling. On this test program, a composite repair was installed on 12-in pipe where an internal local notch (50% deep and 6” on the hoop direction) was installed at the weld to simulate lack of fusion or represent a poor quality weld. Testing results show that a composite repair is capable of considerably reducing strains at the weld and increasing the axial and bending load capacity of the carrier pipe.
Keywords: Composite Repair, Geohazards
78. Use of Mobile Fleet of Leak Detection Devices to Mitigate Risk During Pipeline Repair Program
Adrian Banica1, Steve Edmondson1, Tim Edward2
1Direct-C, Edmonton, Canada, 2Onebridge, Edmonton, Canada
Abstract
New IoT standalone leak detection systems can be rapidly deployed to cover potential leaks, however covering an entire pipeline is cost prohibitive so a method for selecting the locations for deployment is required.
This paper examines how data science & machine learning software combined with environmental assessments can lead to deployment of targeted leak monitoring devices that employ nanotechnolgy based coatings to optimize a pipeline repair program.
When a risk is noted on a pipeline, currently there is little recourse between doing an expensive direct assessment on that location; or letting that location remain unmonitored until resources exist to examine it. New IoT targeted leak detection technology allows an economical middle ground where many risk locations can be monitored for minute traces of signs of a leak, all at a fraction of the price of a direct assessment. With such timely alerting of a leak, the consequences at that site can be greatly reduced. These leak detectors only work in a very localized area and depend on areas of concern being accurately identified. It is modern, advanced ILI alignment and integrity analysis software that provides this key risk placement data.
This leak detection technology uses smart coatings to detect Hydrocarbons, it runs 24/7 and uses alarm-based algorithms to alert to the presence of leaks. It can be rapidly installed in targeted locations that are identified by algorithms as being needed to be repaired and then moved to new locations as those identified defects are repaired.
This paper describes how a fleet of leased mobile leak detection systems were deployed over several months along a pipeline which covered several US States. The units were deployed in High-risk areas that had been identified as needing repair. At the completion of the repair program most of the leased leak detection systems were returned. Feedback from the operator will be included in the presentation.
77. Leveraging Multiple ILIs and Technologies to Identify Possible Integrity Threats Under Type A Sleeves
Michael Plishka1, Kelsey Hooten1, Jason Williams1, Matthew Lewis2
1Colonial Pipeline Company, 2Quest Integrity
Abstract
On August 14, 2020, a leak was discovered on Colonial Pipeline Company’s (Colonial) Line 1 pipeline in Huntersville, North Carolina. The release occurred at a dent, previously repaired with a Type A sleeve. Upon further investigation, it was found that external metal loss and a through-wall crack had developed in the dent sometime after the installation of the Type A sleeve. Type A sleeves are a common remediation method used to reinforce and repair certain anomalies on a pipeline. However, because the sleeve ends are not welded to the carrier pipe, Type A sleeves are not pressure-containing. A remediation plan to identify possible integrity threats under Type A sleeves and convert those Type A sleeves to pressure-containing Type B sleeves on Colonial’s mainlines was implemented.
In close conjunction, Colonial and Quest Integrity developed a plan to first identify every sleeve on Colonial’s mainlines. Once the comprehensive sleeve list was compiled, a qualitative analysis of all sleeve locations was initiated. Utilizing multiple inline inspections (ILI) and tool technologies, such as Ultrasonic Wall Measurement (UT-WM), Ultrasonic Crack Detection (UT-CD), and Combo (MFL + Caliper), each sleeve location was reviewed to determine:
Results from the sleeve review were used to provide a prioritization of the Type A to Type B conversions.
This paper uses case studies from this sleeve characterization and review project to show:
76. Comparing Laser Scans Against In-Line Inspections and Quantifying Bias for Assessment Methods
Sayan Pipatpan, Andreas Pfanger
NDT Global, Stutensee, Germany
Abstract
Ultrasonic technologies have been part of the portfolio of in-line inspection (ILI) vendors for decades, but many operators rely on magnetic flux leakage (MFL) technology when it comes to metal loss corrosion.
This case study is based on a 28” pipeline with external metal loss which was inspected using a MFL tool and – 5 years later – ultrasonic wall thickness measurement (UTWM) tool. This was followed by laser scans at 7 different sites which detected mostly pinholes and pitting corrosion. The number of verified anomalies allowed a statistical analysis of sizing deviations between ILI and field verifications. While most verifications happened after the UTWM inspection, a subset was completed shortly after the MFL inspection.
Detailed side-by-side comparisons between UTWM and the laser scans further illustrated the level of detail offered by direct measurement techniques. They provided in-depth insights on their advantages and limitations, as well as the influence of clustering strategies on length and width sizing accuracy.
Additional assessments in this pipeline led to the investigation of potential bias influencing the corrosion growth estimates. Utilizing subsets of features where no growth was expected, and by integrating the results from laser scans, this bias was quantified.
KEYWORDS FOR SUBJECT AREA: ultrasonic tools, magnetic flux leakage, metal loss corrosion, correlation, verification
75. Dig Data Warehouse to Enable ILI Continuous Improvement
Nathan Verity, Hong Sang, Pu Gong
Onstream Pipeline Inspection Services Inc., Calgary, Canada
Abstract
In order to improve various facets of the ILI product cycle, including sizing accuracy, anomaly or feature identification, and repeatability of inspections a dig data warehouse is needed. Traditionally different vendors and operators have internal formats for this data which can be difficult to use in validating and comparing results across multiple inspections.
To be effective and enable future research, the breadth of data captured in the warehouse, is formatted in a standard format, includes raw inspection data, pipeline metadata, analysis results, and dig measurements including raw laser scan data. The increased in the confidence of ditch measurement enables better trend analysis and adjustment of ILI sizing models. New data signals can also be compared to signals in the warehouse to help identify and classify against verified signals reducing any analysis bias.
This paper will describe the methodology for capturing and utilizing this data to both close the loop of the ILI continuous improvement cycle and provide feedback to customers on the ILI tool performance in the field.
74. Proof of Performance: Flow-Loop-Testing Validation of UHR MFL Technology in the POD, POI and Sizing of Pinholes
James Lavender
Entegra, Houston, USA
Abstract
A major liquid pipeline operator with assets throughout Texas and the Midwestern United States recently engaged us in a blind flow loop test to compare the pinhole detection, characterization, and sizing capabilities of Ultra-High Resolution (UHR) Magnetic Flux Leakage (MFL) vs. their legacy state-of-the-art Ultrasonic In-Line Inspection (ILI) results.
Testing was carried out at PRCI’s Technology Development Center in Houston, Texas. This paper will discuss how the latest advancements in MFL technology impact true pinhole assessment and will present the flow loop test setup, execution and results.
73. Tool Tolerances in MFL In-line Inspection and Why They’re Needed
Kenneth Maxfield1, Mark Briell2
1KMAX Inspection, Millcreek, USA. 2KMAX Inspection, Toronto, Canada
Abstract
While the principle of magnetic flux leakage is relatively simple, it’s application in in-line inspection of carbon steel pipe is far more complex. MFL system design and analysis encompass complex interactions between the magnetic field and flux leakage produced by defects in the pipe wall, making signal identification & interpretation difficult. Thus, the need for tool tolerances.
This paper discusses the cause and effect of wide-ranging factors which influence the reported depths & dimensions of MFL In-line Inspection data. Including,
72. Application of Advanced Data Analytics to Improve Metal Loss Tolerance Specifications
Geoff Hurd¹, Keila Caridad², Scott Miller¹, Melissa Gurney¹, Samaneh Sadeghi¹, Aaron Schartner², Vincent Tse²
¹Baker Hughes, Calgary, Canada, ²TC Energy, Calgary, Canada
Abstract
In recent years there has been greater and greater desire to reduce pipeline maintenance costs through improvements to the effectiveness and efficiency of integrity management programs. Extracting as much information out of data obtained through each In-line Inspection (ILI) to better understand sizing tolerance performance and accuracy is an area of key interest as it has direct impact on repair decisions. Today, higher data volumes captured through multiple sensing techniques are being collected by ILI tools than ever before and the interpreted results are established as one of the most effective assessment techniques for managing pipeline safety.
In addition to this improved condition assessment data, validation programs are generating exponentially increasing volumes of now highly reliable and accurate truth data. This essential combination of high-quality inspection and validation data provides the opportunity to re-think how we establish performance specifications for the different ILI technologies. Traditional methods of utilizing relatively low volumes of isolated artificial defects that attempt to represent defects expected to be found can be replaced with vast ranges of actual real-world defects. Extensive “Big Data” libraries of high-resolution field measurements married to raw signal data captured by the tools provides new and exciting opportunities for innovative improvements that can be made to the detection, characterization and sizing of pipeline anomalies.
This paper will present a machine learned technique applied to vast quantities of dig and tool data to improve metal loss (corrosion) sizing tolerance performance. This method goes beyond the common industry practice to divide metal loss into a small number of categories based on arbitrary discrete defect length and width to include a much wider range of factors that truly affect Magnetic Flux Leakage (MFL) metal loss sizing to predict an individual defect-by-defect tolerance. This provides a more precise prediction of metal loss tolerances that reduces the general conservatism that has been built into existing tolerance specifications over the years while maintaining the necessary conservatism when needed to ensure pipeline safety. This paper will also present examples of the specific benefits operators may realize utilizing these newly predicted tolerance specifications.
71. Integrity Planning Utilizing In-Line Inspection Data
Brian Dew, Amin Eshraghi, Evelyn Rawlick
Acuren, Calgary, Canada
Abstract
Three in-line inspection (ILI) runs were done on a 10-inch Grade X52 sour gas pipeline which was constructed in 2009. There was suspected oxygen ingress early in the operating life of the pipeline and uninhibited methanol was regularly used in the pipeline. The ILIs were completed in 2010, 2015, and 2020. The first run identified 789 internal metal loss features with the deepest feature being 41% of wall thickness deep. The second run identified 1917 internal metal loss features with the deepest feature being 55% of wall thickness deep. The third run identified 3812 internal metal loss features and 494 cluster anomalies and reported the deepest metal loss feature to be 80% of wall thickness deep.
Probability of Exceedance (POE) analysis was utilized to assess the 2020 ILI data due to the significant degradation being found in the pipeline. The work presented in this paper utilized the ILI and subsequent integrity dig data to further support the POE analysis. Upon receipt of 2020 ILI data, the internal corrosion features were characterized, first, and the burst pressure for each feature was calculated. Based on the calculated burst pressure, it was recommended that the pipeline maximum operating pressure (MOP) be lowered from the original 9,930 kPa to 5,500 kPa to reduce the number of required immediate repairs. Next, a POE analysis was conducted using the calculated unmitigated corrosion rate and the recommended reduced MOP. Features which exceeded the specified POE threshold from Year 0 to Year 5 were identified and integrity digs for the identified joints were prioritized and recommended to the pipeline operator.
After completion of the integrity digs and direct inspection of the pipe, the 2020 ILI run was regraded, and the POE analysis was updated. Additional findings from the inspection associated with blisters and cracking were addressed and added into the integrity program along with the POE assessment.
This paper provides details of the ILI data analysis, corrosion rate calculation, and the methodology used to prioritize the integrity digs. In addition, the incorporation of integrity dig data into refining the future integrity program and updating the POE assessment is discussed.
70. Determining Active vs Passive Internal Corrosion using Data Science
Yevgeniy Petrov1, Megan Scudder1
1OneBridge Solutions, Boise, USA
Abstract
Integrity engineers struggle with determining active vs passive internal corrosion, specifically on legacy pipelines with a history of internal corrosion. ILI tools typically under-call internal metal loss anomalies and each ILI tool vendor has different pitting algorithms. This can create issues when attempting to compare run to run data. There may be a mix of over- and under-called anomalies throughout the entire population that when compared on a system level, can create a false narrative that the corrosion is not active or severe.
This research considers two methods that address this problem: specific identification of newly-replaced pipe and an analysis of the distribution of localized pit-to-pit anomaly growth values. Pipe sections that have been replaced between ILI runs essentially act as large coupons, providing valuable data about the active growth of internal corrosion. The second model uses a localized corrosion growth score based on the mean, standard deviation and skewness of the distribution of individual pit-to-pit anomaly growth measurements. Constituent anomalies for the growth distributions are accumulated in sections spanning roughly 500 feet, designed to be sensitive to local corrosion conditions. Using this approach, will reduce the influence of tool bias and provide operators with a ranking system based on a calculated growth score to understand where they have a high density of active internal corrosion and where severe internal corrosion is occurring.
69. Optimizing a Reassessment Plan with Probabilistic Monte Carlo Analysis: A Summary of Recent Developments to Better Support Operational Decision-Making
Michael Turnquist1, Ted Anderson2, Miguel Martinez1
1Quest Integrity, Boulder, CO, USA. 2TL Anderson Consulting, Cape Coral, FL, USA
Abstract
The economic conditions surrounding the oil and gas industry are in a permanent state of flux. Pipeline operators constantly need to evaluate different options for managing their assets to achieve the greatest potential commercial benefit without sacrificing safety and reliability. Seam weld integrity continues to be one of the most challenging threats for pipeline operators to manage. The continued improvement of crack-detection ILI technology provides operators with more options for reassessment, as it may be more prudent to deploy this technology for assets that have been previously managed with hydrotesting only.
The probabilistic analysis methodology discussed in this paper focuses on the management of crack-like features in the pipeline longitudinal seam weld. TL Anderson Consulting and Quest Integrity have developed an industry-leading probabilistic model to assess the seam weld integrity threat (this model has been presented at multiple past PPIM conferences and other industry events). This paper will present an overview of recent improvements to the model which will enable operators to identify an optimal reassessment plan. These recent improvements will provide pipeline operators with direct answers to the following questions:
The probabilistic analysis methodology presented in this paper will quantify the probability of failure over time associated with multiple future hydrotest and ILI scenarios. Specifically with regards to ILI, this analysis methodology will identify the expected number of required repairs following the inspection and the corresponding reinspection interval in order to maintain an acceptable level of reliability. This information is critical for pipeline operators to decide whether to move forward with ILI or hydrotesting as the primary strategy for reassessment.
68. Failure Analyses and Consequent Mitigation: Case Studies
Ming Gao, Ravi Krishnamurthy
Blade Energy Partners, Houston, USA
Abstract
It is well established that pipelines have the fewest fatalities of any of the various modes of transportation. Failures do occur, however, for a variety of reasons. In this paper, cases of failure due to SCC, weld defects and hydrogen-assisted cracking are analyzed with interdisciplinary approach that combines metallography/fractography, environmental chemistry, fracture mechanics and hydrostatic/ILI based assessment to identify root cause of the failures. Lessons learned from each of the cases analyzed serve as a basis for development of improved integrity management plan for prevention and will be presented in the paper.
For illustration, analysis of an onshore natural gas pipeline that failed recently in South America is shown here. Fractographic analysis with high-resolution matting fracture surface technique identified hydrogen assisted cracking is the mechanism for the failure while the source of hydrogen was driven by cathodic protection operated at near − 1200 mV CSE. Microstructural analysis showed no hard spots associated with the failure. API 579 FAD Level-3 tearing instability analysis confirmed that critical crack size was 90% deep x73 mm long that is consistent with macro-fractographic analysis based on chevron marks and the failure pressure. From the lesson learned, improvement of the distribution and control of the cathodic protection current is critical to avoid high generation of hydrogen at sites where the coating is broken or has faults
67. A Case Study of Crack Diagnosis in Natural Gas Liquid Pipelines
Nathan Leslie1, Andreina Guedez1, Sayan Pipatpan2
1NDT-Global, Houston, USA. 2NDT-Global, Stutensee, Germany
Abstract
Natural Gas Liquids (NGL) are a group of hydrocarbons that are a biproduct of natural gas processing and refining including ethane, propane, normal butane, isobutane, and pentanes plus also known as natural gasoline. As the infrastructure to aid in the exportation for NGL’s have grown so have the requirements to safeguard the assets that are used to transport these liquids by utilizing in-line inspection technologies.
This case study will focus on the deployment of an ultrasonic in-line inspection technology in an NGL Line as well as comparison of crack data analysis from the tool and NDE data from field verifications. The service was deployed for a north American customer to diagnose the potential for hook cracks in their 154 mile, 18” pipeline.
The main challenge that had to be overcome was configuring the service to properly diagnose potential cracks in the pipeline given that the medium for this inspection differed significantly from typical liquid inspection mediums regarding sound velocity and attenuation.
Results from data analysis from the ILI service showed accurate detection and identification of crack like features and were validated with NDE phased array UT measurements which characterized these complex crack geometries.
66. CVN or CTOD for Pipeline Fracture Mechanics? An Overview of Advantages and Disadvantages
Jonathan Brewer, Colton Sheets
Stress Engineering Services, Inc., Houston, USA
Abstract
The longitudinal seam weld fracture toughness of 36-inch OD x 0.406-inch WT, Gr. X52 pipe was evaluated using both Charpy V-notch (CVN) and Crack Tip Opening Displacement (CTOD) testing. Both testing results were converted to the fracture toughness parameter, K, using the methodology outlined in API 579-1/ASME FFS-1 Annex 9F. The correlations between fracture toughness and CVN data results in a large range of toughness values. However, the correlation between fracture toughness and CTOD data results in a single toughness value. This paper describes the fracture toughness calculations and how these results are implemented for pipeline fracture mechanics analyses. This is relevant to engineers and managers as it shows the technical differences between completing CVN vs. CTOD testing for pipeline integrity management assessments.
65. Automated Methods to Estimate Transition Temperature, Upper Shelf Energy, and Uncertainty from Charpy V-Notch Data
Nathan Switzner2, Michael Rosenfeld2, Peter Martin2, Peter Veloo3, Brian Patrick3, Lanya Ahmed1, Joel Anderson4
1American University of Iraq, Sulaimani, Sulaymaniyah, Iraq. 2RSI -Pipeline Solutions, New Albany, USA. 3Pacific Gas and Electric, San Ramon, USA. 4RSI -Pipeline Solutions, Oklahoma City, USA
Abstract
Pipeline feature toughness is a critical input for fitness for service assessments and MAOP reconfirmation based on the ECA approach. For these applications, toughness has historically been estimated from laboratory Charpy V-Notch (CVN) testing via the Upper Shelf Energy (USE) and 85% Shear Appearance (ductile to brittle) Transition Temperature (SATT). Two approaches are widely accepted for estimation of the USE and SATT from a set of CVN tests performed over a range of temperatures: (1) curve fitting a hyperbolic tangent to the experimental data, and (2) analytical solution of a system of empirical equations.
From a practical perspective, the unconstrained curve fitting method (1) is only accurate when the test data span a sufficient range of temperatures to sample both the lower and upper shelves and contain multiple points in the transition region. Additionally curve fitting is a manual, time-consuming procedure with poor repeatability.
Because of these challenges, pipeline operators often use the analytical solution method (2) that was originally proposed by Rosenfeld (Oil and Gas Journal, 1997) and later implemented in API-579 9F.2.2. However, this approach uses assumptions that can lead to over- or under-conservative estimates of toughness. Additionally, the uncertainty associated with the solution has not been quantified. As a result, both approaches often require the pipeline operator to accept unknown and potentially significant uncertainty in their toughness estimates.
This paper will provide a consistent and repeatable method to estimate the ductile to brittle transition temperature and upper shelf energy for CVN data that is applicable to any pipeline regardless of vintage. The method utilizes the hyperbolic tangent approach by applying several simplifying assumptions to effectively constrain the curve fitting to a physically meaningful range without compromising the accuracy of the solution. It will be shown that this approach increases the accuracy and reliability of the calculated values for incomplete datasets. We will identify the physical meaning of the assumptions and show how to estimate the uncertainty such that conservatism can be maintained for subsequent calculations compared to other methods.
64. Measuring Toughness with Instrumented Indentation Methods: Fact or Fiction?
Ted L Anderson
TL Anderson Consulting, Cape Coral, USA
Abstract
There is a strong desire among pipeline operators to quantify material properties with nondestructive in-ditch measurements. In addition to operators’ obvious motivation to maintain pipeline integrity and to avoid releases, PHMSA’s new Mega Rule for vintage gas lines imposes regulatory pressure to characterize pipe properties. Performing destructive material testing on cut-outs is an effective but very expensive option. Consequently, the prospect of nondestructive in-ditch material testing is extremely attractive.
A number of vendors offer in-ditch technology to infer yield and tensile strength. One such technology entails pressing a small spherical indenter into exposed steel on the OD of a pipe joint. This technique resembles a conventional hardness test, except that these modern indentation devices are instrumented to measure the force versus deflection response.
While instrumented indentation methods are certainly capable of measuring the strength properties of steel, some vendors have claimed that this technology can also measure material toughness. The present paper examines this claim in detail.
The author invokes basic metallurgical principles to argue that it is simply impossible for an indentation test to “measure” fracture toughness. The plastic flow properties of steel are weakly related to fracture properties. That is, two steels with identical strength properties can have very different toughness properties. The indentation test cannot distinguish between two such steels. This paper includes experimental benchmarks that demonstrate the lack of correlation between tensile properties and fracture toughness.
63. From One to Many – Composite Repair of SCC
David Futch1, Casey Whalen2, Sean Moran3
1ADV Integrity, Waller, USA, 2CSNRI, Houston, USA, 3Williams, Salt Lake City, USA
Abstract
Composite repairs have been traditionally utilized as a means to repair features identified on pipeline systems including corrosion and dents. Recently, several industry-based studies have been performed to investigate the repair of longitudinal cracks and crack-like features. These studies demonstrated the ability to reinforce crack and crack-like indications, however, were reinforced with overdesigned repair thicknesses and only repaired a singular approximately 3-inch-long crack. While this is conservative, additional layers increase cost and complexity of the repair.
This paper summarizes a two-phase program utilizing pipe containing field-identified colonies of stress corrosion cracking. Phase 1 of the testing program utilized nominal 30-inch OD x 0.325-inch WT, API 5L, Grade X52 pipe material and Phase 2 of the testing program utilized nominal 10-inch OD x 0.188-inch WT, API 5L, Grade X52 material.
Varying repair thicknesses were installed to further investigate the ability of a carbon fiber composite repair system to reinforce SCC indications of varying lengths and depths. Additionally, one sample during both testing phases was repaired while under pressure. To accomplish a comparison between samples, several criteria were compared: the ability to survive full-scale pressure cycling and subsequent burst test, a reduction in strain measured across repaired crack-like indications, and any subsequent growth identified after completion of the full-scale tests.
9. Damage Prevention 2.0 : Analysis of operational data from an automated ROW airborne visual inspection of seven pipelines: crude oil leak detection, 3rd party encroachment detection and advanced image documentation.
Eric Bergeron1, Alexandre Thibeault1, Ray Philipenko2
1Flyscan Systems Inc., Quebec, Canada. 2Enbridge Pipelines, Edmonton, Canada
Abstract
For years, pipeline operators have relied on human observers flying at low altitude to perform the mandated visual inspections of their right-of-way (ROW), often completed in single pilot-observer configuration, without any automatic documentation or detection system. This paper presents the first real-life results of a test campaign performed by Flyscan Systems over ROW’s of seven operators in seven US states and two Canadian provinces. Capabilities developed by Flyscan in collaboration with Enbridge include real-time hyperspectral leak detection and location and reporting of threats in the right-of-way. The paper will discuss the technology and system capabilities with details outlining detection of unauthorized 3rd party activity (machinery, abnormal construction activities), as well as generation of high definition 2D orthomosaics and 3D point cloud, vegetation analysis and digital surface ground mapping of the entire length of a 500-meter-wide ROW.
The paper will also review how new technologies can provide operators with a complementary tool that provides consistent, repeatable, and automated detection of high-priority threats to the integrity of pipelines. Statistics on detection performance will be presented, including unplanned threats and simulated (hidden) leaks. Real-life operational results will be covered including latency in detection, volume of data to be manipulated, cloud computing aspects as well as operational “up time” that can be expected. A development roadmap will be reviewed illustrating the path to fully automating all functions performed by human observers, including detection of ground movement, riverbank erosion, marker counting and localisation, exposure of pipelines after serious weather events, and automation of class location determination.
2. Evaluating the Suitability of the US Pipeline Network for Hydrogen service
Simon Slater1, Neil Gallon2, Ryan Sager3, Richard Ingolia3, Sebastiaan Schuite3
1ROSEN, Columbus, USA, 2ROSEN, Newcastle upon Tyne, UK, 3ROSEN, Houston, USA
Abstract
In response to the move towards net-zero carbon emissions, operators in the US are considering if and how existing natural gas pipelines can be converted to blended or 100% hydrogen service. Particularly given the cost of, and public opposition to, new pipelines.
This change will bring new challenges in terms of integrity management and at a minimum require a re-evaluation of the way the pipelines are operated. Building new pipelines specifically for hydrogen transportation can clearly mitigate the risk, but it may not be necessary. European operators are envisaging that ~60% of their European Hydrogen Backbone will consist of repurposed pipelines. When considering which pipelines are suitable for repurposing, the first reaction may be to dismiss the use of vintage pipelines, which are assumed to have inferior material properties compared with modern pipelines, and thus increased susceptibility to issues of embrittlement and accelerated fatigue crack growth, and hence higher risk. This may be unduly pessimistic, and we first need to consider the condition of existing lines.
A long history of pipeline inspection means that ROSEN has a significant database, which provides an indicative picture of both the material properties and condition of the US pipeline networks. In this paper some of the questions raised regarding the suitability of the pipeline network for hydrogen service in relation to existing knowledge and code guidance are explored. Specifically, we investigate the extent of existing features, such as crack-like features, dents, hard spots, and significant corrosion that could be a concern in hydrogen service under various scenarios of operating pressures and pressure cycling. In addition, we review the range of material properties and attributes present in the current natural gas transmission system, and how these compare with guidance in standards for hydrogen pipelines and developing industry knowledge.
Finally, we consider how pipeline condition and properties may influence integrity management in the presence of hydrogen. In some cases, converting these vintage lines to hydrogen may offer an opportunity to meet the existing guidelines for conversion and establish a safe operating envelope for hydrogen transportation, without the need for new-build. This paper will discuss the pro’s and con’s for the industry in terms of integrity management of converting existing pipelines to blended or 100% hydrogen service and a best practice approach for selecting candidate pipelines.
38. Variability and Mitigative Measures for Estimating Yield Strength in Line Pipe by Instrumented Indentation Testing
Peter Martin1, Jeffrey Kornuta2, Emily Brady2, Nathan Switzner1, Jonathan Gibbs3, Peter Veloo3
1RSI, New Albany, USA. 2Exponent, Houston, USA. 3Pacific gas and Electric, Walnut Creek, USA
Abstract
Natural gas pipeline operators in the United States are increasingly implementing materials verification programs (MVP) to validate the properties of pipelines that lack reliable records. These programs rely on nondestructive testing (NDT) methods, such as Instrumented Indentation Testing (IIT), to estimate the mechanical properties of pipeline steels in situ. The NDT approach is attractive because it does not require material to be cut from the pipe, as does traditional mechanical/tensile testing. However, IIT and other NDT methods infer the bulk mechanical properties from a relatively thin surface layer, and extrapolation to through-wall properties can introduce errors due to factors including material inhomogeneity and residual stresses from manufacturing. This work will consider the variability in the IIT yield strength from seven line pipes tested in multiple locations by two different vendors. It will be shown that while the measured IIT yield strength is often within ±10% of the tensile test result, some results can exceed this range. Furthermore, it will be shown that the yield strength estimated by IIT can vary by as much as 20% based on both the axial and circumferential location on the pipe. Sources of this variation, including the effects of sampling depth, will be discussed with consideration of residual stress, decarburization, and alloying variability. Recommendations will be made for best practices to identify and mitigate measurement uncertainty related to these effects.
48. Development of a Multi-Diameter and Low-pressure Compatible Tool to Inspect for Selective Seam Weld Corrosion
John Nonemaker1, Lance Wethey1, Colin Bradley2, Mustafa Jamaly2, Susanna Kaumeyer 2, Kirk Strachan2
1ROSEN, Houston, USA. 2Enbridge, Houston, USA
Abstract
Enbridge operates a low-pressure multi-diameter natural gas pipeline in the Northeast United States that is susceptible to selective seam weld corrosion (SSWC). The diameter ranges from NPS 24” to NPS 30” with 15 diameter changes over a length of 13.0 miles. SSWC is an environmentally assisted mechanism in which there is increased degree of metal loss in the longitudinal weld in comparison to the surrounding pipe body. Rosen’s RoCorr MFL-C Ultra technology was selected to obtain inspection data in a single in-line inspection for metal loss and long seam features. The multi-diameter and low-pressure operating characteristics of the pipeline presents in-line inspection challenges such as stuck tools, speed excursions and degraded data, particularly when the tool encounters bends and fittings. This paper presents a systematic approach for developing an appropriate in-line inspection tool from the perspective of a natural gas pipeline operator and in-line inspection technology provider, including a description of the in-line inspection execution considerations, in-line inspection tool design and testing process, tool features to mitigated degraded data and field validation results. This case study demonstrates that tool developments for low-pressure and multi-diameter pipelines should be considered as a long-term integrity management strategy.
46. Making hard decisions
Simon Slater1, Khanh Tran1, Jason Edwards1, Ann Reo2, Sean Moran2, David Futch3
1ROSEN, Columbus, USA. 2Williams, Tulsa, USA. 3ADV Integrity, Magnolia, USA
Abstract
The definition of a hard spot is introduced in the updated Gas Rule 49 CFR 192 Part 2 as “an area on steel pipe material with a minimum dimension greater than two inches (50.8 mm) in any direction and hardness greater than or equal to Rockwell 35 HRC (Brinell 327 HB or Vickers 345 HV10)”. This update sets an expectation for operators to manage the threat through a combination of assessment, using ILI and in-ditch validation, and an appropriate response.
Over the past two years, Williams Transco has utilized in-line inspection technology capable of detecting, identifying and characterizing hard spots on several transmission pipeline systems. Various types of reported material hardness anomalies have been subsequently verified in a validation campaign, of which a number occurred on not only flash welded A.O. Smith pipes, but also vintage DSAW pipes from a wide range of manufacturers.
This paper will present the results of extensive non-destructive and destructive testing of validated material hardness anomalies, to establish a thorough understanding of the different types of hard spots that can exist, and discuss recommendations for assessing these anomalies and defining appropriate response options.
15. Preventing Product Releases into Coastal Waterways and Ship Channels
Joseph Lamberth
Quest Integrity, Stafford, USA
Abstract
Pipeline failures in today’s social, environmental, political, and global sustainability climate have a consequential impact on pipeline operators and owners. These consequences are exponentially higher when the hydrocarbon release takes place near, over or into coastal waterways, ship channels and oceans.
Even so, regulatory pressure and compliant stewardship lags the onshore transmission pipeline industry and related Integrity Management Programs (IMP’s). The financial impact and ramifications to shareholder value for spills over the past couple of decades have impacted the safety and health of neighboring communities and wildlife and ultimately cost operators billions in fines, legal costs, and the negative impacts to brand equity and sustainability goals. High consequence assets require direct measurements that cover the entire pipe surfaces to help ensure the fitness for service and flow assurance necessary to support their critical yet intermittent operation.
This presentation will highlight how a Northeastern Pipeline Company with wharf line operations is taking this threat seriously by using built-for-purpose ultrasonic inline inspection technology, seldom needing line modifications, to assess the integrity and fitness for service of their wharf line piping network. This approach enabled the company to optimize capacity by safely maximizing throughput while also minimizing risk to environment and business continuity.
The Operator had multiple pipelines spanning several diameters servicing a wharf used to transfer fuel from the dock to the tank farm. The goal for this project was to gain confidence in the continued safe and reliable operation of these pipelines by having 100% of the piping inspected to ensure all potential integrity threats were known, and if needed, appropriate action could be taken to mitigate any significant risks identified in the assessment. To accomplish this, the Operator utilized ultrasonic inline inspection technology to inspect the lines for both wall loss and deformation in a single pass.
Additional reasons to those above for selecting this technology included the need for a bi-directional tool capable of negotiating tight bends that posed the least risk for getting lodged during operations, while collecting direct, accurate measurements of anomalies across the entire pipeline. The end result was a successful execution on the first mobilization, preliminary and final reporting were delivered in an expeditious manner to help ensure safe continued operations.
By nature, inspection of dock side pipelines requires different planning and support than onshore pipelines. This paper will elaborate on such a process and how the efficiency and ease of a well-planned project can impact future operations by reducing risk, ensuring the safe and reliable service of critical energy infrastructure.
66. Fatigue Testing (Small and Full Scale) Validation of SCC Recoating
Ryan Milligan1, Ming Gao1, Ravi Krishnamurthy1, Richard Kania2, Elvis Sanjuan2
1Blade Energy Partners, Houston, USA. 2TC Energy, Calgary, Canada
Abstract
For gas pipelines it is important to identify SCC colonies that can be recoated without grinding and operate for another 50+ years. One of the key elements of this study was the small scale and full-scale fatigue testing of SCC colonies for validation. The focus of this paper is on the testing methodology and results.
The fatigue testing was conducted in the base metal, weld and HAZ. Small scale testing was first utilized to establish the baseline behavior along with J-R data. The full-scale testing was conducted in pre-existing SCC colonies in the base metal and utilized application of hydraulically pressurized water.
For the weld region, SCC cracks were not adjacent to the weld, consequently a crack was generated using an EDM notch. The crack growth in the full-scale ring-samples was generated using a servo-hydraulic machine. This required development of a specialized K solution using FEA.
The nature of the fatigue cracking was matched between small- and full-scale testing using SEM analysis of the fracture surface. Integrated analysis of the small scale, full scale and fractographic results validated more than 50 years of remaining fatigue life for recoated SCC cracks in gas pipelines.
53. Above and Below: A Holistic Geohazard Monitoring Solution
Daniel Bahrenburg1, Andy Young2, Jason Edwards1, Amin Singh1, John Norman3
1ROSEN, Houston, USA. 2ROSEN, Newcastle, United Kingdom. 3Teren, Lakewood, USA
Abstract
Geological and hydrological processes continuously reshape the surface of the Earth in ways that are not always predictable or easy to detect. Both cataclysmic and routine weather events are drivers of the geological and sedimentary change that ultimately result in pipeline geohazards. Operators need to consider these processes when constructing new pipelines or managing the integrity of existing assets.
Accounting for the influence of onshore or subsea land movement on structures is the primary goal of any effective geohazard management program. Traditionally, geotechnical monitoring programs are based on distributed point measurements in a defined area of ground movement. Active monitoring of ground movement and pipeline stress states is typically performed with discrete monitoring equipment, such as slope inclinometers or strain gauges. This can provide sufficient information for management of simple pipeline geometries located within basic geological environments and, most importantly, where hazards have already been identified. Frequently, hazards that result in pipeline failures are unmonitored or in areas that do not appear to be problematic, particularly where the surface expression is subtle and not identified by traditional surveillance methods.
To meet the demands placed on operators by advancing regulation and severe weather conditions, more frequent and comprehensive appraisals of pipeline right-of-way corridors will be required. For liquids transmission operators, this occurred in 2019 with 49 CFR 195.414. For gas transmission operators, this will become effective in May 2023 with 49 CFR 192.613.
This paper will demonstrate a holistic and integrated geohazard monitoring solution, which utilizes in-line inertial mapping and electromagnetic stress measurement to assess the condition of the pipeline alongside aerial laser topographical surveys (also known as light detection and ranging, or LiDAR) to evaluate the state of right-of-way at the surface. LiDAR provides invaluable insights into the characteristics of the land surface and whether there are features or anomalies that could represent land instability. Inertial mapping reveals the occurrence of discrete flexural loading and its proximity to performance limits. Additionally, recent case studies have shown the ability of new ILI technologies to accurately measure uniform longitudinal stress resulting from axial loading on pipelines. The integration of these three data collection techniques ultimately results in a high level of confidence when diagnosing and characterizing active geohazard threats.
This approach not only provides the ability to identify geohazards, but also assists with setting appropriate inspection intervals to track changes to pipeline integrity and hazard development. An additional advantage of these complementary technologies is that they provide a robust baseline for any geotechnical program and increased efficacy in the design of site surveys, the selection of monitoring points and guidance toward the most appropriate remediation solution.
40. Combining Nondestructive Techniques to Obtain Full Vintage Pipeline Asset Fracture Toughness at Both the Seam and Pipe Body
Intisar Rizwan i Haque, Bryan Feigel, Brendon Willey, Simon Bellemare, Parth Patel
MMT, Natick, USA
Abstract
For vintage transmission pipeline assets, material toughness data is often limited to laboratory testing of opportunistic pipe cutouts because, even if original Material Test Records (MTR) are available, the manufacturing specifications for the line pipe did not have fracture toughness requirements until they were added in the 1980s. Given the need to obtain Traceable, Verifiable, and Complete (TVC) material data in certain assessments and re-confirmation, nondestructive evaluations (NDE) are an attractive alternative to pipe cutouts if these solutions can be validated and accepted. Past attempts to validate indentation and frictional sliding techniques for the pipe body toughness have proved challenging. This paper summarizes recent progress in developing and validating two recent techniques based on frictional sliding. The first technique uses the Hardness, Strength, and Ductility (HSD) testing process which operates on the principle of frictional sliding over longitudinally welded seams, allowing, by a combination of surface field test and a database, to produce predictions for the Charpy V Notch (CVN) properties. A prediction of the CVN shear transition for these seams is currently validated and used for pilot projects. The second technique is a new concept that evolved from Nondestructive Toughness Testing (NDTT) using a wedge stylus to Blade Toughness Meter (BTM) which uses a significantly sharper stylus to mimic more closely the conditions at the tip of a crack. In a lab prototype phase, the BTM tester is intended to be adapted for pipe body testing as early validation studies show a stronger correlation with the laboratory toughness results in comparison to NDTT. This paper presents the recent progress and the validation status of both techniques as well as their benefit through initial case studies.
23. Innovative Pipeline Evacuation Technology for Reducing Methane Releases to the Environment During Pipeline Maintenance and Pigging Operations
Rita Hansen, Jeff Witwer, Mitch Jacobs
Onboard Dynamics, Bend, USA
Abstract
Pipeline operators are showing a growing interest in adapting new technology solutions and operating practices to reduce methane releases during pipeline operations and maintenance. This increasing attention is focused on methane capture and recovery during routine pigging operations. The number of pigging operations, and the fact that they are usually conducted on a predictable schedule, suggests that this source of methane release should be a prime target for operators seeking to improve their environmental profile.
This paper will provide an overview of technologies and operating practices that can be implemented to reduce methane releases during pigging, highlighting technology features that are most important in determining project success. The important product features that will be discussed include gas capture time, system set up time, and consideration of equipment physical size and how these factors all impact gas capture time and cost.
We have developed and will present a calculator that can be used to estimate the reduction in methane released for every launch and receive operation based on pipeline size and pressure.
22. ILI Tool Speed Control Using Gas Recompression –– Better Data / No Venting or Flaring
Adam Murray, Branden Allen
WeldFit Corporation, Houston, USA
Abstract
The purpose of in-line inspection (ILI) is to provide reliable information about pipeline integrity so operators can prioritize maintenance and repair. Typically, ILI tools are propelled through pipelines mechanically. Either they flow at the same rate as product or are moved by differential pressure, which occurs when the operator releases downstream pressure through flaring or venting.
However, both methods are limited in their ability to reliably control the speed of the ILI tool as it travels through the pipeline. Lack of speed control, that is, failing to keep the inspection tool moving at a reduced and constant speed, makes it more difficult for the tool’s sensitive sensors to pick up critical anomalies, affecting data quality. If the tool moves too quickly, it can miss defects or damage, producing inaccurate or incomplete readings. When the tool travels too slowly, it can exaggerate findings, creating a false impression of the pipeline’s wall condition. In addition, varied tool speeds make it more difficult for data analyzers to piece together information about the pipeline.
Unreliable ILI data can lead to expensive and time-consuming tool reruns or unnecessary digs. To improve data results, many ILI tool manufacturers incorporate speed control into their devices. However, this limits the vendor options for operators.
After lack of speed control during five consecutive ILI tool runs led to insufficient data each time, the nation’s largest interstate natural gas operator turned to a novel, engineered solution to controls gas flow and ILI tool speed: recompression technology.
Recompression technology is typically used to reduce methane emissions during pipeline isolation. In this case, equipment with straight-line capabilities, meaning it moves gas at a constant rate, created a constant pressure differential across the ILI tool. That enabled the tool to travel at consistent speed throughout the pipeline.
Using recompression technology, the operator collected accurate data in a single run. They also avoided flaring product, helping them achieve their environmental, social, and governance (ESG) goals.
This white paper will discuss problems related to ILI tool speed control and describe how recompression technology was used to improve ILI data collection while also eliminating nearly 100% of methane emissions.
45. Knowing the Long Seam: Essential Insights Using UHR MFL Technology
Miguel Galeana, Rick Desaulniers
Entegra, Indianapolis, USA
Abstract
Metal loss that aligns with a pipe’s long seam poses an imminent integrity threat as well as a threat to an operator’s bottom line. But the impact and potential costs of false calls – both negative and positive – can be mitigated with an integrated ILI system that combines Ultra-High Resolution MFL technology with the insight and assessment of human-experience based data analysis. In this paper, we’ll explore how the ever-growing capabilities of MFL – and the ability to extract nuanced data from it – can improve both outcomes and efficiency.
From coincidental metal loss to preferential metal loss, trim and other manufacturing anomalies, we will investigate state-of-the-art MFL technologies, including their ability to detect ERW and flash-welded pipe and size axially-oriented anomalies. Then we will show how the latest in UHR and its facilitation of DA makes all the difference when assessing pipeline integrity.
10. A Probabilistic Method to Predict Nominal Wall Thickness
Owen Oneal1, Masoud Moghtaderi-Zadeh1, Peter Veloo1, Colin Bullard1, Cameron Fisch1, Michael Fernandez2
1Pacific Gas & Electric, Oakland, USA. 2Kiefner & Associates, Inc., Sugarland, USA
Abstract
Under the PHMSA 2019 Gas Transmission Rule, Operators must opportunistically verify material properties, such as nominal wall thickness (NWT), for pipeline features lacking traceable, verifiable, and complete (TVC) records. Non-destructive examination (NDE) such as ultrasonic testing (UT) might be performed on one or more locations to measure the wall thickness. The number of measurements collected can vary by several orders of magnitude depending on the technique used, ranging from manual 12-point UT measurements to automated UT measurements which can scan the entire pipe surface generating tens of thousands of measurements. Prior to the PHMSA 2019 Gas Transmission Rule, Operators had to assess NWT following §192.109, which by design resulted in conservative outcomes. Because NWT has a first order impact on design pressure, excessive conservatism risks reducing operating capacity. This can have serious financial and operational consequences including pressure reductions and disruptions to normal operations. Operators could benefit from developing their own procedures for verifying unknown NWT using NDE under §192.607; however, they must demonstrate that the new procedures meet the special requirements for nondestructive methods and provide an equivalent or better level of safety to §192.109.
The Pacific Gas and Electric Company (PG&E) has developed a methodology, known as the Confidence Interval Method (CIM), to assess unknown NWT intended to satisfy the requirements of §192.607 by demonstrating a conservative accounting for measurement inaccuracy and uncertainty. PG&E collaborated with Kiefner and Associates, Inc. to implement CIM in a software tool. CIM uses statistics and probability theory to combine in situ wall thickness measurements, industry standards for NWT dimensions, and manufacturing tolerances encapsulated in historical editions of American Petroleum Institute Specification 5L Line Pipe. A comparison between CIM and §192.109 was performed using a validation dataset consisting of in-situ wall thickness measurements taken on pipes with TVC NWT of record. It was observed that CIM more accurately predicted the TVC NWT of record compared with §192.109. CIM addresses the uncertainty in measurement data, and when necessary, makes conservative assumptions with 95% confidence levels. The paper will also discuss how the number of measurements influences the NWT assessment by comparing results where 12-point UT and automated UT were both performed and make recommendations on the minimum number of measurements that should be collected.
29. Beyond Standard ILI Analysis – Meaningful Interaction to Look Out for Specific Threat
Dennis Vogel1, Gurwinder Nagra2, Matthew Ma2, Garrett Meijer2
1Baker Hughes, Stutensee, Germany. 2Enbridge, Edmonton, Canada
Abstract
Within the framework of the requirements defined by API 1163, close cooperation between the operator and ILI service provider is required to manage pipeline integrity. Nevertheless, many factors could contribute towards the lack of cooperation – discussion of requirements and challenges, lessons learnt, and sharing of NDE results. There is growing evidence of a willingness to share NDE results; however, this paradigm shift is not just because operators understand that the vendor always has full visibility of ILI data to support performance validation. Rather, there is also the realization that improvement processes can be stimulated in general. Furthermore, through meaningful interaction, a holistic inspection project can be achieved on a pipeline-specific basis. A case study will show how a specific pipeline threat was addressed by considering historical records beyond the standard analysis of an inspection project by utilizing additional ILI data sets (integrated analysis). This would not have been possible without close cooperation from the start of the inspection project.
24. Keeping Pigging Safely Grounded as Hydrogen Takes-Off
Neil McKnight, Mike Kirkwood
T.D. Williamson, Newcastle, UK
Abstract
16. OPEX Optimization for Unpiggable Vent Line/Low Flow Pipeline via Self-Propelling Robotic ILI Tool
Mohamed Ali Abdullah¹
¹PETRONAS, Kuala Lumpur, Malaysia
Abstract
OBJECTIVE/SCOPE
This paper is to share the development of Self-Propelling Robotic In-Line Inspection technology that PETRONAS embark as OPEX optimization for un-piggable pipeline. Lack of conventional inspection methods to inspect un-piggable pipelines such as vent pipelines without pig traps facility and low flow pipelines, has prompted PETRONAS to embark on technology development journey for Self-Propelling Robotic ILI.
METHODS/PROCEDURES
The development of the Self-Propelling Robotic In-Line technology consists enhancement of robotic tethered crawler tool to a wireless robotic tool, testing and validation using actual full scale fabrication test loop. Fabricated test loop includes horizontal and vertical section with bends of 1.5D to simulate the inspection tool travel as per actual site condition representing vent line.
The enhancement consists of wireless connection range, optimum speed and distance, movement of slippery surface which grease was applied on the vertical section and emergency extraction of inspection robot.
RESULTS/OBERVATIONS/CONCLUSIONS
Robotic ILI qualification test which was successfully met PETRONAS requirement based on full scale factory acceptance test. The test was focused and able to meet below success criteria: –
1. Robotic ILI tool able to self-propel on vertical test spool.
2. Robotic ILI tool able to move with wireless connection for the intended travel length.
3. Emergency retrieval tool procedure and mechanism in the event of faulty robotic ILI or loss of connection.
4. Sensor detection capability at POD 90% and POI 80%.
Based on the evaluated technology, Robotic ILI solution is feasible in ascertaining the un-piggable pipeline integrity and recommended solution to tackle high operational costs that upstream operators face when inspecting their pipelines using current available methods. Deployment of this technology is estimated to provide up to 30% OPEX optimization.
The technology has been evaluated to be technically ready and pilot tested PETRONAS asset which will be shared in our detail paper covering below areas:
1. Robotic ILI tool able to travel successfully total length of pipeline.
2. Detection capability at POD 90% and POI 80% for anomalies covering metal loss and girth weld anomales.
NOVEL/ADDITIVE INFORMATION
Current approach to inspect un-piggable vent or low flow pipeline is Crawler ILI type technology which propelled by umbilical cable whereby the pipeline requires to be in shutdown mode. While, inspection using Self-Propelling Robotic ILI can be applied for un-piggable pipeline i.e. low flow pipeline and vent line with short duration or no requirement of shutdown.
63. Leveraging ILI Crack Profiles
Lyndon Lamborn1, Stephan Tappert2
1Enbridge Liquids Pipelines, Edmonton, Canada. 2Baker Hughes, Stutensee, Germany
Abstract
As an ultrasonic crack in-line inspection tool probes a crack, the depth at each ‘ping’ return can be estimated from the amplitude vs depth algorithm. The result is a crack ‘profile’. Leveraging this profile as part of integrity decision-making is not a new notion, and represents a natural progression from legacy rectangular, to (current) semi-elliptical, and finally to equivalent fracture ellipse based on the profile. With technological advancements in the past decade on both the ILI and in-the-ditch crack assessment sides, sufficient data quality and quantity exist to judge whether consideration of crack UTCD ILI profiles is appropriate for integrity decision-making.
17. 192 Final Rule (RIN2) – Essential Elements and Guidelines to Perform a Dent Engineering Critical Assessment
Shanshan Wu1, Joe Bratton1, David Kemp2, Jing Wang3
1DNV, DUBLIN, USA. 2DNV, Dublin, USA. 3TC Energy, Calgary, Canada
Abstract
The Pipeline and Hazardous Materials Safety Administration (PHMSA) issued RIN2 of the Final Rule (frequently referred to as the “Mega Rule”) on August 4, 2022, which will impact the pipeline industry’s approach for the assessment of dents and other mechanical damages. The Mega Rule prescribes detailed requirements in the Code of Federal Regulations (CFR) Title 49 Part §192.712(c) for how to perform a dent engineering critical assessment (ECA).
This paper is purposing to share the understanding of the requirements from the Mega Rule when performing a dent ECA by a detailed example. The example includes the identification of other potential threats in the vicinity of a dent, dent profile comparison, dent strain assessment using the Ductile Failure Damage Indicator (DFDI) and Strain Limit Damage (SLD) methodologies, and dent fatigue assessment.
To fathom the new Mega Rule for gas operators and achieve the best compliance, guidance regarding best practices in performing a dent ECA will be provided hereby through a detailed work example. Limitations of utilizing the methodologies prescribed in Part §192.712 (c) will be discussed in conjunction with the guidance for awareness.
35. Optimizing Risk Decisions with Imperfect Data
Joel Anderson
RSI Pipeline Solutions, Oklahoma City, USA
Abstract
In any integrity management program, there are always competing alternatives for any decision. Such as dig or not to dig, replace or not to replace. If perfect information were always available, like a math problem where everything except the answer is given, risk engineers would be an unnecessary expense. The next best alternative would be an exhaustive corpus of data with frequencies of every outcome and condition combination. However, in all but the most trivial cases, these don’t exist either and the engineer is dealt partial, imperfect information where the true state of nature is uncertain. To deal with this uncertainty in everyday life people develop heuristics, mental shortcuts that allow us to process this information with the least amount of effort and time. But when the probabilities are imprecise and the data imperfect, decisions based on these shortcuts can be fraught with biases and fallacies. All decisions carry some risk that is dependent on the (uncertain) true state of nature, and the potential loss associated with a given course of action.
This paper will discuss the fundamentals of decision theory and demonstrate an innovative application of them that incorporates existing knowledge and potential consequences. This will be used to quantify the tradeoffs of competing alternatives in an pipeline integrity management program to arrive at a decision that minimizes the risk based on the state of knowledge that is available.
36. Estimating Excavation Damage (Outside Force) ‘Hit Rates’ Using Machine Learning Models Trained on In-Line Inspection Data and Geographical Information
James White, Steven Carrell, Amine Ait Si Ali, Jonny Martin, Roland Palmer-Jones
ROSEN Group, Newcastle upon Tyne, United Kingdom
Abstract
External interference damage is one of the main causes of pipeline failure reported in publicly available industry statistics, from agencies such as the United States Pipeline and Hazardous Materials Safety Administration (PHMSA). Thus, failures due to external interference are often the most significant contributors to pipeline probability of failure in risk assessments and can play a significant role in operator decisions regarding risk-control measures, for example when it comes to the installation of additional impact protection, pipeline diversion or pressure restrictions.
The probability of failure due to external interference damage can be estimated by combining the probability that damage occurs (i.e. that the pipeline is hit), the probability that the impact is sufficient to cause instant failure and the probability of degradation to failure, given that damage has occurred. Degradation to failure is assessed using industry standard engineering models (such as the limit state functions given in Annex O of CSA Z662-19). However, the key challenge is predicting where, when, and with what energy the external interference damage may happen.
The prediction of a “hit-rate,” or impact frequency, is often subjective or based on statistics which may not be applicable to the pipeline under assessment. Top-of-line (ToL) deformation damage (dents) reported by in-line inspection (ILI) are a clear indicator of past external interference, which could have been caused by third parties, contractors or the operator themselves. In a recent in-house research study ILI data and pipeline parameters from ROSEN’s Integrity Data Warehouse (IDW) – which at the time of writing contains results from over 20,000 inspections – has been combined with geographical information on population density, land use, crossings and socioeconomics, and used to train machine learning models to estimate the frequency of external interference damage (per mile-year), or ‘hit-rate’ for pipelines where the route is known but reliable statistics for ‘hit-rate’ are not available.
This paper presents the results of the study describing the extensive dataset used from a selection of pipelines in the USA, the development of the models and how they were trained and tested, and finally showing the model performance, discussing the capabilities and limitations, and implications for risk assessment studies.
37. Gas Transmission Valve Closure and Emergency Response Considerations
Keith Leewis
L&A Inc, Calgary, Canada
Abstract
This paper provides a summary of transient flow predictions from an ignited gas rupture site when closing both valves in a valve section at increasing timing intervals. The closure response time from detection of a line break to valve closure has less effect on emergency responder search and rescue initiation inside the PIR than the public may expect. The effect of various mitigations to shorten the interval will be discussed.
39. Identifying Irregular and Erroneous Chemical Composition Data from In Situ Nondestructive Testing
Janille Maragh1, Peter Martin2, Joel Anderson2 Jonathan Gibbs3, Peter Veloo3, Jeffrey Kornuta4
1Exponent, Inc., Menlo Park, CA, USA. 2RSI Pipeline Solutions LLC, New Albany, OH, USA. 3Pacific Gas and Electric Company, San Ramon, CA, USA. 4Exponent, Inc., Houston, TX, USA
Abstract
Nondestructive testing (NDT) of chemical composition is a critical component of the Pacific Gas and Electric Company’s (PG&E) materials verification program. Additionally, 49 CFR § 192.607 states that the operator must “conservatively account for measurement inaccuracy and uncertainty using reliable engineering tests and analyses.” Accurate and precise NDT composition data can be used to determine or verify certain characteristics of a pipe, for example vintage, grade, or manufacturing process. However, it has been observed that composition measurements may at times be inconsistent across various field analytical tools, possibly due to the variability of experimental, environmental, and other statistical (random) factors. Irregular or erroneous field NDT measurements are problematic because they could lead to the mischaracterization of pipe features during the materials verification process.
In this paper, we present a systematic procedure rooted in data science for the analysis of field NDT chemical composition data. First, NDT composition data for a set of pipe features are collected using field analytical techniques, such as optical emission spectroscopy (OES), laser induced breakdown spectroscopy (LIBS), X-ray fluorescence (XRF), and laboratory analysis of filings by atomic absorption (AA) and combustion. Next, the data are statistically analyzed using only the measurements in the incoming dataset and, when possible, are compared to measurements obtained for the same pipe features using other NDT composition analysis techniques. Following this analysis, the data are compared to historical composition data previously obtained for features with similar attributes—such as outer diameter (OD), seam type, and nominal wall thickness (NWT)—to identify potentially erroneous measurements. Finally, we present case studies illustrating the application of the proposed process to data obtained for pipe features at PG&E with abnormally high manganese measurements, and we demonstrate how the identification of the elevated manganese values as anomalous mitigated potential downstream challenges during the materials verification process.
41. ILI Validation Case Study: Evaluating the impact of a weld cap on a vintage ERW pipeline inspected with an ultrasonic crack detection tool
Ian Smith1, Ted Anderson2
1IDSmith Pipeline Engineering, LONDON, Canada. 2TL Anderson Consulting, Cape Coral, USA
Abstract
An ultrasonic crack detection ILI was run as part of a liquid pipeline’s integrity management program. ILI validation, using API 1163, was performed to determine the effectiveness of the ILI in detecting, identifying and sizing cracks. This case study will discuss the results of the ILI validation with specific focus on the impact of the ILI measurement errors upon the severity assessment of the cracks and different options that were used to account for the errors and maintain desired levels of conservatism.
The most common linear anomaly type in this ERW pipeline was crack like lack of fusion flaws. The pipeline had undertrimmed welds with remaining weld caps and the ILI only specified measurement in the ‘base material’ and would not reliably detect reflectors located in the weld cap. The ILI did not meet its specifications for detection, depth or length accuracy with a tendency to undersize both depth and length. The impact of the weld caps were identified as the primary cause for the errors.
The impact of under prediction of both depth and length on the burst pressure assessment was evaluated. To evaluate the impact of the field found anomalies upon the integrity of the pipeline a FEA assessment was performed using the phased array field verification results upon the most severe anomaly not identified by the ILI to account for excess conservatism in longer cracks with a complex profile. Integrity decision making was made using the context provided by the evaluations of the impact to severity assessments and not solely upon measurement accuracies.
Keywords: ILI Validation, Engineering Assessment, Integrity Management
42. Tool Performance Estimation Considering the Effect of Fixed vs Variable Slope
Thomas Dessein, Alex Fraser, Juan Rojas, Jason Skow
Integral Engineering, Edmonton, Canada
Abstract
The performance of in-line inspection (ILI) measurements is one of the primary sources of uncertainty for corrosion and crack assessments. Operators typically perform validation digs to determine how well the ILI performed at sizing features. The API Standard 1163, “In-line Inspection Systems Qualification”, defines three levels of analysis that operators use to validate the ILI sizing accuracy. The first level relies on previous experience with the ILI system and adherence to operating procedures, the second level uses validation dig data to determine if the vendor specification can be used, and the third level uses advanced statistical methods to estimate performance from validation dig data.
The recently published third edition of API 1163 provides two example methodologies to perform a level 3 analysis. Both methods make simplifying assumptions to reduce the complexity of the problem, but one of the key differences between them is that the first method assumes the slope of the best-fit line on a unity plot is fixed at 1.0. In this paper, the effect of fixing the slope at 1 to estimate tool performance is investigated and compared against a method where slope is allowed to be variable. Several realistic datasets are evaluated using both methods and the results are compared. The effect on burst pressure for representative corrosion features is also investigated for both methods.
43. Tolerance of ILI Validation Inspections, Why Is It Important, and How to Reduce It.
1, Spencer Fowler2, Daniel Torres3
1ROSEN, Newcastle, United Kingdom. 2ROSEN, houston, USA. 3ROSEN, Houston, USA
Abstract
ILI tools are supplied with a strictly controlled and validated tolerance to apply to integrity calculations in order to make safe engineering decisions. It is a requirement under API 1163 to validate the performance of the ILI tool in the ditch following an ILI campaign with field verification technicians using a range of technologies and procedures. What is the tolerance of the technique being used? And since they are manually applied and dependent on the operator, what is the tolerance associated with the technician?
In contrast to what is commonly assumed, field verifications are not absolute and there can be a significant variation between operators, technologies, and sizing techniques. It is a costly and sometimes complex operation to understand the performance of field verification technicians using a range of technologies, but an important aspect in ensuring compliance and safe operation of pipelines.
This paper discusses the attempts at understanding a universal tolerance by international codes and standards which can be used in conjunction with API 1163, and how these values can be utilized in a validation exercise of ILI tool performance. If these universal values are not suitable then we will discuss how these tolerances can be reduced and measured. We will look at a practical example of this application for inspection of thin walled ERW inspection and the implications of understanding the tolerance of the inspector on the validation process and ultimately the safety of the pipeline network.
44. A novel concept addressing material properties and loading conditions with a dynamic micro-magnetic sensor
Sebastian Huehn, Dietbert Wortelen, Werner Thale, Christian Otte
ROSEN Technology and Research Center GmbH, Lingen, Germany
Abstract
In 2013/14, an eddy current sensor in a magnetic field for material properties was introduced; together with a population approach that addresses the requirements stated in current U.S. regulations, it determines pipe grade. A novel sensor technology has been developed now, called DMPL (Dynamic Material Properties Loading), which addresses a broader range of material properties, including toughness and, additionally, the axial and circumferential stress condition of a pipeline.
The patent pending technology is a high-resolution non-harmonic micro-magnetic sensor. Essentially, micro-magnetic sensors consist of a magnet yoke, an excitation and a receiving coil to generate and record a hysteresis curve. When testing a component, the generated hysteresis curve contains information about the mechanical properties and the loading conditions of this component. Conventional micro-magnetic sensor applications are mainly used as handheld devices for static local measurements and play a reliable role in quality control of steel plates during manufacturing. To cope with such challenging conditions during in-line inspections as high tool velocities, low power consumption and sensor liftoff, the sensor technology was upgraded and adapted. Using an extensive material database for machine learning is the key factor in this multitalented concept.
This paper provides an introduction of the technology and its suitability in the areas of axial stress condition and material properties demonstrated by laboratory measurements, full-scale tests and first operational experiences. Based on these tests, which comprise a large set of test samples, a first assessment of sizing capabilities is given, and further aspects such as measuring resolution are discussed.
KEYWORD(S) FOR SUBJECT AREA
ILI applications
Stress
Strain
Loading conditions
Strength
Toughness
47. Validating Selective Seam Weld Corrosion Classification Using ILI Technology
Matthew Romney, Dane Burden, Ron Lundstrom
T.D. Williamson, Salt Lake City, USA
Abstract
Selective seam weld corrosion (SSWC) occurs when a susceptible long seam, such as low-frequency electric resistance welding (LF-ERW) manufactured prior to 1970, is subjected to an active corrosion environment. When this occurs, the seam weld corrodes more aggressively than the pipe body, resulting in a deep V-shaped groove aligned with the seam axis. An SSWC anomaly poses a greater threat to pipeline integrity, when compared to a similar volume of general corrosion crossing the long seam (CCLS), due to the aggressive corrosion depth growth rate and orientation to the primary stress.
The pipeline industry has struggled to consistently distinguish between SSWC and CCLS anomalies. In an effort to overcome this gap, T.D. Williamson (TDW) participated in a DOT project that resulted in the development of a SSWC classifier. The classifier leverages the data collected by the Multiple Dataset (MDS) platform. MDS incorporates 5 primary technologies (high-field axial magnetic flux leakage, high-field spiral/helical magnetic flux leakage, low-field axial magnetic flux leakage, high resolution geometry, high resolution mapping), overcoming gaps in each individual technology, providing a comprehensive integrity assessment. The classifier has since been used with various operators to characterize long seam corrosion anomalies.
In 2022, TDW published an industry first specification that characterized the performance of the SSWC classifier. The paper will discuss the statistical backing of the published specification, demonstrating the field data basis and validation. Examples of SSWC and non-SSWC feature classifications will be discussed.
Keywords: In-line Inspection, Corrosion, Corrosion Crossing the Long Seam, Data Science, Multiple Dataset, Magnetic Flux Leakage, Geometry, Deformation, Interacting Features, Precision & Recall, Selective Seam Weld Corrosion, CCLS, DEF, GEO, ILI, MDS, MFL, SMFL, SSWC
49. ILI Ultrasonic Shear Wave and Compression Wave Inspections Capabilities for Selective Seam Corrosion (SSC)
Rogelio Guajardo1, Debbie Wong2, Anna Rodriguez1, Diego Luna3
1NDT Global, Barcelona, Spain. 2NDT Global, Calgary, Canada. 3NDT Global, Mexico City, Mexico
Abstract
Selective seam corrosion (SSC) can be considered as a complex feature from the Ultrasonic (UT) ILI perspective. The main reason is that it is a metal loss (corrosion) which would infer that a compression wave inspection is the best technology to address it. However, because of its geometry and dimensions it does provides reflections similar to cracks, so the shear wave technology would be optimal to detect narrow corrosions.
These features being at/in the long seam can be a threat to the pipeline and need to be known to the pipeline operator so that the required actions and measurements are taken to ensure the safety of the asset.
This raises the questions: 1- Which UT technology should be used to detect these features? and 2- What are the capabilities of the UT compression wave and shear wave ILI tools in regard to selective seam corrosion (SSC)?
This paper will present the results from a systematic approach where simulations, pull tests, and NDE correlations from ILI runs were performed. As conclusions it will provide the reader a guide on:
50. One Step Ahead: the Italian Experience on Coping with Illegal Tapping
Marco Marino1
1SolAres Srl, Milan, Italy
Abstract
As widely known and reported by prestigious publications such as CONCAWE reports, the phenomenon of Illegal Tapping in Europe was – and still is, with a much lesser impact – the main cause of concern for pipeline operators, especially in the years from 2015 to 2020.
This presentation aims at providing an insight on a specific country, Italy, which experienced a very high impact over illegal tapping phenomena.
The problem today is considered, if not entirely solved, at least controlled and contained, by looking at today’s numbers related to illegal tapping events. Nevertheless, achieving this result required a process which took several years and the development of an innovative technology, which, coupled with a bold innovation plan on several organizational aspects, led to the success case shown in the presentation.
Looking back to the past, important takeaways can be grasped, most importantly the basic fact that technology alone cannot solve this problem: the reduction of illegal tapping activities/spillages was achieved by developing a multi-disciplinary approach based on technology, engineering, operations, and security.
All the premises above are coupled with the fact that illegal tapping entails the active participation of a malevolent third party, acting and evolving to overcome any implemented strategy and technology.
The past experience can – and currently is – applicable to other scenarios in other parts of the world where the phenomenon is still active or even worse, is entirely at its beginning and finds fertile soil for growth, given the current instable international situation.
51. Challenges Facing Illegal Tapping: Pipeline Protection in Brazil
Fabio Evangelho
Petrobras Transporte S.A., Rio de Janeiro, Brazil
Abstract
Illegal tapping is a global phenomenon. Sharing experiences is the key to understanding how to face and prevent this crime. In a positive way, we believe we have created in Brazil the term “Pipeline Protection” as a concept that gathers all diverse initiatives we have been exchanging with some pipeline operating companies from other countries.
We have used a multidisciplinary approach that involves: innovative control room procedures, legal issues, new technologies search, the subtle art of communication with local communities and public security forces.
It is an industry-wide, international endeavor to demonstrate that illegal tapping is not only a concern for operators, but for society as a whole.
52. Use of ILI data to identify illegal tapping
Milton Carvajalino1
1CENIT, Bogotá, Colombia
Abstract
This presentation will explain development of a methodology to analyze and correlate information from successive, separate MFL ILI inspections to identify illicit valves (taps) in hydrocarbon transportation pipeline systems; generation of recognition patterns for dimensions and configuration of illicit valves; density prediction of areas with greater vulnerability to this threat; consideration of socio-geographic factors along the rights of way.
Deliverables from the project included:
54. How should we respond to geohazards?
Rhett Dotson1, Alex McKenzie-Johnson2
1D2 Integrity, LLC, Houston, USA. 2Geosyntec Consultants, Inc., The Woodlands, USA
Abstract
The threat from geohazards has received increased awareness from operators and increased scrutiny from regulators over the last decade. Most recently the Pipeline and Hazardous Materials Safety Administration (PHMSA) issued an advisory bulletin to highlight the importance for integrity management related to the potential for damage to pipeline facilities caused by earth movement and other geological hazards. The elevated attention from operators has resulted in an increased interest in and use of both bending strain and in-situ site assessments for the identification and assessment of geohazards. However, after properly identifying and assessing a site, many operators experience challenges in determining an appropriate integrity response. Historical integrity practices based on corrosion or crack management have relied upon excavation as a first step in remediation with follow-up responses based on in the ditch findings. Unfortunately, this process is typically not a best practice for geohazards. The excavations are often significantly larger, the site conditions may be less stable, and typical remediations such as sleeves or composites are not practical. This paper will serve as a guideline for helping operators responding to a geohazard threat by providing guidance on data collection, mitigation, and future monitoring.
55. Management of Geohazard Personnel Safety for Working in Challenging Terrain
Emily Ortis1, Tim Waggott2, Evan Shih3, Dave Gauthier3, Chad Fournier2
1Pacific Northern Gas, Vancouver, Canada. 2Pacific Northern Gas, Terrace, Canada. 3BGC ENGINEERING INC., Vancouver, Canada
Abstract
Pacific Northern Gas Ltd. (PNG) owns and operates sweet dry natural gas systems with service extending from Prince Rupert on the British Columbia West Coast to the northeast of the province in the towns of Fort St. John, Dawson Creek, and Tumbler Ridge. PNG’s transmission system operates at high pressures and traverses through one of the most rugged and challenging terrains in North America, with unique weather and geohazard challenges.
There has been an increased focus on the integrity and maintenance of PNG’s assets to ensure a safe and reliable energy supply to the communities. This has led to a considerable increase in the scale and size of PNG’s in-line inspection (ILI) program and, consequently, the associated field activities (e.g., ILI runs, pig barrel modifications, integrity digs, regular maintenance and system betterment projects, etc.) on the pipeline system. This requires field operations in proximity to geohazards and potentially unstable terrain, posing a significant personnel safety risk to the field crews. This presented an opportunity for the development of a management tool to support planning and field-level safety decisions.
A Geohazard Situational Awareness Tool has been developed in collaboration with BGC Engineering (BGC) to manage the identified field safety risks during the construction season. This tool is based on the PNG’s baseline geohazard assessment findings, more specifically, earth and rock slope hazards, debris flow and debris flood hazard crossings, and hydrological hazards of river crossings and rivers in close proximity to the PNG right of way. This tool provides automatic and semi-automatic daily recommendations on the geohazard safety risks based on predictions supported by weather data and hindcasting/forecasting. This tool enables PNG to make field-level risk-based decisions about short-term fieldwork planning and execution to ensure the safe completion of the associated field activities.
This article will present PNG and BGC’s challenges and successes in developing and implementing this pioneer solution for managing identified geohazard risks to personnel safety during the fieldwork season. The intent of this paper is to ensure other operators are aware of the available options to manage personnel safety for working in high-risk geohazard terrains.
Keywords: geohazard, personnel safety, gas pipeline, risk analysis
57. Room Temperature Time Dependent Creep Behavior of Low Frequency ERW Pipe Seams and Implications on Managing Pressure Reversals in Hydrostatic Tests
Dave Warman1, Dan Jia1, Yong-Yi Wang1, Michael Bongiovi2, Chad Destigter2
1Center for Reliable Energy Systems, Dublin, USA. 2Enterprise Products, Houston, USA
Abstract
The presence of low frequency (LF) ERW seam weld defects (e.g., lack of fusion, stitching, and hook cracks) can reduce the pressure-carrying capacity of a line pipe. In cases where these defects may have been subjected to a hydrostatic test, there is a possibility that the seam weld defects could fail at a lower pressure upon re-pressurization. This type of failure, which occurs at a pressure less than the previous pressure and where no time dependent degradation has contributed, is commonly referred to as a pressure reversal.
LF ERW seam flaws can fail when held at a constant load below the straight-off to failure load. This is because ductile materials can exhibit time-dependent creep behavior even at room temperature. Evidence of time dependent behavior is provided by failures that occur during the maximum pressure hold period of a hydrostatic test.
Time dependent growth and reverse yielding can be detrimental when performing multiple high pressure hydrostatic tests which can result in many blowouts during the hydrotests, and flaws that survive the hydrotest may experience some ductile tearing that could be detrimental to fatigue life.
This paper covers:
The testing methodology is successful in showing the time-dependent creep behavior of the bondline flaws at elevated loads, as well as establishing that after reducing the pressure down to zero and back to load, the time dependent creep behavior could be re-activated.
58. Accounting for Residual Stress in the Predicted Failure Pressure Calculation
Michael Rosenfeld1, Scott Fannin2
1RSI Pipeline Solutions LLC, New Albany, Ohio, USA, 2Pacific Gas and Electric, San Ramon, USA
Abstract
Pipeline safety regulations require performing a calculation of the predicted failure pressure (PFP) of defects as part of an engineering critical assessment. Whether to include residual stress from pipe manufacturing, and selecting the magnitude of residual stress, can significantly affect the outcome of PFP calculation. Guidance for accounting for residual stress is inconsistent. A survey was performed of several dozen research reports describing testing and analyses of residual stresses induced by the pipe manufacturing process for various types of line pipe. A simple method for determining whether to account for residual stress, and if so, at what magnitude, has been devised for various categories of ERW pipe, and also for non-ERW pipe.
59. Estimate Pressure at Feature Location in a Complex Pipeline System
Fan Zhang, Daniel Gutierrez
Phillips 66, Houston, USA
Abstract
Determining the pressure level at a feature location in a pipeline is critical for further assessment, such as comparing it with calculated burst pressure, or deriving the local pressure spectrum over time for fatigue evaluation. Currently, API RP 1176 (2016 First Edition) Section 8 provides an equation to estimate local pressure based on immediate upstream and downstream pressure gauge records and the location of the feature. This equation is useful for a simple pipeline with uniform flowrate and up to two pipe segments with different diameters between two pressure gauges. However, real pipeline systems can be more complex. For example, a pipeline segment, located between two pressure transmitters, may be composed of a large diameter subsegment in between two smaller diameter subsegments. The pipeline segment may also include injection or strip off points between the gauges which results in different flowrate along sections of the segment. In this paper, a more universal approach with a group of equations was developed which can calculate the local pressure in a complex pipeline with any number of subsegment of various diameters and flowrates. The methods reduce to the one in API RP 1176 for a simple pipeline system. Working examples are also provided to demonstrate the application.
60. Effect of pipe-soil interaction parameters on pipeline thermal stress analysis
Kshama Roy¹, Suborno Debnath², Joseph Bratton¹
¹DNV Canada Ltd., Calgary, Canada, ²Northern Crescent Inc.
Abstract
Thermal stress analysis is an integral part of the design and integrity assessment of buried pipelines. In the current industry practice, the numerical beam-spring model is extensively used for the stress analysis of buried pipelines under operational (e.g. temperature and pressure) loads. In the beam-spring model, the pipe-soil interaction is simulated using a series of orthogonal soil springs aligned in the axial, lateral, vertical upward and vertical downward directions as recommended by American Lifelines Alliance (ALA) and Pipeline Research Council International (PRCI) guidelines. This paper reviews the assumptions and limitations of the existing methods for structural pipe-soil interaction modelling and investigates the sensitivity of pipe stress values to the pipe-soil interaction parameters using finite element (FE) analysis. The commercial FE software package, Abaqus is used in the present study. A case study mimicked to an actual pipeline is used in the present study to see the practical effects of using different pipe-soil interaction parameters. Results show a significant dependence of the pipeline stresses not only on the pipe-soil interaction parameters but also on using the different design guidelines. The variation in the pipeline stress responses from the FE results indicates that the estimated pipe-soil interaction parameters obtained from different guidelines need to be consistent enough to simulate pipeline stress response under pressure and temperature loading.
61. Know When Using MFL for Effective Area is Wrong!
Christopher De Leon1
1D2 Integrity, Houston, USA
Abstract
Performing corrosion assessments on reported MFL features is a fundamental competency in pipeline integrity management. ASME B31.G provides three methods of calculating burst pressure associated with defect assessment for corrosion, namely B31.G, Modified B31.G, and Effective Area. Each method is based on a geometry and depth profile of the corrosion defect, which may be explicit or an approximation. The technical documentation for each methodology’s application is widely available and well understood. However, the transformation of MFL signal data into metal loss feature characterization as a function of feature length, width, and depth for use in Effective Area calculations is not well understood. If the MFL based depth profile is not representative of the corrosion defect, then the burst calculation using the Effective Area methodology may not be conservative and potentially a safety concern. This paper will use a case study where MFL-A technology was incorrectly used to calculate burst pressure using the Effective Area methodology, highlight MFL technology’s challenge in providing accurate corrosion depth profiles to perform Effective Area calculations, and share guidance on how to qualify MFL data for use in Effective Area calculations.
62. Overcoming detection and sizing challenges for slanted/skewed cracking by combining axial and circumferential crack detection In-line inspections
Oscar Anguila1, Francisco Ibarrola1, Jordi Aymerich1, Rogelio Guajardo1, Katherine Hartl2
1NDT Global, Barcelona, Spain. 2NDT Global, Houston, USA
Abstract
Pipeline operators widely use In-line inspection (ILI) ultrasonic tools to manage their integrity. Specifically for cracking related threats, tool selection will be driven by many factors, one being the crack orientation in relation to the pipe axis. Axial linear anomalies such as; fatigue cracks, lack of fusion and stress corrosion cracking (SCC) can be present due to fatigue, manufacturing related issues, or environmental conditions that favor their development. For circumferential linear anomalies it is not that different, these conditions will also impact their time-dependency state.
Measurement techniques used for crack detection have boundary conditions such as minimum length and depth, but more importantly, the deviation angle from the pipe axis or the circumferential axis will directly have an impact in the ILI tool measurement that will result in an analysis bias to undersize the depth or in a worst case scenario, directly limit the possibility of the feature being analyzed due to signal amplitudes within noise levels and/or below analysis thresholds.
During a field verification campaign of vintage pipe, areas with SCC were uncovered for which the geometries were found to be slanted over the pipe body following areas of coating disbondment. The pipeline had been inspected with both; axial and circumferential crack detection tools which allowed further integration of the data and the possibility to derive a methodology, that is reproducible, providing the user trustworthy and actionable data.
This paper will address the detection challenges of the ILI technology while documenting the necessary steps (incl. non-standard analysis) to derive a methodology that led to improved reporting and depth sizing
KEYWORDS FOR SUBJECT AREA: ultrasonic tools, stress corrosion cracking, spider web cracking, depth sizing, correlation
64. Burst Pressure Prediction for Axial Cracks in Pipelines with Complex Profiles
Thomas Dessein1, Ted Anderson2
1Integral Engineering, Edmonton, Canada. 2TL Anderson Consulting, Cape Coral, USA
Abstract
Crack-like anomalies in pipelines are complex features that typically have an irregular profile. However, due to modelling complexity, the common practice is to approximate such profiles with a semi-elliptical crack whose length is equal to the total flaw length and whose depth corresponds to the maximum depth of the flaw. This approach is very conservative and can result in significant underestimates of burst pressure.
This paper describes recent improvements to the PRCI MAT-8 fracture model that account for arbitrary crack profiles. An extensive finite element study was undertaken to model numerous non-ideal longitudinal crack profiles in pipe joints. The output from these analyses led to a procedure to convert an arbitrary crack profile into an equivalent semi-elliptical crack. The depth of the equivalent crack is equal to the maximum flaw depth, but the length is typically much less than the total flaw length. This modification results in burst pressure estimates that are more accurate and less conservative than the traditional approach.
The procedure improves upon an earlier phase of work (PPIM 2019) that developed an approach which was accurate for cracks with an isolated deeper section that dominates the fracture demand. Since then, more real-world profiles have been assessed and several cases identified for which the previous procedure underestimated the fracture demand. The new procedure resolves this while ensuring a slight conservative bias and maintaining an accuracy that is comparable to typical inline inspection tool length sizing accuracy.
The new algorithm considers interactions between deeper sections of the crack profile to increase the length of the equivalent semi-elliptical crack. While the new algorithm was developed and calibrated using machine learning techniques, it can be implemented without any specialized machine learning tools.
65. Phenomenology and Traits of SCC – and the ILI Challenge it Presents
Brian Leis
Worthington, Worthington, USA
Abstract
Recent work considered the factors controlling SCC and typical cracking speeds based on laboratory test data to identify the factors and quantify the laboratory speeds, which it used to formulate bathtub speed curves that compared favorably to typical field cracking speeds. This paper adds significantly to the hundreds of cracks in the field dataset considered previously. Traits typical of the field cracking are trended and compared with current ILI crack-tool reporting criteria to identify their strengths and potential weaknesses concerning safety and reliability.
Fracture features typical of ruptures and major spills due to SCC are contrasted to those evident for leaks and larger secondary cracking, for benign field cracking, and finally for field cracking at the scale of the steel’s microstructure. It is shown that regardless of the scale the recurrent traits of failures causing ruptures and major spills are comparable down to the smallest of cracking – indicating that the mechanics of SCC is scalable. The associated crack populations are then trended relative to their spacing and sizing as evident on the pipe’s OD surface, on its fracture surfaces, or in x-sections of intact cracking. The resulting populations of surface lengths and profiled depths are then trended for well in excess of a 1000 cracks. That population was then parsed based on their sizes and field response as 1) benign, 2) secondary cracks remote to ruptures and major spills, 3) larger secondary cracks adjacent to ruptures and major spills, leaks and smaller spills, and finally 4) ruptures and major spills.
The parsed dataset was then trended relative to a normalized form of crack aspect ratio as a function of normalized of depth, which effectively discriminated between each of the four parsed datasets. The usual crack-tool reporting criteria specified relative to length and depth were then recast as a function of pipe diameter and wall thickness, such that they could be contrasted with the field data. This identified what amongst this field population would be reported if the tool successfully identified and called each of the cracks. The results showed that the current criteria cull the benign cracking and the smaller secondary features, and report all outcomes that led to ruptures and major spills. Thus, the reporting criteria avoid digs for benign cracking, and successfully capture cracking that poses immediate concern for failure. While effective as just noted, portions of the population that are reaching sizes that have posed a threat in past are less effectively reported. The results indicate that depth is not a key factor in this outcome – rather it was controlled by crack length. This, coupled with the observation that crack length is underreported to an extent controlled by aspect ratio, suggests improved safety and reliability could be affected significantly by improvements in length sizing and length reporting. These aspects are elaborated further in the paper.
KEYWORDS FOR SUBJECT AREA: Crack assessment, ILI applications
93. EMAT Lessons Learned Using Direct Assessment Findings
Matthew Romney1, Kayla Stark Barker1, Ron Lundstrom1, Daniel Bruce2, Alireza Kohandehghan3
1T.D. Williamson, Salt Lake City, USA. 2Pacific Northern Gas, Terrace, Canada. 3Pacific Northern Gas, Vancouver, Canada
Abstract
Different cracking mechanisms can potentially affect pipelines depending on the operating conditions, product, coating type, pipe manufacturing process, and environment. These mechanisms include manufacturing-related crack-like linear indications (e.g., seam weld lack of fusion, subsurface or surface breaking laminations), construction-related cracks (e.g., girth weld cracks, in-service fillet weld toe cracks), cracks formed in mechanical damages, and environmentally assisted cracking (EAC). One of the most important forms of EAC relevant to pipeline structures is stress corrosion cracking (SCC) that has been of particular focus in the past two decades.
Due to the severe consequence of linear indication-related pipeline failures and nonlinear growth and propagation of specific types of linear indication integrity threats, pipeline operators continuously push for new technologies, methods, and procedures for assessing and mitigating pipeline integrity risks pertaining to crack and crack-like anomalies. Inline inspection (ILI) is proven as one of the most effective means that leads to significant improvement in the integrity management of these threats. A key ILI technology that has proven useful for the detection, classification, and sizing of gas pipeline crack and crack-like features is Electromagnetic Acoustic Transducer (EMAT) technology.
Understanding how technologies works and how their performance can be improved is of essence to the success of an ILI-based integrity management program. This article will present and discuss Pacific Northern Gas Ltd. (PNG), and T.D. Williamson (TDW) lessons learned, challenges, and successes of utilizing EMAT ILI technology to identify, classify, quantify, and mitigate crack and crack-like integrity threat risks across multiple gas pipeline systems. Utilizing an EMAT system, populations of anomalies will be reviewed and compared with direct assessment findings. Recommendations and potential mitigation strategies will also be presented.
Keywords: cracks, deformation, electromagnetic acoustic transducer, environmentally assisted cracking, gas pipeline, geometry, inline inspection, magnetic flux leakage, metal loss, Multiple Dataset, pipeline integrity, stress corrosion cracking, , DEF, EAC, EMAT, GEO, ILI, LFM, MDS, MFL, SCC, SMFL
34. Assessing the accurate topography of complex channeling corrosion by means of ultrasonic wall measurement tools. A case study and experiences
Kerstin Munsel1, Katherine Hartl1, Christoph Jaeger2, Santiago Urrea3
1NDT Global, Houston, USA. 2NDT Global, Stutensee, Germany. 3NDT Global, Stutensee, USA
Abstract
This paper presents a case study of an offshore pipeline with pitting and long axial corrosion that had been continuously inspected by Magnetic Flux Leakage (MFL) and was recently inspected with an Ultrasonic Wall Thickness Measurement (UTWM) tool. An anonymized comparison of 3 MFL inspections and the recent UTWM inspection is presented. This analysis demonstrates the challenges associated with the two methods, and how UTWM can be used to acquire topography that describes the complete extent of metal loss. Further, the case study also shows a new and more customized approach to providing data that enables a better comparison of results between different ILI methods. Finally, direct measurement data enables advanced integrity methods, like DNV-RP-F101 Appendix D, which uses wall thickness and standoff data to calculate pipeline capacity and system effect considering the effects of long axial corrosion continuously spanning multiple pipe joints.
KEYWORDS FOR SUBJECT AREA: ultrasonic tools, metal loss corrosion, correlation, complex channeling corrosion, DNV-RP-F101 Appendix D
33. Applying Ultra-High-Resolution MFL To Achieve a Better Integrity Assessment of Pits-in-Pits.
Rick Desaulniers
Entegra, Toronto, Canada
Abstract
The VP of Asset Integrity for a major US west coast liquids operator once asked us to guess the number one cause of leaks on their pipeline systems over the previous year. The answer? 20% deep metal loss … in other words, deep (through wall) pinholes were embedded in an area of less than 20% deep corrosion, also known as “pits-in-pits”. With the advent of Ultra-High Resolution (UHR) Magnetic Flux Leakage (MFL) In-Line Inspection (ILI) techniques, the nuances of complex corrosion can now be reliably explored … including pits-in-pits.
This paper will describe how an increased sensor density and sampling frequency in combination with human-experience based decision making in the analysis process can be deployed to accurately detect, characterize, and size potentially injurious complex corrosion. Data comparisons with in-the-ditch results will be presented.
25. Using Controlled Acoustics to Find a Stuck Pig
Steven Bourgoyne, David Murray
Seismos, Austin, USA
Abstract
SCOPE:
A pipeline operator was preparing to run an in-line inspection on a 4’’ NGL Line in South Texas. Prior to the inspection, the operator launched a 31’’ Mandrel Pig with a Gauge Plate and Cleaning Tool. The mandrel pig was unable to flow the total distance and got caught somewhere in the middle of the pipeline. An unsuccessful second and third pig was launched two weeks later to try and dislodge the first gauge plate pig. Several methods were used to locate the pigs, including geophones, transmitter detection receivers, and mainline block valve pressure differentials.
PROCESS:
To find the missing pig, Seismos used an Acoustic Transmitter, Acoustic Sensor, and Data Acquisition Unit (DAQ) to create controlled acoustics within the pipeline. The equipment was attached to the pipeline at above-ground stations through standard Male Pipe Thread (MPT) connections.
The acoustic transmitter emits a pressure pulse that causes a tube wave to travel via the pipeline media down the length of the pipe. The acoustic energy reflects off the object and the return signal is captured by the acoustic sensor. Signal processing software is used to analyze the return signal providing the object’s precise location.
RESULTS:
Seismos informed the operator of the location of the lost pigs, which ended up being 2+ miles away from where the operator initially thought going into the project. The operator decided to start excavating based on Seismos’ analysis. The pigs were found precisely where Seismos’ analysis had indicated.
********
44. Application of MFL ILI Data for Pipeline Material Verification
Joe Craycraft1, Ransom Stamps1, Tim Arnold1, Andrew Corbett2, Rick Gonzales3, Luke Jain1, Guillermo Solano2, Ron Thompson2
1Campos EPC, Denver, USA. 2Novitech Inc, Vaughan, Canada. 3Xcel Energy, Denver, USA
Abstract
Natural gas transmission pipeline operators are required to maintain Traceable, Verifiable, and Complete (TVC) documentation for certain pipe material properties in accordance with United States Federal Code. Pipeline operators are obligated to reconfirm missing TVC material property information. One route of reconfirmation is material verification in accordance with Title 49 CFR 192.607. AMFL and CMFL data from inline inspection is applied in this study to match pipe joints to a specified minimum yield strength (SMYS). This technology application is proposed to provide an alternate methodology to commonly applied destructive and in situ nondestructive test methods. This alternate ILI-based method would reduce compliance costs as well as health and safety exposures associated with pipeline excavation and other activities required to complete destructive testing and in situ nondestructive testing. Material verification using historic ILI MFL data was validated using available TVC documentation as well as destructive and nondestructive test data. Statistical analysis is applied to identify sampling requirements to achieve a 95% confidence level when applying ILI material verification information in combination with destructive testing and/or in situ nondestructive testing data.
Categories: Data management; ILI analysis; materials identification, verification
20. Navigating the New §192.712 Regulation on Dents
Rhett Dotson1, Fernando Curiel2
1D2 Integrity, LLC, Houston, USA, D2 Integrity, LLC, Houston, USA, 2DCP Midstream, Houston, USA
Abstract
API RP 1183 was released in 2021 and was expected to be a precursor for updated regulations addressing dent assessments. In the fall of 2022, the Pipeline and Hazardous Materials Safety Administration (PHMSA) released the final part of the updated gas rule. In this part of the rule, §192.712(c) specifically addressed the assessment of dents and other mechanical damage. This paper examines the new section of code and provides technical guidance on how these dent regulations can be understood and applied in integrity management programs. In addition, this paper will examine where API RP 1183 and the updated gas rule are not aligned.
79. Meet the Transformer Robots in Disguise
McKenzie Kissel1, Dominik Seepersad2, Peter Fisher2, Ryan Kolebaba1, Rob van Woudenberg1
1Onstream Pipeline, Calgary, Canada. 2Enbridge, London, Canada
Abstract
Gas storage is a critical infrastructure that provides the ability to balance natural gas transmission systems to meet short- and long-term user demands. Natural gas can be stored in above ground facilities, and below ground in caverns and rock formations. There are over 400 active gas storage facilities throughout the North America that provide over 20% of the natural gas required to meet the seasonal winter month demand. These storage facilities are part of the gas transmission network and are directly tied to the system to be accessed as needed. Given the criticality of the natural gas storage infrastructure, like all pipeline infrastructure, it must be inspected. In many cases the pipelines from the natural gas storage wells to the main measurement regulating facilities do not have provisions to inspect the lines efficiently while under pressure or via inline with the media due to flow conditions, pipe fittings and lack of launch and receive facilities. Furthermore, given the criticality of the storage infrastructure, there are very tight outage windows to complete the pipeline inspections. Due to the inspection challenges, these systems are usually completed via a robotic crawler. This paper reviews the recent inline inspection campaign of a network system feeding a natural gas storage infrastructure, through detailed planning and pre job testing, the ability to efficiently and effectively utilize MFL combination tether technology to inspect the network in unprecedented time. Using tether technology, the 13-pipeline segment system, was inspected in under one week, which included multiple pipeline diameters, vertical launches, and short radius bends.
ILI Applications, “Unpiggable” inspections and technologies
32. Survey of Impact: RIN-2 Final Rule – Safety of Gas Transmission Pipelines
Chris Bullock1, Lara Gran2, Luke Whitrock3
1Integrity Solutions Ltd, Bossier City, USA. 2Integrity Solutions Ltd, Missoula, USA. 3Integrity Solutions Ltd, Denver, USA
Abstract
New federal regulations contained in RIN 2137–AF39 titled “Safety of Gas Transmission Pipelines: Repair Criteria, Integrity Management Improvements, Cathodic Protection, Management of Change, and Other Related Amendments” impose new requirements on natural gas transmission pipeline operators. This presentation will provide an initial survey of impact of the Final Rule on operators affected by the final piece of a decade-long effort by PHMSA to amend its regulations of onshore gas pipelines, known as the “Gas Mega-Rule”.
This new rulemaking considers lessons learned from recent onshore gas transmission pipeline incidents and codifies a management of change process. The rulemaking also clarifies certain integrity management, assessment, corrosion control, repair, high consequence area (HCA), and extreme weather event requirements, as well as revises or creates new definitions related to the above amendments.
Compliance requirements, key dates, and a sample case study on the ramifications to corrosion control and integrity management repair criteria will be provided. Integrity Solutions® Ltd will not be producing a white paper to support the presentation, however, an advanced preview of the presentation can be provided.
1. PHMSA Updates Related to Data and GIS
Monique Roberts1, Leigha Gooding2, Blaine Keener2
1PODS Association, Houston, USA. 2PHMSA, Washington DC, USA
Abstract
PHMSA Updates Related to Data and GIS
Did you know that the NPMS system uses the PODS model? So, if you have ever uploaded your NPMS submittal you have used PODS! PHMSA has been a member of PODS for over a decade now in fact, so the PODS Association works closely to make sure that all data tables and schema are standardized for use by all operators and service companies that support them. The PODS Model is operator designed to comply with regulations, support specific pipeline operations and decrease risk through digital twin/asset knowledge management.
Joining PPIM in-person will be Leigha Gooding, PHMSA OPS GIS Manager and Monique Roberts, PODS Executive Director. Leigha manages the NPMS system so we will hear first hand on regulation, data and GIS.
This presentation will cover a high-level overview of the NPMS submittal process, the radical increase in segmentation and new attributes that PHMSA is expecting operators to capture as well as some news from the PODS Community and the recent ILI module release on PODS 7.
79. Benefits of MFL Robotic Pipeline Inspection in Assessing Difficult-to-Assess Pipelines
Brent Gearhart1, Chris Figgatt1, Rod Lee2
1TC Energy, Charleston, USA. 2Intero Integrity Services, Toronto, Canada
Abstract
The robotic inline inspection method has been utilized by distribution and transmission pipeline operators for over a decade. Since its inception, many advancements have been made. This paper discusses the implications and applications of some recent advancements. Furthermore, TC Energy and Intero Integrity Services will discuss the operational benefits of using MFL robotic pipeline inspection for two difficult-to-inspect pipelines by drawing experiences from using robotics in a 20-inch pipeline and an 8-inch pipeline.
89. Detection and Sizing of Selective Seam Weld Corrosion Using Axial and Circumferential MFL Micron ILI Technology
Ron Thompson, Andrew Corbett, Guillermo Solano
Novitech Inc., Vaughan, Canada
Abstract
This research and development are for the purpose of optimizing an In-line inspection (ILI) system for the detection, characterization, and sizing of selective seam weld corrosion (SSWC). This technology utilises both Axial Flux Leakage (AMFL) and Circumferential Magnetic Flux Leakage (CMFL) measuring systems. The technology is also designed to take up to 1,600 readings per square inch providing the required resolution to detect and size SSWC.
This paper will present several phases of the study that include conceptual development, pull testing, and field verification from live runs on pipeline systems containing SSWC. It includes the development of software and analysis tools that utilize varying signal responses to both AMFL and CMFL for different metal loss geometries.
The evaluation of SSWC, and of general corrosion coinciding with the long seam weld area, requires both AMFL and CMFL ILI data that has been collected with very high resolution. This research shows that field-tool correlation improves when the process of characterization and sizing SSWC is carried out in the following three steps:
1. The use very high-resolution data to better delineate SSWC from within the general corrosion area, and to provide precise positioning of the long seam weld.
2. Determine whether the long seam corroded areas exhibit wedge, groove, or axial slot like shapes that are typical of SSWC. These features are frequently in aeras of significant corrosion adding to the complexity of characterization and sizing.
3. Apply both AMFL and CMFL sizing algorithms to the preselected SSWC locations to properly size axially orientated wedge or groove-like features.
This paper will also illustrate additional challenges found during field verifications. These include the occurrences metal loss coinciding with seam flaws such as lack of fusion and hook crack flaws, and the current development of analysis tools that address these compounded flaws that can, on occasion be misclassified as SSWC.
85. Going Above and Below – Material Property Verification Documentation Review
Simon Slater1, Richard Ingolia2, Jamie Skinner3, Aaron Long3
1ROSEN, Columbus, USA. 2ROSEN, Houston, USA. 3NiSource, Hammond, USA
Abstract
The introduction of regulatory changes by PHMSA in 49 CFR 192, for Traceable, Verifiable and Complete (TVC) pressure test and material property records meant that pipeline operators have had address their systems of record. The challenge is to determine the status of existing documentation for all pipe and components in pipelines, pipeline subsystems, and metering & regulating stations.
Reviewing, aligning, interpreting, and managing the significant amount of data and documentation accumulated over the history of these networks presents a challenge. Processes and specifications have been established to ensure that historical records are treated correctly and consistently in the context of regulatory language. Once extracted, the data is integrated into auditable systems of record, which can be easily visualized to support and facilitate programs for regulatory compliance and Integrity Management.
This paper will present a summary of the processes and applications that a partnership between the operator and engineering consultancy has implemented to surmount these challenges, including document management, Geographical Information Systems (GIS) and geospatial analysis, in-field verification for stations, and quality control methods. Commentary will be provided on the treatment of historical records in the context of the new regulatory requirements, where interpretation is often required. Finally, a discussion on how operators can use these systems and processes to inform and implement strategies for MAOP reconfirmation and material verification will also be provided.
62. Pressure Reduction Determination Through Reverse Failure Pressure Modeling and Staggered Implementation
Carl LeClerq
DynamicRisk, Spring, USA
Abstract
When an integrity-related condition that could impair the serviceability of a pipeline is identified or suspected, operators may consider temporary restrictions or reduced operating pressures as both an immediate response and during subsequent maintenance activities. Pressure reductions lower operating stresses and effectively mitigate the immediate integrity threats posed by such condition for a period of time – thus reducing asset risk. North American pipeline regulations, industry standards, and operator standard practices provide various levels of guidance regarding failure pressure modelling and pressure reductions as a response to identified or suspected conditions. However, these practices require known or assumed values to complete failure pressure models and obtain meaningful pressure reductions. Those operators aiming to use “known” data in the models may be required to perform direct inspections or extensive record review to collect such data; if “assumed” values are utilized, results may lead to overly conservative pressure reductions and unnecessary disruptions in business operation. This paper provides a process to determine critical flaw sizes and resultant pressure reductions for time-dependent threats that account for “unknown” or low-confidence data by reversing the failure pressure equations for a given model. Supporting case studies are provided as examples in application of this methodology, including guidance on implementing staggered pressure reductions.
27. Minimizing the Error in Corrosion Growth Rate Estimation from Box-to-Signal Matching
Jed Ludlow, Jonathan Hardy
T.D. Williamson, Salt Lake City, USA
Abstract
The benefits of conducting signal-to-signal matching between two successive in-line inspection (ILI) runs for purposes of estimating corrosion growth rates have been discussed at length in the pipeline industry. However, in many situations, the complete signal data for both inspections are not available to the analyst. Perhaps only the raw signal data for the current inspection is available and only a reporting spreadsheet is provided for the prior inspection. In this case, a box-to-signal matching exercise is required. How should this exercise be conducted such that it minimizes the error in the estimated corrosion growth rate?
There are multiple ways that error can creep into a corrosion growth rate analysis, especially when full signal data is not available for both inspections. Some of the largest sources of error are related to anomaly alignment rather than to depth measurement uncertainty. These include:
These types of errors introduce substantial scatter into the distributions of change-in-depth between inspections and can result in significant errors in growth rate estimates. This paper presents practical strategies that operators and service providers can adopt to avoid these large error sources.
21. Full-Scale Fatigue Testing and Assessment of Dents on Brittle Longitudinal Welds – A Detailed Management Approach for a Liquid Pipeline in Chile
Pedro Guillen1, Jamie Martin1, Ricardo Alarcon2, Roberto Jadue2
1ROSEN Group, Newcastle upon Tyne, United Kingdom. 2SONACOL, Santiago, Chile
Abstract
SONACOL owns and operates a 135 km, 6-inch diameter pipeline refined products pipeline located in Chile, which was constructed in 1964 from longitudinally welded (ERW) pipe with thicknesses between 5.16 and 12.7 mm. This pipeline has been inspected on multiple occasions for metal loss, deformations and cracks as part of its Integrity Management Plan. Following the most recent inspection and subsequent integrity assessment, an operational pressure reduction was introduced as some of the reported dents were considered to pose an immediate threat to the pipeline integrity. Of particular concern were dents identified to be associated with brittle longitudinal seam welds.
SONACOL supported by ROSEN have developed a strategy to assure the continuous safe operation of this pipeline. This involved a full scale testing and various levels of assessment increasing in complexity.
The strategy included the selection of critical dents, which were removed from the pipeline and underwent a full-scale fatigue testing, NDT assessment and material characterisation tests. Testing results demonstrated an acceptable level of conservatism in the assessment methods since fatigue growth was found to be overestimated. Dents were prioritised using an initial EPRG fatigue assessment followed by an FEA assessment. Additionally, the API 1183 longitudinal weld interaction was used to determine the likely effect of welds on the fatigue life of dents. The integrity assessment, which incorporated all ILI reported features including crack like anomalies, was used to develop a refined repair plan. This strategy has allowed Sonacol to continue operating the pipeline and demonstrate a suitable safety margin for that.
This paper summarises the different stages through the process of developing the dent management strategy.
7. Thought Bias: The Hidden Pipeline Integrity Threat
Michael Rosenfeld, Joel Anderson
RSI Pipeline Solutions, LLC, New Albany, USA
Abstract
Pipeline regulations, industry standards, and technical research set forth extensive guidance for managing threats to pipeline integrity through a formal integrity management (IM) plan. Such plans rely on a rigorous procedural approach to identify threats and mitigate risk on a prioritized basis in a systematic and repeatable process. One subtle threat that is not just overlooked but is almost invisible to many integrity management personnel is that of biased thought processes. Because they typically go unrecognized for what they are such biases can seriously undermine the effectiveness of IM programs in a variety of ways that lead to poor decisions. Such biases may also affect routine pipeline construction and maintenance projects outside of IM work but which may lead to long-term IM implications. Even when information to the contrary exists prior to the decision, people can become anchored to a fallacy, unwilling to move from it. The various forms of bias, examples of their potential adverse effects on pipeline integrity, warning signs, and potential avoidance methods are discussed.
6. Three Emerging Threats: Climate Change, Cyberattack and Vandalism
Eduardo Munoz
Dynamic Risk, Calgary, Canada
Abstract
Regulation changes have prompted pipeline operators in the US and Canada to request assistance with the assessment of threats not deemed a concern or priority in the past. The operators’ renewed interest on these threats coincides with PHMSA requests to incorporate Climate Change and Cyberattack into the existing pipeline risk models. The likelihood of failure for such threats is difficult to validate because of the lack of proper lagging and leading indicators. This work presents a tentative framework for hazard identification, data gathering, risk modeling, and integrity management of Climate Change, Cyberattack and Vandalism. Additional considerations are presented for consequence assessment and interacting threats.
31. The Future of In-Line Inspection (ILI): New U.S. Gas-Gathering Pipeline Regulations and ILI – What to Do, and Not to Do, to Comply with the Law, an Operator’s Perspective
BERNARDO CUERVO, Mark McQueen
G2 Integrated Solutions, now Entrust Solutions Group, Houston, USA
Abstract
Traditionally, most gas gathering lines were small diameter low-pressure systems traversing sparsely populated areas, posing little risk from a business, safety, and environmental concern. More recently, the volume of gas transported through gathering systems has increased significantly due to the advancements in horizontal drilling and hydraulic fracturing techniques. Subsequently, gas gathering systems have evolved into larger-diameter pipelines operating at much higher pressures in formerly rural areas. As a result, the Pipeline and Hazardous Materials Safety Administration (PHMSA) issued a final rule that expands Federal pipeline safety oversight to all onshore gas-gathering pipelines. This new rule changes the definition of a regulated gas-gathering pipeline. More than 400,000 additional miles will be covered by Federal reporting requirements. This paper describes how a competent and proactive operator implemented a program to comply with the new regulations and prepared thousands of gathering pipelines for inspection with ILI tools. The lessons learned will be illustrated with a case study.
30. In-Depth Review of DOT 192 & 195 Pipeline Incidents and Accidents for 2010-2021
Derek Sollberger
IC Solutions, Edmond, USA
Abstract
For the past two years I have presented at the GPA-Midstream conferences on individual analysis of the natural gas transmission and hazardous liquids pipeline PHMSA incident and accident history. Over the last decade, natural gas pipeline operators experienced $1.4B in damages from 1,364 events. Each of these events had the potential to collect 622 unique data entries related to the incident. For the hazardous liquids pipelines, the overall costs nearly double at $2.7B in damages on nearly 4,000 events, with a similar count of unique data points required in accident reporting. The presentation included analysis, trends, and opportunities for improvement. The initial exercise was initiated after realizing the PHMSA accident reporting form, RSPA F 7000-1, had undergone a significant revision in 2010 and was now collecting more than twice the data of the previous version form. The same improvements were relevant for PHMSA F 7100.2 I now plan to conduct a comparison of natural gas and hazardous liquid pipeline data sets along with European pipeline accident history and highlight areas of potential improvement in pipeline safety.
My evaluation and analysis consists of the following:
I believe this data set and associated presentation provides a useful industry review for the last decade of pipeline incidents and accidents. Operator representatives for engineering, operations, construction, and HES organizations can benefit from the industry lessons learned, potential risks, and opportunities for improvement.
Keywords: DOT 192 & 195 – Compliance, Operations & Maintenance, Pipeline Safety, and Safety & Reliability
28. Lessons Learned from Applying Probability of Exceedance (POE) Analyses
Tom Bubenik, Steven Polasik, Ben Hanna
DNV USA, Dublin, USA
Abstract
The Probability of Exceedance (POE) methodology was introduced in the late 1990s to manage corrosion on pipelines after in-line inspections (ILIs). It helps prioritize anomaly locations for remediation by calculating their likelihoods of exceeding one or more thresholds that correspond to potential leaks and ruptures. By applying POE, a pipeline operator can assess how the likelihood of a release changes with time, which can be used to design rational and science-based remediation programs.
DNV has developed and used an improved POE methodology to analyze a range of pipelines and develop remediation strategies. The methodology explicitly considers growth in both the depth and length directions. In conducting these analyses, a number of learnings were developed. Understanding how longer anomalies (e.g., clusters of individual anomalies) grow to failure is critical. This paper will discuss how different growth methodologies can affect coalescence of individual pits in clusters and the severity and likelihood of failures due to rupture.
26. The Mega Rule brings greater challenges to “Pigging the Unpiggable” that will require new chemical pigging technologies.
Buck Houchin1, Martin Ridge2, Dorian Granizo1, Joe Conine1
1PIC Chemicals, Tomball, USA. 2Sanccus Limited, Aberdeen, United Kingdom
Abstract
Many of the 425,000 miles of gathering system pipelines now being regulated under the Mega Rule are a byproduct of the growth of the natural gas production from unconventional shales. New gas pipelines were constructed without envisioning the challenges of meeting rigorous standards. Minimizing leak risks caused by internal corrosion is one of the foundational pillars of the regulation. Pipelines with corrosion risks must show increased monitoring, sampling and pig cleaning. Gathering pipelines, by their very nature, often have mechanical barriers to traditional mechanical pigging. Solutions for mechanical impediments such as variable diameters, tie end connectivity, hard 90 degree turns, tees and tee bars and many other obstacles are provided. Chemical gels fit into 3 categories that include liquid gels (targeted cleaning), gel pigs (liquid/liquid pigging), and solid gel pigs (gas propelled). Linear Chemical gels can pick up debris and safely dissolve contaminants such as iron sulfide and magnetite as well as work as a surveillance pig to locate blockage like wax and scale. Hygroscopic drying gel pigs are invaluable as part of hydrotesting operations. Liquid gel pigs are rigid crosslinked gels that automatically adjust to varying diameters and mechanical barriers to serve as a spacer, barrier or swab pig. New solid gel pigs called Shape Memory Pigs (SMP) can adjust up to 50% diameter changes over great distances. When encountering excessive barriers or blockage the SMP will break up into small flowable pieces avoiding sticking risks. It can be launched with its own canister or formed in situ by pumping through a needle valve as liquid into a compressible, full bore solid pig. SMP can be propelled with liquids, gas or multiphase flow. Any barrier that prevents utilizing mechanicals pigs can be accommodated by these new novel technologies. This paper provides design guidelines for selecting and customizing solutions using these chemical pigging technologies..
19. Investigating the Impact of Changes to Formation Strain Predictions on Dent Integrity Management of Gas Pipelines
Morry Bankehsaz1, Ryan Sager1, David Slane2
1ROSEN USA, Houston, USA. 2PG&E, San Ramon, USA
Abstract
Pipeline Research Council International (PRCI) has recently completed a study funded in part by the Department of Transportation (DOT) and the Pipeline Hazardous Materials Safety Administration (PHMSA) to improve dent/cracking assessment methods for mechanical damage assessment.
Results from the DOT PHMSA project 855 have suggested that the current equations found within Appendix R of ASME B31.8 used to predict dent strain may under-estimate the formation strains, especially for deep and narrow dents or for unconstrained dents. Formation strain is an important characteristic of dents, with critical values potentially inducing the formation of cracks. US DOT regulation 49 CFR 192 requires injurious dents to be remediated while noting that dents where critical strain values are not exceeded may remain in operation as a monitored condition. Accurate prediction of the formation strain for any dent is important in ensuring the structural integrity of the pipeline.
Findings from the DOT PHMSA research program have proposed a modification to the ASME equations in order to better estimate the strain incurred during formation. The new methodology modifies the ASME equations through the adjustment of the axial membrane strain component as well as the incorporation of an additional circumferential membrane strain component. Furthermore, an additional correction for unrestrained dents has been proposed.
Understanding that industry standards and regulations are driven by research performed by PRCI and others, it is essential to understand the impact that these changes to formation strain predictions may have on dent integrity management of US operated gas pipelines. This study investigates the acceptability of dents by comparing strain values, calculated from the current ASME equations, against the methodology proposed in DOT PHMSA project 855. In-service dents for a wide range of pipe geometry and dent shapes from several gas pipelines have been utilized for this study. The current work details the comparison and findings for restrained and unrestrained dents assessed using the dent profiles captured during ILI tool runs. Furthermore, the strain assessment results are compared against critical strain limits to illustrate the impact the proposed methodology will have on gas pipeline systems operating currently. Finally, a discussion as to how these results may be incorporated into the Integrity Management plans of gas pipeline operators is presented.
18. Detaining Dents – Determining Restraint for Dents Measured by ILI Case Study
Jonathan Hardy1, Christopher Newton2
1T.D. Williamson, Salt Lake City, USA. 2Phillips 66, Houston, USA
Abstract
The assessment of dented pipelines received a key advancement in standardized approaches with the first publication of API Recommended Practice 1183 – Assessment and Management of Pipeline Dents. One important factor in estimating the fatigue life of a dented pipeline, as described in API RP 1183, is determining the restraint condition of the dents. API RP 1183 describes a process for determining a dent’s restraint condition according to the results from the PRCI MD-4-9 research project. This main method for determining dent restraint calculates a restraint parameter based on characteristic lengths and areas of the dent shape. It improves upon the traditional techniques of using a dent’s orientation to determine restraint or conservatively assuming all dents to be unrestrained. Difficulties can be encountered, however, in applying it practically to dents measured by ILI. For example, identifying pipe geometry baseline shape and proper smoothing of raw deformation data.
This paper describes the API RP 1183 restraint parameter, the challenges encountered when applying it to dents measured by ILI, and helpful tips for improving restraint determination results. A case study is presented involving determining the restraint condition of 231 dents with shallow depths, many of which initial restraint parameter calculations disagreed with experience-based restraint determination. Recommendations for handling these cases and for potential future work and improvements are made.
14. Perception vs Reality: Managing ILI Verification for Internal Corrosion
Paul Spoering, Mike Niosi, Taras Bolgachenko, Keith Walters
Onstream Pipeline Inspection, Calgary, Canada
Abstract
Pipelines which transport dry natural gas and refined products are generally less likely to have an active internal corrosion threat. The primary corrosion-related threat for these types of pipelines is external corrosion. Non-destructive examination (NDE) can be performed on these pipelines which provides pipeline operators with a high degree of confidence in external corrosion measurement. Although ILI-to-NDE correlation can still present challenges with external corrosion, the verification and measurement is relatively straightforward. So long as the NDE process is well documented with images and recordings such as raw laserscan data, any alignment discrepancies can be resolved offline, well after the NDE is completed.
On the other hand, ILI verification is much more challenging for pipeline systems which are susceptible to internal corrosion, or to a combination of both internal and external corrosion. In-situ NDE for internal corrosion is very difficult as the defects are not visible, making it difficult to assure NDE technicians that they are scanning precisely the right locations. Assuming that the defects are currently located, they are typically measured with techniques that are not as robust and reliable as more direct measurement techniques such as high-resolution laserscan. For pipelines with both internal and external corrosion, the different corrosion mechanisms can create very different corrosion morphologies so the verification of sizing for external corrosion is not necessarily representative of the inspection performance for internal corrosion. Due to a lack of offline data and details such as images and raw scan files, resolving alignment and sizing discrepancies after the dig is completed is very difficult.
Through a series of case studies comparing ILI, NDE and destructive testing methods, this paper will explore the unique challenges to post-ILI verification of internal corrosion defects and the significant general uncertainty to be considered when assessing ILI performance.
13. Limitations and pitfalls of non-destructive examination techniques for the validation of in-line inspections
Sayan Pipatpan1, Tannia Haro2
1NDT Global, Stutensee, Germany. 2NDT Global, Houston, USA
Abstract
Field verifications are the most reliable option for the qualification of an in-line inspection (ILI) technology or the validation of an individual ILI survey. This includes inspecting the reported anomalies in situ with non-destructive examination (NDE) methods to confirm their dimensions and characteristics.
It is a common misconception to see NDE results as ‘absolute truth’. As an example, API Standard 1163:2018 recommends using a NDE method with tolerances 3 times smaller than ILI if NDE tolerances shall be ignored. Due to the continuing improvement in in-line inspections, some ILI technologies may nowadays match or even surpass NDE in terms of sizing accuracy.
The paper focuses on 2 different verification scenarios using advanced NDE technologies – inspecting external metal loss with laser scans, and inspecting crack-like anomalies in seam welds with phased array UT. Using examples from various inspection projects, the limitations and pitfalls are discussed, providing a ‘behind the scenes’ view on NDE.
The insights can help with the selection of suitable verification procedures for ILI anomalies, as well as the interpretation of verification results and their comparison with the ILI report.
KEYWORDS FOR SUBJECT AREA: field verifications, pitfalls, laser scans, phased array UT, crack, crack fields, metal loss
12. Pipeline Integrity Dig Lessons Learned, Challenges, and Improvements
Nathan Weigl1, Jordan Brooke1, Alireza Kohandehghan2
1Pacific Northern Gas Ltd., Smithers, Canada. 2Pacific Northern Gas Ltd., Vancouver, Canada
Abstract
Pacific Northern Gas Ltd. (PNG) owns and operates sweet dry natural gas systems with service extending from Prince Rupert on the British Columbia West Coast to the northeast of the province in the towns of Fort St. John, Dawson Creek, and Tumbler Ridge. PNG’s transmission system operates at high-pressure levels and traverses through one of the most rugged and challenging terrains in North America with unique weather and geohazard challenges. There has been an increased focus on the integrity and maintenance of PNG’s assets to ensure a safe and reliable energy supply to its customers. This has led to a considerable increase in the scale and size of PNG’s in-line inspection (ILI) program and, consequently, the integrity dig program. Modifications to its existing integrity dig program were required to ensure timely and efficient completion of the required integrity digs while meeting the technical, safety, and environmental requirements.
The structural changes include improvements in scope definition, scope communication, planning, contractor management, screening, permitting (regulatory, landowner, environmental, etc.), constructability reviews, budget estimation, construction prioritization, technical and safety requirements, execution, documentation, close-out regulatory submissions and notifications, and record keeping. Numerous challenges have been encountered that led to valuable lessons and significant improvements in all aspects of the work. Understanding that the maturity of integrity dig programs can typically take up to 3+ years, this is an ongoing process of learning lessons and their implementation of the practices for in-progress and future work.
This article will present PNG’s experience encountering common and rare challenges during the integrity dig work. Furthermore, this paper will detail lessons learned and improvements implemented into the existing processes for safety, technical, and efficiency. The intent of this paper is to share this knowledge with other operators to enhance the performance and effectiveness of their existing integrity dig processes and procedures. The ultimate outcome of this is to contribute to the continuous improvement of the industry’s best practices.
Keywords: pipeline integrity dig process, coatings, codes and standards, direct assessment, environmental studies, geohazards, geospatial systems and data, integrity management plans, IMPs, materials identification, NDE, regulations and compliance, repair and rehabilitation, SCC assessment and management, weld integrity
11. Operator Statistical and Probabilistic Grade Estimation Using API 1176
Tara McMahan1, William Harper1, Tom Bubenik1, Benjamin Hanna1, Adriana Nenciu2
1DNV GL, Dublin, USA. 2Otterbein University, Westerville, USA
Abstract
A key property of a pipe joint is its specified grade. For some segments, the grade is unknown due to mergers and acquisitions, lost records for legacy pipe, or other reasons. The U.S. Department of Transportation’s Pipeline and Hazardous Materials Safety Administration (PHMSA) has updated regulations leading to the need to better understand joint grade. PHMSA developed revisions to address the recommendations made by the National Transportation Safety Board (NTSB), which highlighted the importance of using accurate material properties to assess the integrity of pipelines.
GradeIt is a Power BI app that provides both a statistical and probabilistic grade estimation based on yield strength. This is not only for individual joints but with a larger look at the population of interest. The fidelity of the grade estimation relies on the number of data points, as there may be multiple yield strength measurements for each joint. GradeIt includes an adjustable degree of conservatism by allowing the user to set desired probability levels. New metrics are introduced to quantify the quality of the overall segment grade relative to the assumption of differing pipe grades.
Case studies illustrate the utility and possibilities, as well as the challenges, involved with the identification of potential segment grades. This includes sensitivity evaluation to arrive at defendable grades for pipeline segments without defined grades as well as verifying grades and populations for lines with already assigned grades.
8. Pipeline Integrity Management Applications Using High Fidelity Fiber Optic Monitoring & Machine Learning
Ehsan Jalilian, Steven Koles, Mike Hooper, John Hull
Hifi, Calgary, Canada
Abstract
Distributed fiber optic sensing has been gaining significant momentum in pipeline industry adoption. While initial deployment of this technology has focused on preventative leak detection, new value-added applications continue to emerge which deliver data that are more oriented to long term pipeline integrity management and direct operational support.
Different fiber optic sensing technologies exist which can be appropriately leveraged for various applications. High fidelity distributed sensing (HDS) achieves a very high signal-to-noise ratio (SNR), compared to other sensing or monitoring technologies. Along with high SNR, HDS also provides integrated acoustics, temperature and strain/vibration, and is optimized to do so over long distances without degradation of fidelity. This makes the HDS technology particularly appropriate for preventative pipeline leak detection as well as a number of other value-added applications which can leverage acoustics and either real time or cumulative strain/vibration measurements. These cumulative strain measurements can be extremely valuable from a pipeline integrity perspective in terms of monitoring applications such as slope stability, ground subsidence, and other points of measured strain including a variety of pigging-related activities.
A recent novel application involved collaborating with a major producer (Suncor Energy) for the successful remediation of ovality issues with a segment of the pipe constructed via boring. The HDS data assisted in the process via monitoring of multiple pig-induced strain signatures as different construction techniques were used to sequentially alleviate the pipe ovality issue associated with the vertical pipeline loading, and a caliper pig was used during each individual sequential step. Such measurements bring direct operational savings, while also assisting the pipeline operator in understanding where the dynamic / elastic segments exist along the right-of-way and detecting strain anomalies in a spatial or temporal context.
Case studies will be provided to showcase the value of using supervised / unsupervised machine learning and high-fidelity distributed sensing to enable ground disturbance / security intrusions, geotechnical monitoring of earthquakes and slope movement, pig detection / real time pig tracking, as well as analysis of multiple pig runs. A specific case study will be provided to demonstrate how the cumulative strain analysis provided by the HDS technology contributed to the identification of the geohazard risks to a specific pipeline, leading to the ultimate decommissioning and relocation of the pipe. Other “value added” applications such as flow monitoring of anomaly detection, flow rate, pressure, and density estimation will also be presented.
5. An Optimal Approach on Acceptance Criteria for Ripples in Pipeline Field Bends Under Internal Pressures
Enyang Wang1, Aaron DInovitzei1, Rick Gailing1, Abdelfettah Fredj1, Bingyan Fang2, Jing Ma3
1BMT, Ottawa, Canada. 2Baker Hughes, Calgary, Canada. 3Exxon Mobil, Houston, USA
Abstract
In the fitness-for-service of a pipeline field bend containing ripples (or mild wrinkles), existing criteria from codes and standards (e.g., ASME B31.8 and CSA Z662) were considered (initially reported in the PRCI study PR-218-9925). These acceptance criteria define the maximum allowable ripple crest-to-trough depths (d) normalized by the pipe outside diameters (D) as a function of the hoop stress (operating stress as defined in the standards). For a gas pipeline, the maximum allowable d/D ratios are 1% and 2% at hoop stresses ≥ 47 ksi (324 MPa) and ≤ 37 ksi (255 MPa), respectively. For a liquid pipeline, the maximum allowable d/D ratios are 0.5% and 2% at hoop stresses ≥ 47 ksi (324 MPa) and ≤ 20 ksi (138 MPa), respectively.
In the fatigue life integrity assessment, the codes and standards recommend employing the PRCI stress concentration factor (SCF) equations to calculate the increase of stress levels if d/D ratios are greater than the simple and conservative limits (e.g., Fig. 10.6 of CSA Z662-2019). In total, three sets of SCF equations were developed for three loading conditions (i.e., internal pressure ~ SCFP, bending moment ~ SCFM, and temperature differential ~ SCFT).
In the recent ripple fitness-for-service assessment, it was found that the PRCI-SCF approach becomes strongly dependent on the a/C term (i.e., (a/C)^(-2.971)), where a and C are the ripple width and pipe circumference, respectively. It was observed that using a/C may lead to an unconservative SCF evaluation if the ripple is narrow (in width), e.g., at relatively lower a/C ratios (a/C<0.2). It is noted that the ripple width is generally calculated from the in-line inspection (ILI) data (e.g., normalized circumferential variations of caliper data). It may inevitably introduce a certain degree of inherent measurement inaccuracies, especially in the circumferential direction where it interacts with other features (e.g., pipe ovality).
The present study reviews the PRCI-SCF approach and corresponding applicable ranges by conducting probabilistic analyses. A revised PRCI-SCF approach was proposed to improve the prediction accuracy of stress increases for ripples or mild wrinkles in pipeline field bends under internal pressures. Two sets of data (PRCI PR-218-9925 and industrial pipe tally data) were used to generate random samples in the probabilistic study. The assessment results indicate that (1) the PRCI-SCF approach mainly considered the impact of axial profiles of ripples or mild wrinkles (i.e., depth and length/wavelength); (2) impacts of circumferential profiles, namely the feature width, were indirectly considered, and limited numbers of feature widths (a) were chosen from the feature depth-to-wall thickness (d/t); (3) the revised PRCI-SCF approach has a better prediction accuracy for evaluating SCF under the internal pressure loading (SCFp), and (4) the revised approach also has a straightforward definition with four applicable conditions and one correction factor.
4. Applying API RP 1183 to Real-World In-Line Inspection Dent Data
Aaron Lockey1, Susannah Turner1, Tim Turner1, Mike Kirkwood2
1Highgrade Associates, Newcastle, United Kingdom. 2T.D. Williamson, Swindon, United Kingdom
Abstract
The publication of API Recommended Practice 1183 (API RP 1183) in 2020 represented a significant leap forward in standardising advanced pipeline dent assessments, and in normalising this type of assessment for pipeline operators. Beyond screening, API RP 1183 defines two main types of assessment for dent fatigue life modelling: using closed-form equations and dent shape parameters based on extensive testing and simulation (Levels 1 and 2) and detailed assessment using finite element analysis (Level 3).
This paper describes the difficulties encountered when applying the API RP 1183 guidance in the assessment of 949 dents in three separate pipelines. The points addressed in the paper include:
The method to calculate the required shape parameters from real-world in-line inspection (ILI data), which can be problematic to navigate.
One of the key issues with API RP 1183 is the focus on a closed-form approximation, and the general approach to the use of finite element analysis (FEA) based directly on ILI data is somewhat “discouraged” given the research factored in the code. This paper discusses an alternative, validated, approach for FEA of dents that provides a reliable and effective implementation of Level 3 fatigue assessment based directly on ILI data which removes unnecessary conservatism, provides greater accuracy and insights, and can be efficiently automated.
The paper also presents a number of real examples from the sample data and discusses the key decisions that had to be made for each dent type.
3. Your API 5L Vintage Line Pipe Fracture Toughness Data Would Likely Fall Within This Range
Sergio Limon1, Carlos Madera2, Kevin Coulter3, Ken George4, Ravi Krishnamurthy4
1Blade Energy Partners, Salt Lake City, UT, USA. 2Dow Chemical, Angleton, TX, USA. 3Dow Chemical, Freeport, TX, USA. 4Blade Energy Partners, Houston, TX, USA
Abstract
When assessing structural integrity of energy pipelines with cracks and seam weld defects, we are interested in the tolerance of the line pipe material to resist fracture in the presence of a planar defect. This material characteristic is known as fracture toughness. There are two sources of fracture toughness data commonly used in the pipeline industry: toughness measured from a starting blunt notch loaded dynamically and fracture toughness obtained from a starting sharp crack subjected to quasi-static loading. Often, neither of these two types of toughness are available for a pipeline for which an engineering planar defect assessment is to be performed. Therefore, conservative assumptions would need to be made.
A fracture toughness database comprised of nearly one hundred J-integral toughness data measured from API 5L pre-1980s ERW/EFW line pipe samples was analyzed. The fracture toughness tests were conducted in accordance with ASTM E1820 at room temperature. The analysis of these J-integral data point to ranges of seam weld bondline and pipe body toughness values that can be used in engineering assessments of pipelines with planar defects. The fracture toughness ranges are expressed in terms of Mean and Mean ± Standard Deviations. These values will support using lower bound toughness assumptions while avoiding the reliance of overly conservative toughness data. Recent J-integral toughness data from pre-1980s ERW/EFW pipe fall within these ranges. All J-integral toughness tests were conducted using a standardized sub-size test specimen and the transferability of fracture toughness results from sub-scale testing samples to full-scale pipe conditions are explored in the paper.
Use Your Layers Wisely – Composite Repair of SCC
David Futch1, Sean Moran2, Casey Whalen3
1ADV Integrity, Inc., Waller, USA. 2Williams, Salt Lake City, USA. 3CSNRI, Houston, USA
Abstract
Composite repairs have been traditionally utilized as a means to repair features identified on pipeline systems including corrosion and dents. Recently, several industry-based studies have been performed to investigate the repair of longitudinal cracks and crack-like features. These studies demonstrated the ability to reinforce crack and crack-like indications, however, were reinforced with overdesigned repair thicknesses. While this is conservative, additional layers increase cost and complexity of the repair.
This study utilized nominal API 5L, Grade X52, 10-inch OD x 0.188-inch WT pipe removed from the field containing actual SCC indications to fabricate four full-scale test samples. Thicker pup extensions were utilized to ensure a higher stress level within the portion of pipe containing the SCC indications. The SCC indications present had a max interconnecting length of 16 inches and a maximum depth of 68% of the wall thickness.
Varying repair thicknesses were installed to further investigate the ability of a carbon fiber composite repair system to reinforce SCC indications of varying lengths and depths. Additionally, one sample was repaired while under pressure. To accomplish a comparison between samples, several criteria were compared: the ability to survive full-scale pressure cycling and subsequent burst test, a reduction in strain measured across repaired crack-like indication using a uniaxial strain gage, and any subsequent growth identified after completion of the full-scale tests. All cracks were broken open after testing to confirm starting and final crack depth.
In-Depth Review of DOT 192 & 195 Pipeline Incidents and Accidents for 2010-
2021
Derek Sollberger
IC Solutions, Edmond, USA
Abstract
Presenter: Derek Sollberger, PE
Title: President and Owner
Category: DOT 192 & 195 – Compliance, Operations & Maintenance, Pipeline Safety, and Safety &
Reliability
Company: Integrity and Compliance Solutions, LLC
Abstract:
For the past two years I have presented at the GPA-Midstream conferences on individual analysis of the
natural gas transmission and hazardous liquids pipeline PHMSA incident and accident history. Over the
last decade, natural gas pipeline operators experienced $1.4B in damages from 1,364 events. Each of
these events had the potential to collect 622 unique data entries related to the incident. For the
hazardous liquids pipelines, the overall costs nearly double at $2.7B in damages on nearly 4,000 events,
with a similar count of unique data points required in accident reporting. The presentation included
analysis, trends, and opportunities for improvement. The initial exercise was initiated after realizing the
PHMSA accident reporting form, RSPA F 7000-1, had undergone a significant revision in 2010 and was
now collecting more than twice the data of the previous version form. The same improvements were
relevant for PHMSA F 7100.2 I now plan to conduct a comparison of natural gas and hazardous liquid
pipeline data sets along with European pipeline accident history and highlight areas of potential
improvement in pipeline safety.
My evaluation and analysis consists of the following:
A comparison of the form versions and general observations on the now consistent format and units
as well as the incremental data collected.
Geographical representation of incident history for 2010-2021, with volume and failed asset
representation in point size scale and color notation.
Asset specific evaluation data for major categories including: Vessel, Compressor, Valve, and Pipe.
Each asset category analysis includes unique design trends related to: commodity carried, cause,
year of manufacture, failed component, nominal size, seam type, external pipe coating type, and
current function.
Each asset category analysis includes unique operational trends related to: natural force
contributors, incorrect operation factors, equipment activity, year of install, availability and use of
procedures, incident identifiers, corrosion type, current corrosion efforts, current integrity programs,
and ILI history.
Incident release volumes and cost details for each asset were reviewed for financial impact on
operators.
Operator Annual report data was utilized to identify any disproportionate conditions related to:
seam type, manufacture year, etc.
Incident costs were evaluated with comparison to consolidated operator Annual Report data for
predictive incident volume and cost per mile evaluations.
Key observations and recommendations were summarized for each asset category with supporting
industry standards and recommended practices references.